Introduction to LED Grow Light PCBs
Light-emitting diode (LED) grow lights have revolutionized the indoor farming and horticulture industry. These energy-efficient and long-lasting light sources provide the optimal spectrum for plant growth, making them a popular choice for both commercial and hobbyist growers. At the heart of every LED grow light is a printed circuit board (PCB) that ensures proper functioning and reliability. In this comprehensive guide, we’ll dive deep into the world of LED grow light PCB manufacturing, covering everything from design considerations to assembly and testing.
Understanding the Basics of LED Grow Light PCBs
What is a PCB?
A printed circuit board (PCB) is a flat, insulating substrate that mechanically supports and electrically connects electronic components using conductive tracks, pads, and other features etched from one or more layers of copper laminated onto or between layers of a non-conductive substrate. PCBs are used in nearly all electronic products, including LED grow lights.
The Role of PCBs in LED Grow Lights
In LED grow lights, PCBs serve several essential functions:
- Mechanical support: PCBs provide a stable platform for mounting LEDs and other electronic components.
- Electrical connectivity: Conductive tracks on the PCB allow for the flow of electricity between components, enabling the LEDs to illuminate.
- Heat dissipation: PCBs help to dissipate heat generated by the LEDs, preventing overheating and ensuring optimal performance.
Types of PCBs Used in LED Grow Lights
There are several types of PCBs used in LED grow lights, each with its own advantages and disadvantages:
PCB Type | Description | Advantages | Disadvantages |
---|---|---|---|
Single-layer | A PCB with conductive tracks on one side only | Low cost, simple design | Limited routing options, lower heat dissipation |
Double-layer | A PCB with conductive tracks on both sides | Improved routing options, better heat dissipation | Higher cost, more complex design |
Multi-layer | A PCB with three or more layers of conductive tracks | Excellent routing options, superior heat dissipation | Highest cost, most complex design |
Designing LED Grow Light PCBs
Factors to Consider When Designing LED Grow Light PCBs
When designing an LED grow light PCB, several key factors must be considered:
- LED selection: Choose LEDs with the appropriate wavelengths and intensities for the target plant species.
- PCB material: Select a PCB material with good thermal conductivity and dielectric properties, such as aluminum or Copper-Clad Laminate.
- Thermal management: Incorporate heat sinks, thermal vias, and other features to ensure proper heat dissipation.
- Power requirements: Design the PCB to handle the required voltage and current for the chosen LEDs.
- Connectivity: Include connectors and interfaces for power supply, control systems, and other peripherals.
PCB Layout and Routing Considerations
Proper PCB layout and routing are crucial for optimal LED grow light performance:
- Component placement: Arrange components to minimize signal interference and maximize heat dissipation.
- Track width and spacing: Ensure that tracks are wide enough to handle the required current and spaced appropriately to prevent crosstalk and signal integrity issues.
- Ground planes: Incorporate ground planes to reduce electromagnetic interference (EMI) and improve signal integrity.
- Thermal management: Use thermal relief pads and vias to conduct heat away from components and into the PCB substrate.
Simulation and Testing
Before manufacturing the PCB, it’s essential to simulate and test the design to ensure proper functionality and reliability:
- Schematic simulation: Use electronic design automation (EDA) software to simulate the circuit and verify its behavior.
- Thermal simulation: Analyze the thermal performance of the PCB using computational fluid dynamics (CFD) software.
- Signal integrity analysis: Evaluate the signal integrity of the PCB design using electromagnetic simulation tools.
- Prototype testing: Manufacture a small batch of prototype PCBs and test them under real-world conditions to validate the design.
