What is Functional Testing?
Functional testing, also known as functional test, is a quality assurance (QA) process where a completely assembled and powered PCB is comprehensively tested to validate its functionality. The goal is to verify that the board does what it is supposed to do and meets all functional requirements, catching any defects or issues before the PCB is integrated into a larger system or shipped to the customer.
Functional testing differs from other common tests like in-circuit test (ICT) that are done earlier in the process and focus more on testing individual components and solder connections on the board. Functional test looks at the PCB as a complete system and tests its end-to-end functionality, inputs/outputs, interfaces, etc. under normal operating conditions. It is usually one of the last steps before the board is considered complete.
The Functional Testing Process
The exact process for functional testing can vary depending on the specifics of the PCB and the manufacturer, but it generally involves the following key steps:
1. Planning and Setup
The first step is to identify what needs to be tested on the PCB based on its design, specifications, and functional requirements. This includes defining test coverage, creating a test plan, and determining what test equipment and software will be needed.
Common things tested include:
- Power-on/power-off
- Reset
- Inputs (buttons, switches, sensors, etc.)
- Outputs (LEDs, displays, speakers, etc.)
- Communication interfaces (USB, Ethernet, wireless, etc.)
- Analog functions
- Digital functions
- Firmware/software
- Specific application functions
- Stress tests
- Boundary tests
A test fixture or jig is usually designed and built to securely hold the PCB and connect it to the test equipment. Test points are determined to access all the necessary signals. Automated tests are programmed and manual tests are documented.
2. Connection and Powering
With everything defined, the PCB is connected to the test equipment, usually via fixtures/jigs with pogo pins or edge connectors making contact with test points on the board. Depending on the test, it may receive power from an external power supply or from USB/batteries. The PCB is powered on and booted up.
3. Functional Test Execution
The meat of functional testing is the actual execution of all the planned tests on the powered PCB. This is often a combination of:
- Automated tests run by software
- Manual tests done by a test operator
- Visual inspection of the powered PCB
- Testing of any human input devices
- Testing of any output devices or interfaces
- Running of test scripts or test cases
- Stress testing and boundary condition testing
- Extended run (“soak”) tests
The test software will run through various functional test routines, comparing inputs to expected outputs. A test operator may manually interact with the PCB, pushing buttons, flipping switches, and confirming expected results. Hot mock-ups connected to the PCB can simulate real-world interfaces and conditions.
Everything is compared against the specifications and requirements to confirm correct operation. Issues are logged for debugging. Tests may be repeated multiple times to confirm consistent results.
4. Results and Reporting
As tests are executed, the results are logged to determine a pass/fail status for the board. This includes capturing any specific issues and the overall test coverage achieved.
Failed boards are typically debugged to determine the root cause of the failure (design issue, manufacturing defect, etc.). Bugs are identified to be fixed. Boards are then reworked or scrapped.
The test results are compiled into a report, often including performance metrics, yields, defect paretos, and a summary for management. Traceability data is recorded tying the test report to the specific board, components, design revision, software, test equipment, and operators involved.
Types of Functional Tests
There are many different types of functional tests that may be performed on an assembled PCB, depending on its purpose and design. Some common examples include:
Test Type | Description |
---|---|
Power-On | Tests powering the board on and off to verify correct startup and shutdown. |
Power Consumption | Measures the board’s current draw and power consumption under various conditions. |
Digital I/O | Toggles digital inputs and verifies the correct output response. |
Analog I/O | Applies analog voltages and waveforms and measures the output response. |
LED Test | Powers LEDs and light pipes and verifies their color and function. |
Display Test | Runs patterns and images on any displays and verifies pixels, backlight, etc. |
Audio Test | Plays tones and audio files and verifies speakers and audio jacks. |
Touch Test | Verifies any touchscreens or Touch Sensors respond correctly. |
Keyboard Test | Presses all buttons and keys and verifies the correct input is registered. |
Memory Test | Verifies reading/writing of RAM, Flash, EEPROM, SD cards, etc. |
Communication Ports | Transfers data over USB, Ethernet, RS-232, SPI, I2C, CAN, etc. and verifies protocol. |
Wireless Test | Verifies WiFi, Bluetooth, NFC, RFID, GPS and other radio communications. |
Stress Tests | Runs the board at max speed, max power, high temp, etc. to verify operation under stress. |
Burn-In Test | Runs the board for an extended period (hours+) to catch early failures and infant mortality. |
The specific mix of functional tests performed will be tailored to the particular PCB being manufactured. The goal is to exercise all the board’s functions and catch any possible issues.
