Introduction to Track width in PCB Design
Track width is a crucial aspect of printed circuit board (PCB) design that significantly impacts the performance, reliability, and manufacturability of electronic devices. In PCB design, tracks are the conductive paths that carry electrical signals and power between components. The width of these tracks plays a vital role in determining the current-carrying capacity, signal integrity, and overall functionality of the circuit board.
Understanding the Basics of Track Width
Track width refers to the physical width of the conductive paths on a PCB. It is typically measured in mils (thousandths of an inch) or millimeters. The appropriate track width for a particular PCB design depends on several factors, including:
- Current requirements
- Voltage levels
- Signal frequency
- PCB manufacturing constraints
- Thermal considerations
Choosing the right track width is essential to ensure that the PCB can handle the required current without overheating, maintain signal integrity, and be manufactured efficiently and cost-effectively.
Current-Carrying Capacity and Track Width
One of the primary reasons why track width is important in PCB design is its impact on current-carrying capacity. The amount of current that a track can safely carry without overheating or causing damage to the PCB depends on its cross-sectional area, which is determined by its width and thickness.
Calculating Current-Carrying Capacity
The current-carrying capacity of a track can be calculated using the following formula:
I = k * ΔT^0.44 * A^0.725
Where:
– I is the maximum current in amps
– k is a constant that depends on the temperature rise and the type of conductor material (e.g., 0.048 for copper)
– ΔT is the temperature rise above ambient in °C
– A is the cross-sectional area of the track in mils²
By increasing the track width, designers can increase the cross-sectional area and, consequently, the current-carrying capacity of the track.
IPC-2221 Standards for Track Width
The IPC (Association Connecting Electronics Industries) provides guidelines for determining the appropriate track width based on the required current-carrying capacity. The IPC-2221 standard, “Generic Standard on Printed Board Design,” offers a table that relates track width to current-carrying capacity for various temperature rises and copper thicknesses.
Current (A) | Track Width (mils) for 1 oz. Copper |
---|---|
0.5 | 10 |
1.0 | 20 |
2.0 | 40 |
3.0 | 60 |
4.0 | 80 |
5.0 | 100 |
Table 1: IPC-2221 Track Width Guidelines for 1 oz. Copper
Designers should refer to the IPC-2221 standard and other relevant guidelines when determining the appropriate track width for their PCB designs.
Signal Integrity and Track Width
Track width also plays a significant role in maintaining signal integrity in PCB designs. Signal integrity refers to the quality of electrical signals as they propagate through the circuit board. Poor signal integrity can lead to issues such as signal distortion, crosstalk, and electromagnetic interference (EMI).
Impedance Control and Track Width
In high-speed PCB designs, controlling the characteristic impedance of tracks is crucial for maintaining signal integrity. The characteristic impedance of a track depends on several factors, including its width, thickness, and the properties of the surrounding dielectric material.
To achieve the desired characteristic impedance, designers must carefully select the appropriate track width and spacing. Wider tracks generally have lower impedance, while narrower tracks have higher impedance. The exact relationship between track width and impedance depends on the PCB Stackup and the dielectric properties of the substrate material.
Crosstalk and Track Width
Crosstalk occurs when signals from one track interfere with signals on adjacent tracks. This interference can lead to signal distortion and other issues that compromise the performance of the circuit board. To minimize crosstalk, designers must carefully control the spacing between tracks and the width of the tracks themselves.
Wider tracks generally have a greater potential for crosstalk because they have larger surface areas and are more likely to couple with adjacent tracks. By using narrower tracks and increasing the spacing between them, designers can reduce the risk of crosstalk and improve signal integrity.
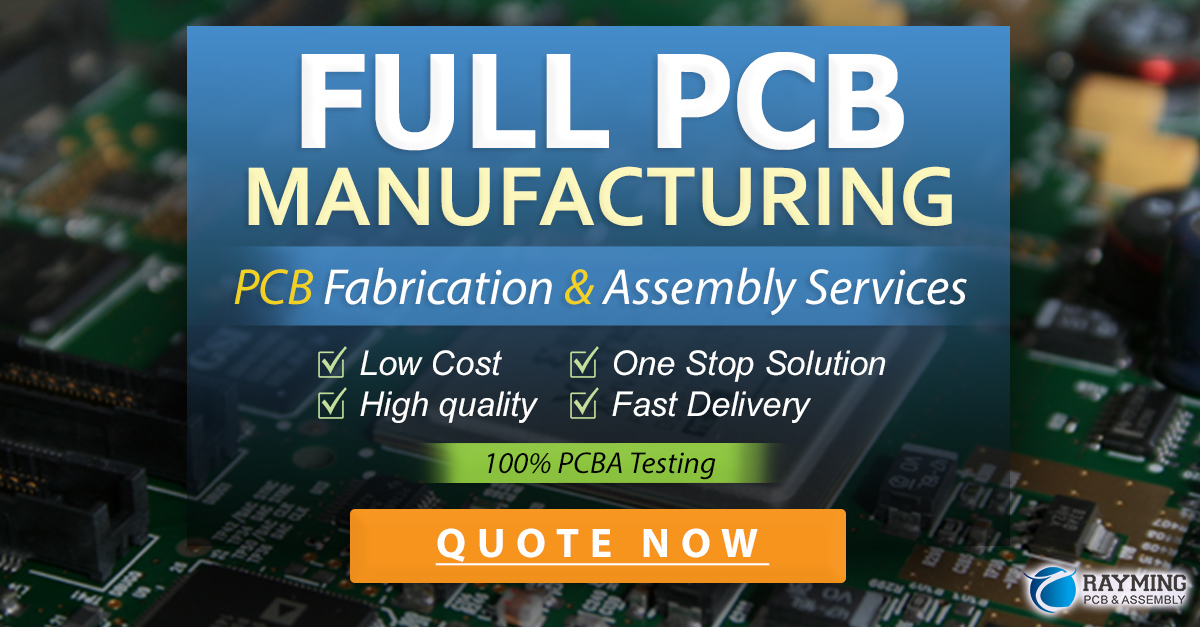
Manufacturing Considerations and Track Width
Track width is not only important for the electrical performance of a PCB but also for its manufacturability. PCB manufacturers have specific capabilities and limitations when it comes to producing circuit boards with different track widths.
