Introduction to Flexible Printed Circuit Board Assembly (FPCBA)
Flexible Printed Circuit Board Assembly (FPCBA) is a cutting-edge technology that has revolutionized the electronics industry. FPCBAs offer numerous advantages over traditional rigid PCBs, including increased flexibility, reduced weight and size, and improved reliability. As we look ahead to 2024, it’s clear that FPCBA will continue to play a crucial role in the development of new electronic devices and systems.
What is a Flexible Printed Circuit Board?
A flexible printed circuit board (FPCB) is a thin, lightweight, and flexible circuit board that can be bent, folded, or twisted without damaging the electrical components. FPCBs are made from a flexible substrate material, such as polyimide or polyester, and are coated with a conductive material, such as copper, to create the circuit pattern.
Advantages of FPCBs
FPCBs offer several advantages over traditional rigid PCBs:
- Flexibility: FPCBs can be bent, folded, or twisted to fit into tight spaces or conform to irregular shapes.
- Reduced weight and size: FPCBs are thinner and lighter than rigid PCBs, making them ideal for portable devices and aerospace applications.
- Improved reliability: FPCBs are more resistant to vibration and shock than rigid PCBs, making them more reliable in harsh environments.
- Increased design freedom: FPCBs allow for more creative and innovative product designs, as they can be shaped to fit the contours of the device.
FPCBA Market Trends and Forecasts
Market Size and Growth
The global FPCBA market is expected to reach $27.5 billion by 2024, growing at a CAGR of 11.2% from 2019 to 2024. The growth of the FPCBA market is driven by several factors, including the increasing demand for smaller, lighter, and more flexible electronic devices, the growth of the Internet of Things (IoT), and the increasing adoption of FPCBAs in the automotive and healthcare industries.
Market Segmentation
The FPCBA market can be segmented based on several factors, including:
- Application: Consumer electronics, automotive, healthcare, aerospace and defense, others
- Type: Single-sided, double-sided, multi-layer
- Region: North America, Europe, Asia-Pacific, Rest of the World
Application | Market Share (2024) |
---|---|
Consumer Electronics | 35% |
Automotive | 25% |
Healthcare | 20% |
Aerospace & Defense | 15% |
Others | 5% |
Key Players in the FPCBA Market
Some of the key players in the FPCBA market include:
- Nippon Mektron
- Fujikura
- Flexium Interconnect
- Zhen Ding Technology
- Nitto Denko
- Interflex
- Sumitomo Electric Industries
- Career Technology
- Multi-Fineline Electronix
- Ichia Technologies
FPCBA Manufacturing Process
The FPCBA manufacturing process involves several steps, including:
- Circuit Design: The circuit design is created using computer-aided design (CAD) software.
- Substrate Preparation: The flexible substrate material is cut to size and cleaned.
- Copper Lamination: A thin layer of copper is laminated onto the substrate.
- Circuit Patterning: The circuit pattern is etched onto the copper layer using photolithography.
- Cover Layer Application: A cover layer is applied to protect the circuit pattern.
- Solder Mask Application: A solder mask is applied to protect the copper traces from oxidation and short circuits.
- Surface Finishing: A surface finish, such as gold or nickel, is applied to the exposed copper areas to prevent oxidation and improve solderability.
- Component Assembly: The electronic components are mounted onto the FPCBA using Surface Mount Technology (SMT) or Through-hole technology (THT).
- Testing and Inspection: The assembled FPCBA is tested and inspected for quality and functionality.
Challenges in FPCBA Manufacturing
Despite the advantages of FPCBAs, there are several challenges in the manufacturing process, including:
- Handling: FPCBs are thin and flexible, making them difficult to handle during the manufacturing process.
- Alignment: Ensuring proper alignment of the circuit pattern and components can be challenging due to the flexibility of the substrate.
- Soldering: Soldering components onto FPCBAs requires special techniques and equipment to avoid damaging the flexible substrate.
- Reliability: Ensuring the reliability of FPCBAs in harsh environments requires careful design and testing.
