Introduction to LED PCB
An LED PCB, or Light Emitting Diode Printed Circuit Board, is a specialized type of printed Circuit Board Designed to support and control LED lights. LEDs have become increasingly popular in recent years due to their energy efficiency, long lifespan, and versatility in various applications, ranging from simple indicator lights to complex lighting systems.
Key Components of an LED PCB
- Substrate
- Copper Traces
- Solder Mask
- Silkscreen
- LEDs
- Resistors
- Capacitors
- Connectors
Advantages of Using LED PCBs
Energy Efficiency
One of the primary advantages of using LED PCBs is their energy efficiency. LEDs consume significantly less power compared to traditional lighting solutions, such as incandescent or fluorescent bulbs. This reduced power consumption translates to lower energy bills and a smaller environmental footprint.
Long Lifespan
LEDs have a much longer lifespan compared to other lighting technologies. A typical LED can last up to 50,000 hours or more, which is several times longer than incandescent or fluorescent bulbs. This extended lifespan means less frequent replacements and lower maintenance costs.
Versatility
LED PCBs can be designed to support a wide range of LED types, colors, and configurations. This versatility allows for the creation of custom lighting solutions tailored to specific applications, such as automotive lighting, medical devices, or architectural lighting.
Compact Size
LEDs are much smaller than traditional light bulbs, allowing for more compact PCB designs. This space-saving characteristic is particularly beneficial in applications where size constraints are a concern, such as in portable devices or miniature displays.
LED PCB Design Considerations
Thermal Management
One of the critical design considerations for LED PCBs is thermal management. Although LEDs generate less heat compared to other lighting technologies, they still produce heat that needs to be dissipated effectively to ensure optimal performance and longevity. Poor thermal management can lead to reduced light output, color shifts, and premature failure of the LEDs.
To address thermal management, LED PCB designers employ various techniques, such as:
- Using high-quality, thermally conductive PCB materials
- Incorporating thermal vias to transfer heat from the LED to the PCB
- Designing adequate copper pour areas to dissipate heat
- Utilizing heat sinks or other cooling solutions
Current and Voltage Control
LEDs require precise current and voltage control to operate correctly and maintain consistent light output. Overdriving an LED with excessive current can lead to reduced lifespan or even immediate failure. To ensure proper current and voltage control, LED PCBs often incorporate the following components:
- Current-limiting resistors
- Constant current drivers
- Voltage Regulators
Light Distribution and Optics
Achieving the desired light distribution and optical performance is another important consideration in LED PCB design. Factors such as LED placement, lens design, and reflector geometry can significantly impact the overall light output and distribution.
Some common techniques for optimizing light distribution and optics include:
- Using secondary optics, such as lenses or reflectors, to shape the light beam
- Arranging LEDs in specific patterns to achieve uniform illumination
- Selecting LEDs with the appropriate viewing angle and intensity
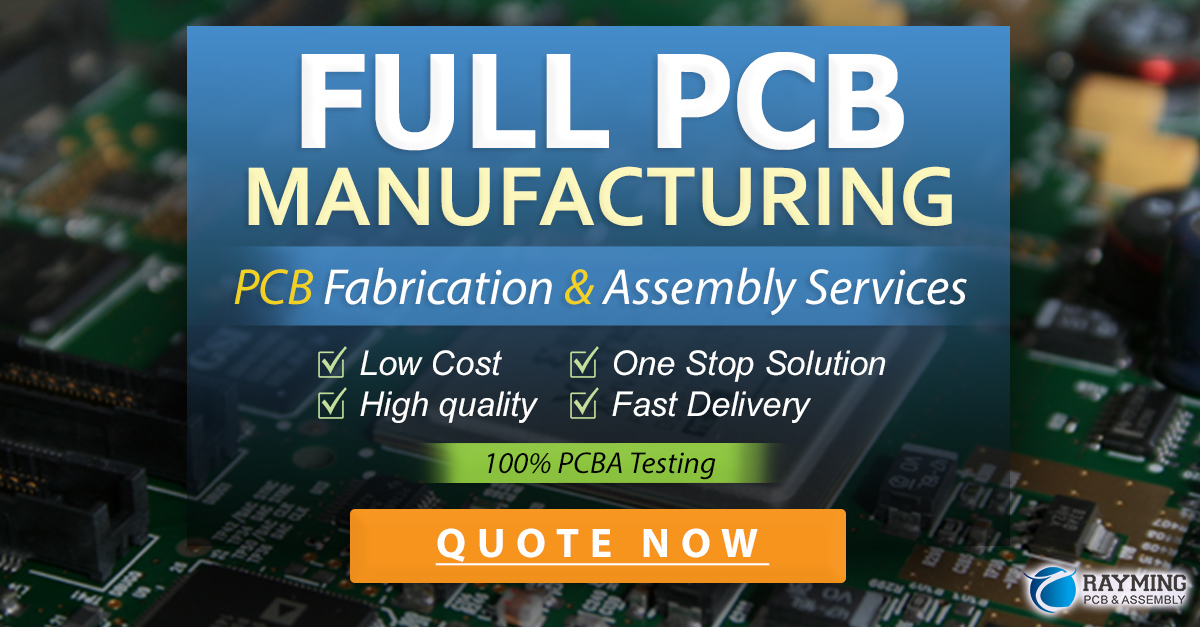
LED PCB Manufacturing Process
PCB Fabrication
The LED PCB manufacturing process begins with the fabrication of the printed circuit board itself. This involves the following steps:
- Substrate selection and preparation
- Copper lamination
- Photoresist application and exposure
- Etching and plating
- Solder mask application
- Silkscreen printing
LED Assembly
Once the PCB is fabricated, the LED assembly process can begin. This typically involves the following steps:
- Solder paste application
- LED placement
- Reflow soldering
- Inspection and testing
Quality Control
To ensure the quality and reliability of LED PCBs, manufacturers employ various quality control measures throughout the production process. These may include:
- Automated optical inspection (AOI)
- X-ray inspection
- Functional testing
- Burn-in testing
Applications of LED PCBs
LED PCBs find applications in a wide range of industries and products, such as:
