Key Characteristics of Heavy Copper PCBs
Copper Weight
The primary distinguishing factor of heavy Copper PCBs is the increased copper weight. Standard PCBs typically have copper weights ranging from 0.5 oz to 2 oz per square foot. In contrast, heavy copper PCBs can have copper weights of 3 oz, 4 oz, 6 oz, or even higher, depending on the specific application requirements.
The following table compares the copper thickness and current carrying capacity of different copper weights:
Copper Weight (oz/ft²) | Copper Thickness (mm) | Current Carrying Capacity (A/mm) |
---|---|---|
0.5 | 0.0175 | 0.5 |
1 | 0.035 | 1 |
2 | 0.07 | 2 |
3 | 0.105 | 3 |
4 | 0.14 | 4 |
6 | 0.21 | 6 |
Improved Current Carrying Capacity
The increased copper weight in heavy copper PCBs allows for higher current carrying capacity compared to standard PCBs. This is particularly important in power electronics applications, where high currents need to be efficiently distributed across the board without causing excessive heat generation or voltage drop.
The improved current carrying capacity also enables designers to use fewer layers in the PCB Stack-Up, potentially reducing the overall board thickness and manufacturing costs.
Enhanced Thermal Management
Heavy copper PCBs offer better thermal management than standard PCBs due to the increased thermal conductivity of the thicker copper traces and planes. The improved heat dissipation helps to reduce hot spots on the board, minimizing the risk of component failure and extending the overall lifespan of the electronic device.
In some cases, heavy copper PCBs can even eliminate the need for additional heatsinks or cooling solutions, simplifying the overall system design and reducing costs.
Mechanical Strength and Durability
The thicker copper layers in heavy copper PCBs contribute to improved mechanical strength and durability. This is particularly important in applications that are subjected to harsh environmental conditions, such as extreme temperatures, vibrations, or shocks.
The enhanced mechanical properties also make heavy copper PCBs less susceptible to warping and twisting during the manufacturing process, ensuring better yields and reduced production costs.
Applications of Heavy Copper PCBs
Heavy copper PCBs find applications in various industries where high power handling, efficient thermal management, and reliability are crucial. Some of the key application areas include:
Power Electronics
Power electronics systems, such as switching power supplies, inverters, and motor drives, often require heavy copper PCBs to handle high currents and efficiently dissipate heat. The improved electrical and thermal performance of heavy copper PCBs ensures reliable operation and extends the lifespan of power electronic devices.
Automotive Electronics
Modern automotive systems rely heavily on electronics for various functions, such as engine management, battery management, and advanced driver assistance systems (ADAS). Heavy copper PCBs are used in automotive electronics to provide reliable performance in harsh operating conditions, including extreme temperatures, vibrations, and electromagnetic interference (EMI).
Industrial Equipment
Industrial equipment, such as welding machines, CNC machines, and robotics systems, often incorporate heavy copper PCBs to handle high power requirements and ensure reliable operation in demanding environments. The enhanced thermal management and mechanical strength of heavy copper PCBs contribute to the overall robustness and longevity of industrial electronic systems.
Telecommunications Infrastructure
Telecommunications infrastructure, including base stations, routers, and switches, requires high-power PCBs to handle the increasing data transmission rates and network traffic. Heavy copper PCBs are used in these applications to provide efficient power distribution, improved signal integrity, and effective thermal management.
Aerospace and Defense Systems
Aerospace and defense systems demand the highest levels of reliability and performance, often in extreme environmental conditions. Heavy copper PCBs are used in these applications to ensure robust operation, withstand harsh environments, and meet stringent safety and regulatory requirements.
Design Considerations for Heavy Copper PCBs
Designing heavy copper PCBs requires careful consideration of various factors to ensure optimal performance and manufacturability. Some of the key design considerations include:
Trace Width and Spacing
When designing heavy copper PCBs, it is essential to properly size the trace widths and spacings to accommodate the increased copper weight. Thicker copper traces require wider minimum trace widths and spacings to ensure proper etching and avoid short circuits.
