Introduction to LED driver circuits
Light-emitting diodes (LEDs) have become increasingly popular in modern lighting applications due to their energy efficiency, long lifespan, and versatility. However, LEDs require a specific current and voltage to operate optimally, which is where LED driver circuits come into play. In this article, we will explore the concept of LED driver circuits, focusing on constant current source driver circuits and their corresponding diagrams.
What is an LED Driver Circuit?
An LED driver circuit is an electronic circuit designed to regulate the power supplied to an LED or an array of LEDs. Its primary function is to provide a constant current or voltage to the LEDs, ensuring stable and consistent illumination. LED driver circuits protect the LEDs from voltage fluctuations and ensure they operate within their specified current and voltage ranges.
Importance of Constant Current in LED Lighting
LEDs are current-driven devices, meaning their brightness is directly proportional to the current flowing through them. Overdriving an LED with excessive current can lead to reduced lifespan or even permanent damage. On the other hand, insufficient current results in dimmer light output. To achieve optimal performance and longevity, it is crucial to maintain a constant current through the LEDs.
Constant Current Source LED Driver Circuits
Basic Constant Current Source Circuit
A basic constant current source circuit for driving LEDs consists of the following components:
- Voltage source (e.g., battery or power supply)
- Current-limiting resistor
- LED or LED array
The current-limiting resistor is connected in series with the LED and is responsible for setting the current flowing through the LED. The resistor’s value is calculated based on the LED’s forward voltage drop and the desired current.
Here’s a simple diagram illustrating a basic constant current source circuit:
+-------+
| |
| LED |
| |
+---+---+
|
|
R
|
|
+----+----+
| |
| Power |
| Supply |
| |
+---------+
The resistor value can be calculated using Ohm’s law:
R = (V_supply - V_LED) / I_LED
Where:
– R is the resistor value in ohms (Ω)
– V_supply is the voltage of the power supply
– V_LED is the forward voltage drop of the LED
– I_LED is the desired current through the LED
Improved Constant Current Source Circuits
While the basic constant current source circuit is simple and effective, it has limitations. The current through the LED can still vary with changes in the power supply voltage or the LED’s forward voltage drop. To overcome these limitations, more advanced constant current source circuits have been developed.
1. LM317 Adjustable Voltage Regulator Circuit
The LM317 is a popular adjustable voltage regulator IC that can be configured as a constant current source. By adding a resistor between the output and adjustment pins of the LM317, the current through the LED can be set and maintained at a constant value.
Here’s a diagram of an LM317-based constant current source LED driver circuit:
+--------+
| |
| LED |
| |
+---+----+
|
|
R1
|
|
+-----+-----+
| |
IN | LM317 | OUT
| |
+-----+-----+
|
|
R2
|
|
GND
The current through the LED is determined by the value of resistor R1 and can be calculated using the following equation:
I_LED = 1.25V / R1
Resistor R2 is used to set the minimum load current for the LM317 and is typically chosen to be around 120Ω.
2. Transistor-Based Constant Current Source Circuit
Another approach to designing a constant current source LED driver circuit is to use a transistor. In this configuration, the transistor acts as a current regulator, maintaining a constant current through the LED.
Here’s a diagram of a transistor-based constant current source LED driver circuit:
+--------+
| |
| LED |
| |
+---+----+
|
|
R1
|
|
+-----+-----+
| |
| Q1 |
| |
+-----+-----+
|
|
R2
|
|
GND
In this circuit, transistor Q1 (e.g., a BJT or MOSFET) is used to control the current through the LED. Resistor R1 sets the base or gate current of the transistor, which in turn determines the collector or drain current (I_LED). Resistor R2 provides a path for the base or gate current.
The current through the LED can be calculated using the following equation:
I_LED = (V_supply - V_BE) / R1
Where:
– V_BE is the base-emitter voltage drop of the transistor (approximately 0.7V for a BJT)
Constant Current Source LED Driver ICs
For more advanced and precise control over LED current, dedicated constant current source LED driver ICs are available. These ICs integrate the necessary components and circuitry to provide a stable and adjustable constant current output. Some popular LED driver ICs include:
- LM3414
- TPS92515
- AL8805
- BCR401
These ICs offer features such as dimming control, PWM (Pulse Width Modulation) capability, and protection functions (e.g., over-temperature, short-circuit, and open-Circuit Protection).
LED Array Configurations
When designing LED lighting systems, it is common to use multiple LEDs to achieve the desired light output. LEDs can be arranged in various configurations, such as series, parallel, or a combination of both.
Series Configuration
In a series configuration, LEDs are connected in a single string, with the cathode of one LED connected to the anode of the next. The total voltage drop across the LED string is the sum of the individual LED forward voltage drops.
Here’s a diagram illustrating a series LED configuration:
+--------+ +--------+ +--------+
| | | | | |
+------+ LED1 +-------+ LED2 +-------+ LED3 +------+
| | | | | |
+--------+ +--------+ +--------+
Advantages of series configuration:
– Ensures equal current through all LEDs
– Requires a single current-limiting resistor or constant current source
Disadvantages of series configuration:
– Higher voltage supply is needed to accommodate the total voltage drop
– If one LED fails (open-circuit), the entire string will not illuminate
Parallel Configuration
In a parallel configuration, LEDs are connected with their anodes and cathodes in parallel. Each LED branch has its own current-limiting resistor or constant current source.
