Introduction to Halogen-Free PCBs
In recent years, there has been a growing concern about the environmental impact and health hazards associated with the use of halogens in printed circuit boards (PCBs). Halogens, such as chlorine and bromine, have been widely used in the manufacturing of PCBs due to their excellent flame-retardant properties. However, when these substances are exposed to high temperatures or come in contact with water, they can release toxic fumes that pose serious health risks and contribute to environmental pollution. As a result, the electronics industry has been moving towards the adoption of halogen-free PCBs as a safer and more eco-friendly alternative.
What are Halogens?
Halogens are a group of chemical elements that include fluorine (F), chlorine (Cl), bromine (Br), iodine (I), and astatine (At). These elements are highly reactive and have similar chemical properties. In the context of PCBs, the most commonly used halogens are chlorine and bromine, which are added to the PCB materials as flame retardants.
The Risks of Using Halogens in PCBs
The use of halogens in PCBs has been associated with several health and environmental risks:
-
Toxic Fumes: When exposed to high temperatures, such as during a fire, halogenated PCBs can release toxic fumes, including dioxins and furans. These substances are known to cause serious health problems, such as cancer, reproductive disorders, and immune system damage.
-
Environmental Pollution: The disposal of halogenated PCBs can lead to the release of toxic substances into the environment. These substances can contaminate soil, water, and air, posing a threat to wildlife and human health.
-
Occupational Health Hazards: Workers involved in the manufacturing and handling of halogenated PCBs are at risk of exposure to toxic fumes and chemicals, which can lead to various health problems.
What are Halogen-Free PCBs?
Halogen-free PCBs are printed circuit boards that are manufactured without the use of halogenated flame retardants. These PCBs are made using alternative materials that provide similar or better flame-retardant properties while minimizing the environmental and health risks associated with halogens.
Advantages of Halogen-Free PCBs
-
Reduced Environmental Impact: Halogen-free PCBs do not release toxic substances when disposed of, reducing the risk of environmental pollution.
-
Improved Safety: In the event of a fire, halogen-free PCBs do not release toxic fumes, making them safer for both users and firefighters.
-
Compliance with Regulations: Many countries and organizations have implemented regulations and standards that restrict or prohibit the use of halogens in electronic products. By using halogen-free PCBs, manufacturers can ensure compliance with these regulations.
-
Better Recycling Potential: Halogen-free PCBs are easier to recycle, as they do not contain toxic substances that require special handling and disposal procedures.
Materials Used in Halogen-Free PCBs
Several alternative materials are used in the manufacturing of halogen-free PCBs:
-
Phosphorus-based Flame Retardants: These substances provide excellent flame-retardant properties and are considered a safer alternative to halogens.
-
Metal Hydroxides: Aluminum hydroxide and magnesium hydroxide are commonly used as flame retardants in halogen-free PCBs. They work by releasing water vapor when exposed to high temperatures, which helps to extinguish flames.
-
Nitrogen-based Compounds: Melamine and other nitrogen-based compounds can be used as flame retardants in halogen-free PCBs.
-
Ceramic Fillers: Ceramic fillers, such as silica and alumina, can be added to PCB materials to improve their flame-retardant properties.
Material | Advantages | Disadvantages |
---|---|---|
Phosphorus-based Flame Retardants | – Excellent flame-retardant properties | – Potential for moisture absorption |
– Considered safer than halogens | – Higher cost compared to halogenated PCBs | |
Metal Hydroxides | – Non-toxic and environmentally friendly | – Requires higher loading levels |
– Good flame-retardant properties | – Can affect the mechanical properties of PCBs | |
Nitrogen-based Compounds | – Good flame-retardant properties | – Limited compatibility with some PCB materials |
– Low smoke and toxicity | – Potential for moisture absorption | |
Ceramic Fillers | – Excellent thermal stability | – Can increase the weight and thickness of PCBs |
– Good flame-retardant properties | – Higher cost compared to other fillers |
Manufacturing Process of Halogen-Free PCBs
The manufacturing process of halogen-free PCBs is similar to that of traditional PCBs, with a few key differences:
-
Material Selection: The first step in manufacturing halogen-free PCBs is to select the appropriate materials, such as the base substrate, copper foil, and solder mask. These materials must be free of halogens and meet the required flame-retardant standards.
-
Lamination: The selected materials are then laminated together using heat and pressure to form a Multilayer PCB.
-
Drilling: Holes are drilled through the PCB to accommodate components and connectors.
-
Plating: The drilled holes are plated with copper to establish electrical connections between the layers.
