Introduction to Blank PCBs
A Blank PCB, also known as a bare circuit board, is a printed circuit board without any components soldered onto it. It is the foundation upon which electronic devices are built, providing the necessary electrical connections and mechanical support for various components such as resistors, capacitors, integrated circuits, and connectors.
Blank PCBs are essential in the electronics industry, as they enable the creation of custom electronic devices tailored to specific applications. They are widely used in various sectors, including consumer electronics, automotive, aerospace, medical devices, and telecommunications.
Types of Blank PCBs
There are several types of Blank PCBs, each with its own unique characteristics and manufacturing process. The most common types include:
-
Single-sided PCBs: These PCBs have conductive traces on only one side of the board, making them the simplest and most cost-effective option for basic electronic circuits.
-
Double-sided PCBs: These PCBs have conductive traces on both sides of the board, allowing for more complex circuits and higher component density compared to single-sided PCBs.
-
Multi-layer PCBs: These PCBs consist of multiple layers of conductive traces separated by insulating layers, enabling even more complex circuits and higher component density. They are commonly used in advanced electronic devices that require compact designs and high performance.
-
Flexible PCBs: These PCBs are made from flexible materials, such as polyimide, allowing them to bend and conform to various shapes. They are often used in wearable electronics, medical devices, and applications that require flexibility.
-
Rigid-Flex PCBs: These PCBs combine the benefits of both rigid and flexible PCBs, featuring rigid sections for mounting components and flexible sections for connecting different parts of the device or for fitting into tight spaces.
Advantages of Using Blank PCBs
Using Blank PCBs offers several advantages in the design and manufacturing of electronic devices:
-
Customization: Blank PCBs allow for the creation of custom circuit designs tailored to specific applications, enabling designers to optimize the layout and functionality of their devices.
-
Cost-effectiveness: By using Blank PCBs, manufacturers can reduce the cost of production, as they can purchase the boards in bulk and populate them with components as needed, avoiding the need for expensive custom-made boards for each device.
-
Reliability: Blank PCBs are manufactured using high-quality materials and strict quality control processes, ensuring reliable performance and longevity of the final electronic device.
-
Flexibility in design: With various types of Blank PCBs available, designers have the flexibility to choose the most suitable board for their application, considering factors such as size, complexity, and environmental requirements.
-
Faster prototyping: Using Blank PCBs allows for faster prototyping and testing of electronic devices, as designers can quickly assemble and modify their circuits without waiting for custom-made boards.
Manufacturing Process of Blank PCBs
The manufacturing process of Blank PCBs involves several steps, each requiring precise control and adherence to industry standards. The main steps in the process are:
-
Design and layout: The first step is to create the PCB design using specialized software, such as Altium Designer or Eagle. The design includes the placement of components, routing of conductive traces, and the creation of solder pads and vias.
-
Substrate preparation: The substrate, typically made of fiberglass or other insulating material, is cut to the desired size and shape. Copper Foil is then laminated onto one or both sides of the substrate, depending on the type of PCB being manufactured.
-
Drilling: Holes are drilled into the PCB substrate to accommodate through-hole components and vias, which connect different layers of the board.
-
Patterning: The desired circuit pattern is transferred onto the copper foil using a photolithography process. This involves applying a light-sensitive resist to the copper, exposing it to UV light through a photomask, and then developing the resist to remove the unexposed areas.
-
Etching: The exposed copper is removed using a chemical etching process, leaving behind the desired conductive traces, pads, and vias.
-
Resist removal: The remaining photoresist is stripped away, revealing the final copper pattern on the PCB.
-
Surface finish: A surface finish, such as HASL (Hot Air Solder Leveling), ENIG (Electroless Nickel Immersion Gold), or OSP (Organic Solderability Preservative), is applied to the exposed copper to protect it from oxidation and improve solderability.
-
Solder Mask Application: A solder mask, typically green in color, is applied to the PCB surface, covering the areas where soldering is not required. This helps to prevent short circuits and improves the board’s aesthetic appearance.
-
Silkscreen printing: Text, logos, and component identifiers are printed onto the PCB surface using a silkscreen printing process, making it easier to assemble and troubleshoot the final device.
-
Quality control: The manufactured Blank PCBs undergo thorough quality control checks, including visual inspection, electrical testing, and dimensional verification, to ensure they meet the required specifications and standards.
