How Does Surface-mount technology Work?
In surface-mount technology, the components are placed directly onto the surface of a printed circuit board. The components are typically smaller than their through-hole counterparts and have small metal tabs or end caps that can be soldered directly to the PCB’s surface. The components are generally mounted on both sides of the circuit board, allowing for higher component density and more compact designs.
The SMT manufacturing process involves several steps:
-
Solder Paste Application: A thin layer of solder paste, a mixture of tiny solder particles and flux, is applied to the PCB’s surface where the components will be placed. This is typically done using a stencil printing process.
-
Component Placement: The surface-mount components are precisely placed onto the solder paste-covered pads on the PCB. This is usually performed by automated pick-and-place machines, which can place hundreds of components per minute with high accuracy.
-
Reflow Soldering: After component placement, the PCB goes through a reflow soldering process. The board is heated in a reflow oven, causing the solder paste to melt and form a permanent electrical and mechanical bond between the component leads and the PCB pads.
-
Inspection and Testing: After soldering, the assembLED PCBs undergo visual inspection and automated optical inspection (AOI) to identify any manufacturing defects or component placement errors. Electrical testing may also be performed to ensure proper functionality.
Advantages of Surface-Mount Technology
SMT offers several advantages over through-hole technology:
-
Smaller Size: Surface-mount components are typically much smaller than through-hole components, allowing for more compact PCB designs and smaller electronic devices.
-
Higher Component Density: With components mounted on both sides of the PCB and the smaller size of SMT components, designers can achieve much higher component densities, enabling more complex circuits in smaller spaces.
-
Improved Performance: SMT components have shorter leads, which reduces parasitic capacitance and inductance, resulting in better high-frequency performance and reduced signal distortion.
-
Lower Cost: The SMT process is highly automated, which reduces labor costs and increases production efficiency. Additionally, the smaller size of SMT components results in lower material costs.
-
Increased Reliability: SMT components have a stronger mechanical bond to the PCB due to their smaller size and the use of solder paste, resulting in better resistance to vibration and thermal stress.
Surface-Mount Component Packages
Surface-mount components come in a variety of package types, each with its own characteristics and advantages:
-
Chip Components: These are the smallest and most basic SMT components, including resistors, capacitors, and inductors. They are rectangular in shape and have no leads, with metallized ends that are soldered directly to the PCB pads.
-
Small Outline Packages (SOP): SOPs are integrated circuits (ICs) with leads extending from two opposite sides of the package. They are available in various sizes and lead counts, such as SOP-8, SOP-14, and SOP-16.
-
Quad Flat Packages (QFP): QFPs are ICs with leads extending from all four sides of the package. They are commonly used for microcontrollers, microprocessors, and other complex ICs. QFPs come in various sizes and lead counts, such as QFP-44, QFP-64, and QFP-100.
-
Ball Grid Arrays (BGA): BGAs are ICs with an array of solder balls on the bottom of the package instead of leads. The solder balls provide electrical connections to the PCB pads. BGAs offer the highest pin count and density among SMT packages.
-
Land Grid Arrays (LGA): LGAs are similar to BGAs but have flat contact pads instead of solder balls. They require a socket or a special soldering process to attach them to the PCB.
-
Chip Scale Packages (CSP): CSPs are very small ICs with dimensions close to the die size. They have a small footprint and low profile, making them suitable for space-constrained applications.
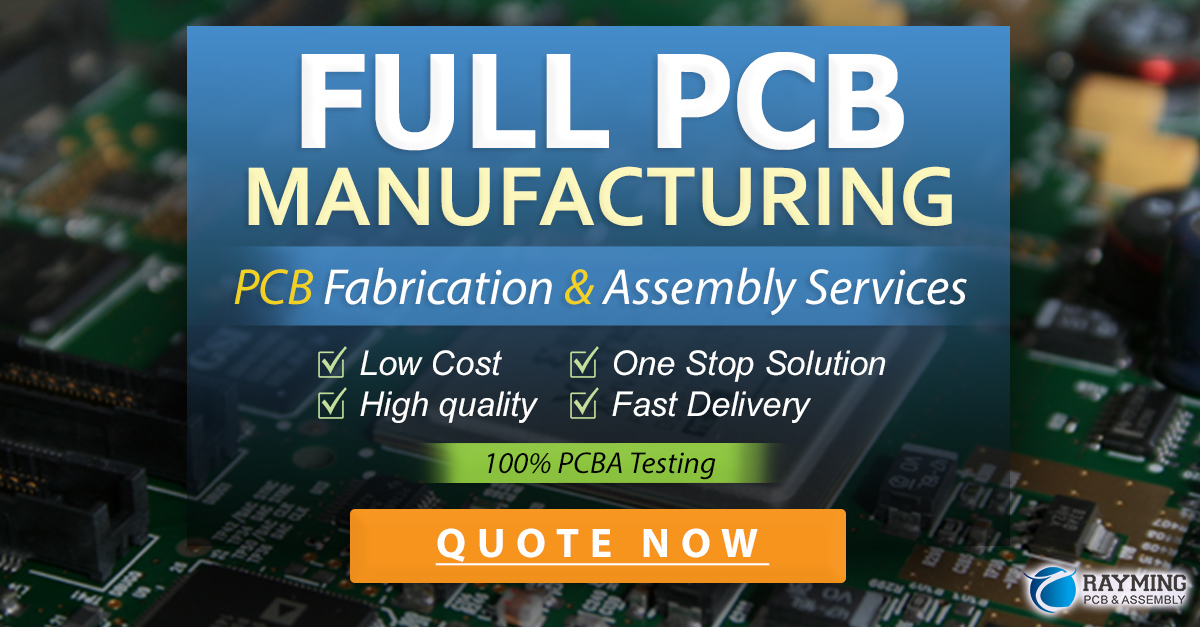
Challenges in Surface-Mount Technology
Despite its many advantages, SMT also presents some challenges:
-
Thermal Management: With higher component density and smaller package sizes, thermal management becomes more critical in SMT designs. Proper PCB layout, thermal vias, and heat sinks may be necessary to dissipate heat effectively.