-
Etching: The unwanted copper is removed from the PCB surface using a chemical etching process, leaving behind the desired circuit pattern.
-
Solder Mask Application: A solder mask is applied to the PCB surface to protect the copper traces and prevent short circuits.
-
Surface Finishing: The exposed copper areas are coated with a protective layer, such as nickel/gold or immersion tin, to prevent oxidation and improve solderability.
-
Quality Control: The finished PCBs undergo a series of quality control tests to ensure that they meet the required specifications and are free of defects.
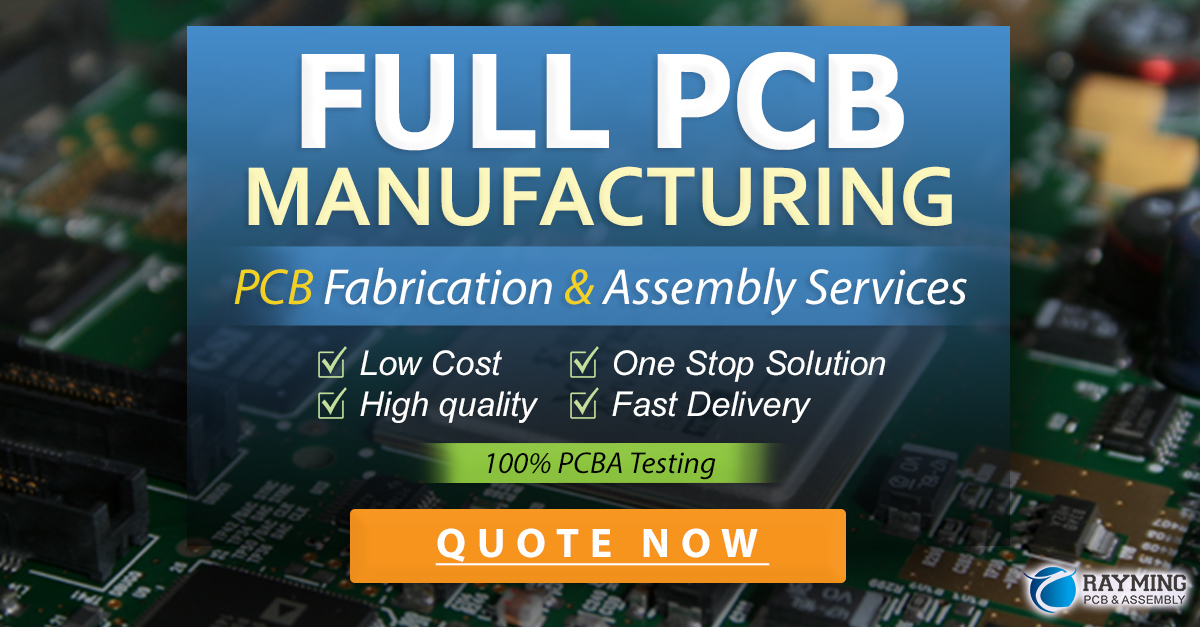
Standards and Regulations for Halogen-Free PCBs
Several international standards and regulations have been developed to ensure the safety and environmental sustainability of halogen-free PCBs:
IEC 61249-2-21
The International Electrotechnical Commission (IEC) has established the IEC 61249-2-21 standard, which defines the requirements for halogen-free materials used in the manufacturing of PCBs. According to this standard, a material is considered halogen-free if it meets the following criteria:
- Chlorine (Cl) content: < 900 ppm
- Bromine (Br) content: < 900 ppm
- Total halogens (Cl + Br) content: < 1500 ppm
RoHS Directive
The Restriction of Hazardous Substances (RoHS) Directive, implemented by the European Union, restricts the use of certain hazardous substances in electrical and electronic equipment, including PCBs. Under the RoHS Directive, the maximum concentration values for halogens are:
- Polybrominated biphenyls (PBBs): 0.1%
- Polybrominated diphenyl ethers (PBDEs): 0.1%
WEEE Directive
The Waste Electrical and Electronic Equipment (WEEE) Directive, also implemented by the European Union, aims to minimize the environmental impact of electronic waste by promoting the recycling and proper disposal of electronic products. Halogen-free PCBs are easier to recycle and dispose of, making them a preferred choice for compliance with the WEEE Directive.
Applications of Halogen-Free PCBs
Halogen-free PCBs are widely used in various industries and applications where environmental sustainability and safety are of utmost importance:
-
Consumer Electronics: Many consumer electronic devices, such as smartphones, laptops, and televisions, are now manufactured using halogen-free PCBs to comply with environmental regulations and meet consumer demand for eco-friendly products.