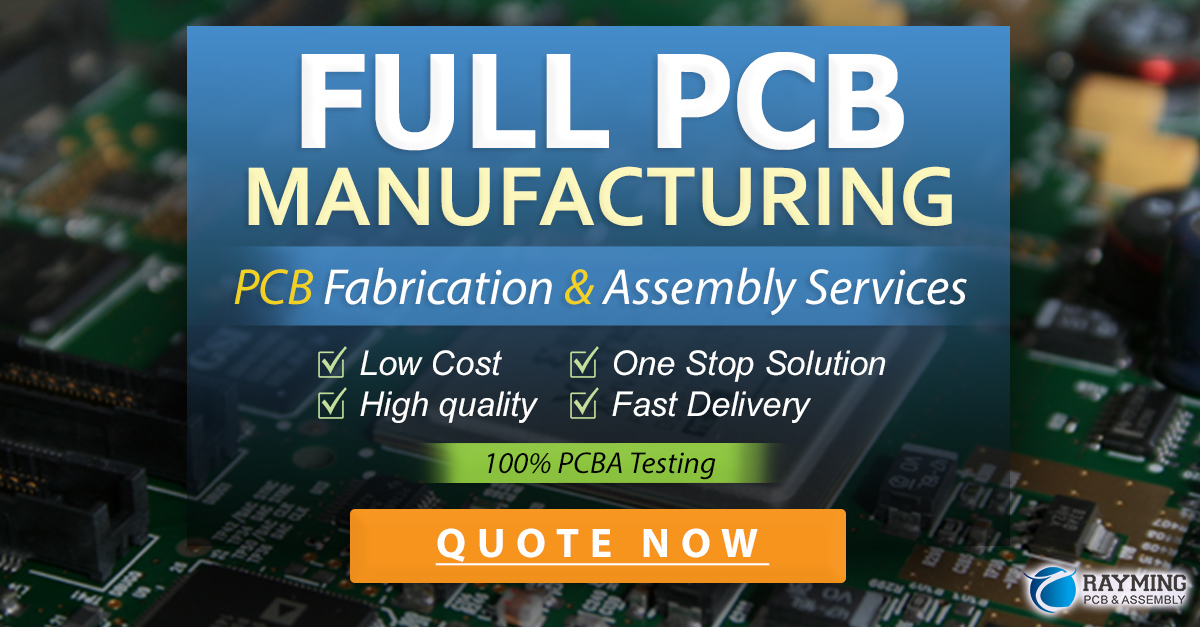
Manufacturing LED Grow Light PCBs
Choosing a PCB Manufacturer
Selecting the right PCB manufacturer is crucial for ensuring the quality and reliability of your LED grow light PCBs. Consider the following factors when choosing a manufacturer:
- Experience: Look for a manufacturer with experience in producing LED grow light PCBs or similar high-power, thermally-demanding applications.
- Capabilities: Ensure that the manufacturer has the equipment and expertise to handle your specific PCB design, including multi-layer boards and advanced features.
- Quality control: Choose a manufacturer with strict quality control processes, such as ISO 9001 certification, to ensure consistent and reliable results.
- Lead time and cost: Consider the manufacturer’s lead time and pricing to ensure that they align with your project timeline and budget.
PCB Fabrication Process
The PCB fabrication process involves several key steps:
- PCB design: The PCB design is created using EDA software and exported as Gerber files.
- PCB manufacturing: The Gerber files are used to manufacture the PCB, which typically involves the following sub-steps:
a. Substrate preparation: The PCB substrate is cleaned and prepared for lamination.
b. Lamination: Copper foil is laminated onto the substrate using heat and pressure.
c. Drilling: Holes are drilled into the PCB for through-hole components and vias.
d. Plating: The drilled holes are plated with copper to create electrical connections between layers.
e. Etching: Unwanted copper is removed using a chemical etching process, leaving behind the desired conductive tracks.
f. Solder mask application: A protective solder mask is applied to the PCB, exposing only the areas intended for soldering.
g. Silkscreen printing: Text and symbols are printed onto the PCB for component identification and assembly guidance. - PCB Assembly: The manufactured PCB is populated with components, either through manual soldering or automated pick-and-place machines.
- Testing and inspection: The assembLED PCB undergoes various tests and inspections to ensure proper functionality and quality.
