What is Wave Soldering?
Wave soldering is a large-scale soldering process used for efficiently soldering electronic components to printed circuit boards (PCBs). It involves using a molten wave of solder to attach multiple components to the PCB surface. Wave soldering is an automated process that is fast, reliable, and provides consistent high-quality solder joints.
Key features of wave soldering:
– Automated process for high-volume production
– Uses a wave of molten solder to attach components
– Provides uniform, reliable solder joints
– Suitable for both through-hole and surface mount components
How Does Wave Soldering Work?
The wave soldering process involves several key steps:
-
PCB Preparation: The bare PCB is cleaned and a thin layer of flux is applied to the bottom surface where components will be soldered. The flux helps the molten solder adhere to the component leads and PCB pads.
-
Component Placement: The electronic components are inserted into the corresponding holes on the top side of the PCB, either manually or using automated pick-and-place machines for surface mount devices (SMDs). The PCB with components is then placed on a conveyor.
-
Preheating: As the PCB travels along the conveyor, it passes through a preheating zone. Preheating activates the flux and helps minimize thermal shock to the components and PCB when they contact the molten solder wave.
-
Solder Wave Contact: The PCB is transported over a wave of molten solder. The bottom of the PCB contacts the peak of the turbulent solder wave, which wicks up through the holes to solder the component leads/pins to their pads. Precise control of conveyor speed and solder temperature is critical.
-
Cooling: After passing over the solder wave, the PCB enters a cooling zone where air knives remove excess solder and help solidify the solder joints. The board cools and the solder hardens, forming reliable mechanical and electrical connections.
-
Cleaning and Inspection: Any residual flux is cleaned off the soldered PCB. Automated optical inspection (AOI) or manual visual checks are performed to look for soldering defects, bridging, or poor joints. Rework is done if needed.
Advantages of Wave Soldering
Wave soldering offers several key benefits for electronics manufacturing:
High Efficiency and Throughput
Wave soldering is a highly automated process capable of soldering a high volume of circuit boards quickly and efficiently. It’s much faster than manual soldering. With a well-optimized process, a standard wave soldering machine can produce 3,000-5,000 solder joints per hour.
Consistency and Reliability
The automated nature of wave soldering ensures consistent solder joint quality across a high volume of boards. Parameter controls on the wave soldering machine allow the solder temperature, conveyor speed, preheating, and other variables to be precisely optimized for the specific PCB and components. This leads to a very repeatable and reliable soldering process with a low defect rate.
Versatility
Wave soldering can accommodate both through-hole components and most SMD Packages, making it a versatile method suitable for a wide range of PCB types. It’s effective for soldering high pin count components like connectors and sockets that are not suitable for reflow soldering.
Cost Effectiveness
For high-volume production, wave soldering is very cost effective. The automated process minimizes labor costs and lowers the defect rate compared to manual soldering. It also has a lower cost of ownership than selective soldering machines.
