Introduction to the Bill of Materials (BOM)
In the world of manufacturing and product development, the Bill of Materials (BOM) is an essential document that provides a detailed list of all the components, parts, and materials required to produce a finished product. The BOM serves as a roadmap for the entire production process, ensuring that all necessary items are accounted for and that the final product meets the desired specifications.
What is a Bill of Materials?
A Bill of Materials, often referred to as a BOM list, is a comprehensive list of all the components, parts, raw materials, and assemblies needed to manufacture a product. It includes the quantity of each item required, as well as relevant information such as part numbers, descriptions, and supplier details. The BOM is a critical tool for managing the production process, as it ensures that all necessary components are available when needed and that the final product is built to the correct specifications.
The Importance of a BOM List
The BOM list plays a crucial role in several aspects of the manufacturing process:
-
Production Planning: The BOM helps production planners determine the required quantities of each component, allowing them to schedule production runs efficiently and avoid shortages or excess inventory.
-
Procurement: The BOM provides a clear list of all the items that need to be purchased, enabling the procurement team to source components from the appropriate suppliers and ensure timely delivery.
-
Cost Control: By itemizing all the components and their quantities, the BOM allows for accurate cost calculations and helps identify opportunities for cost reduction.
-
Quality Assurance: The BOM serves as a reference for quality control, ensuring that the finished product contains all the required components and meets the specified quality standards.
-
Communication: The BOM is a common language that facilitates communication between different departments, such as engineering, production, and procurement, ensuring that everyone is working towards the same goal.
Types of Bill of Materials
There are several types of BOMs, each serving a specific purpose in the product development and manufacturing process.
1. Engineering BOM (EBOM)
The Engineering BOM, also known as the Design BOM, is created by the product design team and includes all the components and assemblies required to build the product as designed. The EBOM focuses on the product’s functional requirements and design specifications, without considering the manufacturing process or supply chain constraints.
2. Manufacturing BOM (MBOM)
The Manufacturing BOM is derived from the EBOM and is tailored to the specific needs of the manufacturing process. The MBOM takes into account factors such as manufacturing sequence, assembly instructions, and packaging requirements. It may also include additional items needed for the production process, such as lubricants or protective materials.
3. Sales BOM (SBOM)
The Sales BOM, also known as the Customer BOM, is a simplified version of the BOM that is used for sales and marketing purposes. The SBOM includes only the high-level components or features that are relevant to the customer, without delving into the detailed technical specifications.
4. Service BOM
The Service BOM is used for after-sales support and maintenance purposes. It includes all the components and parts that may need to be replaced or repaired during the product’s lifetime, as well as any tools or equipment required for servicing the product.
BOM Hierarchy and Structure
A BOM list is typically organized in a hierarchical structure, with the finished product at the top and the individual components and subassemblies arranged in a tree-like structure below it.
Single-Level BOM
A single-level BOM lists all the components and parts required for a product, without showing the relationships between them. This type of BOM is suitable for simple products with few components.
Example of a Single-Level BOM:
Level | Part Number | Description | Quantity |
---|---|---|---|
0 | FP001 | Finished Product | 1 |
1 | C001 | Component A | 2 |
1 | C002 | Component B | 1 |
1 | C003 | Component C | 3 |
Multi-Level BOM
A multi-level BOM, also known as an indented BOM, shows the hierarchical relationships between the components and subassemblies. This type of BOM is more suitable for complex products with multiple levels of assemblies.
