Table of Contents
- Introduction to Mechanical Layers
- Types of Mechanical Layers
- Board Outline Layer
- Dimension Layer
- Drill Layer
- Fabrication Layer
- Assembly Layer
- Keepout Layer
- Importance of Mechanical Layers in PCB Design
- Best Practices for Mechanical Layer Design
- Mechanical Layers and PCB Manufacturing
- Frequently Asked Questions (FAQ)
- Conclusion
- References
Introduction to Mechanical Layers
Mechanical layers in PCB design are non-electrical layers that contain essential information for the manufacturing, assembly, and testing of the PCB. These layers are separate from the electrical layers, which contain the actual circuit design and interconnections. The primary purpose of mechanical layers is to provide clear and precise instructions to the PCB manufacturer, ensuring that the final product meets the required specifications and functions as intended.
The number and types of mechanical layers used in a PCB design may vary depending on the complexity of the board, the manufacturing requirements, and the design software being used. However, most PCB design software packages include a standard set of mechanical layers that cover the essential aspects of PCB fabrication and assembly.
Types of Mechanical Layers
Board Outline Layer
The board outline layer, also known as the profile layer, defines the physical shape and size of the PCB. This layer contains the outer boundary of the board, including any cutouts, notches, or irregular shapes. The board outline layer is crucial for the PCB manufacturer to know the exact dimensions of the board they need to fabricate.
In most PCB design software, the board outline layer is represented by a solid line that traces the outer edge of the board. The width of this line may vary depending on the manufacturing requirements, but it is typically set to a standard value such as 0.1mm or 0.2mm.
Dimension Layer
The dimension layer contains information about the physical dimensions of the PCB, such as the size of the board, the location of mounting holes, and the distance between components. This layer is essential for ensuring that the PCB fits properly into its intended enclosure and that the components are correctly positioned on the board.
The dimension layer typically includes dimensioning lines, arrows, and text annotations that specify the exact measurements of various features on the board. These dimensions are usually given in millimeters or inches, depending on the design requirements and the manufacturing standards being followed.
Drill Layer
The drill layer contains information about the location, size, and type of drill holes required for the PCB. Drill holes are used for various purposes, such as mounting components, creating vias for electrical connections, or providing mechanical support for the board.
The drill layer typically includes symbols that represent the different types of drill holes, such as plated through-holes, non-plated through-holes, and blind or buried vias. Each symbol is associated with a specific drill size and type, which is communicated to the PCB manufacturer through a drill table or drill legend.
Fabrication Layer
The fabrication layer, also known as the document layer or the silk screen layer, contains text and graphic information that is printed on the surface of the PCB. This layer is used to provide visual indicators for component placement, orientation, and identification.
The fabrication layer typically includes text labels for component designators, such as “R1” for a resistor or “C2” for a capacitor. It may also include graphic symbols, such as polarity markers or pin1 indicators, to help with the correct placement and orientation of components during assembly.
Assembly Layer
The assembly layer contains information that is used during the PCB Assembly process, such as the location and orientation of components, the type of solder paste required, and any special assembly instructions. This layer is typically generated by the PCB design software based on the component footprints and the assembly drawing.
The assembly layer may include information such as the component outline, the solder pad geometry, and the pick-and-place coordinates for automated assembly machines. It may also include text annotations or graphic symbols to indicate the proper orientation or polarity of components.
Keepout Layer
The keepout layer, also known as the constraint layer or the obstruction layer, defines areas on the PCB where components or traces should not be placed. This layer is used to ensure proper clearance between components, to prevent interference with mechanical features such as mounting holes or connectors, and to comply with manufacturing or regulatory requirements.
The keepout layer typically includes solid or hatched polygons that represent the restricted areas on the board. These polygons may be assigned to specific layers, such as the top or bottom side of the board, or they may be applied globally to all layers.