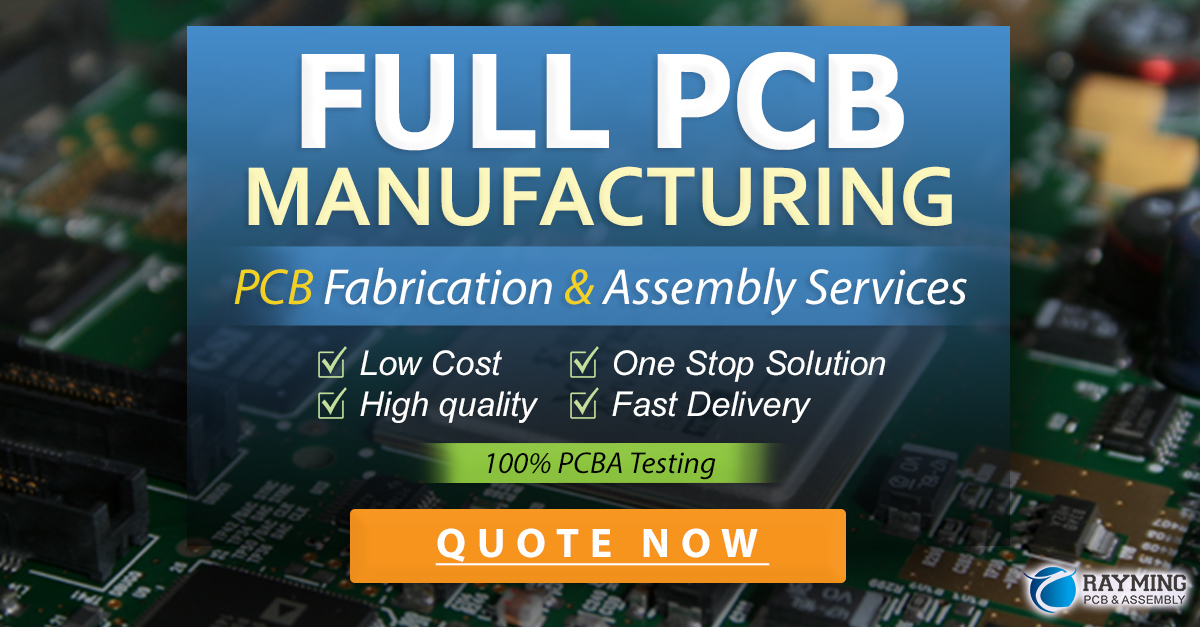
Benefits of Functional Testing
So why is functional testing such an important part of PCB Assembly? There are several key benefits:
Catch Defects Early
The biggest benefit of functional test is catching board problems and defects before the PCB ships to the customer. While it can’t catch every possible issue, it acts as a final gate to prevent field failures and expensive recalls. Finding and fixing bugs at this stage is much faster and cheaper than dealing with them later.
Verify Design
Functional testing provides real validation that the PCB design meets the actual requirements. It tests that the board really works as intended under various conditions. Running a new design through functional test is a key milestone before giving the green light for volume production.
Improve Quality
More comprehensive functional testing means more defects get caught and the overall outgoing quality and reliability improves. Dialing in the right set of functional tests will optimize quality metrics. The data can also be analyzed to identify problem areas, improve processes, guide re-designs, and drive continuous improvement.
Traceability
Functional test results provide a record of each board’s unique performance that can be tied back to its serial number. This traceability is very useful for failure analysis, warranty claims, and quality audits. It shows the board was tested and the specific results.
