What is Through-hole Assembly?
Through-hole assembly, also known as through-hole technology (THT), is a method of mounting electronic components on a printed circuit board (PCB) by inserting component leads through holes drilled in the board and soldering them to pads on the opposite side. This assembly technique has been widely used since the early days of PCB manufacturing and remains relevant today for certain applications, despite the growing popularity of surface mount technology (SMT).
Advantages of Through-hole Assembly
Through-hole assembly offers several advantages over other assembly methods:
-
Mechanical Strength: Components mounted using through-hole technology have stronger mechanical bonds to the PCB, as the leads are inserted through the board and soldered on the opposite side. This makes through-hole assemblies more resistant to vibration and physical stress.
-
Ease of Manual Assembly: Through-hole components are easier to handle and place manually compared to their surface-mount counterparts. This makes through-hole assembly a preferred choice for low-volume production, prototyping, and hobbyist projects.
-
Visual Inspection: Soldered joints in through-hole assembly are visible on the component side of the PCB, making it easier to visually inspect the quality of the solder connections.
-
High Power Handling: Through-hole components often have higher power handling capabilities due to their larger size and better heat dissipation properties.
Disadvantages of Through-hole Assembly
Despite its advantages, through-hole assembly also has some drawbacks:
-
Board Space: Through-hole components require holes to be drilled in the PCB, which takes up valuable board space. This limits the component density and makes it challenging to design compact circuits.
-
Higher Manufacturing Costs: Drilling holes in the PCB adds an extra step to the manufacturing process, increasing production time and costs compared to surface mount technology.
-
Limited Component Availability: As surface mount technology has become more prevalent, the variety of through-hole components available in the market has decreased, making it harder to source components for new designs.
Through-hole Assembly Process
The through-hole assembly process involves several steps, from PCB preparation to final inspection. Here’s a detailed look at each stage:
1. PCB Preparation
Before assembling components, the PCB must be prepared:
- Drilling: Holes are drilled in the PCB according to the component layout. The Hole Size depends on the lead diameter of the components.
- Deburring: After drilling, any burrs or rough edges around the holes are removed to ensure proper component fitment.
- Cleaning: The PCB is cleaned to remove any dirt, grease, or contaminants that may affect the soldering process.
2. Component Placement
Once the PCB is prepared, components are placed on the board:
- Manual Placement: For low-volume production or prototyping, components are placed manually using tweezers or a vacuum pen. The component leads are inserted through the corresponding holes on the PCB.
- Automatic Insertion: In high-volume production, automatic insertion machines are used to place components rapidly and accurately. These machines pick and place components using programmed coordinates.
3. Soldering
After component placement, the leads are soldered to the pads on the opposite side of the PCB:
- Wave Soldering: In wave soldering, the PCB is passed over a molten solder wave, which solders the component leads to the pads. This method is suitable for high-volume production.
- Hand Soldering: For low-volume or prototype assemblies, soldering is done manually using a soldering iron. The soldering iron is used to heat the component lead and pad while applying solder.
4. Inspection and Cleaning
After soldering, the assembLED PCB undergoes inspection and cleaning:
- Visual Inspection: The solder joints are visually inspected for quality, looking for any bridging, Cold Solder Joints, or insufficient solder.
- Automated Optical Inspection (AOI): In high-volume production, AOI systems are used to quickly and accurately detect soldering defects.
- Cleaning: Any flux residue or contaminants left behind from the soldering process are cleaned using solvents or cleaning agents.
5. Testing and Rework
Finally, the assembled PCB is tested and reworked if necessary:
- Functional Testing: The PCB is powered on and tested for proper functionality, ensuring that all components are working as intended.
- Rework: If any defects or issues are found during testing, the PCB is reworked. This may involve desoldering and replacing faulty components or fixing soldering defects.
