What is an Annular Ring?
An annular ring, also known as a printed circuit board (PCB) annular ring, is a circular copper pad that surrounds a drilled hole on a PCB. The primary purpose of an annular ring is to provide a reliable electrical connection between the component lead and the copper trace on the PCB. Annular rings play a crucial role in ensuring the integrity and functionality of electronic devices.
Key Features of Annular Rings
- Circular copper pad surrounding a drilled hole
- Provides electrical connection between component lead and copper trace
- Ensures integrity and functionality of electronic devices
- Manufactured using various techniques, such as etching, plating, and drilling
Importance of Annular Rings in PCB Manufacturing
Annular rings are essential in PCB manufacturing for several reasons:
-
Electrical Connectivity: Annular rings ensure a reliable electrical connection between the component lead and the copper trace on the PCB. This connection is vital for the proper functioning of the electronic device.
-
Mechanical Stability: Annular rings provide mechanical support to the component leads, preventing them from moving or becoming disconnected during the assembly process or when the device is in use.
-
Solderability: Annular rings facilitate the soldering process by providing a sufficient surface area for the solder to adhere to, creating a strong and reliable joint between the component lead and the PCB.
-
Signal Integrity: Properly designed annular rings help maintain signal integrity by minimizing impedance discontinuities and reducing the risk of signal reflections or distortions.
Annular Ring Design Considerations
When designing annular rings for PCBs, several factors must be taken into account to ensure optimal performance and reliability:
1. Annular Ring Size
The size of the annular ring is a critical design consideration. The ring must be large enough to provide a sufficient surface area for soldering and to accommodate any manufacturing tolerances. However, it should not be too large, as this can lead to unnecessary copper usage and increased manufacturing costs.
The minimum annular ring size is typically determined by the PCB manufacturer’s capabilities and the specific requirements of the electronic device. Industry standards, such as IPC-6012, provide guidelines for minimum annular ring sizes based on the hole diameter and the PCB’s class (Table 1).
Hole Diameter (mm) | Class 1 (mm) | Class 2 (mm) | Class 3 (mm) |
---|---|---|---|
0.3 – 0.5 | 0.05 | 0.1 | 0.15 |
0.5 – 1.0 | 0.1 | 0.15 | 0.2 |
1.0 – 2.0 | 0.15 | 0.2 | 0.25 |
2.0 – 3.0 | 0.2 | 0.25 | 0.3 |
Table 1: Minimum Annular Ring Sizes (IPC-6012)
2. Drill Hole Size and Tolerance
The drill hole size and tolerance are closely related to the annular ring size. The hole must be large enough to accommodate the component lead while allowing for proper soldering. However, it should not be too large, as this can weaken the mechanical stability of the connection.
Drill hole tolerances are essential to ensure that the hole is positioned accurately relative to the annular ring. Misaligned holes can lead to insufficient annular ring coverage, compromising the electrical and mechanical integrity of the connection.
3. Copper Thickness
The copper thickness of the annular ring is another important design consideration. Thicker copper provides better current carrying capacity and improved mechanical strength. However, increasing the copper thickness also increases the manufacturing cost and can make the PCB more challenging to etch.
The copper thickness is typically specified in ounces per square foot (oz/ft²). Common copper thicknesses for PCBs range from 0.5 oz/ft² to 2 oz/ft², with 1 oz/ft² being the most widely used (Table 2).
Copper Thickness (oz/ft²) | Thickness (µm) |
---|---|
0.5 | 17.5 |
1.0 | 35 |
2.0 | 70 |
Table 2: Common Copper Thicknesses for PCBs
4. Solder Mask and Solder Paste
The solder mask and solder paste are essential components in the PCB assembly process that directly impact the annular ring.
Solder mask is a protective layer applied to the PCB surface, covering the copper traces while leaving the annular rings exposed. The solder mask helps prevent solder bridges and short circuits during the soldering process. It is important to ensure that the solder mask aperture is properly aligned with the annular ring to allow for optimal soldering.
Solder paste is a mixture of tiny solder particles suspended in flux. It is applied to the annular rings before component placement and soldering. The solder paste volume and composition must be carefully controlled to ensure a reliable solder joint. Insufficient solder paste can lead to weak or incomplete solder joints, while excessive solder paste can cause solder bridging or other defects.