Here’s a diagram illustrating a parallel LED configuration:
+--------+
| |
+------+ LED1 +------+
| | | |
| +--------+ |
| |
| +--------+ |
| | | |
+------+ LED2 +------+
| | | |
| +--------+ |
| |
| +--------+ |
| | | |
+------+ LED3 +------+
| |
+--------+
Advantages of parallel configuration:
– Lower voltage supply can be used
– If one LED fails (open-circuit), the other LEDs will continue to illuminate
Disadvantages of parallel configuration:
– Requires a current-limiting resistor or constant current source for each LED branch
– Current may not be evenly distributed among the LEDs due to variations in forward voltage drops
Series-Parallel Configuration
A series-parallel configuration combines the benefits of both series and parallel arrangements. LEDs are connected in series strings, and these strings are then connected in parallel.
Here’s a diagram illustrating a series-parallel LED configuration:
+--------+ +--------+
| | | |
+------+ LED1 +-------+ LED2 +------+
| | | | | |
| +--------+ +--------+ |
| |
| +--------+ +--------+ |
| | | | | |
+------+ LED3 +-------+ LED4 +------+
| | | |
+--------+ +--------+
Advantages of series-parallel configuration:
– Allows for a balance between voltage and current requirements
– Provides some level of redundancy if an LED fails (open-circuit)
Disadvantages of series-parallel configuration:
– More complex wiring compared to pure series or parallel configurations
– Requires careful consideration of LED forward voltage drops and current distribution
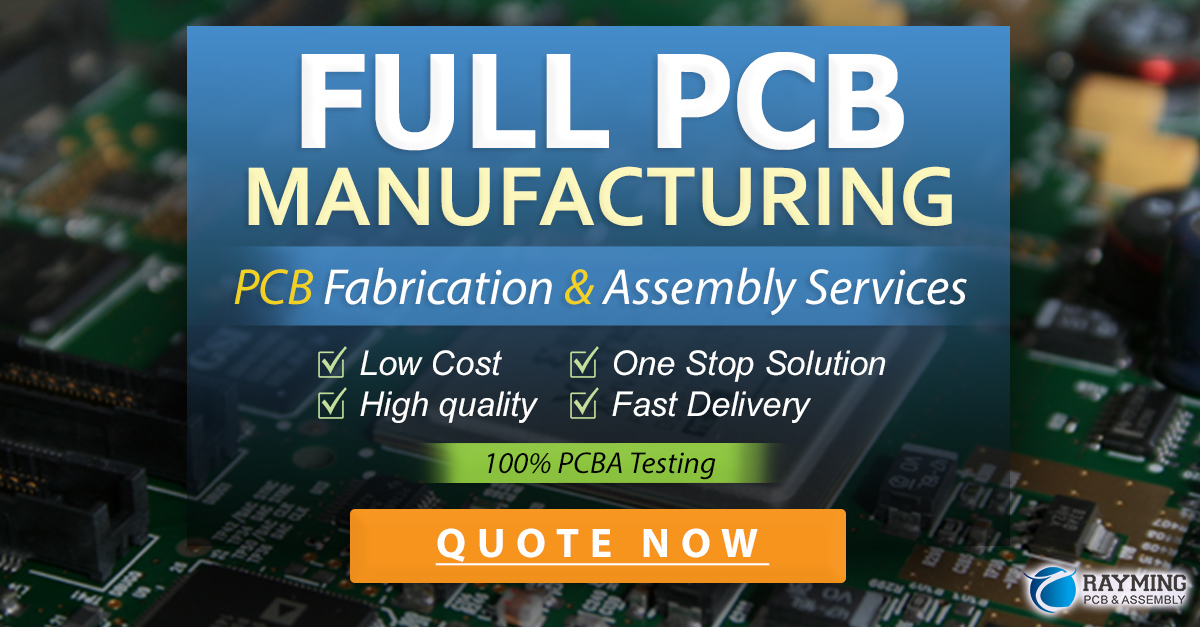
Dimming Control in LED Driver Circuits
Dimming control is a desirable feature in many LED lighting applications. It allows for adjustable light output and can contribute to energy savings. There are several methods for implementing dimming control in LED driver circuits.
PWM Dimming
Pulse Width Modulation (PWM) dimming is a commonly used technique for controlling LED brightness. In PWM dimming, the LED is rapidly switched on and off at a high frequency, with the duty cycle (the ratio of on-time to the total period) determining the perceived brightness.