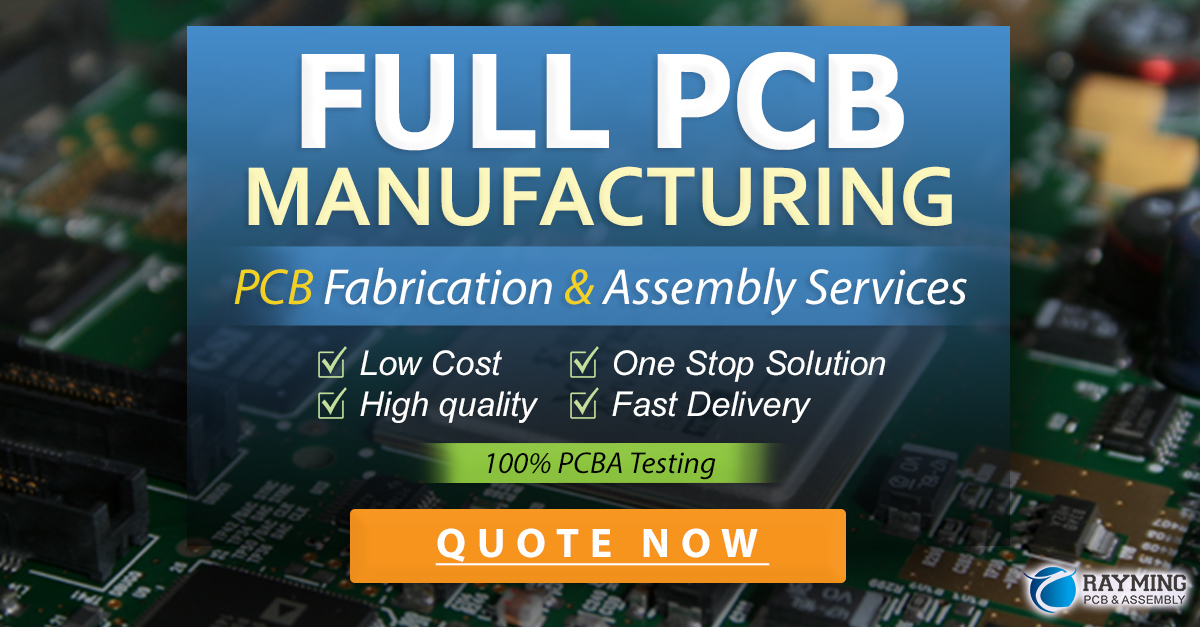
Applications of FPCBAs
FPCBAs are used in a wide range of applications, including:
Consumer Electronics
FPCBAs are widely used in consumer electronics, such as smartphones, tablets, laptops, and wearables. The flexibility and reduced size and weight of FPCBAs make them ideal for these applications, where space is limited and weight is a critical factor.
Automotive
FPCBAs are increasingly being used in the automotive industry, particularly in advanced driver assistance systems (ADAS), infotainment systems, and electric vehicles. The flexibility and reliability of FPCBAs make them well-suited for the harsh environments found in vehicles.
Healthcare
FPCBAs are used in a variety of medical devices, including wearable sensors, implantable devices, and diagnostic equipment. The flexibility and biocompatibility of FPCBAs make them ideal for these applications, where they must conform to the contours of the body and be safe for long-term use.
Aerospace and Defense
FPCBAs are used in aerospace and defense applications, such as satellites, aircraft, and military equipment. The reduced weight and size of FPCBAs make them ideal for these applications, where every gram counts and space is at a premium.
Future of FPCBA Technology
As we look ahead to 2024 and beyond, it’s clear that FPCBA technology will continue to evolve and advance. Some of the key trends and developments to watch include:
Miniaturization
As electronic devices continue to shrink in size, FPCBAs will need to become even smaller and more flexible. This will require advances in materials science, manufacturing processes, and design tools.
Increased Functionality
FPCBAs will need to incorporate more functionality, such as sensors, antennas, and energy harvesting components, to meet the demands of new applications and use cases.
Advanced Materials
New materials, such as graphene and carbon nanotubes, may be used to create even thinner and more flexible FPCBAs with improved electrical and thermal properties.
3D Printing
3D printing technology may be used to create complex, three-dimensional FPCBAs with embedded components and circuitry.
Sustainability
As concerns about electronic waste and sustainability continue to grow, FPCBAs will need to be designed for recyclability and reuse.
Frequently Asked Questions (FAQs)
- What is the difference between FPCBs and rigid PCBs?
-
FPCBs are thin, lightweight, and flexible, while rigid PCBs are thick, heavy, and rigid. FPCBs can be bent, folded, or twisted, while rigid PCBs cannot.
-
What are the advantages of using FPCBAs?
-
FPCBAs offer several advantages, including increased flexibility, reduced weight and size, improved reliability, and increased design freedom.
-
What are the challenges in manufacturing FPCBAs?
-
The challenges in manufacturing FPCBAs include handling the thin and flexible substrate, ensuring proper alignment of the circuit pattern and components, soldering components without damaging the substrate, and ensuring reliability in harsh environments.
-
What are some common applications of FPCBAs?
-
FPCBAs are commonly used in consumer electronics, automotive, healthcare, and aerospace and defense applications.
-
What are some future trends and developments in FPCBA technology?
- Future trends and developments in FPCBA technology include miniaturization, increased functionality, advanced materials, 3D printing, and sustainability.
Conclusion
Flexible Printed Circuit Board Assembly (FPCBA) is a game-changing technology that has transformed the electronics industry. As we look ahead to 2024, it’s clear that FPCBA will continue to play a crucial role in the development of new electronic devices and systems. With its numerous advantages, including increased flexibility, reduced weight and size, and improved reliability, FPCBA is well-positioned to meet the demands of an increasingly connected and mobile world. However, there are also several challenges that must be addressed, including manufacturing processes, reliability, and sustainability. By working together to overcome these challenges and push the boundaries of what’s possible with FPCBA technology, we can create a brighter, more innovative future for the electronics industry and beyond.
Leave a Reply