Introduction to Ceramic PCB
Ceramic printed circuit boards (PCBs) are a specialized type of PCB that utilizes ceramic materials as the substrate instead of the more common FR-4 or other organic materials. CeramIC PCBs offer unique properties that make them ideal for certain applications, particularly those that require high thermal conductivity, high-frequency operation, or resistance to extreme temperatures and harsh environments.
In this comprehensive article, we will delve into the world of ceramic PCBs, exploring their materials, types, manufacturing processes, advantages, disadvantages, and applications. By the end of this article, you will have a thorough understanding of ceramic PCBs and their role in the electronics industry.
What is a Ceramic PCB?
A ceramic PCB is a printed circuit board that uses a ceramic material as the substrate, which is the base material that supports the conductive traces and components. The most common ceramic materials used in PCB manufacturing are alumina (aluminum oxide) and aluminum nitride (AlN).
Ceramic PCBs are known for their excellent thermal conductivity, which allows them to dissipate heat more efficiently than traditional FR-4 PCBs. This property makes them suitable for high-power applications or situations where heat management is critical. Additionally, ceramic PCBs have a low coefficient of thermal expansion (CTE), which means they maintain their dimensional stability even when subjected to temperature fluctuations.
Advantages of Ceramic PCBs
- High thermal conductivity
- Low coefficient of thermal expansion (CTE)
- Excellent electrical insulation properties
- High-frequency operation capability
- Resistance to extreme temperatures and harsh environments
- Good mechanical strength and durability
Disadvantages of Ceramic PCBs
- Higher cost compared to FR-4 PCBs
- More brittle than organic PCBs
- Limited flexibility in design and layout
- Challenging to manufacture, requiring specialized equipment and processes
Materials Used in Ceramic PCBs
Alumina (Al2O3)
Alumina, or aluminum oxide, is the most widely used ceramic material in PCB manufacturing. It is known for its excellent electrical insulation properties, high thermal conductivity, and good mechanical strength. Alumina PCBs are available in various purities, with 96% and 99.6% being the most common. Higher purity alumina offers better performance but comes at a higher cost.
Aluminum Nitride (AlN)
Aluminum nitride is another popular ceramic material used in PCBs. It has a higher thermal conductivity than alumina, making it an ideal choice for applications that require even better heat dissipation. AlN PCBs also have a lower dielectric constant, which is beneficial for high-frequency applications. However, AlN is more expensive than alumina and is more challenging to process.
Comparison of Alumina and Aluminum Nitride
Property | Alumina (96%) | Aluminum Nitride |
---|---|---|
Thermal Conductivity | 24-28 W/mK | 170-180 W/mK |
Dielectric Constant | 9.0-9.8 | 8.6-8.9 |
Coefficient of Thermal Expansion | 6.5-7.5 ppm/°C | 4.5-4.7 ppm/°C |
Flexural Strength | 340-400 MPa | 300-350 MPa |
Cost | Moderate | High |
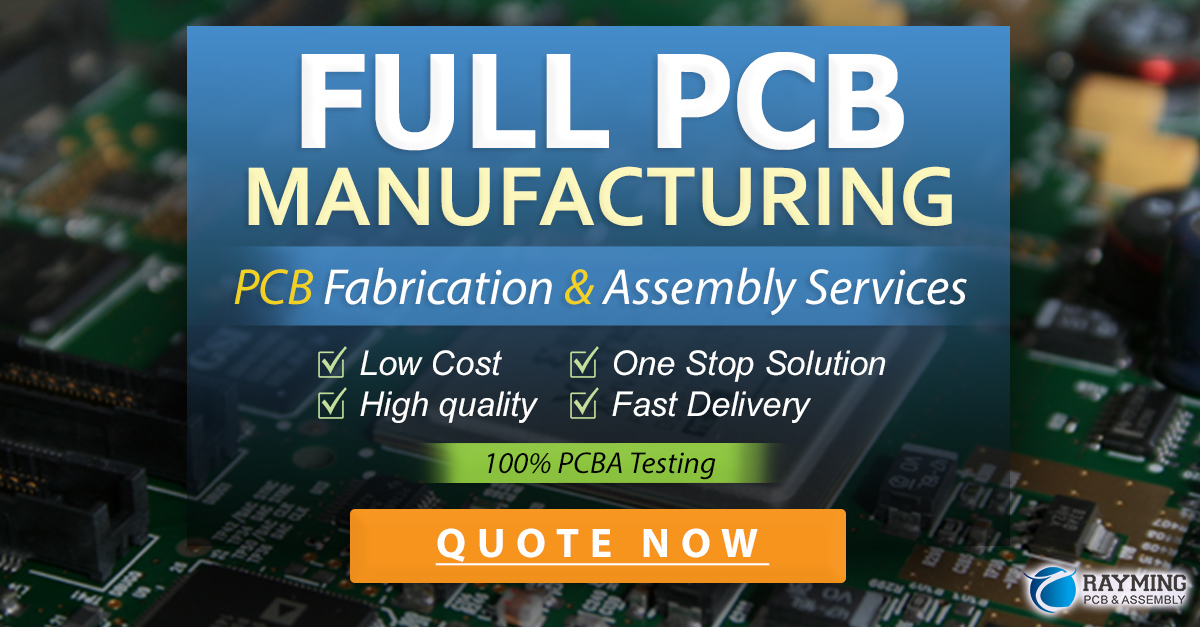
Types of Ceramic PCBs
Single-layer Ceramic PCBs
Single-layer ceramic PCBs consist of a single ceramic substrate with conductive traces on one side. They are the simplest and most cost-effective type of ceramic PCB. Single-layer ceramic PCBs are suitable for basic circuits and applications that do not require high complexity or density.