- Automotive lighting
- General lighting
- Backlight units for displays
- Medical devices
- Signage and advertising
- Architectural lighting
- Portable devices
- Industrial equipment
Trends in LED PCB Technology
Miniaturization
As LED technology continues to advance, there is a growing trend towards miniaturization. Smaller LEDs and more compact PCB designs are enabling the development of increasingly compact and portable lighting solutions.
Smart Lighting
The integration of LED PCBs with smart technologies, such as wireless connectivity and sensors, is driving the growth of smart lighting systems. These systems offer features like remote control, color-changing capabilities, and automatic adjustments based on ambient conditions.
Flexible and Stretchable PCBs
The development of flexible and stretchable PCB materials is opening up new possibilities for LED lighting applications. These innovative PCBs can conform to curved surfaces and withstand bending and stretching, enabling the creation of flexible and wearable lighting solutions.
Choosing the Right LED PCB Manufacturer
When selecting an LED PCB manufacturer, consider the following factors:
- Experience and expertise in LED PCB design and manufacturing
- Quality control processes and certifications
- Production capacity and lead times
- Customer support and technical assistance
- Pricing and cost-effectiveness
FAQ
What is the difference between an LED and a traditional light bulb?
LEDs are solid-state devices that emit light through electroluminescence, while traditional light bulbs, such as incandescent or fluorescent bulbs, generate light through heating a filament or exciting a gas. LEDs are more energy-efficient, have a longer lifespan, and are more compact compared to traditional light bulbs.
Can LED PCBs be customized for specific applications?
Yes, LED PCBs can be custom-designed to meet the specific requirements of various applications. Factors such as LED type, color, intensity, and distribution can be tailored to suit the needs of a particular project.
How do I ensure proper thermal management in my LED PCB design?
To ensure proper thermal management in your LED PCB design, consider using high-quality, thermally conductive PCB materials, incorporating thermal vias, designing adequate copper pour areas, and utilizing heat sinks or other cooling solutions.
What are the benefits of using flexible or stretchable LED PCBs?
Flexible and stretchable LED PCBs offer the ability to conform to curved surfaces and withstand bending and stretching. This enables the creation of innovative lighting solutions, such as flexible displays, wearable devices, and automotive lighting that can adapt to complex shapes and contours.
How do I select the right LED PCB manufacturer for my project?
When choosing an LED PCB manufacturer, consider factors such as their experience and expertise in LED PCB design and manufacturing, quality control processes, production capacity, customer support, and pricing. It’s essential to partner with a manufacturer that can meet your specific requirements and provide reliable, high-quality LED PCBs.
Conclusion
LED PCBs have revolutionized the lighting industry, offering energy efficiency, long lifespan, versatility, and compact size. By understanding the key components, design considerations, and manufacturing processes involved in LED PCBs, engineers and designers can create innovative lighting solutions for a wide range of applications.
As LED technology continues to advance, trends such as miniaturization, smart lighting, and Flexible PCBs are shaping the future of LED PCB design and manufacturing. By staying informed about these developments and partnering with experienced LED PCB manufacturers, businesses can harness the power of LED lighting to create cutting-edge products and solutions.
Characteristic | LED | Incandescent | Fluorescent |
---|---|---|---|
Efficiency | High | Low | Moderate |
Lifespan | Long (up to 50,000 hours) | Short (1,000-2,000 hours) | Moderate (7,000-15,000 hours) |
Size | Compact | Bulky | Moderate |
Heat Generation | Low | High | Moderate |
Color Rendering | Excellent | Good | Moderate |
By embracing LED PCB technology and understanding its advantages, businesses can unlock new opportunities for growth, innovation, and sustainability in the rapidly evolving world of lighting.
Leave a Reply