-
Soldering Complexity: SMT requires precise control of solder paste application, component placement, and reflow soldering processes. Defects such as bridging, tombstoning, and insufficient solder joints can occur if the process is not well-controlled.
-
Rework and Repair: Reworking or repairing SMT assemblies can be more challenging than through-hole assemblies due to the smaller component sizes and the need for specialized tools and techniques.
-
Moisture Sensitivity: Some SMT components, particularly plastic-encapsulated ICs, are sensitive to moisture absorption. Proper storage, handling, and baking procedures must be followed to prevent moisture-related defects during soldering.
-
Electrostatic Discharge (ESD) Protection: Many SMT components, especially MOSFET transistors and CMOS ICs, are sensitive to ESD. Proper ESD Protection measures must be implemented during handling, assembly, and testing.
Applications of Surface-Mount Technology
SMT has enabled the development of a wide range of electronic devices and systems, including:
-
Consumer Electronics: Smartphones, tablets, laptops, gaming consoles, and wearables all heavily rely on SMT for their compact and high-performance designs.
-
Automotive Electronics: SMT is used in various automotive electronic systems, such as engine control units, infotainment systems, and advanced driver assistance systems (ADAS).
-
Medical Devices: SMT enables the development of compact and reliable medical devices, such as implantable pacemakers, hearing aids, and portable monitoring equipment.
-
Industrial Electronics: SMT is used in industrial control systems, automation equipment, and Internet of Things (IoT) devices for its reliability and robustness.
-
Aerospace and Defense: SMT is employed in avionics, satellite systems, and military equipment for its high performance and reliability in harsh environments.
The Future of Surface-Mount Technology
As electronic devices continue to become smaller, more powerful, and more complex, SMT will continue to evolve to meet the demands of the industry. Some trends and developments in SMT include:
-
Advanced Packaging Technologies: New packaging technologies, such as wafer-level packaging (WLP), 3D packaging, and system-in-package (SiP), are being developed to further increase component density and performance.
-
Miniaturization: SMT components are becoming even smaller, with some chip components measuring as small as 0.2 mm x 0.1 mm (01005 size). This trend enables the development of even more compact and lightweight electronic devices.
-
Flexible and Stretchable Electronics: SMT is being adapted for use in flexible and stretchable electronic circuits, enabling the development of novel applications such as wearable electronics and flexible displays.
-
High-Density Interconnect (HDI) PCBs: HDI PCBs, which feature finer pitch components and narrower traces, are becoming more common in SMT designs to accommodate higher component densities and faster signal speeds.
-
Automation and Industry 4.0: SMT manufacturing processes are becoming increasingly automated and integrated with Industry 4.0 technologies, such as robotics, machine vision, and artificial intelligence, to improve efficiency, quality, and flexibility.
As surface-mount technology continues to advance, it will play a crucial role in shaping the future of the electronics industry and enabling the development of innovative and transformative products.
Frequently Asked Questions (FAQ)
- What is the difference between surface-mount technology (SMT) and through-hole technology (THT)?
-
SMT components are mounted directly onto the surface of the PCB, while THT components have leads that are inserted through holes in the PCB and soldered on the opposite side. SMT allows for smaller components, higher component density, and better high-frequency performance compared to THT.
-
Can surface-mount components be soldered by hand?
-
Yes, surface-mount components can be soldered by hand using a fine-tip soldering iron, tweezers, and a steady hand. However, hand soldering SMT components can be challenging due to their small size and the need for precise control. It is more common to use reflow soldering or specialized soldering equipment for SMT Assembly.
-
Are all electronic components available in surface-mount packages?
-
While most modern electronic components are available in surface-mount packages, some specialized or high-power components may only be available in through-hole packages. However, the vast majority of components used in consumer electronics, industrial systems, and other applications are available in SMT packages.
-
What is the smallest surface-mount component size?
-
The smallest commonly used surface-mount component size is 01005, which measures 0.4 mm x 0.2 mm. Some specialized components may be even smaller, but they are not widely used due to the challenges in handling and assembly.
-
How can I learn more about designing and manufacturing with surface-mount technology?
- There are many resources available to learn about SMT design and manufacturing, including online tutorials, workshops, and courses offered by universities, industry associations, and electronics manufacturers. Practical experience through hands-on projects and collaboration with experienced designers and engineers is also valuable for developing SMT skills and knowledge.
Leave a Reply