Example of a Multi-Level BOM:
Level | Part Number | Description | Quantity |
---|---|---|---|
0 | FP001 | Finished Product | 1 |
1 | A001 | Assembly A | 1 |
2 | C001 | Component A1 | 2 |
2 | C002 | Component A2 | 1 |
1 | A002 | Assembly B | 1 |
2 | C003 | Component B1 | 3 |
2 | C004 | Component B2 | 2 |
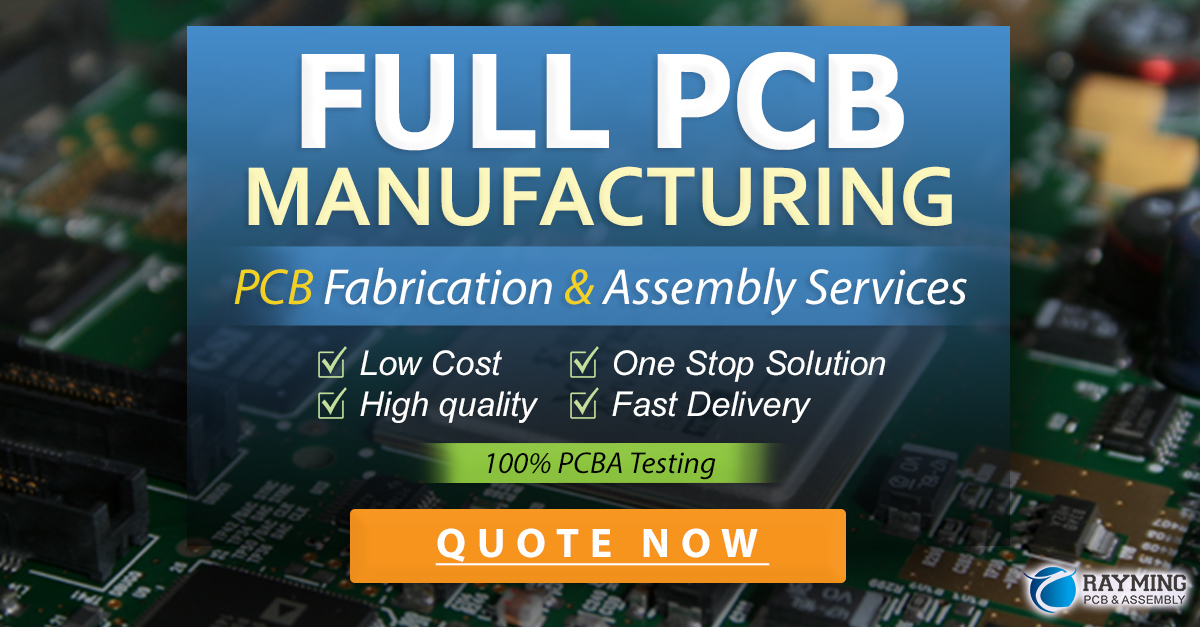
Creating a BOM List
Creating a comprehensive and accurate BOM list is crucial for the success of any manufacturing project. The following steps outline the process of creating a BOM:
1. Gather Product Information
Start by collecting all relevant information about the product, including design specifications, engineering drawings, and any existing documentation.
2. Identify Components and Assemblies
Break down the product into its individual components and assemblies, identifying each item’s unique part number and description.
3. Determine Quantities
For each component and assembly, determine the quantity required to produce one unit of the finished product.
4. Specify Suppliers and Procurement Details
Include information about the suppliers for each component, such as supplier name, contact information, and lead times. Also, specify any special procurement requirements, such as minimum order quantities or preferred shipping methods.
5. Organize the BOM Hierarchy
Arrange the components and assemblies in a hierarchical structure, showing the relationships between them and the overall product.
6. Review and Validate
Review the BOM list for accuracy and completeness, ensuring that all necessary components are included and that the quantities and specifications are correct. Validate the BOM with the relevant stakeholders, such as engineering, production, and procurement teams.
BOM Management Best Practices
Effective BOM management is essential for streamlining the manufacturing process and ensuring product quality. The following best practices can help optimize BOM management:
1. Use a Centralized BOM Database
Maintain a centralized database for storing and managing BOM information, ensuring that all teams have access to the most up-to-date and accurate data.
2. Implement Version Control
Use version control to track changes to the BOM over time, allowing for easy identification of the most current version and enabling traceability of product changes.
3. Establish Standard Naming Conventions
Develop and enforce standard naming conventions for parts, components, and assemblies to ensure consistency and clarity across the organization.
4. Regularly Review and Update BOMs
Conduct regular reviews of BOMs to ensure that they remain accurate and up-to-date, especially after design changes or supplier updates.
5. Integrate with Other Systems
Integrate the BOM database with other key systems, such as Enterprise Resource Planning (ERP), Product Lifecycle Management (PLM), and Manufacturing Execution Systems (MES), to ensure seamless data flow and facilitate real-time decision-making.
BOM Software and Tools
Managing BOMs can be a complex and time-consuming task, especially for products with numerous components and subassemblies. Fortunately, there are several software solutions and tools available to streamline BOM management:
1. Spreadsheet Software
For simple products with few components, spreadsheet software like Microsoft Excel or Google Sheets can be used to create and manage BOMs. However, spreadsheets can become cumbersome and error-prone for more complex products.
