Introduction to PCB Stackup
A printed circuit board (PCB) is a fundamental component in modern electronics. It provides a platform for mounting and interconnecting electronic components to create a functional circuit. The arrangement of layers in a PCB, known as the PCB stackup, plays a crucial role in determining the board’s performance, reliability, and manufacturability.
In this article, we will focus on the stackup of a 3-layer PCB, exploring its structure, benefits, and design considerations. By understanding the intricacies of a 3-layer PCB stackup, designers and engineers can make informed decisions to optimize their PCB designs.
What is a 3 Layer PCB?
A 3-layer PCB consists of three conductive layers separated by insulating material. The three layers are typically arranged as follows:
- Top Layer: This is the uppermost conductive layer, where components are usually placed and routed.
- Inner Layer: Also known as the core layer, this is the middle conductive layer sandwiched between the top and bottom layers.
- Bottom Layer: This is the lowermost conductive layer, often used for routing and placing components on the opposite side of the board.
The insulating material, called the substrate or dielectric, separates the conductive layers and provides electrical isolation. The most common substrate materials are FR-4, a glass-reinforced epoxy laminate, and Rogers materials for high-frequency applications.
Advantages of a 3 Layer PCB
Increased Routing Flexibility
One of the primary advantages of a 3-layer PCB is the increased routing flexibility compared to a single-layer or double-layer board. With an additional conductive layer, designers have more space to route traces and accommodate complex circuitry. This is particularly beneficial for designs with a high component density or intricate interconnections.
Improved Signal Integrity
Signal integrity is a critical factor in PCB design, especially for high-speed and sensitive circuits. A 3-layer PCB offers improved signal integrity by providing a dedicated inner layer for power and ground planes. By separating the power and ground from the signal layers, the board can minimize electromagnetic interference (EMI) and reduce noise coupling between signals.
Enhanced Shielding and Grounding
The inner layer of a 3-layer PCB is often used as a ground plane, which acts as a shield against electromagnetic interference. By strategically placing the ground plane between the top and bottom layers, designers can create a Faraday cage effect, reducing the impact of external noise sources on the circuit. Additionally, a solid ground plane provides a low-impedance return path for high-frequency signals, minimizing ground bounce and improving signal quality.
Cost-Effective Solution
While a 3-layer PCB may have a higher initial cost compared to a single-layer or double-layer board, it offers a cost-effective solution for many applications. The increased routing flexibility and improved signal integrity of a 3-layer PCB can help reduce the overall board size, component count, and manufacturing complexity. This, in turn, can lead to lower assembly costs and higher yields.
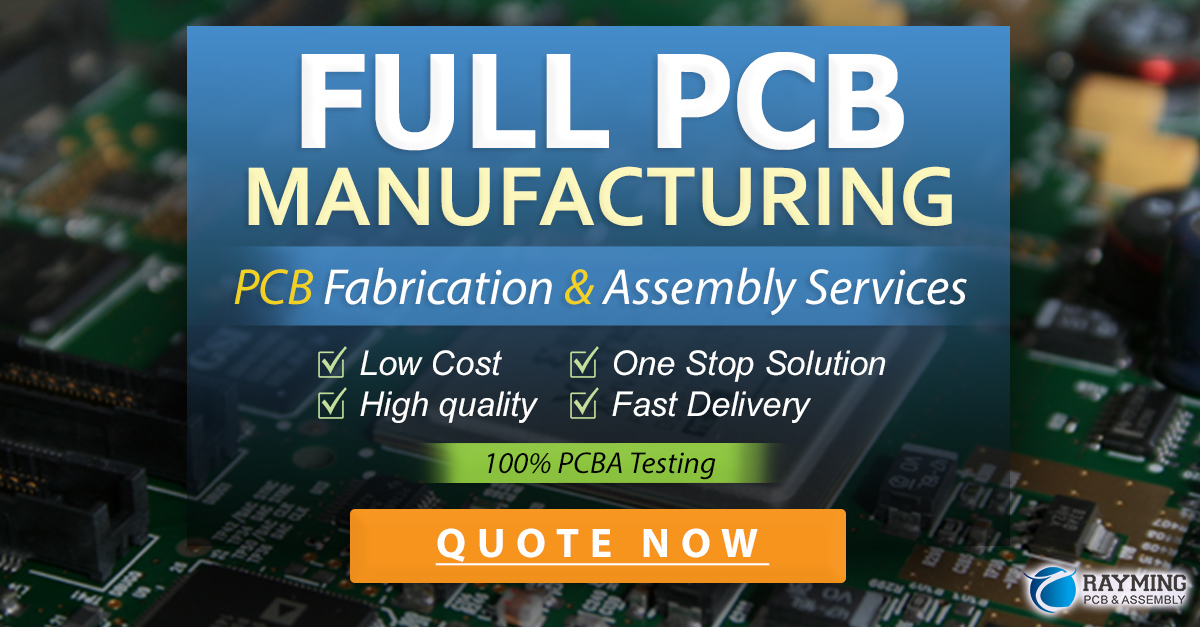
Designing a 3 Layer PCB Stackup
Layer Arrangement
When designing a 3-layer PCB stackup, it’s essential to consider the arrangement of the layers to optimize performance and manufacturability. A typical 3-layer stackup arrangement is as follows:
Layer | Description |
---|---|
Top | Signal layer, component placement |
Inner | Power or ground plane |
Bottom | Signal layer, component placement |
The top and bottom layers are primarily used for component placement and signal routing, while the inner layer serves as a power or ground plane. This arrangement provides a balanced distribution of copper and helps maintain the board’s structural integrity.
Material Selection
Choosing the right materials for a 3-layer PCB stackup is crucial for achieving the desired electrical and mechanical properties. The most common substrate material is FR-4, which offers a good balance of cost, performance, and availability. However, for high-frequency or specialized applications, designers may opt for low-loss materials like Rogers laminates.
When selecting materials, consider the following factors:
- Dielectric constant (Dk): Affects the signal propagation speed and impedance.
- Dissipation factor (Df): Determines the amount of signal loss in the substrate.
- Thermal conductivity: Influences the board’s ability to dissipate heat.
- Mechanical strength: Impacts the board’s durability and reliability.
Thickness and Spacing
The thickness of the conductive layers and the spacing between them play a significant role in the PCB’s electrical characteristics and manufacturability. Thinner layers and tighter spacing can improve signal integrity and reduce the board’s overall thickness. However, they also increase manufacturing complexity and cost.
When determining the layer thickness and spacing, consider the following guidelines:
- Use copper weights appropriate for the current carrying requirements and manufacturability.
- Maintain a minimum spacing between traces to prevent short circuits and signal crosstalk.
- Follow the manufacturer’s recommendations for minimum trace width and spacing based on the chosen fabrication process.
Via Placement and Optimization
Vias are conductive holes that allow signals to pass between layers in a PCB. In a 3-layer PCB stackup, vias are used to connect the top and bottom signal layers to the inner power or ground plane. Proper via placement and optimization are essential for maintaining signal integrity and minimizing manufacturing issues.
Consider the following tips for via placement and optimization:
- Place vias close to the components to minimize the loop area and reduce inductance.
- Use an appropriate via size and pad diameter based on the manufacturing capabilities and design requirements.
- Optimize via placement to reduce the number of vias and improve routing efficiency.
- Consider using blind or buried vias for high-density designs or to improve signal integrity.
Manufacturing Considerations
Fabrication Process
The fabrication process for a 3-layer PCB involves several steps, including:
- Lamination: The conductive layers and insulating substrates are laminated together under heat and pressure to form a solid board.
- Drilling: Holes are drilled through the board for vias and component mounting.
- Plating: Copper is plated onto the drilled holes to create electrical connections between layers.
- Patterning: The desired circuit pattern is transferred onto the conductive layers using photolithography and etching techniques.
