Introduction to Electronic Contract Manufacturing
Electronic Contract Manufacturing (ECM) is a business model where a company, known as the contract manufacturer, produces electronic components or products on behalf of another company, known as the original equipment manufacturer (OEM). The OEM outsources the manufacturing process to the contract manufacturer, who is responsible for assembling, testing, and delivering the final product according to the OEM’s specifications and requirements.
ECM has become increasingly popular in the electronics industry due to its numerous benefits, such as cost reduction, flexibility, and access to specialized expertise and equipment. This guide will provide a comprehensive overview of Electronic Contract Manufacturing, including its advantages, challenges, and best practices.
The Electronic Contract Manufacturing Process
The ECM process typically involves the following steps:
-
Design and Development: The OEM provides the contract manufacturer with the product design, specifications, and requirements. The contract manufacturer may also offer design support and recommendations to optimize the product for manufacturability and cost-effectiveness.
-
Prototyping: The contract manufacturer creates prototypes of the product to validate the design and functionality. This step allows for any necessary adjustments or improvements before mass production begins.
-
Component sourcing: The contract manufacturer procures the necessary components and materials from suppliers, often leveraging their established relationships and purchasing power to secure better prices and lead times.
-
Assembly: The contract manufacturer assembles the electronic components and subassemblies according to the OEM’s specifications. This process may involve various techniques such as surface mount technology (SMT), through-hole assembly, and manual assembly.
-
Testing and Quality Control: The assembled products undergo rigorous testing and quality control procedures to ensure they meet the OEM’s requirements and industry standards. This may include Functional Testing, environmental testing, and reliability testing.
-
Packaging and Shipping: The finished products are packaged and shipped to the OEM or directly to their customers, depending on the agreed-upon terms and logistics arrangements.
Throughout the ECM process, effective communication and collaboration between the OEM and the contract manufacturer are crucial to ensure a smooth and successful outcome.
Advantages of Electronic Contract Manufacturing
ECM offers several key advantages for OEMs:
-
Cost Reduction: By outsourcing the manufacturing process, OEMs can avoid the high capital investments required for setting up and maintaining their own production facilities. Contract manufacturers often have economies of scale and can offer lower unit costs due to their higher production volumes and efficient operations.
-
Flexibility and Scalability: ECM allows OEMs to quickly ramp up or down production volumes based on market demand, without the need to invest in additional equipment or workforce. This flexibility enables OEMs to respond more effectively to changing market conditions and customer requirements.
-
Access to Specialized Expertise and Equipment: Contract manufacturers often have specialized expertise and state-of-the-art equipment that may not be economically feasible for OEMs to acquire or maintain in-house. By partnering with a contract manufacturer, OEMs can leverage this expertise and technology to improve product quality, reliability, and performance.
-
Focus on Core Competencies: Outsourcing the manufacturing process allows OEMs to focus on their core competencies, such as product design, marketing, and sales. This focus can lead to improved innovation, faster time-to-market, and enhanced customer satisfaction.
-
Risk Mitigation: ECM helps OEMs mitigate various risks associated with manufacturing, such as supply chain disruptions, quality issues, and regulatory compliance. Contract manufacturers often have robust risk management processes and contingency plans in place to ensure continuity of supply and product quality.
