What is a Bill of Materials?
A Bill of Materials (BOM) is a comprehensive list of all the components, parts, and materials required to manufacture a product. It serves as a crucial document in the production process, ensuring that all necessary items are accounted for and available when needed. The BOM typically includes part numbers, descriptions, quantities, and sometimes even supplier information.
Types of Bill of Materials
There are several types of BOMs, each serving a specific purpose in the manufacturing process:
-
Engineering BOM (EBOM): This type of BOM is created by the engineering team and includes all the components and parts required to design and prototype the product.
-
Manufacturing BOM (MBOM): The MBOM is derived from the EBOM and is tailored for the manufacturing process. It includes all the components and parts needed to produce the final product.
-
Sales BOM (SBOM): The SBOM is a simplified version of the BOM, used by the sales team to communicate the product’s components and features to customers.
-
Service BOM (SVBOM): This BOM lists all the components and parts required for the maintenance and repair of a product.
Designing a Bill of Materials Type File
When designing a BOM type file, it’s essential to consider the following factors:
1. File Format
Choose a file format that is compatible with your company’s software systems and can be easily shared among different departments. Common file formats for BOMs include:
- Excel spreadsheets
- CSV (Comma-Separated Values) files
- XML (eXtensible Markup Language) files
- PDFs (Portable Document Format)
2. File Structure
Organize your BOM file in a logical and consistent manner. A well-structured BOM should include the following information:
Column Name | Description |
---|---|
Item No. | A unique identifier for each component or part |
Part Name | A brief description of the component or part |
Quantity | The number of units required for each component or part |
Unit of Measure | The standard unit used to measure the quantity (e.g., pieces, liters, kilograms) |
Part Number | The manufacturer’s or supplier’s identifying number for the component or part |
Description | A more detailed description of the component or part, including specifications and materials |
Supplier | The name of the supplier or manufacturer of the component or part |
Cost | The cost per unit of the component or part |
3. Hierarchy and Indentation
Use a hierarchical structure and indentation to represent the relationships between components and subassemblies. This makes the BOM easier to read and understand.
Example:
1. Bicycle
1.1 Frame
1.1.1 Top Tube
1.1.2 Down Tube
1.1.3 Seat Tube
1.2 Wheels
1.2.1 Front Wheel
1.2.1.1 Rim
1.2.1.2 Spokes
1.2.1.3 Hub
1.2.2 Rear Wheel
1.2.2.1 Rim
1.2.2.2 Spokes
1.2.2.3 Hub
1.3 Drivetrain
1.3.1 Crankset
1.3.2 Chain
1.3.3 Cassette
4. Revision Control
Implement a revision control system to track changes made to the BOM over time. This helps maintain accuracy and ensures that all team members are working with the most up-to-date version of the document.
Include the following information in your revision control system:
- Revision number
- Date of revision
- Name of the person making the revision
- Description of the changes made
5. Integration with Other Systems
Consider integrating your BOM file with other systems, such as:
- Enterprise Resource Planning (ERP) software
- Product Lifecycle Management (PLM) software
- Computer-Aided Design (CAD) software
Integration helps streamline the product development process and ensures that all departments are working with the same data.
Best Practices for Maintaining a Bill of Materials
To ensure the accuracy and effectiveness of your BOM, follow these best practices:
-
Regularly update the BOM: As changes occur in the product design or manufacturing process, update the BOM accordingly. This helps prevent errors and delays in production.
-
Use consistent naming conventions: Establish and adhere to a consistent naming convention for components and parts. This makes it easier to search for and identify items within the BOM.
-
Collaborate with other departments: Encourage collaboration between engineering, manufacturing, procurement, and other relevant departments to ensure that the BOM accurately reflects the needs of all stakeholders.
-
Conduct regular audits: Periodically review the BOM to verify its accuracy and completeness. This helps identify any discrepancies or outdated information.
-
Train team members: Provide training to all team members who will be using the BOM to ensure that they understand its structure, purpose, and how to maintain it properly.