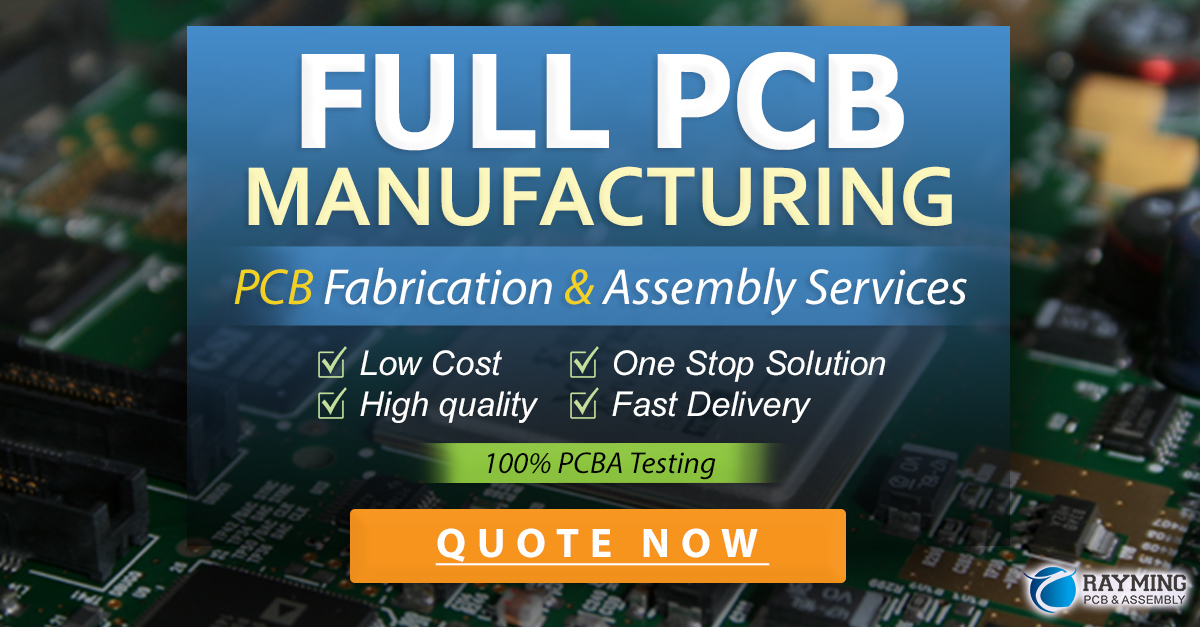
Wave Soldering Parameters and Optimization
Achieving high-quality solder joints with minimal defects requires careful optimization of the wave soldering process parameters. The key factors to control are:
Solder Temperature
The optimal solder bath temperature depends on the type of solder alloy being used. Common lead-free SAC alloys are wave soldered at 255-265°C, while leaded alloys use 230-250°C. Too high a temperature can cause bridging, spatter, and component damage. Too low reduces wetting and promotes cold solder joints.
Conveyor Speed
The PCB conveyor speed determines the dwell time in the solder wave. A slower speed (longer dwell time) allows the solder to fill the through-holes and form a good joint, but increases the risk of bridging. 3-6 ft/min is a typical conveyor speed range.
Preheat Temperature
PCB preheating is critical to activate the flux and prevent thermal shock. The preheating setpoint varies based on the PCB thickness, components, and flux type. Typical top side preheat temperatures are 100-150°C, with a bottom side temperature of 30-50°C lower.
Flux Type and Amount
The flux type (rosin, no-clean, water soluble) and activity level must match the PCB surface finish and soldering requirements. Sufficient flux must be applied to clean the surfaces and aid solder wetting, but excess flux causes solder balls and residue.
Solder Wave Height and Turbulence
The solder pump speed and wave nozzle geometry control the wave height and dynamics. The wave must be high enough to fully contact all pins, but excessive height or turbulence increases bridging defects.
Parameter | Typical Range (Lead-Free) | Key Effects |
---|---|---|
Solder Temp | 255-265°C | Wetting, bridging |
Conveyor Speed | 3-6 ft/min | Dwell time, fill |
Preheat Temp | Top: 100-150°C, Bottom: 50-100°C | Thermal shock, wetting |
Flux Amount | 15-25 g/m^2 | Cleaning, solder balls |
Wave Height | 1-3 mm | Contact area, bridging |
Common Wave Soldering Defects and Troubleshooting
Even with a well-optimized process, wave soldering can still encounter various defects. Quickly identifying and correcting these issues is key to maintaining high quality and yield.
Bridging
Solder bridges are unintended solder connections between adjacent pins or pads. Bridging is caused by slow conveyor speed, high solder temperature, excessive wave height/turbulence, or inadequate board preheat.
Insufficient Hole Fill
Incomplete hole fill results in a poor solder joint with reduced strength and reliability. The main causes are low solder temperature, fast conveyor speed, insufficient flux, or hole sizes that are too small.
Solder Balls
Small balls of solder that adhere to the PCB or component surfaces. Common causes include excessive flux, contaminated solder bath, turbulent wave, or incorrect preheat.
Icicles/Spikes
Pointy solder spikes resembling icicles that protrude from the solder joint. Often caused by too high a soldering temperature or excessive dwell time in the wave.