Customer Confidence
A PCB that has passed functional testing gives the customer confidence that they are receiving a board verified to operate correctly. Providing them the functional test report shows it went through a thorough validation process. This is especially important for critical applications like medical, aerospace, automotive, etc.
Challenges of Functional Testing
While very beneficial, functional testing does have some challenges compared to other PCB test methods:
Complexity
Testing the functionality of a complete PCB can be complex, especially for boards with many features. All the interfaces, firmware, and end-use cases may not be fully defined or available to the manufacturer. Specialized test equipment and significant engineering time may be required to develop a comprehensive test suite.
Coverage
Unlike other tests that can access every single net on a PCB, functional test is more limited to the available I/O, pins, and interfaces. There may be some internal buses, components, or signal paths that are hard to exercise thoroughly. Achieving full coverage of every function requires additional test points and creative test design.
Time and Cost
The time to fully run through a board’s functional tests can be quite long compared to faster methods like flying probe or ICT. When factoring in the engineering development time and test equipment, the cost per board can also be higher, though still cheaper than the cost of field failures. There are always tradeoffs between test speed, coverage, and cost that factor into the overall manufacturing strategy.
Automation
While some functional tests can be automated by software, many still require some human interaction with the PCB to push buttons, flip switches, make connections, and verify some outputs. The fixtures can also be more complicated to make contact with the board under power. A careful balance of automated vs manual testing has to be determined.
Defect Isolation
Because functional test is looking at the PCB as a complete functional item, failing results may not directly pinpoint the specific component or root cause of a problem, especially for complex boards. Further debugging and fault isolation has to be performed to find and repair the issue, usually with other tools like boundary scan, visual inspection, or x-ray.
Overcoming these challenges requires careful planning and execution of the functional test strategy as part of the overall PCB development and New Product Introduction (NPI) process.
FAQ
What is functional testing?
Functional testing is a quality assurance process where a completed and assembled printed circuit board (PCB) is powered on and tested to verify its end-to-end functionality per the design requirements. It’s typically one of the last steps in PCB assembly before the board is approved for shipment.
How is functional testing different from other PCB tests?
Other tests like flying probe or ICT focus on testing individual PCB Components, solder joints, and connections on an unpowered board. Functional testing looks at the PCB as a complete powered system and tests its overall operation, inputs/outputs, and real-world interfaces. It catches defects that other tests might miss.
What kind of things are checked during functional test?
The specifics vary by the board design, but functional tests commonly check things like power functions, resets, digital and analog I/O, LEDs, displays, speakers, keypads, touchscreens, memory, communications (USB, Ethernet, wireless, etc.), and application-specific functions under normal and stressed conditions.
Are functional tests manual or automated?
It’s usually a mix of both. Some functional tests can be fully automated by software, while others require a human operator to interact with the PCB to press buttons, flip switches, make connections, and verify results. A test plan will specify which steps are manual vs. automated.
How long does functional testing take?
The total time to execute a PCB’s functional tests can range from a few minutes to several hours or more, depending on the complexity of the board and how extensive the testing is. Some boards may undergo long burn-in tests to catch early failures. Compared to other testing methods, functional test tends to be slower but more comprehensive. The time and cost are weighed against the importance of the final quality.
Conclusion
In summary, functional testing plays a vital role in the PCB assembly process to verify the final board operates correctly per its requirements before being shipped to the customer. By powering on the completed PCB and exhaustively testing its inputs, outputs, interfaces, and functions, defects can be caught that would otherwise be missed by other test methods.
While functional testing can be complex and time-consuming, it provides a high level of confidence that the PCB’s design has been validated and the product meets all functional requirements. Dialing in the right functional test strategy is key to balancing quality, cost, and speed in electronics manufacturing.
As PCB designs continue to evolve in complexity, functional testing will also progress with more automated and sophisticated methods to keep pace. Investing the time and effort upfront to develop a solid functional test plan will pay dividends in smoother product launches, lower field failure rates, and satisfied customers. No PCB assembly is truly complete without it.
Leave a Reply