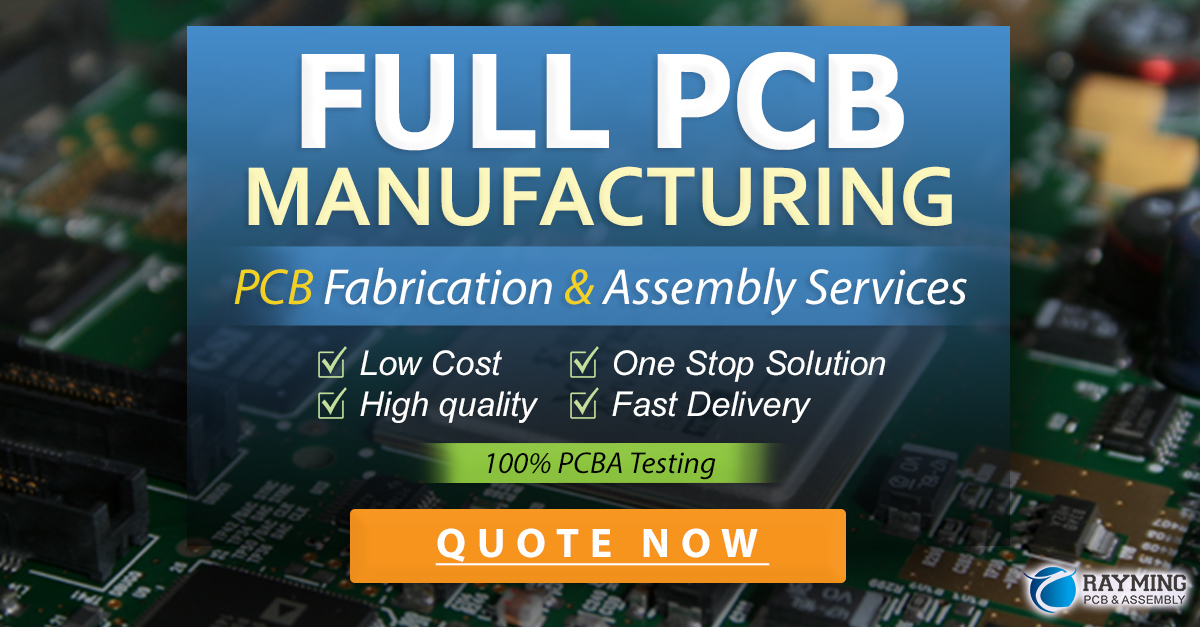
Frequently Asked Questions (FAQ)
-
What is the difference between a BOM and a parts list?
A BOM is a more comprehensive document that includes not only the list of parts but also the quantities, descriptions, and hierarchical relationships between components. A parts list, on the other hand, is a simpler document that only lists the individual components without specifying the quantities or relationships. -
How often should I update my BOM?
It’s essential to update your BOM whenever changes occur in the product design or manufacturing process. This could include changes to component specifications, suppliers, or quantities. Regular updates help ensure that all team members are working with the most accurate and up-to-date information. -
Can I use the same BOM for different products?
While some components or subassemblies may be shared across different products, it’s generally recommended to create a unique BOM for each product. This helps maintain clarity and prevents confusion between different product variations. -
How do I handle component substitutions in my BOM?
If a component needs to be substituted, create a new revision of the BOM and clearly indicate the substitution. Include the reason for the substitution, the new component’s specifications, and any impact on the overall product design or manufacturing process. -
What should I do if I find errors in my BOM?
If you discover errors in your BOM, correct them as soon as possible and create a new revision of the document. Communicate the changes to all relevant team members and ensure that everyone is working with the updated version. Conduct a root cause analysis to determine how the error occurred and implement measures to prevent similar issues in the future.
Conclusion
A well-designed and maintained Bill of Materials is essential for streamlining the product development and manufacturing process. By following best practices and utilizing appropriate file formats, structures, and revision control systems, you can ensure that your BOM serves as an accurate and effective tool for your organization. Regular collaboration, audits, and training will help maintain the integrity of your BOM and contribute to the overall success of your product.
Leave a Reply