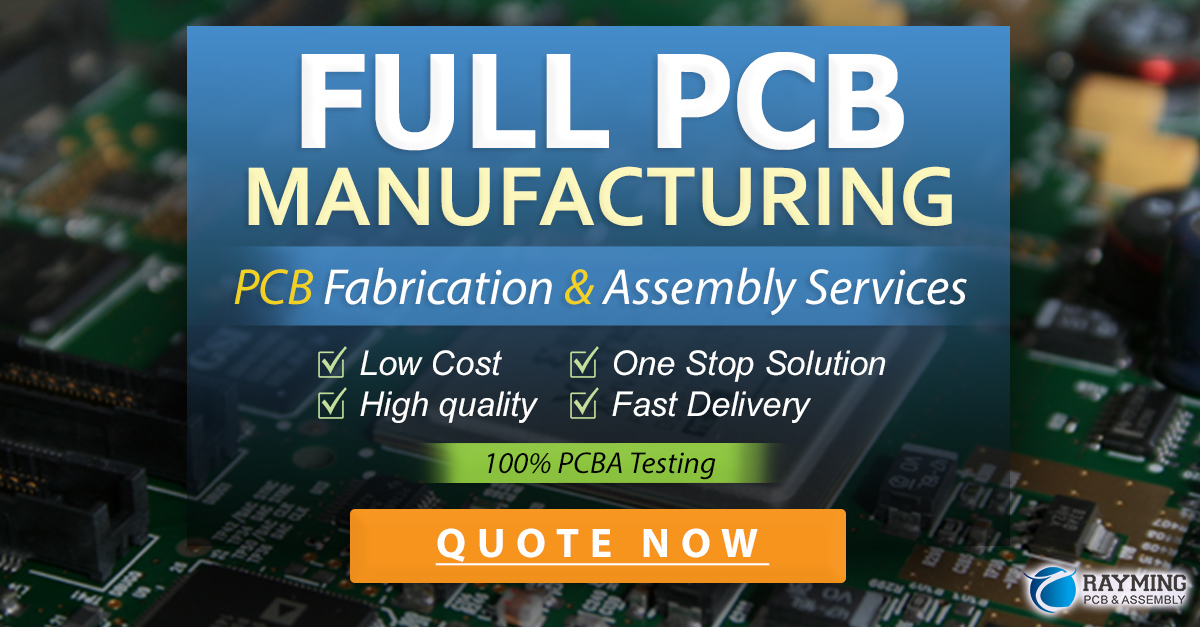
Challenges and Considerations in Electronic Contract Manufacturing
While ECM offers numerous benefits, there are also some challenges and considerations that OEMs should be aware of:
-
Intellectual Property (IP) Protection: When outsourcing the manufacturing process, OEMs need to ensure that their IP rights are adequately protected. This may involve implementing non-disclosure agreements (NDAs), confidentiality clauses, and other legal safeguards to prevent unauthorized access or use of proprietary information.
-
Communication and Collaboration: Effective communication and collaboration between the OEM and the contract manufacturer are essential for successful ECM. Cultural differences, language barriers, and time zone differences can sometimes pose challenges in this regard. Establishing clear lines of communication, regular progress updates, and well-defined roles and responsibilities can help mitigate these issues.
-
Quality Control and Compliance: While contract manufacturers are responsible for ensuring product quality and compliance with relevant standards and regulations, OEMs still need to maintain oversight and conduct regular audits to verify that their requirements are being met. Establishing a robust quality management system and defining clear quality metrics and acceptance criteria are crucial for maintaining product quality and reliability.
-
Supply Chain Management: OEMs need to work closely with their contract manufacturers to manage the supply chain effectively. This includes ensuring the availability and quality of components, managing inventory levels, and coordinating logistics and delivery schedules. Establishing a transparent and collaborative supply chain management process can help minimize disruptions and ensure timely delivery of products.
-
Cost Management: While ECM can lead to cost savings, OEMs need to carefully manage and monitor costs throughout the manufacturing process. This includes negotiating favorable terms with contract manufacturers, optimizing product designs for cost-effectiveness, and implementing cost reduction initiatives where possible. Regular cost analyses and benchmarking can help identify opportunities for further cost optimization.
Best Practices in Electronic Contract Manufacturing
To ensure a successful and mutually beneficial ECM Partnership, OEMs should consider the following best practices:
-
Partner Selection: Choosing the right contract manufacturer is crucial for the success of the ECM relationship. OEMs should evaluate potential partners based on factors such as technical capabilities, quality standards, financial stability, and track record of delivering similar products. Conducting thorough due diligence and reference checks can help in making an informed decision.
-
Clear Specifications and Requirements: OEMs should provide clear and comprehensive product specifications and requirements to the contract manufacturer. This includes detailed design files, Bill of Materials (BOM), assembly instructions, and quality and performance criteria. Ensuring that all requirements are well-defined and understood by both parties can help avoid misunderstandings and delays during the manufacturing process.
-
Regular Communication and Collaboration: Establishing regular communication channels and collaboration mechanisms is essential for effective ECM. This may involve setting up regular progress reviews, joint problem-solving sessions, and performance evaluations. Encouraging open and transparent communication can help identify and address issues early, leading to better outcomes.