Through-hole Component Types
Through-hole components come in various packages and sizes. Some common types include:
Axial Lead Components
Axial lead components have leads extending from opposite ends of the component body. Examples include:
- Resistors
- Capacitors
- Diodes
- Inductors
Radial Lead Components
Radial lead components have leads extending from the same side of the component body. Examples include:
- Electrolytic Capacitors
- Ceramic Capacitors
- LEDs
DIP (Dual Inline Package) Components
DIP components have two parallel rows of leads extending from the component body. Examples include:
- Integrated Circuits (ICs)
- Sockets
- Connectors
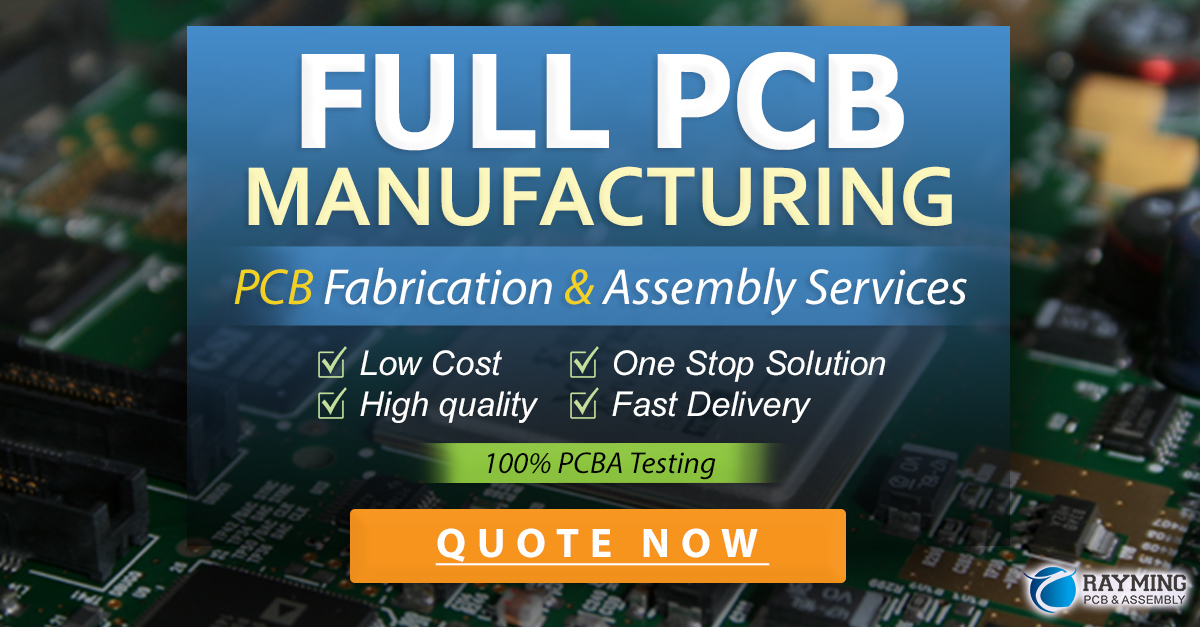
Through-hole Assembly Best Practices
To ensure reliable and high-quality through-hole assemblies, follow these best practices:
-
Use the correct hole size: Ensure that the hole diameter is appropriate for the component lead size. Holes that are too small can make insertion difficult, while oversized holes may result in weak solder joints.
-
Maintain lead spacing: Follow the recommended lead spacing for components to avoid short circuits and ensure proper fitment.
-
Trim leads after soldering: After soldering, trim the excess lead length to prevent short circuits and improve the overall appearance of the assembly.
-
Use the appropriate soldering temperature: Set the soldering iron temperature according to the solder type and component requirements. Excessive heat can damage components or cause solder joint defects.
-
Inspect solder joints: Regularly inspect solder joints for quality, looking for signs of bridging, cold solder joints, or insufficient solder.
-
Use flux: Apply flux to the component leads and pads before soldering to improve solder wetting and create stronger solder joints.