The following table provides general guidelines for minimum trace widths and spacings based on different copper weights:
Copper Weight (oz/ft²) | Minimum Trace Width (mm) | Minimum Trace Spacing (mm) |
---|---|---|
0.5 – 1 | 0.1 | 0.1 |
2 | 0.15 | 0.15 |
3 | 0.2 | 0.2 |
4 – 6 | 0.25 | 0.25 |
Thermal Management
Designing effective thermal management is crucial for heavy copper PCBs to ensure efficient heat dissipation and prevent component failure. This can be achieved through various techniques, such as:
- Incorporating thermal vias to transfer heat from the components to the copper layers
- Using large copper pour areas to spread the heat evenly across the board
- Placing temperature-sensitive components away from high-power components
- Utilizing thermal interface materials (TIMs) to enhance heat transfer between components and the PCB
Layer Stack-up
The layer stack-up of a heavy copper PCB should be carefully designed to optimize electrical performance, thermal management, and manufacturability. Some key considerations include:
- Placing heavy copper layers strategically to minimize the number of layers required
- Using symmetrical stack-ups to prevent warping and ensure even copper distribution
- Incorporating dedicated ground and power planes to improve signal integrity and reduce EMI
- Using appropriate dielectric materials to achieve the desired electrical properties and thermal performance
Manufacturing Constraints
Heavy copper PCBs pose unique manufacturing challenges due to the increased copper weight and associated processing requirements. Designers should work closely with the PCB manufacturer to ensure that the design is compatible with their manufacturing capabilities and guidelines. Some key manufacturing constraints to consider include:
- Minimum Hole Sizes and pad diameters for drilling and plating
- Copper plating limitations and maximum aspect ratios
- Etching and soldermask registration tolerances
- Minimum Annular Ring requirements for vias and through-holes
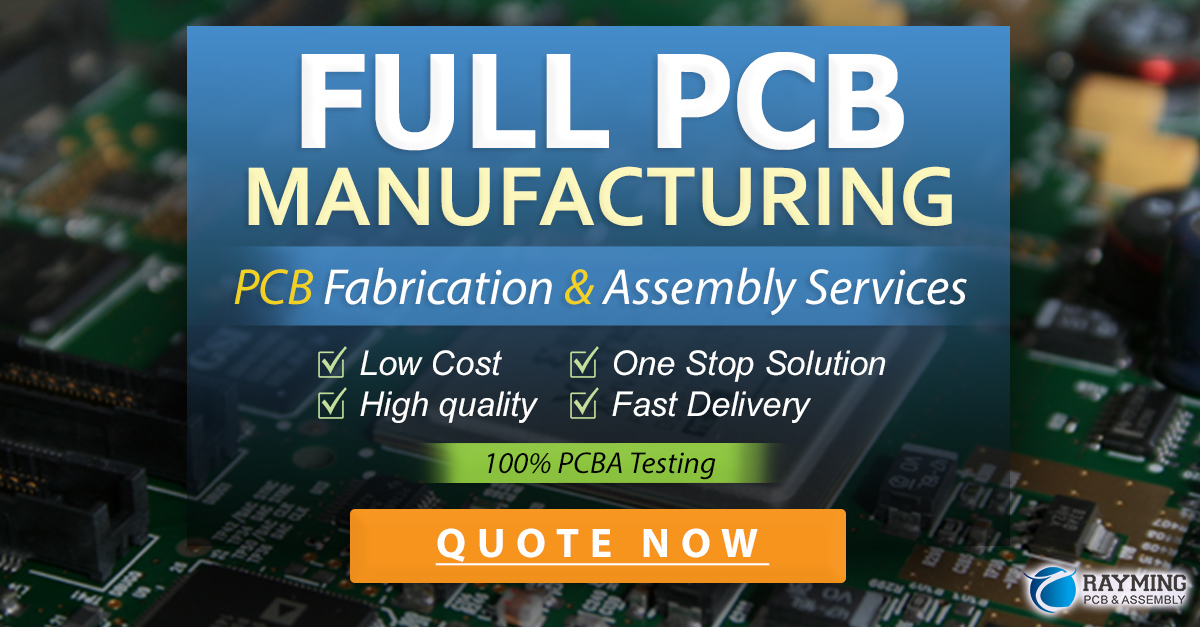
FAQ
1. What is the difference between heavy copper PCBs and standard PCBs?
Heavy copper PCBs have thicker copper traces and planes compared to standard PCBs, typically with copper weights of 3 oz/ft² or higher. This increased copper weight provides improved electrical and thermal performance, making heavy copper PCBs suitable for high-power applications.
2. What are the benefits of using heavy copper PCBs?
The benefits of using heavy copper PCBs include:
– Higher current carrying capacity
– Improved thermal management and heat dissipation
– Enhanced mechanical strength and durability
– Potential for reducing the number of layers in the PCB stack-up
– Elimination of additional heatsinks or cooling solutions in some cases
3. In what industries are heavy copper PCBs commonly used?
Heavy copper PCBs are commonly used in industries that require high power handling, efficient thermal management, and reliability, such as:
– Power electronics
– Automotive electronics
– Industrial equipment
– Telecommunications infrastructure
– Aerospace and defense systems
4. What are the key design considerations for heavy copper PCBs?
When designing heavy copper PCBs, key considerations include:
– Properly sizing trace widths and spacings to accommodate the increased copper weight
– Designing effective thermal management through techniques such as thermal vias, copper pour areas, and strategic component placement
– Optimizing the layer stack-up for electrical performance, thermal management, and manufacturability
– Ensuring compatibility with the PCB manufacturer’s capabilities and guidelines
5. Are heavy copper PCBs more expensive than standard PCBs?
Yes, heavy copper PCBs are generally more expensive than standard PCBs due to the increased copper weight and associated manufacturing complexities. However, the improved performance and potential for reducing the overall system complexity can offset the higher initial costs in many applications.
Conclusion
Heavy copper PCBs offer superior electrical and thermal performance compared to standard PCBs, making them an essential component in high-power applications across various industries. By understanding the key characteristics, applications, and design considerations of heavy copper PCBs, engineers and designers can create robust and reliable electronic systems that meet the demanding requirements of modern technology.
As the demand for high-power electronics continues to grow, the importance of heavy copper PCBs will only increase. Designers who stay up-to-date with the latest advancements in heavy copper PCB technology and manufacturing processes will be well-positioned to create innovative solutions that push the boundaries of performance and reliability in their respective fields.
Leave a Reply