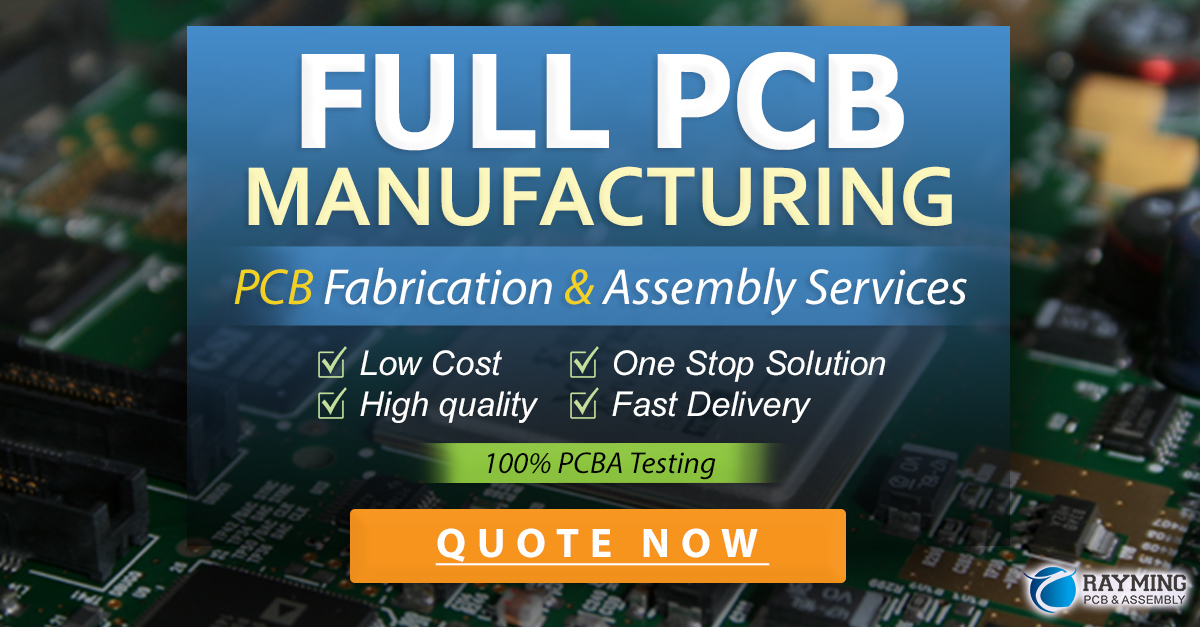
Annular Ring Manufacturing Techniques
Several manufacturing techniques are used to create annular rings on PCBs. The choice of technique depends on factors such as the PCB material, the required accuracy, and the production volume.
1. Etching
Etching is the most common method for creating annular rings on PCBs. The process involves the following steps:
- Applying a photoresist layer to the copper-clad PCB
- Exposing the photoresist to UV light through a photomask with the desired annular ring pattern
- Developing the photoresist to remove the exposed areas
- Etching away the unwanted copper using a chemical solution, leaving the annular rings and traces intact
- Stripping the remaining photoresist layer
Etching is a cost-effective and versatile method suitable for a wide range of PCB designs and production volumes.
2. Plating
Plating is another technique used to create annular rings, particularly for multi-layer PCBs. The process involves the following steps:
- Drilling holes in the PCB at the desired locations
- Applying a thin layer of copper to the hole walls using electroless copper plating
- Electroplating additional copper to increase the thickness of the annular rings
- Applying a photoresist layer and exposing it to UV light through a photomask with the desired annular ring pattern
- Developing the photoresist and etching away the unwanted copper
- Stripping the remaining photoresist layer
Plating allows for the creation of consistent and uniform annular rings, even in high-density PCB designs.
3. Drilling
Drilling is a fundamental process in PCB manufacturing that is closely related to annular ring creation. The drilling process involves:
- Placing the PCB on a drilling machine
- Using a computer-controlled drill bit to create holes at the desired locations
- Cleaning the holes to remove any debris
Accurate drilling is essential for ensuring that the annular rings are properly positioned and sized relative to the holes. Modern CNC drilling machines offer high precision and repeatability, enabling the creation of high-quality annular rings.
Annular Ring Inspection and Quality Control
Inspecting annular rings and ensuring their quality is crucial for the reliability and performance of electronic devices. Several methods are used to inspect annular rings:
1. Visual Inspection
Visual inspection is the most basic method for checking annular rings. This process involves examining the PCB under magnification to look for defects such as:
- Insufficient annular ring coverage
- Misaligned holes
- Solder mask aberrations
- Contamination or debris
While visual inspection is simple and cost-effective, it is subject to human error and may not detect subtle defects.
