What is a Bill of Materials (BOM)?
A Bill of Materials (BOM) is a comprehensive list of all the components, parts, raw materials, subassemblies, and associated quantities needed to manufacture a product. It serves as a critical document in the manufacturing process, providing a clear and organized view of the product’s composition. The BOM is used by various departments, including engineering, procurement, and production, to ensure that all necessary components are available and that the manufacturing process runs smoothly.
Types of Bill of Materials
There are several types of BOMs, each serving a specific purpose in the manufacturing process:
-
Engineering BOM (EBOM): This type of BOM is created by the engineering team and contains all the components and subassemblies required to design and develop a product. The EBOM is typically more detailed than other types of BOMs and may include additional information such as CAD drawings and design specifications.
-
Manufacturing BOM (MBOM): The MBOM is derived from the EBOM and is tailored to the specific needs of the manufacturing process. It includes all the components and subassemblies required to physically produce the product, along with their quantities and any additional manufacturing instructions.
-
Sales BOM (SBOM): The SBOM is a simplified version of the BOM used by the sales team to communicate the product’s composition to customers. It typically includes only the high-level components and subassemblies that are relevant to the customer.
-
Service BOM (SBOM): The SBOM is used by the service and maintenance teams to identify the components and subassemblies required for repairs and maintenance. It may include additional information such as part numbers, supplier details, and recommended replacement intervals.
Importance of Bill of Materials
The Bill of Materials plays a crucial role in the manufacturing process for several reasons:
-
Ensures accurate inventory: By providing a detailed list of all the components and raw materials needed to produce a product, the BOM helps ensure that the correct inventory levels are maintained, minimizing the risk of stockouts or overstocking.
-
Facilitates cost control: The BOM allows manufacturers to accurately calculate the cost of producing a product by considering the cost of each component and subassembly. This information can be used to optimize the manufacturing process and identify cost-saving opportunities.
-
Improves communication: The BOM serves as a central document that can be shared among various departments, ensuring that everyone involved in the manufacturing process has access to the same information. This improves communication and reduces the risk of errors or misunderstandings.
-
Supports quality control: By clearly defining the components and subassemblies required to produce a product, the BOM helps ensure that the finished product meets the required quality standards. Any deviations from the BOM can be quickly identified and addressed.
-
Enables better planning: The BOM provides a clear picture of the materials and components required to produce a product, allowing manufacturers to plan their procurement and production processes more effectively. This can lead to shorter lead times, improved efficiency, and better customer satisfaction.
How to Create a Bill of Materials
Creating a comprehensive and accurate Bill of Materials involves several steps:
Step 1: Identify the Product Structure
The first step in creating a BOM is to identify the product structure, which involves breaking down the product into its individual components and subassemblies. This process is typically done by the engineering team and may involve the use of CAD software or other design tools.
Step 2: Assign Part Numbers
Once the product structure has been identified, each component and subassembly should be assigned a unique part number. This helps ensure that each item can be easily identified and tracked throughout the manufacturing process.
Step 3: Determine Quantities
For each component and subassembly, the required quantity must be determined. This information is typically based on the product design and may be influenced by factors such as expected demand, manufacturing efficiency, and minimum order quantities.
Step 4: Specify Materials and Suppliers
The materials and suppliers for each component and subassembly should be specified in the BOM. This information is critical for ensuring that the correct materials are procured and that the finished product meets the required quality standards.
Step 5: Include Additional Information
Depending on the type of BOM and its intended use, additional information may be included, such as:
- CAD drawings or design specifications
- Manufacturing instructions or process steps
- Lead times for each component or subassembly
- Cost information
- Supplier contact details
Step 6: Review and Approve
Once the BOM has been created, it should be reviewed and approved by the relevant stakeholders, such as the engineering, procurement, and production teams. This helps ensure that the BOM is accurate, complete, and meets the requirements of all departments involved in the manufacturing process.
Step 7: Maintain and Update
The BOM is a living document that should be regularly maintained and updated as changes occur in the product design, materials, or suppliers. Any changes to the BOM should be communicated to all relevant stakeholders to ensure that everyone is working with the most up-to-date information.