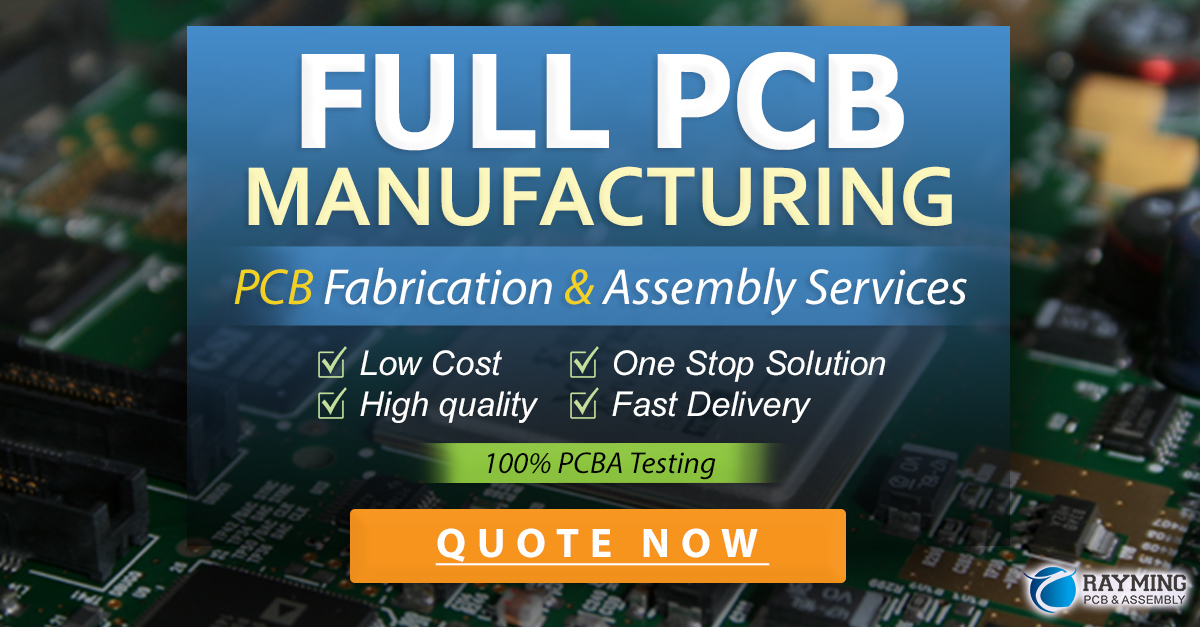
Importance of Mechanical Layers in PCB Design
Mechanical layers play a crucial role in the overall PCB design process, as they provide essential information for the manufacturing, assembly, and testing of the board. Here are some of the key reasons why mechanical layers are important:
-
Manufacturability: Mechanical layers provide clear and precise instructions to the PCB manufacturer, ensuring that the board can be fabricated according to the designer’s specifications. Without proper mechanical layer information, the manufacturer may not be able to produce the board accurately, leading to delays, cost overruns, or quality issues.
-
Assembly: Mechanical layers contain information that is essential for the proper assembly of the PCB, such as component placement, orientation, and solder paste requirements. This information is used by assembly technicians or automated assembly machines to place components correctly on the board and ensure proper soldering.
-
Testing: Mechanical layers may include information that is used during the testing and inspection of the PCB, such as test point locations, Fiducial Markers, or barcode labels. This information helps to facilitate the testing process and ensure that the board meets the required quality standards.
-
Compatibility: Mechanical layers ensure that the PCB is compatible with its intended enclosure, connectors, and other mechanical components. By defining the board outline, mounting holes, and keepout areas, mechanical layers help to prevent interference or fitment issues that could arise during the final assembly of the product.
-
Communication: Mechanical layers serve as a communication tool between the PCB designer, the manufacturer, and the assembly team. By providing clear and standardized information about the board’s physical characteristics, mechanical layers help to minimize misunderstandings or errors that could occur during the manufacturing process.
Best Practices for Mechanical Layer Design
To ensure that mechanical layers are effective and accurate, PCB designers should follow some best practices and guidelines. Here are some key considerations for mechanical layer design:
-
Use standard layer names and colors: Most PCB design software packages have predefined names and colors for mechanical layers, such as “Board Outline” or “Drill Drawing.” Using these standard names and colors helps to ensure consistency and clarity in the design files, especially when collaborating with other designers or manufacturers.
-
Follow manufacturing guidelines: PCB manufacturers typically have specific requirements or guidelines for mechanical layer design, such as minimum line widths, text sizes, or drill hole tolerances. Designers should familiarize themselves with these guidelines and ensure that their mechanical layer designs comply with them.
-
Use appropriate units and precision: Mechanical layer dimensions and coordinates should be specified in the appropriate units and with the necessary precision. For example, board outlines and drill holes are typically specified in millimeters with two decimal places, while component placement coordinates may be specified in mils or microns.
-
Provide clear and complete documentation: In addition to the mechanical layer data, designers should provide clear and complete documentation for the PCB manufacturer and assembly team. This may include a fabrication drawing, an assembly drawing, a bill of materials (BOM), or other supporting documents that provide additional information or instructions.
