Introduction to Glass PCBs
Glass Printed Circuit Boards (PCBs) are an emerging technology that offers a new option for PCB Designers looking for high-performance, reliable, and cost-effective solutions. Glass PCBs are made using a glass substrate instead of the traditional FR-4 material, which provides several advantages over conventional PCBs.
Advantages of Glass PCBs
- High thermal stability
- Excellent dimensional stability
- Low dielectric constant and loss tangent
- High transparency
- Resistance to harsh environments
These properties make glass PCBs ideal for applications that require high-frequency operation, such as 5G networks, automotive radar systems, and aerospace electronics.
Manufacturing Process of Glass PCBs
The manufacturing process of glass PCBs is similar to that of conventional PCBs, with a few key differences:
- Glass substrate preparation
- Copper foil lamination
- Photolithography and etching
- Drilling and plating
- Solder Mask Application and surface finish
Glass Substrate Preparation
The glass substrate is carefully selected based on the desired properties, such as thermal expansion coefficient, dielectric constant, and thickness. The glass is then cleaned and prepared for the subsequent manufacturing steps.
Copper Foil Lamination
A thin layer of copper foil is laminated onto the glass substrate using a high-temperature and high-pressure process. The copper foil adheres to the glass surface, forming a strong bond.
Photolithography and Etching
The desired circuit pattern is transferred onto the copper layer using photolithography. A photoresist is applied, exposed, and developed, leaving the desired pattern. The exposed copper is then etched away, leaving the circuit traces.
Drilling and Plating
Holes are drilled through the glass substrate and copper layer to create vias and Through-holes. The holes are then plated with copper to create electrical connections between layers.
Solder Mask Application and Surface Finish
A solder mask is applied to protect the copper traces and prevent short circuits. Finally, a surface finish, such as ENIG (Electroless Nickel Immersion Gold) or HASL (Hot Air Solder Leveling), is applied to protect the exposed copper and facilitate soldering.
Applications of Glass PCBs
Glass PCBs find applications in various industries due to their unique properties:
- 5G and mmWave communication systems
- Automotive radar and LIDAR
- Aerospace and defense electronics
- Medical devices and imaging systems
- High-speed digital circuits
5G and mmWave Communication Systems
Glass PCBs are particularly suited for 5G and millimeter-wave (mmWave) communication systems due to their low dielectric constant and loss tangent. These properties enable the design of high-frequency circuits with minimal signal loss and distortion.
Automotive Radar and LIDAR
Automotive radar and LIDAR systems require high-frequency operation and tight dimensional tolerances. Glass PCBs offer excellent dimensional stability and low dielectric loss, making them ideal for these applications.
Aerospace and Defense Electronics
Glass PCBs can withstand harsh environments, including extreme temperatures, vibrations, and shocks. This makes them suitable for aerospace and defense electronics, where reliability is critical.
Medical Devices and Imaging Systems
The transparency of glass PCBs allows for the integration of optical components, such as lenses and light guides, directly onto the PCB. This feature is particularly useful in medical devices and imaging systems.
High-Speed Digital Circuits
Glass PCBs’ low dielectric constant and loss tangent enable the design of high-speed digital circuits with reduced signal integrity issues, such as crosstalk and signal reflections.
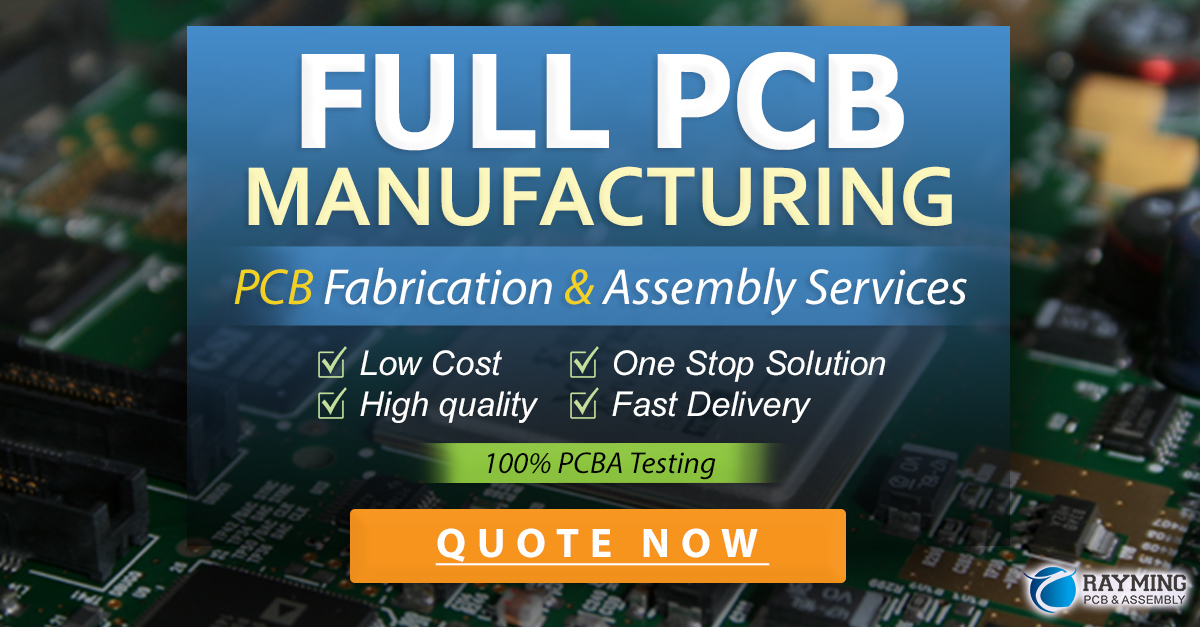
Design Considerations for Glass PCBs
When designing glass PCBs, several factors must be considered to ensure optimal performance and manufacturability:
- Material selection
- Thermal management
- Signal integrity
- Mechanical properties
- Cost
Material Selection
The choice of glass substrate depends on the specific application requirements, such as dielectric constant, thermal expansion coefficient, and transparency. Common glass materials include borosilicate, soda-lime, and fused silica.
