Overview of Surface Mount Technology
Surface Mount Technology involves the placement of electronic components directly onto the surface of a PCB, as opposed to the traditional through-hole technology, where components are inserted into drilled holes and soldered on the opposite side of the board. SMT components are typically smaller and have shorter leads or no leads at all, allowing for more compact designs and increased circuit density.
Benefits of SMT
- Miniaturization: SMT allows for the production of smaller electronic devices, as components can be placed closer together on the PCB.
- Increased reliability: SMT components have shorter leads, reducing the risk of damage during handling and vibration.
- Faster assembly: Automated SMT Assembly processes enable faster production rates compared to through-hole technology.
- Lower costs: SMT requires fewer drilled holes and less manual labor, resulting in lower manufacturing costs.
- Improved performance: Shorter leads and closer component placement reduce signal interference and improve overall circuit performance.
SMT Components
SMT components are designed specifically for surface mounting and come in various package types. Some common SMT component packages include:
- Chip resistors and capacitors
- Small Outline Integrated Circuits (SOIC)
- Quad Flat Packages (QFP)
- Ball Grid Arrays (BGA)
- Leadless Chip Carriers (LCC)
These components are typically smaller than their through-hole counterparts and have flat, solderable terminations or leads that are compatible with the SMT assembly process.
SMT Manufacturing Process
The SMT manufacturing process involves several key steps:
- PCB design and fabrication
- Solder paste application
- Component placement
- Reflow soldering
- Inspection and testing
PCB Design and Fabrication
The first step in the SMT process is designing the PCB Layout using computer-aided design (CAD) software. The layout must consider the component footprints, spacing, and routing requirements. Once the design is finalized, the PCB is fabricated with copper traces, solder mask, and silkscreen markings.
Solder Paste Application
Solder paste, a mixture of tiny solder particles and flux, is applied to the PCB’s surface using a stencil or screen printing process. The stencil has openings that correspond to the component pads on the PCB, allowing the solder paste to be deposited precisely where needed.
Component Placement
SMT components are placed onto the solder paste-coated pads using automated Pick-and-place machines. These machines use vacuum nozzles or grippers to pick up components from feeders and place them accurately on the PCB. High-speed placement machines can place thousands of components per hour.
Reflow Soldering
After component placement, the PCB undergoes reflow soldering. The board is passed through a reflow oven, which heats the solder paste to its melting point. The molten solder then flows around the component leads, creating a strong mechanical and electrical connection. The reflow process is carefully controlled to ensure proper solder joint formation and to prevent component damage.
Inspection and Testing
Once the reflow soldering process is complete, the PCB undergoes visual inspection and automated optical inspection (AOI) to detect any defects, such as missing components, misaligned components, or solder bridging. Electrical testing may also be performed to verify the functionality of the assembLED Circuit.
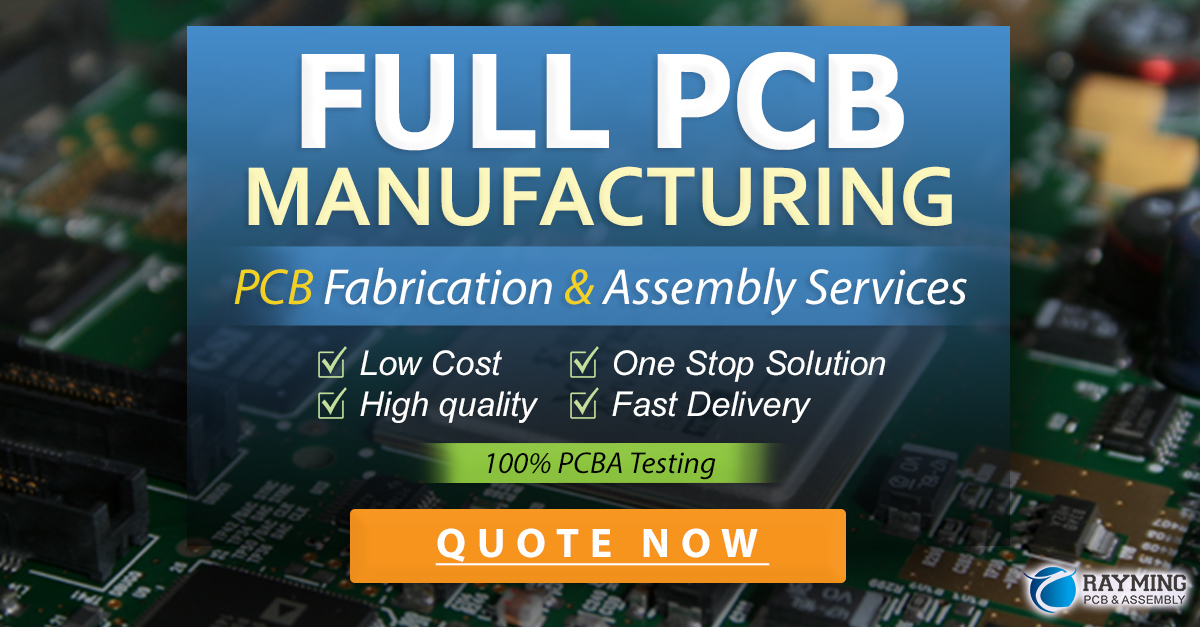
Advantages of SMT
Surface Mount Technology offers several advantages over traditional through-hole technology:
- Space savings: SMT allows for more compact designs, as components can be placed on both sides of the PCB and spaced closer together.