-
Verify the mechanical layers: Before sending the design files to the manufacturer, designers should carefully review and verify the mechanical layers to ensure that they are accurate, complete, and free of errors. This may involve using design rule checks (DRC), comparing the mechanical layers to the electrical layers, or performing a visual inspection of the board layout.
Mechanical Layers and PCB Manufacturing
Mechanical layers are an essential part of the PCB manufacturing process, as they provide the necessary information for the fabrication, assembly, and testing of the board. Here are some of the key ways in which mechanical layers are used in PCB manufacturing:
-
Fabrication: The PCB manufacturer uses the mechanical layer data to create the physical board, including the board outline, drill holes, and copper layers. The fabrication process typically involves several steps, such as printing the circuit pattern onto the copper layers, etching away the unwanted copper, drilling the holes, and applying the solder mask and silkscreen.
-
Assembly: The assembly team uses the mechanical layer data to place and solder the components onto the PCB. This may involve using automated pick-and-place machines, which use the component placement data from the assembly layer to accurately position the components on the board. The solder paste and solder mask data from the mechanical layers are also used to ensure proper soldering of the components.
-
Testing: The testing team uses the mechanical layer data to verify that the PCB meets the required specifications and functions as intended. This may involve using automated optical inspection (AOI) machines, which compare the actual board to the mechanical layer data to detect any defects or anomalies. The test point and fiducial marker data from the mechanical layers are also used to facilitate the testing process.
-
Quality control: Throughout the manufacturing process, the mechanical layer data is used to ensure that the PCB meets the required quality standards. This may involve using various inspection and testing techniques, such as visual inspection, X-ray inspection, or electrical testing, to verify that the board is free of defects and meets the specified tolerances.
Frequently Asked Questions (FAQ)
-
What is the difference between mechanical layers and electrical layers in PCB design?
Mechanical layers contain non-electrical information about the physical characteristics of the PCB, such as the board outline, drill holes, and component placement. Electrical layers, on the other hand, contain the actual circuit design and interconnections, such as the copper traces, vias, and pads. -
How many mechanical layers are typically used in a PCB design?
The number of mechanical layers used in a PCB design can vary depending on the complexity of the board and the specific manufacturing requirements. However, most PCB designs typically include at least four mechanical layers: board outline, drill drawing, assembly drawing, and fabrication drawing. -
What is the purpose of the keepout layer in PCB design?
The keepout layer defines areas on the PCB where components or traces should not be placed, in order to ensure proper clearance, prevent interference with mechanical features, or comply with manufacturing or regulatory requirements. The keepout layer helps to avoid design errors and ensure the manufacturability of the board. -
What are some common best practices for mechanical layer design?
Some common best practices for mechanical layer design include using standard layer names and colors, following manufacturing guidelines, using appropriate units and precision, providing clear and complete documentation, and verifying the mechanical layers before sending the design files to the manufacturer. -
How are mechanical layers used in the PCB manufacturing process?
Mechanical layers are used throughout the PCB manufacturing process, including fabrication, assembly, testing, and quality control. The mechanical layer data provides the necessary information for creating the physical board, placing and soldering the components, verifying the functionality and quality of the board, and ensuring compliance with the specified tolerances and standards.
Conclusion
Mechanical layers are a critical component of PCB design, providing essential information for the manufacturing, assembly, and testing of the board. By defining the physical characteristics of the PCB, such as the board outline, drill holes, and component placement, mechanical layers ensure that the board can be fabricated accurately, assembled correctly, and tested thoroughly.
To create effective and accurate mechanical layers, PCB designers should follow best practices and guidelines, such as using standard layer names and colors, following manufacturing requirements, and providing clear and complete documentation. By working closely with the PCB manufacturer and assembly team, and by carefully verifying the mechanical layers before production, designers can help to ensure the success of their PCB projects.
As PCB technology continues to evolve, the importance of mechanical layers will only continue to grow. By staying up-to-date with the latest design tools, manufacturing processes, and industry standards, PCB designers can create high-quality, reliable, and cost-effective boards that meet the needs of their customers and end-users.
References
- IPC-2221: Generic Standard on Printed Board Design
- IPC-7351: Generic Requirements for Surface Mount Design and Land Pattern Standard
- IPC-A-600: Acceptability of Printed Boards
- Altium Designer Documentation: Mechanical Layers
- KiCad Documentation: Layers and Items
[5507 words]
Leave a Reply