Benefits of Using a Bill of Materials Software
While it is possible to create and maintain a BOM using spreadsheets or other manual methods, using a dedicated BOM software can offer several benefits:
-
Centralized data management: BOM software provides a centralized repository for all BOM-related data, making it easier to access, update, and share information among team members.
-
Automated updates: When changes are made to the product design or materials, BOM software can automatically update the BOM, reducing the risk of errors and ensuring that everyone is working with the most up-to-date information.
-
Integration with other systems: Many BOM software solutions can integrate with other systems, such as ERP, MRP, or CAD software, allowing for seamless data exchange and reducing the need for manual data entry.
-
Improved collaboration: BOM software often includes collaboration features, such as version control, access control, and commenting, making it easier for team members to work together and communicate effectively.
-
Enhanced visibility: BOM software can provide greater visibility into the manufacturing process, allowing managers to track progress, identify potential issues, and make data-driven decisions.
Some examples of popular BOM software solutions include:
- Autodesk Fusion 360
- OpenBOM
- Arena BOM
- Omnify Empower
- Altium Designer
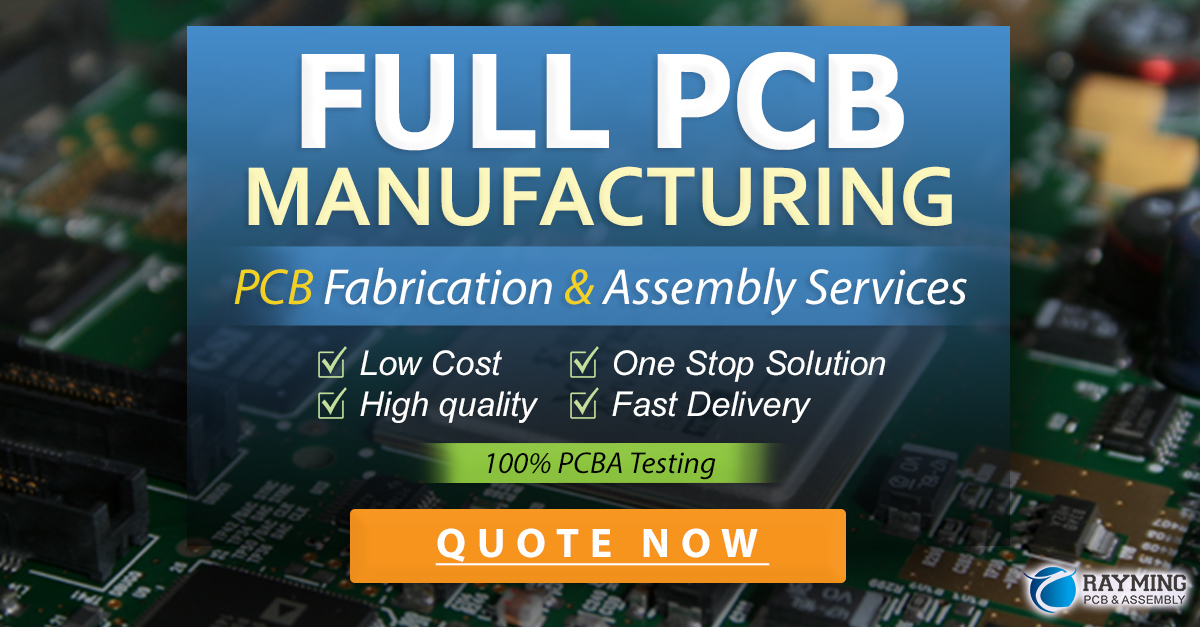
Best Practices for Managing Bill of Materials
To ensure that your Bill of Materials is effective and efficient, consider the following best practices:
-
Standardize part numbering: Develop a standardized part numbering system that is consistent, logical, and easy to understand. This will help reduce confusion and errors in the manufacturing process.
