Introduction to Aluminum PCB
An Aluminum PCB, also known as a metal core PCB or a thermal management PCB, is a type of printed circuit board that uses aluminum as the base material instead of the traditional FR-4 substrate. The aluminum base provides excellent thermal conductivity, allowing for efficient heat dissipation from electronic components. This makes Aluminum PCBs ideal for applications that generate significant amounts of heat, such as high-power LED lighting, automotive electronics, and power electronics.
Advantages of Aluminum PCB
- Enhanced thermal management
- Improved reliability and longevity
- Reduced size and weight
- Cost-effective solution for high-power applications
Structure of an Aluminum PCB
An Aluminum PCB consists of several layers:
-
Dielectric Layer: This layer is an electrical insulator that separates the copper circuit layer from the aluminum base. Common dielectric materials include polyimide, epoxy, and ceramic.
-
Copper Circuit Layer: The copper layer is where the electronic components are mounted and the electrical connections are made. The thickness of the copper layer can vary depending on the application and the required current carrying capacity.
-
Aluminum Base: The aluminum base serves as a heat sink, efficiently dissipating heat generated by the electronic components. The thickness of the aluminum base can range from 0.5mm to 3mm or more, depending on the thermal management requirements.
Layer | Material | Thickness (mm) |
---|---|---|
Copper Circuit Layer | Copper | 0.035 – 0.350 |
Dielectric Layer | Polyimide, Epoxy, Ceramic | 0.025 – 0.100 |
Aluminum Base | Aluminum | 0.500 – 3.000+ |
Manufacturing Process of Aluminum PCB
The manufacturing process of an Aluminum PCB involves several steps:
-
Cleaning and Surface Treatment: The aluminum base is cleaned and treated to improve adhesion between the aluminum and the dielectric layer.
-
Lamination: The dielectric layer is laminated onto the aluminum base using heat and pressure.
-
Drilling: Holes are drilled through the laminated board for component mounting and electrical connections.
-
Plating: The drilled holes are plated with copper to establish electrical connections between layers.
-
Etching: The copper circuit layer is etched to create the desired circuit pattern.
-
Solder mask and Silkscreen: A solder mask is applied to protect the copper circuits, and a silkscreen layer is added for component labeling and identification.
-
Surface Finish: A surface finish, such as HASL, ENIG, or OSP, is applied to the exposed copper areas to improve solderability and protect against oxidation.
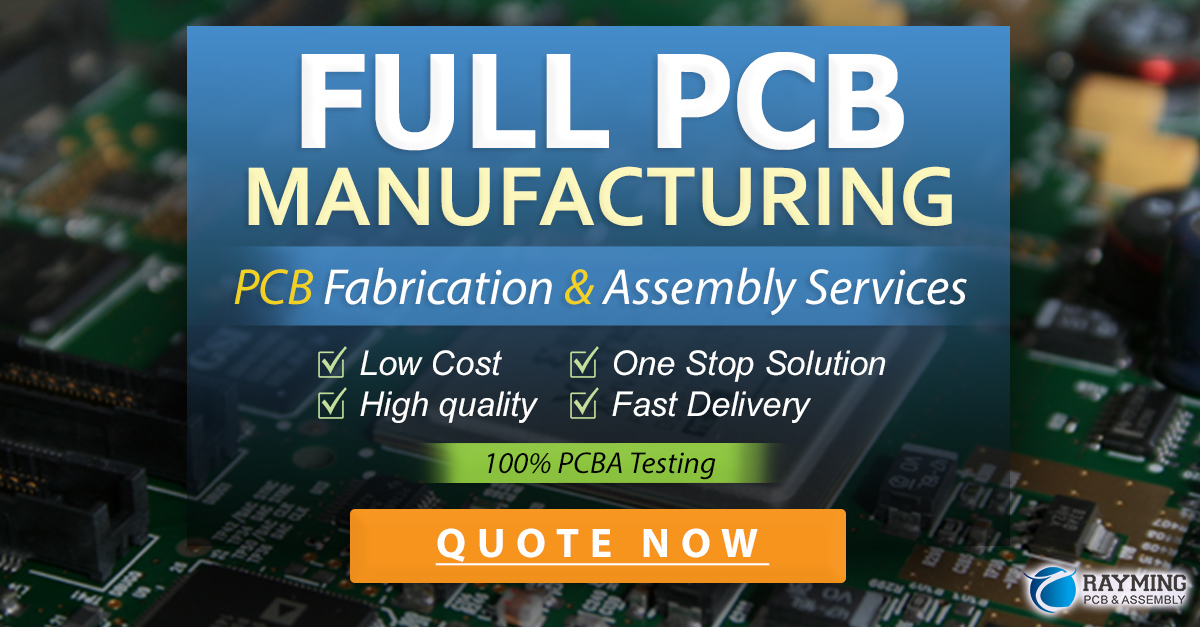
Applications of Aluminum PCB
Aluminum PCBs are used in a wide range of applications that require efficient thermal management:
-
LED Lighting: High-power LED lighting systems generate significant amounts of heat, which can reduce the lifespan and efficiency of the LEDs. Aluminum PCBs help dissipate this heat, ensuring optimal performance and longevity.