Minimum Track Width and Manufacturing Constraints
Each PCB manufacturer has a minimum track width that they can reliably produce. This minimum width depends on the manufacturing process, equipment, and materials used. Designers must ensure that their track widths are compatible with the capabilities of their chosen manufacturer.
Attempting to use track widths that are too narrow for a particular manufacturing process can lead to issues such as:
- Incomplete etching
- Shorts between tracks
- Poor adhesion of the copper to the substrate
- Increased manufacturing costs
Designers should consult with their PCB manufacturer to determine the minimum track width that can be reliably produced and design their boards accordingly.
Cost Implications of Track Width
The choice of track width can also have cost implications for PCB manufacturing. In general, using wider tracks can help reduce manufacturing costs because they are easier to produce and less likely to cause issues during the fabrication process.
However, using excessively wide tracks can also increase costs by consuming more board space and requiring larger PCBs. Designers must strike a balance between track width, manufacturability, and cost to create PCBs that are both functional and economically viable.
Thermal Considerations and Track Width
Track width also plays a role in the thermal management of PCBs. As current flows through the tracks, it generates heat due to the resistance of the copper. If the tracks are too narrow, they may not be able to dissipate this heat effectively, leading to temperature rise and potential damage to the PCB and its components.
Temperature Rise and Track Width
The temperature rise in a track depends on several factors, including the current it carries, its cross-sectional area, and the thermal conductivity of the surrounding materials. Wider tracks have a greater cross-sectional area and can dissipate heat more effectively than narrower tracks.
Designers must consider the expected current loads and ambient temperature conditions when selecting track widths to ensure that the temperature rise remains within acceptable limits. The IPC-2221 standard provides guidelines for determining the maximum allowable temperature rise for various applications.
Thermal Management Techniques and Track Width
In addition to selecting appropriate track widths, designers can use various thermal management techniques to help dissipate heat and prevent excessive temperature rise. These techniques include:
- Using thermal vias to conduct heat away from the tracks and into the PCB substrate
- Incorporating heat sinks or other cooling mechanisms
- Using high-thermal-conductivity materials, such as copper-clad laminates or Metal-Core PCBs
- Optimizing the placement of components and tracks to promote heat dissipation
By combining appropriate track widths with effective thermal management techniques, designers can create PCBs that operate reliably and safely under a wide range of temperature conditions.
Frequently Asked Questions (FAQ)
-
What is track width in PCB design?
Track width refers to the physical width of the conductive paths (tracks) on a printed circuit board. It is typically measured in mils (thousandths of an inch) or millimeters. -
Why is track width important in PCB design?
Track width is important in PCB design because it affects several key aspects of the board’s performance and manufacturability, including current-carrying capacity, signal integrity, manufacturing constraints, and thermal management. -
How does track width affect current-carrying capacity?
The current-carrying capacity of a track depends on its cross-sectional area, which is determined by its width and thickness. Wider tracks have a greater cross-sectional area and can carry more current without overheating or causing damage to the PCB. -
What is the relationship between track width and signal integrity?
Track width can impact signal integrity in several ways. Wider tracks generally have lower impedance and a greater potential for crosstalk, while narrower tracks have higher impedance and are less likely to interfere with adjacent signals. Designers must carefully select track widths and spacing to maintain signal integrity in high-speed PCB designs. -
How does track width relate to PCB manufacturing constraints?
Each PCB manufacturer has a minimum track width that they can reliably produce, which depends on their manufacturing process, equipment, and materials. Designers must ensure that their track widths are compatible with the capabilities of their chosen manufacturer to avoid issues such as incomplete etching, shorts between tracks, and increased manufacturing costs.
Conclusion
Track width is a critical aspect of PCB design that affects the performance, reliability, and manufacturability of electronic devices. By understanding the importance of track width and how it relates to current-carrying capacity, signal integrity, manufacturing constraints, and thermal management, designers can create PCBs that are functional, reliable, and cost-effective.
When selecting track widths for a PCB design, designers should consider factors such as:
- The required current-carrying capacity and voltage levels
- The desired signal integrity and impedance characteristics
- The capabilities and limitations of the chosen PCB manufacturer
- The expected thermal conditions and temperature rise
By following industry standards, such as IPC-2221, and consulting with PCB manufacturers, designers can ensure that their track widths are appropriate for their specific applications and manufacturing processes. With careful attention to track width and other key design considerations, designers can create high-quality PCBs that meet the evolving needs of modern electronic devices.
Leave a Reply