-
Automotive Electronics: The automotive industry has been increasingly adopting halogen-free PCBs for in-vehicle electronics, such as engine control units, infotainment systems, and safety devices, to enhance vehicle safety and reduce environmental impact.
-
Medical Devices: Halogen-free PCBs are used in the manufacturing of medical devices, such as implantable devices and diagnostic equipment, to ensure patient safety and minimize the risk of toxic substance exposure.
-
Industrial Equipment: Industrial equipment, such as control systems, sensors, and power supplies, often use halogen-free PCBs to improve reliability and reduce the risk of fire and toxic fume release in harsh industrial environments.
-
Aerospace and Defense: The aerospace and defense industries rely on halogen-free PCBs for critical applications, such as avionics, communication systems, and weapons systems, to ensure the highest levels of safety and reliability.
Future Trends in Halogen-Free PCBs
As the demand for eco-friendly and safer electronic products continues to grow, the development and adoption of halogen-free PCBs are expected to increase in the coming years. Some of the future trends in halogen-free PCBs include:
-
Advanced Materials: Researchers and manufacturers are continuously working on developing new halogen-free materials with improved flame-retardant properties, thermal stability, and electrical performance.
-
Nanotechnology: The incorporation of nanomaterials, such as carbon nanotubes and graphene, into halogen-free PCBs can enhance their mechanical, thermal, and electrical properties, leading to the development of high-performance and environmentally friendly PCBs.
-
3D Printing: The use of 3D printing technology in the manufacturing of halogen-free PCBs can enable the creation of complex geometries and reduce material waste, resulting in more efficient and sustainable production processes.
-
Recycling and Circular Economy: As the focus on sustainability and waste reduction increases, the electronics industry is expected to place greater emphasis on the recycling and reuse of halogen-free PCBs, contributing to the development of a circular economy.
Frequently Asked Questions (FAQ)
-
Q: Are halogen-free PCBs more expensive than traditional PCBs?
A: Yes, halogen-free PCBs are generally more expensive than traditional PCBs due to the higher cost of halogen-free materials and the additional processing steps required in their manufacturing. However, the long-term benefits of using halogen-free PCBs, such as improved safety and environmental sustainability, can outweigh the initial cost difference. -
Q: Can halogen-free PCBs be used as a drop-in replacement for traditional PCBs?
A: In most cases, halogen-free PCBs can be used as a direct replacement for traditional PCBs without requiring significant design changes. However, it is essential to consult with the PCB manufacturer to ensure compatibility and to address any specific requirements or challenges associated with the transition to halogen-free PCBs. -
Q: How can I ensure that the PCBs I purchase are truly halogen-free?
A: To ensure that the PCBs you purchase are halogen-free, look for manufacturers that comply with the IEC 61249-2-21 standard and provide certification or test reports confirming the halogen content of their products. Additionally, you can request halogen-free materials from your PCB supplier and specify your requirements during the ordering process. -
Q: Do halogen-free PCBs have any limitations or drawbacks compared to traditional PCBs?
A: Halogen-free PCBs may have some limitations compared to traditional PCBs, such as slightly lower flame-retardant properties or higher moisture absorption. However, these limitations can be addressed through proper material selection and design optimization. In most cases, the benefits of using halogen-free PCBs outweigh any potential drawbacks. -
Q: Can halogen-free PCBs be recycled?
A: Yes, halogen-free PCBs are easier to recycle compared to traditional PCBs that contain halogens. The absence of toxic substances in halogen-free PCBs simplifies the recycling process and reduces the risk of environmental contamination during recycling and disposal.
Conclusion
Halogen-free PCBs have emerged as a safer and more environmentally friendly alternative to traditional PCBs that contain halogenated flame retardants. By eliminating the use of halogens, these PCBs minimize the risk of toxic fume release, environmental pollution, and health hazards associated with halogenated materials. The adoption of halogen-free PCBs is driven by growing consumer awareness, stringent environmental regulations, and the electronics industry’s commitment to sustainability.
As the demand for eco-friendly and safe electronic products continues to rise, the development and use of halogen-free PCBs are expected to grow in the coming years. Manufacturers and designers should stay informed about the latest advancements in halogen-free materials, manufacturing processes, and industry standards to ensure the production of high-quality, reliable, and environmentally sustainable PCBs.
By embracing halogen-free PCBs, the electronics industry can contribute to a greener and safer future, reducing its environmental footprint and promoting the well-being of workers, consumers, and the planet as a whole.
Leave a Reply