- Weight reduction: SMT components are generally smaller and lighter than through-hole components, resulting in overall weight savings.
- Improved high-frequency performance: Shorter component leads and closer spacing reduce parasitic inductance and capacitance, enhancing high-frequency performance.
- Automated assembly: SMT is well-suited for automated assembly processes, leading to faster production rates and lower labor costs.
- Increased design flexibility: SMT allows for more complex and dense circuit designs, enabling the development of advanced electronic devices.
Challenges and Considerations
While SMT offers numerous benefits, there are also some challenges and considerations to keep in mind:
- Component handling: SMT components are small and delicate, requiring careful handling and storage to prevent damage.
- Thermal management: The increased component density in SMT designs can lead to higher heat generation, necessitating proper thermal management techniques.
- Rework and repair: Reworking or repairing SMT assemblies can be more challenging than through-hole assemblies due to the smaller component sizes and tighter spacing.
- Moisture sensitivity: Some SMT components are moisture-sensitive and require proper storage and handling to prevent damage during the reflow soldering process.
Applications of SMT
Surface Mount Technology is widely used in various electronic applications, including:
- Consumer electronics: Smartphones, tablets, laptops, and wearables
- Automotive electronics: Engine control units, infotainment systems, and sensors
- Industrial electronics: Process control systems, automation equipment, and instrumentation
- Medical devices: Implantable devices, diagnostic equipment, and monitoring systems
- Aerospace and defense: Avionics, satellite systems, and military communication devices
The adoption of SMT has enabled the development of more advanced, compact, and reliable electronic devices across these industries.
Future Trends in SMT
As electronic devices continue to evolve, Surface Mount Technology is also advancing to meet new challenges and demands. Some future trends in SMT include:
- Miniaturization: The development of even smaller SMT components and package types to enable further device miniaturization.
- Advanced materials: The use of new materials, such as low-temperature co-fired ceramics (LTCC) and high-density interconnect (HDI) substrates, to enhance circuit performance and reliability.
- 3D packaging: The integration of multiple IC chips and components in a single package using 3D stacking techniques to increase functionality and reduce footprint.
- Flexible and stretchable electronics: The development of SMT processes compatible with flexible and stretchable substrates for wearable and implantable devices.
- Increased automation: The adoption of more advanced automation technologies, such as robotic assembly systems and machine vision, to improve productivity and quality control.
Frequently Asked Questions (FAQ)
-
Q: What is the difference between Surface Mount Technology and through-hole technology?
A: Surface Mount Technology involves mounting components directly onto the surface of a PCB, while through-hole technology requires components to be inserted into drilled holes and soldered on the opposite side of the board. SMT allows for smaller, more densely packed designs compared to through-hole technology. -
Q: Can SMT components be soldered using traditional soldering methods?
A: While it is possible to hand-solder SMT components, it is more challenging and time-consuming than soldering through-hole components. SMT is designed for automated assembly processes, such as reflow soldering, which ensures consistent and reliable solder joint formation. -
Q: Are SMT components more expensive than through-hole components?
A: In general, SMT components are less expensive than their through-hole counterparts due to their smaller size and the reduced material usage in their packaging. Additionally, the automated SMT assembly process leads to lower manufacturing costs compared to manual through-hole assembly. -
Q: Can SMT be used for high-power applications?
A: Yes, SMT can be used for high-power applications, but proper thermal management techniques must be employed. This may include the use of heat sinks, thermal vias, or other cooling methods to dissipate heat generated by high-power components effectively. -
Q: Is it possible to mix SMT and through-hole components on the same PCB?
A: Yes, it is possible to have a mixed-technology PCB that incorporates both SMT and through-hole components. This is often done to accommodate components that are not available in SMT packages or to meet specific design requirements. However, the assembly process for mixed-technology boards may be more complex and require additional steps.
Conclusion
Surface Mount Technology has transformed the electronics industry by enabling the production of smaller, lighter, and more reliable electronic devices. By mounting components directly onto the surface of a PCB, SMT allows for increased circuit density, improved performance, and faster assembly processes. As electronic devices continue to advance, SMT will play a crucial role in meeting the ever-growing demands for miniaturization, functionality, and reliability.
Aspect | Surface Mount Technology (SMT) | Through-Hole Technology (THT) |
---|---|---|
Component mounting | Surface-mounted | Inserted into drilled holes |
Component size | Smaller | Larger |
Circuit density | Higher | Lower |
Assembly process | Automated | Often manual |
Manufacturing costs | Lower | Higher |
Solder joint formation | Reflow soldering | Wave or hand soldering |
Reliability | Higher | Lower |
Rework and repair | More challenging | Easier |
Table 1: Comparison of Surface Mount Technology and Through-Hole Technology
By understanding the fundamentals of Surface Mount Technology, its advantages, and its applications, engineers and manufacturers can leverage this technology to design and produce cutting-edge electronic devices that meet the demands of today’s rapidly evolving market.
Leave a Reply