Multilayer Ceramic PCBs
Multilayer ceramic PCBs are composed of multiple layers of ceramic substrates with conductive traces and interconnections between layers. They offer higher circuit density and more complex designs compared to Single-Layer PCBs. Multilayer ceramic PCBs are commonly used in high-performance applications, such as aerospace, military, and telecommunications equipment.
Thick-film Ceramic PCBs
Thick-film ceramic PCBs are manufactured using a screen-printing process to deposit conductive traces and components onto the ceramic substrate. The conductive materials, typically silver or gold, are mixed with a glass frit and printed onto the substrate. Thick-film ceramic PCBs are known for their durability and resistance to harsh environments, making them suitable for automotive and industrial applications.
Thin-film Ceramic PCBs
Thin-film ceramic PCBs are fabricated using a sputtering or evaporation process to deposit thin layers of conductive materials, such as copper or gold, onto the ceramic substrate. This process allows for finer traces and higher circuit density compared to thick-film PCBs. Thin-film ceramic PCBs are often used in high-frequency and microwave applications.
Manufacturing Process of Ceramic PCBs
The manufacturing process of ceramic PCBs differs from that of traditional FR-4 PCBs due to the unique properties of ceramic materials. The main steps involved in the production of ceramic PCBs are:
-
Substrate preparation: The ceramic substrate is cleaned and inspected for any defects or impurities.
-
Via drilling: Holes are drilled into the substrate to create vias that connect different layers of the PCB.
-
Metallization: Conductive traces and pads are deposited onto the substrate using thick-film or thin-film processes, such as screen printing or sputtering.
-
Firing: The metallized substrate is fired in a high-temperature oven to sinter the conductive materials and bond them to the ceramic.
-
Layering and lamination: For multilayer ceramic PCBs, multiple metallized substrates are stacked and laminated together under high pressure and temperature.
-
Component assembly: Surface-mount or Through-hole components are attached to the ceramic PCB using soldering or conductive adhesives.
-
Testing and inspection: The assembled ceramic PCB undergoes various tests and inspections to ensure its functionality, reliability, and compliance with specifications.
Applications of Ceramic PCBs
Ceramic PCBs find applications in various industries and sectors where their unique properties are advantageous. Some of the common applications include:
-
High-power electronics: Ceramic PCBs are used in power amplifiers, Motor drive systems, and high-voltage devices, thanks to their excellent thermal conductivity and electrical insulation properties.
-
High-frequency and microwave devices: The low dielectric constant and low loss tangent of ceramic materials make them suitable for high-frequency applications, such as radar systems, antennas, and telecommunication equipment.
-
Aerospace and military: Ceramic PCBs are used in avionics, satellites, and defense systems due to their resistance to extreme temperatures, vibrations, and harsh environments.
-
Automotive: Ceramic PCBs are employed in engine control units, sensors, and power electronics in vehicles, where they must withstand high temperatures and vibrations.
-
Medical devices: Ceramic PCBs are used in implantable devices, medical imaging equipment, and diagnostic tools, where reliability and biocompatibility are critical.
-
Industrial equipment: Ceramic PCBs are found in various industrial applications, such as process control systems, power distribution, and automation, where they must operate reliably in challenging environments.
Frequently Asked Questions (FAQ)
1. What is the main difference between ceramic PCBs and FR-4 PCBs?
The main difference between ceramic PCBs and FR-4 PCBs is the substrate material. Ceramic PCBs use ceramic materials, such as alumina or aluminum nitride, while FR-4 PCBs use a glass-reinforced epoxy laminate. Ceramic PCBs offer better thermal conductivity, lower CTE, and higher-frequency operation compared to FR-4 PCBs.
2. Are ceramic PCBs more expensive than traditional PCBs?
Yes, ceramic PCBs are generally more expensive than traditional FR-4 PCBs due to the higher cost of ceramic materials and the specialized manufacturing processes required. However, the higher cost is often justified by the superior performance and reliability offered by ceramic PCBs in certain applications.
3. Can ceramic PCBs be used for flexible circuits?
No, ceramic PCBs are not suitable for flexible circuits due to the brittle nature of ceramic materials. Flexible circuits typically use polymeric substrates, such as polyimide or polyester, which can bend and flex without breaking.
4. How do ceramic PCBs handle high temperatures?
Ceramic PCBs are excellent at handling high temperatures due to their high thermal conductivity and low CTE. They can operate reliably in temperatures up to 250°C or higher, depending on the specific ceramic material and manufacturing process used.
5. What are the challenges in designing ceramic PCBs?
Designing ceramic PCBs can be challenging due to the limited flexibility in layout and routing compared to traditional PCBs. Ceramic materials are more brittle, which means that the design must account for mechanical stresses and avoid sharp corners or abrupt changes in geometry. Additionally, the higher cost of ceramic PCBs may require more careful consideration of the circuit design to minimize the board size and layer count.
Conclusion
Ceramic PCBs are a specialized type of printed circuit board that offer unique properties and benefits for certain applications. Their high thermal conductivity, low CTE, and excellent electrical insulation make them ideal for high-power, high-frequency, and harsh environment applications. While ceramic PCBs are more expensive and challenging to manufacture than traditional FR-4 PCBs, their superior performance and reliability justify their use in critical systems and demanding environments.
As technology continues to advance, the demand for ceramic PCBs is expected to grow, particularly in the aerospace, military, automotive, and telecommunications sectors. By understanding the materials, types, manufacturing processes, and applications of ceramic PCBs, engineers and designers can make informed decisions when selecting the most suitable PCB technology for their projects.
Leave a Reply