Introduction to PTFE PCB
Polytetrafluoroethylene (PTFE), commonly known by its trade name Teflon, is a synthetic fluoropolymer widely used in various industries due to its unique properties. PTFE has found its way into the electronics industry as a base material for printed Circuit Boards (PCBs), particularly in high-frequency and high-speed applications. PTFE PCBs, also known as Teflon PCBs, offer superior electrical and mechanical properties compared to traditional PCB materials like FR-4.
Properties of PTFE
PTFE is known for its exceptional properties, which make it an ideal choice for high-performance PCBs:
- Low dielectric constant: PTFE has a low dielectric constant (2.1), which minimizes signal loss and allows for faster signal transmission.
- Low dissipation factor: The low dissipation factor (0.0002) of PTFE ensures minimal signal attenuation and heat generation.
- High thermal stability: PTFE remains stable over a wide temperature range (-200°C to +260°C), making it suitable for harsh environments.
- Excellent chemical resistance: PTFE is resistant to most chemicals, solvents, and acids, ensuring the PCB’s longevity.
- Low moisture absorption: PTFE has a low moisture absorption rate (0.01%), preventing the PCB from absorbing moisture and maintaining its electrical properties.
PTFE Based Laminates
PTFE based laminates are the foundation of Teflon PCBs. These laminates consist of a PTFE substrate reinforced with glass fibers or ceramic fillers to enhance their mechanical strength and dimensional stability. Some common PTFE based laminates include:
Rogers RT/duroid
Rogers Corporation is a leading manufacturer of high-performance PTFE laminates. Their RT/duroid series offers a range of laminates with different dielectric constants and dissipation factors to cater to various applications:
Laminate | Dielectric Constant | Dissipation Factor |
---|---|---|
RT/duroid 5870 | 2.33 | 0.0012 |
RT/duroid 5880 | 2.20 | 0.0009 |
RT/duroid 6002 | 2.94 | 0.0012 |
Taconic TLY
Taconic is another renowned manufacturer of PTFE laminates. Their TLY series offers low dielectric constant and low dissipation factor laminates for high-frequency applications:
Laminate | Dielectric Constant | Dissipation Factor |
---|---|---|
TLY-5 | 2.20 | 0.0009 |
TLY-5A | 2.17 | 0.0009 |
TLY-6 | 2.60 | 0.0010 |
PTFE PCB Manufacturing
The manufacturing process of PTFE PCBs differs from that of standard FR-4 PCBs due to the unique properties of PTFE. The key steps involved in PTFE PCB manufacturing are:
- Material preparation: PTFE laminates are cut to the required size and cleaned to remove any contaminants.
- Drilling: Holes are drilled into the PTFE laminate using specialized drills designed to handle the soft and slippery nature of PTFE.
- Plating: The drilled holes are plated with copper to establish electrical connections between layers.
- Patterning: The desired circuit pattern is transferred onto the PTFE laminate using photolithography or laser direct imaging (LDI).
- Etching: The unwanted copper is removed using a chemical etching process, leaving behind the desired circuit pattern.
- Solder Mask application: A solder mask is applied to protect the copper traces and prevent short circuits.
- Surface finish: A surface finish, such as ENIG (Electroless Nickel Immersion Gold) or HASL (Hot Air Solder Leveling), is applied to the exposed copper pads to improve solderability and protect against oxidation.
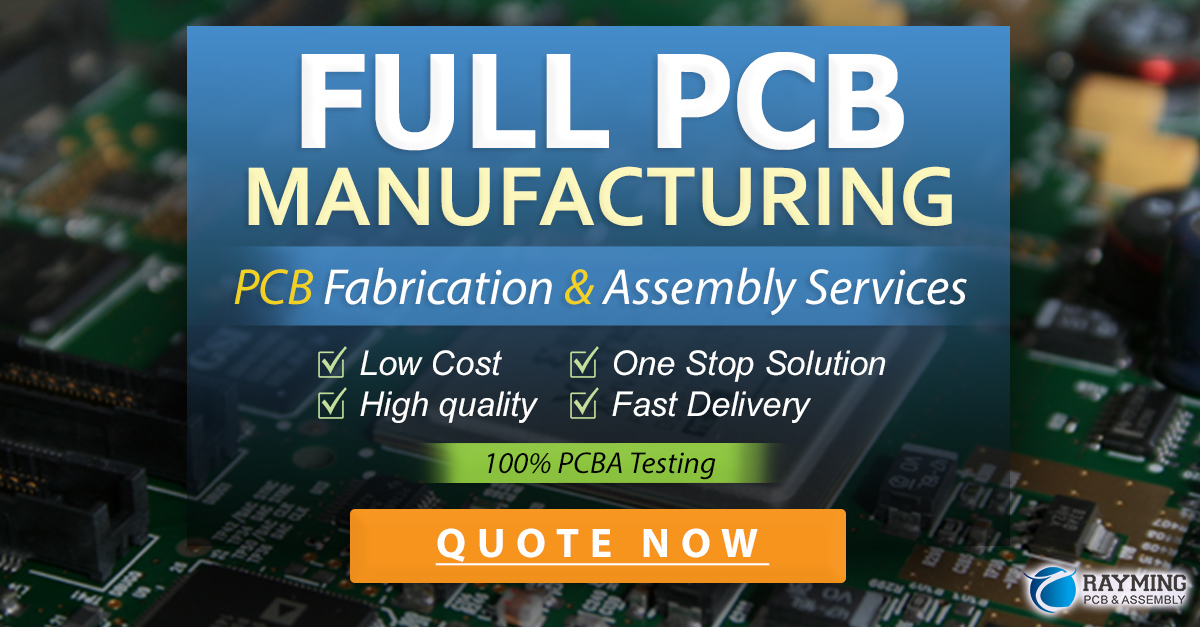
PTFE PCB Costs
PTFE PCBs are generally more expensive than traditional FR-4 PCBs due to the higher cost of PTFE laminates and the specialized manufacturing processes involved. The cost of a PTFE PCB depends on several factors:
- Laminate type: Different PTFE laminates have varying costs, with higher-performance laminates being more expensive.