- Solder Mask Application: A protective solder mask is applied to the board to prevent short circuits and improve solderability.
- Silkscreen Printing: Component labels and other markings are printed onto the board using silkscreen printing.
Design for Manufacturability (DFM)
To ensure a smooth and cost-effective manufacturing process, it’s crucial to incorporate Design for Manufacturability (DFM) principles into the PCB design. Some key DFM considerations for a 3-layer PCB include:
- Adhering to the manufacturer’s design rules and guidelines for minimum trace width, spacing, and hole size.
- Avoiding acute angles and sharp corners in trace routing to prevent acid traps during etching.
- Providing sufficient clearance around holes and vias for proper plating and soldering.
- Using standard component sizes and footprints to simplify assembly and reduce costs.
- Incorporating fiducial markers and tooling holes to facilitate accurate alignment during manufacturing.
Frequently Asked Questions
1. How does a 3-layer PCB compare to a 2-layer PCB in terms of performance?
A 3-layer PCB offers several advantages over a 2-layer PCB, including increased routing flexibility, improved signal integrity, and enhanced shielding and grounding. The additional inner layer in a 3-layer PCB provides a dedicated plane for power or ground, which helps reduce EMI and minimize noise coupling between signals. This results in better overall performance, especially for high-speed and sensitive circuits.
2. Can a 3-layer PCB be used for high-frequency applications?
Yes, a 3-layer PCB can be used for high-frequency applications, provided that the appropriate materials and design techniques are employed. For high-frequency applications, it’s essential to choose low-loss substrate materials, such as Rogers laminates, and optimize the stackup for controlled impedance. Additionally, proper signal routing, via placement, and grounding strategies should be implemented to minimize signal loss and maintain signal integrity at high frequencies.
3. How does the cost of a 3-layer PCB compare to other layer configurations?
The cost of a 3-layer PCB is generally higher than that of a single-layer or double-layer board due to the additional materials and manufacturing steps involved. However, a 3-layer PCB can be a cost-effective solution for many applications, as it offers improved performance and routing flexibility, which can help reduce the overall board size and component count. This, in turn, can lead to lower assembly costs and higher yields, offsetting the initial higher cost of the 3-layer board.
4. What are the limitations of a 3-layer PCB?
While a 3-layer PCB offers several benefits, it also has some limitations. One limitation is the increased manufacturing complexity compared to single-layer or double-layer boards, which can lead to higher fabrication costs and longer lead times. Additionally, a 3-layer PCB may not be suitable for very high-density designs or applications that require a large number of layers, such as complex digital systems or advanced packaging technologies.
5. Can a 3-layer PCB be used for flexible electronics applications?
Yes, a 3-layer PCB can be used for flexible electronics applications, such as wearables, medical devices, and automotive electronics. Flexible 3-layer PCBs, also known as Flex-Rigid PCBs, combine the benefits of a 3-layer stackup with the flexibility and conformability of a flexible substrate material. These boards can be designed to bend, fold, or twist, allowing for greater design freedom and improved reliability in applications subjected to mechanical stress or vibration.
Conclusion
A 3-layer PCB stackup offers a balanced solution for many electronics applications, providing increased routing flexibility, improved signal integrity, and enhanced shielding and grounding. By understanding the structure, benefits, and design considerations of a 3-layer PCB, designers and engineers can make informed decisions to optimize their PCB designs for performance, reliability, and manufacturability.
When designing a 3-layer PCB stackup, it’s essential to consider factors such as layer arrangement, material selection, thickness and spacing, and via placement and optimization. Additionally, incorporating Design for Manufacturability (DFM) principles and working closely with the PCB manufacturer can help ensure a smooth and cost-effective fabrication process.
As electronics continue to evolve and become more complex, the importance of a well-designed PCB stackup cannot be overstated. By leveraging the benefits of a 3-layer PCB and following best design practices, designers can create high-performance, reliable, and manufacturable electronics that meet the ever-growing demands of modern applications.
Leave a Reply