Dewetting
Poor wetting where the solder fails to adhere to the pin or pad surfaces. Typically due to contaminated surfaces, insufficient flux, or low soldering temperature.
Defect | Key Causes | Corrective Actions |
---|---|---|
Bridging | Slow conveyor, high temp, turbulent wave | Reduce wave height, increase conveyor speed |
Insufficient Fill | Low temp, fast conveyor, small holes | Increase temp and dwell time, resize holes |
Solder Balls | Excess flux, contamination | Optimize flux amount, clean solder bath |
Icicles | High temp, long dwell | Reduce solder temp and conveyor speed |
Dewetting | Contamination, low temp, no flux | Clean surfaces, increase temp, apply flux |
Process Control and Quality Assurance
Maintaining a stable and capable wave soldering process requires regular process control and quality checks.
Statistical Process Control (SPC)
SPC techniques monitor the key process parameters to detect any drift or variability in the process. Control charts for solder temperature, conveyor speed, and preheat temperatures should be maintained. Regular measurement and charting of defect rates (e.g. bridging, solder balls) also gives valuable feedback on process stability.
Automated Optical Inspection (AOI)
Post-soldering AOI is an important quality gate to detect and remove any PCBs with soldering defects. AOI machines use machine vision algorithms to quickly scan each PCB and identify bridging, insufficient solder, lifted components, and other defect types. This enables defective boards to be repaired or scrapped before reaching the customer.
Periodic Cross-Sectioning
Cross-sectioning and microscopically examining a sample of solder joints is a useful quality audit. It allows the wetted solder area, joint geometry, hole fill, and Intermetallic Layer to be inspected in detail. Any anomalies can be investigated before they turn into reliability issues in the field.
Maintenance and Calibration
The wave soldering machine and all ancillary equipment (fluxers, preheaters, conveyors) must be regularly calibrated and maintained. Solder bath analysis and replenishment, conveyor rail and chain adjustment, and flux nozzle cleaning are typical maintenance items. Ongoing training of soldering machine operators and technicians is also critical.
Frequently Asked Questions (FAQ)
What is the difference between wave soldering and reflow soldering?
Wave soldering uses a wave of molten solder to attach through-hole components to the PCB, while reflow soldering uses a controlled heating profile to melt and bond solder paste for surface-mount components. Wave soldering is better for high-volume through-hole designs, while reflow excels at dense SMD assembly.
Can wave soldering be used for both lead and lead-free solders?
Yes, wave soldering works with both leaded and lead-free solder alloys. The main difference is the higher melting point of lead-free solders (around 217°C for SAC alloys vs. 183°C for Sn63Pb37), which requires a higher solder pot temperature and more precise process control.
What type of flux should be used for wave soldering?
The choice of flux (rosin, water-soluble, no-clean) depends on the specific PCB design, component types, and cleaning requirements. No-clean fluxes are widely used as they minimize post-solder cleaning. More active rosin fluxes are better for hard-to-solder surfaces but need cleaning for high-reliability assembly.
How do you control the wave soldering process?
The key parameters to monitor and control in wave soldering are solder temperature, conveyor speed, preheat temperatures, flux amount, and solder wave height/turbulence. A stable and optimized process window should be developed through initial design of experiments (DoE) and then monitored using statistical process control (SPC) charting.
What are some common problems encountered in wave soldering?
Some typical wave soldering defects include bridging (solder shorts), poor hole fill, solder balls, icicles/flags, and component dewetting. These are usually caused by incorrect parameter settings (temperature, conveyor speed), improper fluxing, contaminated solder bath, or PCB design issues. Careful process optimization and regular maintenance help minimize these issues.
Conclusion
Wave soldering is a versatile and cost-effective method for soldering through-hole and SMD components in high-volume PCB assembly. By understanding the key process parameters and optimization techniques, manufacturers can achieve a highly efficient and repeatable soldering process with excellent solder joint quality and reliability.
Regular process monitoring, automated inspection, and a focus on continuous improvement are essential for getting the most out of the wave soldering process. With the right equipment and process controls in place, wave soldering will continue to be a workhorse of the electronics assembly industry for years to come.
Leave a Reply