-
Automotive Electronics: Electronic components in vehicles, such as engine control units, power inverters, and battery management systems, are subjected to harsh environmental conditions and high temperatures. Aluminum PCBs provide the necessary thermal management to ensure reliable operation in these challenging environments.
-
Power Electronics: Power converters, motor drives, and other power electronic devices generate substantial heat due to high current flows. Aluminum PCBs effectively dissipate this heat, preventing component failure and improving system reliability.
-
Industrial Control Systems: Industrial control systems often operate in high-temperature environments and require robust thermal management solutions. Aluminum PCBs offer a reliable and cost-effective option for these applications.
-
Aerospace and Defense: Electronic systems in aerospace and defense applications must withstand extreme temperatures and harsh environmental conditions. Aluminum PCBs provide the necessary thermal management and reliability for these critical systems.
Comparison of Aluminum PCB with Traditional FR-4 PCB
Characteristic | Aluminum PCB | FR-4 PCB |
---|---|---|
Thermal Conductivity | High (150-200 W/mK) | Low (0.3-0.4 W/mK) |
Electrical Insulation | Requires dielectric layer | Inherently insulating |
Weight | Heavier than FR-4 | Lighter than Aluminum PCB |
Flexibility | Limited flexibility due to aluminum base | More flexible than Aluminum PCB |
Cost | Higher cost due to additional materials and processing | Lower cost than Aluminum PCB |
Applications | High-power, thermal management critical | General-purpose, low-power |
Design Considerations for Aluminum PCB
When designing an Aluminum PCB, several factors must be considered:
-
Thermal Management: The primary purpose of using an Aluminum PCB is to efficiently dissipate heat. Designers must carefully consider the placement of components, the thickness of the aluminum base, and the layout of the copper circuit layer to optimize thermal performance.
-
Dielectric Material Selection: The choice of dielectric material is critical in an Aluminum PCB. The dielectric must provide adequate electrical insulation while allowing for efficient heat transfer from the copper layer to the aluminum base. Common dielectric materials include polyimide, epoxy, and ceramic.
-
Copper Thickness: The thickness of the copper circuit layer must be carefully selected based on the current carrying requirements of the application. Thicker copper layers can carry more current but may increase the overall thickness of the PCB.
-
Coefficient of Thermal Expansion (CTE): Aluminum and copper have different CTEs, which can lead to thermal stress and warpage during temperature cycles. Designers must consider this and select materials and layouts that minimize CTE mismatches.
-
Mounting and Assembly: Aluminum PCBs require special considerations for component mounting and assembly. The use of thermally conductive adhesives, thermal interface materials, and appropriate soldering techniques is essential for optimal thermal performance and reliability.
Frequently Asked Questions (FAQ)
-
Q: What is the difference between an Aluminum PCB and a Flexible PCB (FPC)?
A: An Aluminum PCB uses an aluminum base for thermal management, while a Flexible PCB (FPC) uses a thin, flexible substrate material for applications requiring bendability or flexibility. Aluminum PCBs are rigid and prioritize thermal performance, while FPCs prioritize flexibility and are typically used in compact or mobile devices. -
Q: Can Aluminum PCBs be used in high-frequency applications?
A: Yes, Aluminum PCBs can be used in high-frequency applications, but special considerations must be made for the dielectric material and the layout of the copper circuit layer. The dielectric material must have a stable dielectric constant and low loss tangent at high frequencies, and the circuit layout must be optimized to minimize signal integrity issues. -
Q: How does the cost of an Aluminum PCB compare to a traditional FR-4 PCB?
A: Aluminum PCBs are typically more expensive than traditional FR-4 PCBs due to the additional materials and processing steps required. However, for applications that require superior thermal management, the added cost of an Aluminum PCB can be justified by improved performance, reliability, and longevity. -
Q: Can Aluminum PCBs be manufactured with multiple copper layers?
A: Yes, Aluminum PCBs can be manufactured with multiple copper layers, allowing for more complex circuit designs and higher component densities. However, the addition of multiple copper layers increases the overall thickness of the PCB and may impact thermal performance. -
Q: Are there any limitations on the components that can be used with Aluminum PCBs?
A: In general, most standard electronic components can be used with Aluminum PCBs. However, some components may require special thermal management considerations, such as the use of thermally conductive adhesives or heat sinks. Additionally, some components may be sensitive to the higher thermal conductivity of the aluminum base, requiring additional insulation or spacing.
Conclusion
Aluminum PCBs offer a unique solution for applications requiring efficient thermal management and high reliability. By combining the thermal conductivity of aluminum with the electrical insulation of a dielectric layer, Aluminum PCBs enable the design of compact, high-power electronic systems that can withstand harsh environmental conditions. While Aluminum PCBs may have a higher initial cost compared to traditional FR-4 PCBs, their superior thermal performance and longevity often justify the investment in applications where thermal management is critical.
As electronic systems continue to push the boundaries of power density and performance, the demand for advanced thermal management solutions like Aluminum PCBs will likely continue to grow. By understanding the structure, manufacturing process, and design considerations of Aluminum PCBs, engineers and designers can leverage this technology to create innovative, reliable, and high-performance electronic systems across a wide range of industries and applications.
Leave a Reply