2. Automated Optical Inspection (AOI)
Automated optical inspection (AOI) uses computer vision technology to scan the PCB and detect annular ring defects. AOI systems capture high-resolution images of the PCB and use advanced algorithms to analyze the images for anomalies.
AOI offers several advantages over visual inspection:
- Faster inspection times
- Consistent and repeatable results
- Ability to detect subtle defects
- Automated data collection and reporting
However, AOI systems can be expensive and may require skilled operators to set up and maintain.
3. X-Ray Inspection
X-ray inspection is a non-destructive testing method that uses X-rays to create images of the internal structure of the PCB. This technique is particularly useful for inspecting annular rings in multi-layer PCBs, where the rings are not visible from the surface.
X-ray inspection can detect defects such as:
- Voids or cracks in the plated through-holes
- Insufficient copper thickness
- Misaligned or missing annular rings
While X-ray inspection provides detailed insights into the internal structure of the PCB, it is a more expensive and time-consuming process compared to visual inspection or AOI.
Annular Ring Repair and Rework
Despite careful design and manufacturing, annular ring defects may still occur. In some cases, these defects can be repaired or reworked to salvage the PCB and avoid costly scrap.
1. Manual Rework
Manual rework involves using hand tools and techniques to repair annular ring defects. Some common manual rework methods include:
- Adding solder to insufficient annular rings
- Removing excess solder or solder bridges
- Repositioning misaligned components
- Cleaning contaminated or corroded annular rings
Manual rework requires skilled technicians and can be time-consuming, but it is often the most cost-effective option for small-scale repairs.
2. Automated Rework
Automated rework systems use computer-controlled tools and processes to repair annular ring defects. These systems can perform tasks such as:
- Precision component placement
- Solder paste dispensing
- Localized heating for solder reflow
- Automated cleaning and inspection
Automated rework offers higher accuracy and consistency compared to manual methods, but the equipment can be expensive and may require specialized training to operate.
3. Selective Plating
Selective plating is a technique used to repair annular rings by selectively depositing additional copper onto the defective area. This process involves:
- Masking off the surrounding area to protect it from plating
- Applying a thin layer of copper using electroless plating
- Electroplating additional copper to build up the annular ring
- Removing the masking and cleaning the PCB
Selective plating allows for targeted repairs without affecting the rest of the PCB, making it a useful technique for addressing localized annular ring defects.
Frequently Asked Questions (FAQ)
-
What is the purpose of an annular ring in PCB design?
The purpose of an annular ring in PCB design is to provide a reliable electrical connection between the component lead and the copper trace on the PCB. Annular rings also offer mechanical stability and facilitate the soldering process. -
How do I determine the minimum annular ring size for my PCB?
The minimum annular ring size is typically determined by the PCB manufacturer’s capabilities and the specific requirements of the electronic device. Industry standards, such as IPC-6012, provide guidelines for minimum annular ring sizes based on the hole diameter and the PCB’s class. -
What are the most common methods for manufacturing annular rings?
The most common methods for manufacturing annular rings are etching, plating, and drilling. Etching is a cost-effective and versatile method, while plating is often used for multi-layer PCBs. Drilling is a fundamental process that is closely related to annular ring creation. -
How can I inspect annular rings for defects?
Annular rings can be inspected using visual inspection, automated optical inspection (AOI), or X-ray inspection. Visual inspection is the most basic method, while AOI offers faster and more consistent results. X-ray inspection is useful for detecting internal defects in multi-layer PCBs. -
What should I do if I discover annular ring defects on my PCB?
If you discover annular ring defects on your PCB, you may be able to repair or rework the defects using manual rework, automated rework, or selective plating techniques. The choice of repair method depends on the nature and extent of the defect, as well as the available resources and expertise.
Conclusion
Annular rings are essential components in PCB manufacturing that ensure reliable electrical connections, mechanical stability, and proper soldering. Designing and manufacturing annular rings requires careful consideration of factors such as size, drill hole tolerance, copper thickness, and solder mask and paste.
Various manufacturing techniques, including etching, plating, and drilling, are used to create annular rings on PCBs. Inspecting annular rings for defects is crucial for ensuring the quality and reliability of electronic devices, and methods such as visual inspection, AOI, and X-ray inspection are commonly employed.
When annular ring defects occur, repair and rework techniques such as manual rework, automated rework, and selective plating can be used to salvage the PCB and avoid costly scrap.
By understanding the importance of annular rings and following best practices in design, manufacturing, inspection, and repair, PCB manufacturers can produce high-quality, reliable electronic devices that meet the ever-increasing demands of today’s technology-driven world.
Leave a Reply