Quality Control and Testing
Rigorous quality control and testing are essential for ensuring the reliability and performance of LED grow light PCBs:
- Visual inspection: PCBs are visually inspected for defects such as incorrect component placement, solder bridges, or damaged traces.
- Automated optical inspection (AOI): Machine vision systems are used to automatically detect and classify PCB defects.
- In-circuit testing (ICT): Electrical tests are performed on the assembled PCB to verify the functionality of individual components and circuits.
- Functional testing: The PCB is tested under real-world operating conditions to ensure proper performance and reliability.
- Burn-in testing: PCBs are subjected to elevated temperatures and power levels to identify early failures and ensure long-term reliability.
Optimizing LED Grow Light PCB Performance
Thermal Management Techniques
Effective thermal management is crucial for maintaining the performance and longevity of LED grow light PCBs. Some common thermal management techniques include:
- Heatsinks: Attach heatsinks to the PCB to dissipate heat away from the LEDs and other components.
- Thermal vias: Use thermal vias to conduct heat from the component side of the PCB to the opposite side, where it can be dissipated more effectively.
- Thermal interface materials (TIMs): Apply TIMs, such as thermal paste or thermal pads, between the PCB and heatsink to enhance heat transfer.
- Active cooling: Implement active cooling solutions, such as fans or liquid cooling systems, for high-power LED grow light applications.
Improving Energy Efficiency
Optimizing the energy efficiency of LED grow light PCBs can help reduce operating costs and environmental impact:
- LED selection: Choose high-efficiency LEDs with a high luminous efficacy (lumens per watt) to minimize power consumption.
- Driver circuit optimization: Design the LED driver circuit to operate at peak efficiency, minimizing losses and heat generation.
- Pulse width modulation (PWM): Implement PWM dimming to adjust LED brightness without sacrificing efficiency.
- Intelligent control systems: Use sensors and control algorithms to optimize LED intensity and spectrum based on plant growth stages and environmental conditions.
Enhancing Spectrum Control
Controlling the light spectrum emitted by LED grow lights is essential for optimizing plant growth and development:
- Multi-channel LED arrays: Use separate LED channels for different wavelengths, allowing for independent control of each color.
- Spectrum-specific LEDs: Select LEDs with peak wavelengths tailored to the specific needs of the target plant species.
- Adjustable spectrum: Implement adjustable spectrum control to adapt the light output to different growth stages and plant types.
- Spectral mixing: Combine different LED colors to create a full-spectrum light source that closely mimics natural sunlight.
Future Trends in LED Grow Light PCB Technology
Advancements in LED Technology
LED technology continues to evolve, offering new opportunities for improving LED grow light PCB performance:
- Higher efficiency LEDs: As LED efficiency improves, grow lights can produce more light output with less power consumption.
- Narrow-band LEDs: LEDs with narrower spectral bandwidths allow for more precise control over the light spectrum.
- UV and IR LEDs: The incorporation of ultraviolet (UV) and infrared (IR) LEDs can provide additional benefits for plant growth and development.
- Flexible and transparent LEDs: Emerging flexible and transparent LED technologies may enable new form factors and applications for LED grow lights.
Integration of IoT and Smart Control Systems
The integration of Internet of Things (IoT) and smart control systems is transforming the way LED grow lights are managed and optimized:
- Remote monitoring and control: IoT-enabled grow lights can be monitored and controlled remotely via web or mobile interfaces.
- Sensor integration: Sensors for temperature, humidity, light intensity, and other environmental factors can be integrated into LED grow light PCBs for real-time monitoring and automation.
- Machine learning and AI: Machine learning algorithms can analyze sensor data and optimize LED grow light settings for maximum plant growth and efficiency.
- Predictive maintenance: IoT systems can monitor LED grow light PCB performance and predict maintenance needs, reducing downtime and extending system lifespan.
Sustainable and Eco-Friendly Manufacturing
As environmental concerns continue to grow, sustainable and eco-friendly manufacturing practices are becoming increasingly important in the LED grow light PCB industry:
- Lead-free and RoHS-compliant: Manufacturers are adopting lead-free and Restriction of Hazardous Substances (RoHS) compliant materials and processes.