2. BOM-Specific Software
Dedicated BOM management software, such as OpenBOM, Arena BOM, and Omnify Software, offer specialized features for creating, managing, and sharing BOMs. These tools often include version control, collaboration features, and integration with other systems.
3. PLM Systems
Product Lifecycle Management (PLM) systems, such as PTC Windchill, Siemens Teamcenter, and Dassault Systèmes ENOVIA, provide comprehensive solutions for managing product data, including BOMs, throughout the entire product lifecycle.
4. ERP Systems
Enterprise Resource Planning (ERP) systems, like SAP and Oracle, often include BOM management capabilities as part of their manufacturing and supply chain management modules.
BOM List Example
To illustrate the concept of a BOM list, let’s consider a simplified example of a bicycle manufacturer creating a BOM for a new bike model.
Bicycle BOM List
Level | Part Number | Description | Quantity | Supplier |
---|---|---|---|---|
0 | BK001 | Bicycle | 1 | |
1 | FR001 | Frame | 1 | Supplier A |
1 | HS001 | Handlebar Set | 1 | Supplier B |
2 | HB001 | Handlebar | 1 | Supplier B |
2 | GR001 | Grips | 2 | Supplier C |
1 | WH001 | Wheel Set | 2 | Supplier D |
2 | RI001 | Rim | 2 | Supplier D |
2 | SP001 | Spokes | 72 | Supplier E |
2 | TI001 | Tire | 2 | Supplier F |
1 | DR001 | Drive Train Set | 1 | Supplier G |
2 | CH001 | Chain | 1 | Supplier G |
2 | CR001 | Crankset | 1 | Supplier G |
2 | CS001 | Cassette | 1 | Supplier G |
This multi-level BOM shows the hierarchical structure of the bicycle, with the main components (frame, handlebar set, wheel set, and drive train set) at level 1 and the subcomponents at level 2. The BOM also includes the quantity of each component required and the supplier information.
Frequently Asked Questions (FAQ)
1. What is the difference between a BOM and a parts list?
A parts list is a simple list of all the components and parts required for a product, without any hierarchical structure or information about the relationships between the items. A BOM, on the other hand, is a more comprehensive document that includes the hierarchical structure, quantities, and additional information such as supplier details and procurement requirements.
2. How often should a BOM be updated?
A BOM should be updated whenever there are changes to the product design, components, or suppliers. It is important to maintain an up-to-date BOM to ensure that the manufacturing process remains accurate and efficient. Regular BOM reviews should be conducted to verify the accuracy of the information and to identify any potential improvements.
3. What is the role of a BOM in supply chain management?
The BOM plays a crucial role in supply chain management by providing a clear list of all the components and materials required to produce a product. This information is used to plan and manage procurement activities, ensuring that the necessary items are available when needed and that the supply chain operates smoothly. The BOM also helps identify potential supply chain risks and opportunities for cost optimization.
4. Can a BOM be used for non-manufacturing purposes?
While BOMs are primarily used in manufacturing, the concept can be applied to other industries as well. For example, in the construction industry, a BOM might be used to list all the materials and components required to build a structure. In the software development industry, a BOM could be used to list all the software components and libraries required to build an application.
5. How does a BOM support collaboration between different teams?
A BOM serves as a common language and reference point for different teams involved in the product development and manufacturing process, such as engineering, procurement, production, and quality control. By providing a clear and comprehensive list of all the required components and materials, the BOM facilitates communication and collaboration between these teams, ensuring that everyone is working towards the same goal and that potential issues are identified and resolved quickly.
Conclusion
The Bill of Materials (BOM) is a fundamental tool in the manufacturing industry, providing a comprehensive list of all the components, parts, and materials required to produce a finished product. By creating and maintaining accurate and up-to-date BOMs, manufacturers can streamline their production processes, improve supply chain management, and ensure product quality.
Effective BOM management involves understanding the different types of BOMs, creating well-structured and hierarchical BOMs, and adopting best practices such as using centralized databases, implementing version control, and integrating with other key systems.
As product complexity continues to increase and supply chains become more global, the importance of robust BOM management will only continue to grow. By investing in the right tools, processes, and strategies for BOM management, manufacturers can position themselves for success in an increasingly competitive and dynamic market.
Leave a Reply