Understanding Printed Circuit Boards (PCBs)
Before diving into the details of Turnkey PCB assembly, it’s essential to understand what PCBs are and their role in modern electronics. PCBs are the backbone of most electronic devices, providing a platform for electrical components to be mounted and interconnected. They consist of a non-conductive substrate, typically made of fiberglass or other composite materials, with conductive copper traces etched onto the surface to form a circuit pattern.
PCBs come in various types, depending on the number of layers, the density of components, and the specific application requirements. Some common types of PCBs include:
PCB Type | Description |
---|---|
Single-sided | Components are mounted on one side of the board, with conductive traces on the opposite side. |
Double-sided | Components and conductive traces are present on both sides of the board. |
Multi-layer | Consists of multiple layers of conductive traces separated by insulating layers, allowing for more complex circuitry and higher component density. |
Flexible | Made of flexible materials, such as polyimide, allowing the PCB to bend and conform to various shapes. |
Rigid-flex | Combines rigid and flexible sections, offering the benefits of both types of PCBs. |
The Turnkey PCB Assembly Process
Turnkey PCB assembly involves several key stages, each critical to ensuring the quality and reliability of the final product. These stages include:
1. PCB Design and Engineering
The first step in turnkey PCB assembly is to design the PCB based on the specific requirements of the product. This involves creating a schematic diagram that represents the electrical connections between components, followed by a PCB layout that determines the physical placement of components and routing of conductive traces.
During the design phase, engineers must consider various factors, such as:
- Component selection and compatibility
- Signal integrity and electromagnetic compatibility (EMC)
- Thermal management and power distribution
- Manufacturing constraints and design for manufacturability (DFM)
2. PCB Fabrication
Once the PCB design is finalized, the next step is to fabricate the bare PCB. This process involves several sub-processes, including:
- PCB material selection and preparation
- Applying a photoresist layer and exposing it to UV light through a photomask
- Developing the photoresist and etching away the unwanted copper
- Drilling holes for through-hole components and vias
- Applying a solder mask and silkscreen for component labeling
3. PCB Assembly
With the bare PCB fabricated, the next stage is to assemble the components onto the board. There are two primary methods for PCB assembly:
Through-Hole Assembly (THA)
In through-hole assembly, components with long leads are inserted into drilled holes on the PCB and soldered onto the opposite side. This method is often used for larger components or in applications that require higher mechanical strength.
Surface Mount Assembly (SMT)
Surface mount assembly involves placing components directly onto the surface of the PCB and soldering them in place. SMT allows for smaller component sizes, higher component density, and faster assembly speeds compared to THA.
The PCB assembly process typically involves the following steps:
- Solder paste application: A precise amount of solder paste is applied to the PCB pads using a stencil or screen printing process.
- Component placement: Components are picked and placed onto the PCB using automated pick-and-place machines or manual placement for smaller batches.
- Reflow soldering: The PCB is heated in a reflow oven, causing the solder paste to melt and form a permanent connection between the components and the PCB.
- Inspection and testing: The assembLED PCB undergoes visual inspection and automated optical inspection (AOI) to identify any defects or issues. Functional testing may also be performed to ensure the PCB operates as intended.
4. Post-Assembly Services
After the PCB is assembled, additional post-assembly services may be required depending on the specific application and customer requirements. These services can include:
- Conformal coating: Applying a protective layer to the PCB to shield it from environmental factors such as moisture, dust, and chemicals.
- Potting: Encapsulating the PCB or specific components in a resin or epoxy compound for added protection and insulation.
- Cable assembly: Connecting cables, wires, and connectors to the PCB for integration into the final product.
- Box build assembly: Integrating the PCB into an enclosure or housing, along with other mechanical components, to create a complete product.
Benefits of Turnkey PCB Assembly
Turnkey PCB assembly offers several key benefits for companies looking to outsource their electronics manufacturing:
- Cost savings: By outsourcing the entire PCB assembly process to a single vendor, companies can reduce costs associated with managing multiple suppliers, inventory, and logistics.
- Time-to-market: Turnkey PCB assembly providers have streamlined processes and expertise in PCB design, fabrication, and assembly, enabling faster product development cycles and shorter time-to-market.
- Quality assurance: Reputable turnkey PCB assembly providers adhere to strict quality control standards and employ advanced inspection and testing methods to ensure the highest quality products.
- Scalability: Turnkey PCB assembly services can accommodate a wide range of production volumes, from prototypes to high-volume production, allowing companies to scale their manufacturing as needed.
- Access to expertise: By partnering with a turnkey PCB assembly provider, companies can leverage the provider’s expertise in PCB design, manufacturing, and assembly, as well as their knowledge of the latest technologies and industry trends.