-
Quality Management: Implementing a robust quality management system is critical for ensuring product quality and reliability. This includes defining clear quality metrics, conducting regular quality audits, and implementing corrective and preventive actions (CAPA) when necessary. OEMs should work closely with their contract manufacturers to establish and maintain effective quality management processes.
-
Continuous Improvement: ECM partnerships should focus on continuous improvement and innovation. This may involve jointly identifying opportunities for process optimization, cost reduction, and product enhancements. Encouraging a culture of continuous improvement and shared goals can help strengthen the partnership and drive long-term success.
FAQs
- What is the difference between Electronic Contract Manufacturing and Original Equipment Manufacturing?
- Electronic Contract Manufacturing (ECM) refers to the outsourcing of the manufacturing process to a third-party company, known as the contract manufacturer. The contract manufacturer is responsible for producing the electronic components or products according to the OEM’s specifications and requirements.
-
Original Equipment Manufacturing (OEM) refers to the company that designs and owns the intellectual property of the product. The OEM may choose to manufacture the product in-house or outsource the manufacturing process to a contract manufacturer.
-
What are the key factors to consider when selecting an Electronic Contract Manufacturer?
- Technical capabilities and expertise in manufacturing similar products
- Quality standards and certifications (e.g., ISO 9001, IPC Standards)
- Financial stability and long-term viability
- Track record of delivering products on time and within budget
- Geographical location and proximity to target markets
- Intellectual property protection and confidentiality measures
- Flexibility and scalability to accommodate changing production volumes
-
Cost competitiveness and value-added services offered
-
How can OEMs ensure the protection of their intellectual property when outsourcing to an Electronic Contract Manufacturer?
- Implement non-disclosure agreements (NDAs) and confidentiality clauses in the contract
- Clearly define the ownership and usage rights of intellectual property
- Establish secure data transfer and storage protocols
- Conduct regular audits and inspections to verify compliance with IP protection measures
- Limit access to sensitive information and designs to only the necessary personnel
-
Consider filing for patents, trademarks, or copyrights to protect critical IP assets
-
What are the common quality management standards and certifications in Electronic Contract Manufacturing?
- ISO 9001: Quality Management System
- IPC standards (e.g., IPC-A-610, IPC-J-STD-001): Guidelines for printed circuit board assembly and soldering
- ISO 13485: Medical Device Quality Management System
- AS9100: Quality Management System for Aerospace and Defense Industries
- IATF 16949: Quality Management System for Automotive Industry
-
ISO 14001: Environmental Management System
-
How can OEMs effectively manage the supply chain when working with an Electronic Contract Manufacturer?
- Establish clear communication channels and processes for sharing supply chain information
- Jointly develop and maintain a comprehensive bill of materials (BOM) and approved vendor list (AVL)
- Implement a robust inventory management system to ensure the availability of components and materials
- Regularly monitor and assess supplier performance, including quality, delivery, and cost metrics
- Develop contingency plans and risk mitigation strategies to address potential supply chain disruptions
- Foster a collaborative and transparent relationship with the contract manufacturer to optimize supply chain efficiency
Conclusion
Electronic Contract Manufacturing offers numerous benefits for OEMs, including cost reduction, flexibility, access to specialized expertise, and risk mitigation. By outsourcing the manufacturing process to a reliable and competent contract manufacturer, OEMs can focus on their core competencies and drive innovation and growth.
However, successful ECM partnerships require careful planning, effective communication, and robust quality management processes. OEMs should select their contract manufacturing partners based on a thorough evaluation of their capabilities, track record, and alignment with their business objectives. Establishing clear specifications, regular collaboration, and a focus on continuous improvement are key to achieving long-term success in Electronic Contract Manufacturing.
As the electronics industry continues to evolve and face new challenges, such as rapid technological advancements, shorter product lifecycles, and increased global competition, Electronic Contract Manufacturing will play an increasingly critical role in enabling OEMs to stay competitive and meet the changing demands of their customers. By leveraging the expertise and capabilities of contract manufacturers, OEMs can drive innovation, improve product quality, and accelerate time-to-market, ultimately leading to greater success in the dynamic and fast-paced world of electronics.
Leave a Reply