Thermal Management
Glass has a lower thermal conductivity compared to traditional PCB materials, which can lead to higher operating temperatures. Proper thermal management techniques, such as using heat sinks and thermal vias, must be employed to ensure reliable operation.
Signal Integrity
The low dielectric constant and loss tangent of glass PCBs enable high-speed signal transmission with minimal distortion. However, proper signal integrity analysis and design techniques, such as Impedance Matching and ground plane design, must be used to optimize performance.
Mechanical Properties
Glass is a brittle material and requires careful handling during manufacturing and assembly. Designers must consider the mechanical stresses and strains that the PCB will experience and design accordingly.
Cost
Glass PCBs are generally more expensive than conventional PCBs due to the specialized materials and manufacturing processes involved. However, the cost can be justified for applications that require the unique properties of glass PCBs.
Challenges and Limitations of Glass PCBs
Despite their numerous advantages, glass PCBs also present some challenges and limitations:
- Brittle nature of glass
- Limited availability of glass materials
- Higher manufacturing costs
- Limited industry experience and knowledge
Brittle Nature of Glass
Glass is a brittle material that can crack or shatter under stress. This property requires careful handling during manufacturing and assembly and may limit the use of glass PCBs in applications with high mechanical stress.
Limited Availability of Glass Materials
The selection of glass materials suitable for PCB manufacturing is currently limited compared to traditional PCB materials. This limitation may restrict the range of applications where glass PCBs can be used.
Higher Manufacturing Costs
The specialized materials and manufacturing processes involved in glass PCB production result in higher costs compared to conventional PCBs. This may limit the adoption of glass PCBs in cost-sensitive applications.
Limited Industry Experience and Knowledge
Glass PCBs are a relatively new technology, and the industry experience and knowledge base are still developing. This may lead to challenges in design, manufacturing, and assembly, as well as a lack of standardization and best practices.
Future Outlook for Glass PCBs
Despite the challenges and limitations, the future outlook for glass PCBs is promising. As the technology matures and the industry gains more experience, it is expected that glass PCBs will find increasing adoption in various applications.
Advancements in Materials and Manufacturing
Ongoing research and development efforts are focused on expanding the range of glass materials suitable for PCB manufacturing and improving the manufacturing processes to reduce costs and increase yields.
Growing Demand for High-Frequency Applications
The increasing demand for high-frequency applications, such as 5G networks and automotive radar systems, is expected to drive the adoption of glass PCBs, which offer superior high-frequency performance compared to conventional PCBs.
Potential for New Applications
The unique properties of glass PCBs, such as transparency and resistance to harsh environments, may enable new applications that are not possible with traditional PCBs. For example, the integration of optical components onto glass PCBs could lead to novel sensor and imaging systems.
Conclusion
Glass PCBs offer a new and exciting option for PCB designers looking for high-performance, reliable, and cost-effective solutions. With their unique properties, such as high thermal stability, excellent dimensional stability, and low dielectric loss, glass PCBs are particularly suited for applications that require high-frequency operation and resistance to harsh environments.
While there are challenges and limitations associated with glass PCBs, ongoing research and development efforts are expected to address these issues and expand the range of applications where glass PCBs can be used. As the technology matures and the industry gains more experience, glass PCBs are poised to become an increasingly important part of the electronics landscape.
FAQ
-
Q: What are the main advantages of glass PCBs compared to traditional PCBs?
A: Glass PCBs offer several advantages, including high thermal stability, excellent dimensional stability, low dielectric constant and loss tangent, high transparency, and resistance to harsh environments. -
Q: What are some common applications for glass PCBs?
A: Glass PCBs find applications in various industries, such as 5G and mmWave communication systems, automotive radar and LIDAR, aerospace and defense electronics, medical devices and imaging systems, and high-speed digital circuits. -
Q: How do the manufacturing processes for glass PCBs differ from those of conventional PCBs?
A: The manufacturing process for glass PCBs is similar to that of conventional PCBs, with a few key differences, such as glass substrate preparation, copper foil lamination, photolithography and etching, drilling and plating, and solder mask application and surface finish. -
Q: What are some of the design considerations when working with glass PCBs?
A: When designing glass PCBs, several factors must be considered, including material selection, thermal management, signal integrity, mechanical properties, and cost. -
Q: What is the future outlook for glass PCBs in the electronics industry?
A: The future outlook for glass PCBs is promising, with ongoing research and development efforts focused on expanding the range of glass materials, improving manufacturing processes, and enabling new applications. As the technology matures and the industry gains more experience, glass PCBs are expected to find increasing adoption in various applications.
Leave a Reply