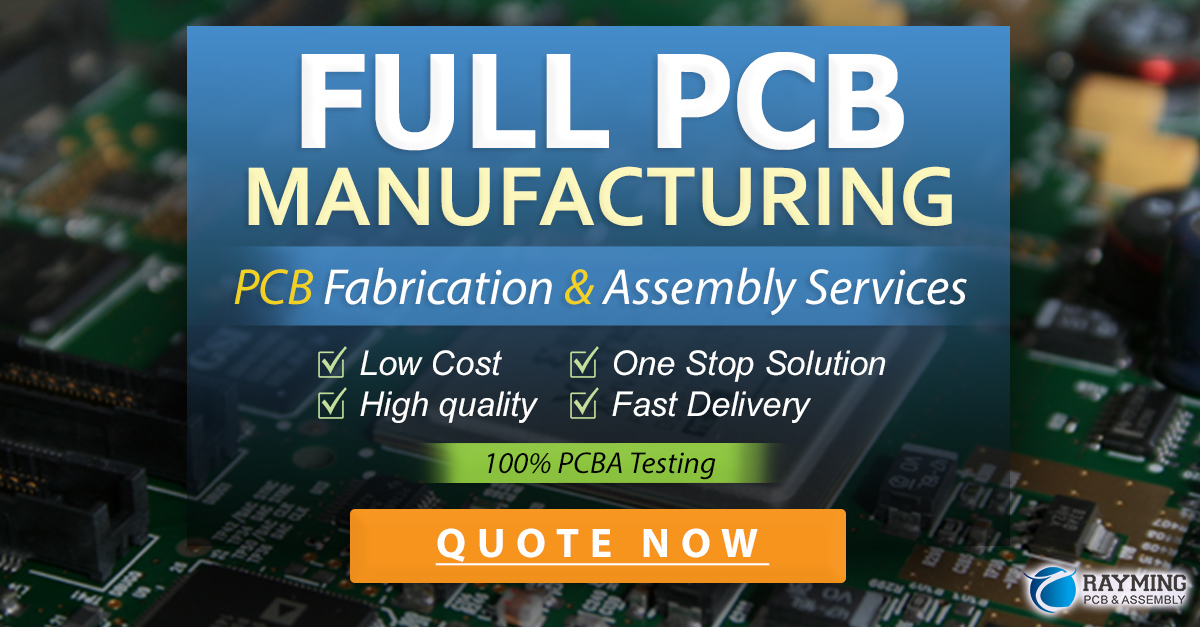
Choosing a Turnkey PCB Assembly Provider
When selecting a turnkey PCB assembly provider, it’s essential to consider several factors to ensure a successful partnership:
- Technical capabilities: Ensure the provider has the necessary equipment, expertise, and processes to handle your specific PCB assembly requirements, including the ability to work with your desired components and technologies.
- Quality certifications: Look for providers with relevant quality certifications, such as ISO 9001, ISO 13485 (for medical devices), or AS9100 (for aerospace and defense), to ensure they adhere to industry-recognized quality standards.
- Communication and support: Choose a provider that offers clear communication channels, responsive support, and a dedicated project management team to ensure smooth collaboration and timely issue resolution.
- Intellectual property (IP) protection: If your PCB design involves proprietary or sensitive information, ensure the provider has robust IP protection measures in place, such as non-disclosure agreements (NDAs) and secure data handling practices.
- Lead times and delivery: Discuss lead times and delivery schedules with potential providers to ensure they can meet your time-to-market goals and accommodate your production volume requirements.
- Cost and value: While cost is an important consideration, it’s crucial to evaluate the overall value provided by the turnkey PCB assembly service, including quality, reliability, and the level of support and expertise offered.
Frequently Asked Questions (FAQs)
- What is the minimum order quantity (MOQ) for turnkey PCB assembly?
-
MOQs vary depending on the provider and the specific project requirements. Some providers offer low MOQs for prototyping and small-batch production, while others may require higher volumes for cost-effective manufacturing. It’s best to discuss your specific needs with potential providers to determine their MOQ policies.
-
How long does the turnkey PCB assembly process typically take?
-
The lead time for turnkey PCB assembly depends on several factors, including the complexity of the PCB design, the availability of components, and the production volume. Prototype and small-batch orders may take a few days to a few weeks, while larger production runs can take several weeks or months. Discuss your specific timeline requirements with potential providers to ensure they can meet your needs.
-
Can turnkey PCB assembly providers source components for my project?
-
Yes, most turnkey PCB assembly providers offer Component sourcing as part of their services. They have established relationships with component suppliers and can help you select and procure the necessary components for your PCB assembly project. This can help streamline the procurement process and ensure the availability of components for your production run.
-
What file formats are required for turnkey PCB assembly?
-
When providing design files for turnkey PCB assembly, you’ll typically need to supply Gerber files (RS-274X format) for the PCB layout, as well as a bill of materials (BOM) and assembly drawings or pick-and-place files. The specific file format requirements may vary depending on the provider, so it’s best to discuss this with them before submitting your design files.
-
How can I ensure the quality of my PCBs when using a turnkey assembly service?
- To ensure the quality of your PCBs, choose a reputable turnkey PCB assembly provider with a proven track record of delivering high-quality products. Look for providers with relevant quality certifications, such as ISO 9001, and discuss their quality control processes, inspection methods, and testing procedures. Additionally, provide clear and comprehensive design files, specifications, and requirements to minimize the risk of errors or misinterpretations during the assembly process.
Conclusion
Turnkey PCB assembly is a comprehensive solution for companies looking to outsource their electronics manufacturing. By encompassing the entire process from PCB design to final product assembly, turnkey services offer numerous benefits, including cost savings, faster time-to-market, quality assurance, and access to expertise.
When selecting a turnkey PCB assembly provider, it’s crucial to consider factors such as technical capabilities, quality certifications, communication and support, IP protection, lead times, and overall value. By partnering with the right provider, companies can streamline their PCB assembly process, reduce risks, and focus on their core competencies while bringing high-quality electronic products to market.
Leave a Reply