- Recycling and waste reduction: PCB manufacturers are implementing recycling programs and waste reduction initiatives to minimize environmental impact.
- Energy-efficient manufacturing: Manufacturers are optimizing their production processes to reduce energy consumption and carbon footprint.
- Sustainable materials: Research into sustainable PCB materials, such as biodegradable substrates and low-impact coatings, is ongoing.
Frequently Asked Questions (FAQ)
- What are the most important factors to consider when choosing an LED for a grow light PCB?
When choosing an LED for a grow light PCB, consider the following factors: - Wavelength: Select LEDs with peak wavelengths that match the photosynthetic needs of your target plant species.
- Efficiency: Choose LEDs with high luminous efficacy (lumens per watt) to minimize power consumption and heat generation.
- Brightness: Ensure that the LED provides sufficient light intensity for your grow light application.
- Beam angle: Consider the LED’s beam angle to ensure proper light distribution over the grow area.
-
Reliability: Choose LEDs from reputable manufacturers with proven reliability and longevity.
-
How do I ensure proper thermal management for my LED grow light PCB?
To ensure proper thermal management for your LED grow light PCB, consider the following strategies: - Use a PCB substrate with good thermal conductivity, such as aluminum or copper-clad laminate.
- Incorporate heatsinks and thermal vias to dissipate heat away from the LEDs and other components.
- Apply thermal interface materials, such as thermal paste or pads, between the PCB and heatsink.
- Implement active cooling solutions, such as fans or liquid cooling, for high-power applications.
-
Monitor PCB temperature during operation and adjust cooling solutions as needed.
-
What are the advantages of using a multi-layer PCB for LED grow lights?
Multi-layer PCBs offer several advantages for LED grow light applications: - Improved routing options: Multiple layers allow for more complex routing and signal isolation.
- Better heat dissipation: Additional layers can be used for power and ground planes, improving heat distribution.
- Reduced EMI: Multiple layers can help reduce electromagnetic interference by providing shielding and separating sensitive signals.
-
Compact design: Multi-layer PCBs enable more components to be packed into a smaller area, reducing overall system size.
-
How can I optimize the energy efficiency of my LED grow light PCB?
To optimize the energy efficiency of your LED grow light PCB, consider the following techniques: - Select high-efficiency LEDs with a high luminous efficacy (lumens per watt).
- Design the LED driver circuit to operate at peak efficiency, minimizing losses and heat generation.
- Implement pulse width modulation (PWM) dimming to adjust LED brightness without sacrificing efficiency.
- Use sensors and control algorithms to optimize LED intensity and spectrum based on plant growth stages and environmental conditions.
-
Monitor power consumption and adjust settings as needed to maintain optimal efficiency.
-
What are some emerging trends in LED grow light PCB technology?
Some emerging trends in LED grow light PCB technology include: - Higher efficiency LEDs: Advancements in LED technology are leading to more efficient and powerful grow light solutions.
- Narrow-band LEDs: LEDs with narrower spectral bandwidths allow for more precise control over the light spectrum.
- Integration of IoT and smart control systems: IoT-enabled grow lights can be monitored and controlled remotely, with sensor integration and machine learning algorithms for optimization.
- Sustainable and eco-friendly manufacturing: PCB manufacturers are adopting sustainable materials and processes to reduce environmental impact.
- Flexible and transparent LEDs: Emerging LED technologies may enable new form factors and applications for LED grow lights.
Conclusion
LED grow light PCBs are essential components in modern horticulture, providing the foundation for efficient, reliable, and optimized plant growth. By understanding the principles of PCB design, manufacturing, and optimization, growers and manufacturers can create LED grow light solutions that maximize plant health, energy efficiency, and sustainability. As LED and PCB technologies continue to advance, the future of LED grow lights looks brighter than ever, with new opportunities for innovation and growth in the indoor farming and horticulture industries.
Leave a Reply