-
Use a single source of truth: Ensure that there is a single, authoritative version of the BOM that is accessible to all relevant stakeholders. This helps prevent the use of outdated or incorrect information.
-
Regularly review and update: Schedule regular reviews of the BOM to ensure that it remains accurate and up-to-date. Any changes should be communicated to all relevant stakeholders in a timely manner.
-
Collaborate with suppliers: Work closely with suppliers to ensure that they understand the BOM requirements and can provide the necessary components and materials in a timely and cost-effective manner.
-
Implement version control: Use version control to track changes to the BOM over time, allowing you to easily identify and revert to previous versions if necessary.
-
Train staff: Provide training to all staff involved in creating, maintaining, or using the BOM to ensure that they understand its importance and how to use it effectively.
-
Leverage automation: Consider using BOM software or other automation tools to streamline the creation and maintenance of the BOM, reducing the risk of errors and improving efficiency.
Frequently Asked Questions (FAQ)
1. What is the difference between a Bill of Materials and a parts list?
While a parts list and a Bill of Materials may seem similar, there are some key differences:
- A parts list typically includes only the individual components or parts required to assemble a product, while a BOM also includes subassemblies, raw materials, and associated quantities.
- A BOM often includes additional information, such as part numbers, supplier details, and cost information, which may not be present in a parts list.
- A BOM is used throughout the manufacturing process, while a parts list is primarily used during the assembly phase.
2. How often should a Bill of Materials be updated?
A Bill of Materials should be updated whenever there are changes to the product design, materials, or suppliers. The frequency of updates will depend on the complexity of the product and the nature of the manufacturing process. In general, it is recommended to review and update the BOM at least once per production cycle or whenever significant changes occur.
3. Can a Bill of Materials be used for multiple products?
While a Bill of Materials is typically created for a specific product, it is possible to use a single BOM for multiple products that share common components or subassemblies. In this case, the BOM would include all the components and subassemblies required for each product, with the quantities adjusted accordingly. This approach can help streamline the manufacturing process and reduce the need for multiple BOMs.
4. What is the role of the Bill of Materials in inventory management?
The Bill of Materials plays a critical role in inventory management by providing a clear picture of the components and raw materials required to produce a product. This information can be used to:
- Determine the optimal inventory levels for each component and raw material
- Identify potential stockouts or overstocking situations
- Plan procurement activities to ensure that the necessary materials are available when needed
- Calculate the cost of inventory and identify opportunities for cost savings
By using the information in the BOM to inform inventory management decisions, manufacturers can optimize their inventory levels, reduce costs, and improve overall efficiency.
5. How can a Bill of Materials help with product costing?
A Bill of Materials can help with product costing by providing a detailed breakdown of all the components and raw materials required to produce a product, along with their associated quantities and costs. This information can be used to:
- Calculate the total cost of producing a product
- Identify the most expensive components or subassemblies
- Compare the cost of different suppliers or materials
- Determine the impact of design changes on product cost
- Set pricing strategies based on a comprehensive understanding of production costs
By using the information in the BOM to inform product costing decisions, manufacturers can ensure that their products are priced appropriately, maintain profitability, and identify opportunities for cost savings.
Conclusion
A Bill of Materials is a critical document in the manufacturing process, providing a comprehensive list of all the components, parts, raw materials, and subassemblies required to produce a product. By creating and maintaining an accurate and up-to-date BOM, manufacturers can improve inventory management, facilitate cost control, enhance communication, support quality control, and enable better planning.
To create an effective BOM, manufacturers should follow a structured process that includes identifying the product structure, assigning part numbers, determining quantities, specifying materials and suppliers, and including any additional relevant information. The use of BOM software can help streamline this process and provide additional benefits, such as centralized data management, automated updates, and improved collaboration.
By following best practices for managing BOMs, such as standardizing part numbering, using a single source of truth, regularly reviewing and updating the BOM, collaborating with suppliers, implementing version control, training staff, and leveraging automation, manufacturers can ensure that their BOM remains an effective tool for driving efficiency, quality, and profitability in the manufacturing process.
Leave a Reply