- Board size: Larger PCBs require more material and processing time, resulting in higher costs.
- Layer count: Multi-layer PTFE PCBs are more expensive than single-layer boards due to the additional processing steps involved.
- Quantity: Higher quantities of PTFE PCBs can lead to lower per-unit costs due to economies of scale.
- Design complexity: Complex designs with high-density interconnects (HDI) or fine-pitch components may increase the manufacturing costs.
On average, a simple single-layer PTFE PCB can cost 2-3 times more than an equivalent FR-4 PCB, while complex multi-layer PTFE PCBs can cost up to 10 times more.
Applications of PTFE PCBs
PTFE PCBs are used in various high-frequency and high-speed applications where Signal Integrity and reliability are critical. Some common applications include:
- Aerospace and defense: Radar systems, satellite communication, and avionics.
- Telecommunications: 5G networks, microwave devices, and base stations.
- Medical devices: MRI machines, high-frequency surgical equipment, and implantable devices.
- Automotive: Advanced driver assistance systems (ADAS), vehicle-to-vehicle (V2V) communication, and autonomous vehicles.
- Industrial: High-frequency power converters, oil and gas exploration equipment, and renewable energy systems.
Advantages of PTFE PCBs
PTFE PCBs offer several advantages over traditional PCB materials:
- Superior signal integrity: The low dielectric constant and dissipation factor of PTFE ensure minimal signal loss and distortion, making it ideal for high-frequency applications.
- Improved reliability: PTFE’s excellent thermal stability and chemical resistance make PTFE PCBs more reliable in harsh environments.
- Reduced crosstalk: The low dielectric constant of PTFE minimizes crosstalk between adjacent signals, improving signal integrity.
- Higher operating frequencies: PTFE PCBs can operate at higher frequencies than FR-4 PCBs, enabling the development of advanced high-speed systems.
Challenges in PTFE PCB Manufacturing
Despite their superior properties, PTFE PCBs present several challenges during manufacturing:
- Softness and slipperiness: PTFE’s soft and slippery nature makes it difficult to handle and process, requiring specialized equipment and techniques.
- Drillability: PTFE’s softness can cause drill bits to wander, leading to inaccurate hole placement and potential reliability issues.
- Adhesion: PTFE’s non-stick properties make it challenging to achieve good adhesion between the copper layers and the PTFE substrate, requiring specialized surface treatments.
- Dimensional stability: PTFE has a higher coefficient of thermal expansion (CTE) than copper, which can cause dimensional instability and warping during manufacturing.
To overcome these challenges, PCB Manufacturers employ specialized techniques and equipment, such as laser drilling, plasma etching, and advanced surface treatments.
Frequently Asked Questions (FAQ)
-
Q: What is the difference between PTFE and FR-4 PCBs?
A: PTFE PCBs have a lower dielectric constant and dissipation factor compared to FR-4 PCBs, making them more suitable for high-frequency and high-speed applications. PTFE also offers better thermal stability and chemical resistance than FR-4. -
Q: Can PTFE PCBs be used for low-frequency applications?
A: While PTFE PCBs are primarily used for high-frequency applications, they can also be used for low-frequency applications where reliability and environmental resistance are critical factors. -
Q: Are PTFE PCBs suitable for flexible circuits?
A: Yes, PTFE laminates can be used to create flexible circuits. Flexible PTFE PCBs offer the same benefits as rigid PTFE PCBs, along with the added advantage of flexibility. -
Q: How can I reduce the cost of PTFE PCBs?
A: To reduce the cost of PTFE PCBs, consider optimizing the board size, minimizing the layer count, and increasing the order quantity. Working closely with your PCB manufacturer can also help identify cost-saving opportunities. -
Q: What surface finishes are compatible with PTFE PCBs?
A: ENIG (Electroless Nickel Immersion Gold) and HASL (Hot Air Solder Leveling) are the most common surface finishes used for PTFE PCBs. Other compatible surface finishes include Immersion Silver and OSP (Organic Solderability Preservative).
Conclusion
PTFE PCBs, or Teflon PCBs, are high-performance printed circuit boards that offer superior electrical and mechanical properties compared to traditional PCB materials. With their low dielectric constant, low dissipation factor, and excellent thermal and chemical stability, PTFE PCBs are ideal for high-frequency and high-speed applications in various industries, including aerospace, telecommunications, medical devices, automotive, and industrial sectors.
The manufacturing process of PTFE PCBs involves specialized techniques and equipment to overcome the challenges associated with handling and processing PTFE laminates. As a result, PTFE PCBs are generally more expensive than FR-4 PCBs, with costs varying based on factors such as laminate type, board size, layer count, and design complexity.
Despite the higher costs, the superior performance and reliability of PTFE PCBs make them an essential component in advanced electronic systems where signal integrity and environmental resistance are paramount. As technology continues to advance and the demand for high-speed communication and data processing grows, the role of PTFE PCBs in shaping the future of electronics will only become more significant.
Leave a Reply