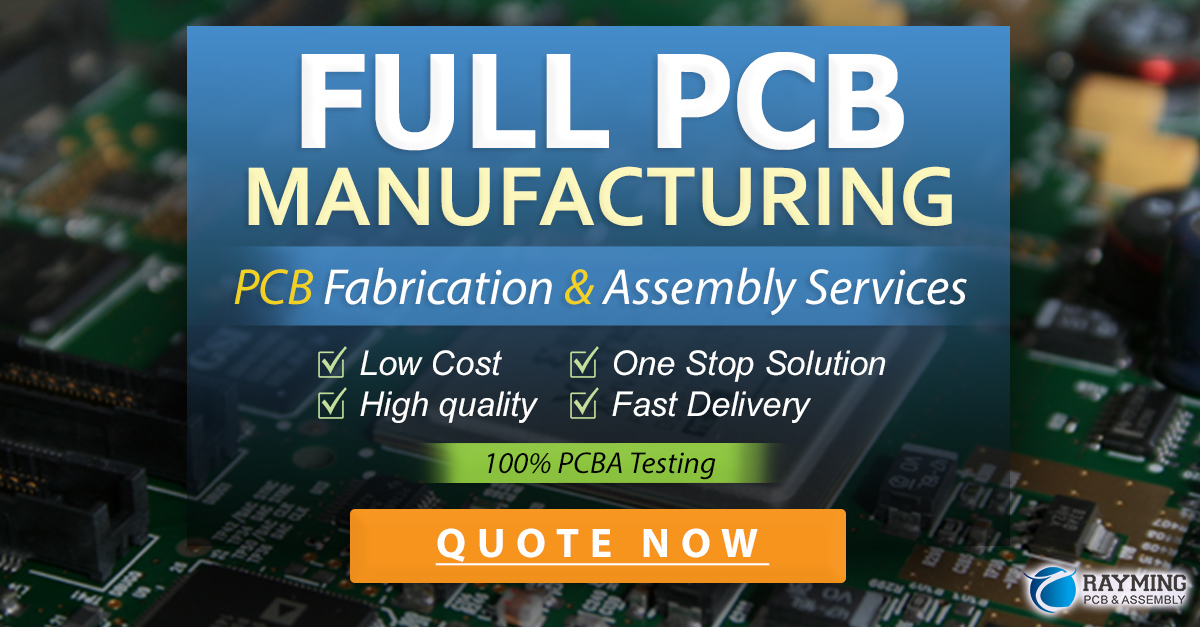
How to Make a Blank PCB at Home
While professional PCB manufacturing requires specialized equipment and facilities, it is possible to create simple Blank PCBs at home using readily available materials and tools. Here’s a step-by-step guide on how to make a single-sided Blank PCB at home:
Materials needed
- Copper-clad board (single-sided)
- Etch-resistant marker or transfer paper
- Ferric chloride solution (PCB etchant)
- Drill or dremel tool
- Sandpaper or steel wool
- Acetone or alcohol for cleaning
- Rubber gloves and safety goggles
Steps
-
Design your circuit: Create your PCB design using PCB design software or by hand-drawing it on paper. Keep in mind the limitations of the home manufacturing process, such as the minimum trace width and spacing.
-
Transfer the design: If using transfer paper, print your design onto the paper using a laser printer. Place the transfer paper face-down onto the copper-clad board and apply heat using an iron. If using an etch-resistant marker, carefully draw your design onto the copper-clad board.
-
Etch the PCB: Prepare the ferric chloride solution according to the manufacturer’s instructions. Wearing rubber gloves and safety goggles, submerge the PCB into the solution, ensuring that the copper side is facing up. Agitate the solution periodically to ensure even etching. Remove the PCB once all the unwanted copper has been etched away.
-
Clean the PCB: Rinse the etched PCB with water and remove any remaining etch-resistant marker or transfer paper using acetone or alcohol.
-
Drill holes: Using a drill or dremel tool, carefully drill holes for through-hole components and vias, as required by your design.
-
Clean and finish: Clean the PCB with sandpaper or steel wool to remove any burrs or rough edges. If desired, apply a thin layer of solder to the pads and traces to protect the copper and improve solderability.
Remember that home-made PCBs may not have the same quality and reliability as professionally manufactured ones, but they can be a good option for simple projects and prototyping.
Frequently Asked Questions (FAQ)
-
What is the difference between a Blank PCB and a populated PCB?
A Blank PCB is a printed circuit board without any components soldered onto it, while a populated PCB has components already soldered in place, ready for use in an electronic device. -
Can I reuse a Blank PCB?
Yes, you can reuse a Blank PCB if it has not been damaged or contaminated. To reuse a Blank PCB, you’ll need to remove any previously soldered components and clean the board thoroughly before soldering new components. -
What is the most common material used for Blank PCBs?
The most common material used for Blank PCBs is FR-4, which is a type of fiberglass-reinforced epoxy laminate. FR-4 is known for its excellent electrical insulation properties, mechanical strength, and thermal stability. -
How do I choose the right Blank PCB for my project?
When choosing a Blank PCB for your project, consider factors such as the complexity of your circuit, the required size and shape of the board, the number of layers needed, and the environmental conditions in which the final device will operate. Consult with PCB manufacturers or experienced designers to help you make the best choice. -
Can I manufacture multi-layer Blank PCBs at home?
Manufacturing multi-layer Blank PCBs at home is extremely challenging and requires specialized equipment and expertise. It is generally not recommended to attempt multi-layer PCB fabrication at home; instead, it is best to rely on professional PCB manufacturing services for such complex boards.
Conclusion
Blank PCBs are the foundation of modern electronic devices, providing the necessary electrical connections and mechanical support for various components. They offer numerous advantages, including customization, cost-effectiveness, reliability, design flexibility, and faster prototyping.
The manufacturing process of Blank PCBs involves several precise steps, from design and layout to substrate preparation, drilling, patterning, etching, and surface finishing. While professional manufacturing is the best option for high-quality and reliable PCBs, simple single-sided boards can be made at home using readily available materials and tools.
When choosing a Blank PCB for your project, consider the complexity of your circuit, the required size and shape, the number of layers needed, and the operating environment. By understanding the fundamentals of Blank PCBs and their manufacturing process, you can make informed decisions and create successful electronic devices.
Leave a Reply