-
Follow ESD precautions: Use appropriate electrostatic discharge (ESD) protection measures, such as grounded workstations and wrist straps, to prevent damage to sensitive components.
Through-hole Assembly vs. Surface Mount Technology
Through-hole assembly and surface mount technology (SMT) are the two primary methods of assembling electronic components on PCBs. Here’s a comparison of the two technologies:
Aspect | Through-hole Assembly | Surface Mount Technology |
---|---|---|
Component Mounting | Leads inserted through holes in the PCB | Components placed directly on the PCB surface |
Board Space | Requires more board space due to drilled holes | Allows for higher component density and smaller board sizes |
Manufacturing Cost | Higher due to additional drilling and soldering steps | Lower due to faster assembly and fewer manufacturing steps |
Component Availability | Limited, as SMT components become more prevalent | Wide variety of components available |
Mechanical Strength | Stronger mechanical bonds due to leads extending through the board | Weaker mechanical bonds, but can be improved with additional adhesives |
Rework and Repair | Easier to rework and replace individual components | More challenging to rework and replace components due to smaller sizes and closer spacing |
Suitability | Ideal for low-volume production, prototyping, and high-power applications | Ideal for high-volume production, compact designs, and high-speed applications |
In modern electronics manufacturing, SMT has largely replaced through-hole assembly due to its advantages in terms of board space, manufacturing cost, and component availability. However, through-hole assembly remains relevant for certain applications, such as high-power devices, connectors, and some legacy designs.
Frequently Asked Questions (FAQ)
-
Q: Can through-hole and surface mount components be used together on the same PCB?
A: Yes, it is possible to use both through-hole and surface mount components on the same PCB. This is called a mixed-technology assembly or hybrid assembly. However, it is essential to consider the manufacturing process and ensure compatibility between the two assembly methods. -
Q: What is the difference between wave soldering and hand soldering in through-hole assembly?
A: Wave soldering is an automated process where the PCB is passed over a molten solder wave, which solders the component leads to the pads. It is suitable for high-volume production. Hand soldering, on the other hand, is a manual process using a soldering iron and is ideal for low-volume production, prototyping, or rework. -
Q: Can through-hole components be used in high-frequency applications?
A: Through-hole components can be used in high-frequency applications, but their performance may be limited compared to surface mount components. The longer leads of through-hole components can introduce parasitic inductance and capacitance, which can affect signal integrity at high frequencies. For high-frequency applications, surface mount components are generally preferred. -
Q: How can I ensure the quality of solder joints in through-hole assembly?
A: To ensure the quality of solder joints, follow best practices such as using the correct hole size, maintaining lead spacing, applying flux, and using the appropriate soldering temperature. Visually inspect the solder joints for any defects, such as bridging, cold solder joints, or insufficient solder. In high-volume production, automated optical inspection (AOI) systems can be used for rapid and accurate defect detection. -
Q: Are there any environmental concerns associated with through-hole assembly?
A: One of the main environmental concerns associated with through-hole assembly is the use of lead-based solder. Lead is a toxic substance that can have harmful effects on human health and the environment. To address this concern, many manufacturers have switched to Lead-Free Solder alloys, such as tin-silver-copper (SAC) alloys, which are more environmentally friendly. Additionally, proper disposal and recycling of electronic waste, including through-hole assemblies, are essential to minimize environmental impact.
Conclusion
Through-hole assembly remains an essential technology in Electronic Manufacturing, despite the growing popularity of surface mount technology. Its advantages in terms of mechanical strength, ease of manual assembly, and high power handling make it suitable for various applications, including low-volume production, prototyping, and high-power devices.
By understanding the through-hole assembly process, component types, and best practices, electronics manufacturers and hobbyists can create reliable and high-quality assemblies. As technology advances, it is crucial to consider the specific requirements of each project and choose the most appropriate assembly method, whether it be through-hole, surface mount, or a combination of both.
Leave a Reply