Here’s a diagram illustrating PWM dimming control in an LED driver circuit:
+--------+
| |
| LED |
| |
+---+----+
|
|
+-----+-----+
| |
IN | LED | OUT
| Driver IC |
| |
+-----+-----+
|
|
PWM
|
|
+------+------+
| |
| PWM Signal |
| Generator |
| |
+-------------+
Advantages of PWM dimming:
– Provides precise and flicker-free dimming control
– Maintains color consistency across the dimming range
– Relatively simple to implement with LED driver ICs that support PWM input
Disadvantages of PWM dimming:
– Requires a PWM signal generator or microcontroller
– May introduce electromagnetic interference (EMI) if not properly filtered
Analog Dimming
Analog dimming involves varying the DC current through the LED to control its brightness. This can be achieved by adjusting the reference voltage or current in the LED driver circuit.
Here’s a diagram illustrating analog dimming control in an LED driver circuit:
+--------+
| |
| LED |
| |
+---+----+
|
|
+-----+-----+
| |
IN | LED | OUT
| Driver IC |
| |
+-----+-----+
|
|
+-----+-----+
| |
| Variable |
| Resistor |
| |
+-----------+
Advantages of analog dimming:
– Smooth and continuous dimming control
– Simple implementation with a variable resistor or potentiometer
Disadvantages of analog dimming:
– Limited dimming range compared to PWM dimming
– Potential color shift at low dimming levels
– Requires a compatible LED driver IC with analog dimming input
Smart Dimming Techniques
In addition to PWM and analog dimming, there are smart dimming techniques that involve intelligent control algorithms and Communication Protocols. These techniques offer advanced features such as:
- Addressable dimming control for individual LEDs or LED groups
- Wireless dimming control via Wi-Fi, Bluetooth, or other communication protocols
- Adaptive dimming based on ambient light conditions or occupancy sensing
- Integration with smart home systems and IoT platforms
Smart dimming techniques often require specialized LED driver ICs and control systems, such as DMX controllers or wireless communication modules.
Thermal Management in LED Driver Circuits
Proper thermal management is crucial for the longevity and performance of LED lighting systems. LEDs generate heat during operation, and excessive heat can lead to reduced lifespan, color shift, and decreased light output.
Importance of Heat Dissipation
Heat dissipation is essential to prevent thermal stress on the LEDs and maintain optimal operating temperatures. The junction temperature of an LED, which is the temperature at the p-n junction, should be kept within the manufacturer’s specified limits.
Factors affecting heat dissipation in LED driver circuits include:
– Power dissipation of the LEDs
– Ambient temperature
– Thermal resistance of the LED package and PCB
– Airflow and ventilation around the LEDs
Thermal Management Techniques
Several thermal management techniques can be employed in LED driver circuits to ensure proper heat dissipation:
- Heat Sinks:
- Attach heat sinks to the LED PCB or individual LEDs to increase the surface area for heat dissipation.
-
Use materials with high thermal conductivity, such as aluminum or copper, for efficient heat transfer.
-
PCB Design:
- Use a PCB with a thick copper layer and large ground planes to improve heat spreading.
-
Minimize the thermal resistance between the LED pads and the PCB Copper.
-
Thermal Interface Materials (TIMs):
-
Apply thermal interface materials, such as thermal paste or thermal pads, between the LED package and the heat sink to enhance thermal conductivity.
-
Airflow and Ventilation:
- Ensure adequate airflow around the LEDs and driver components to facilitate convective cooling.
-
Use fans or other active cooling methods in high-power LED systems.
-
Thermal Feedback and Protection:
- Implement thermal feedback mechanisms, such as Temperature Sensors, to monitor the LED temperature.
- Incorporate thermal protection features in the LED driver circuit, such as over-temperature shutdown or current foldback, to prevent damage to the LEDs.
Proper thermal management helps to ensure the long-term reliability and performance of LED lighting systems.
EMI Considerations in LED Driver Circuits
Electromagnetic Interference (EMI) is a critical consideration in LED driver circuit design. LEDs and their driver circuits can generate high-frequency noise that can interfere with nearby electronic devices and communication systems.
Sources of EMI in LED Driver Circuits
The main sources of EMI in LED driver circuits include:
- Switching Noise:
-
High-frequency switching in LED driver ICs and power converters can generate conducted and radiated EMI.
-
Harmonics and Intermodulation:
-
Non-linear characteristics of LEDs and driver components can produce harmonics and intermodulation products that contribute to EMI.
-
Conducted EMI:
-
High-frequency noise can propagate through the power supply lines and interfere with other devices connected to the same power source.
-
Radiated EMI:
- High-frequency currents flowing through PCB traces and wires can act as antennas and radiate electromagnetic energy.
EMI Mitigation Techniques
To mitigate EMI in LED driver circuits, several techniques can be employed:
- Proper PCB Layout:
- Minimize loop areas and keep high-frequency traces as short as possible.
- Provide a low-impedance return path for high-frequency currents.
-
Use ground planes and proper grounding techniques to minimize radiated EMI.
-
Filtering:
- Implement input and output filters to attenuate high-frequency noise.
-
Use common-mode chokes, ferrite beads, and capacitors to suppress conducted EMI.
-
Shielding:
- Enclose sensitive components or the entire LED driver circuit in a shielded enclosure to reduce radiated EMI.
-
Use shielded cables for interconnections to minimize electromagnetic coupling.
-
Spread-Spectrum Techniques:
-
Employ spread-spectrum clocking or frequency dithering to reduce the peak energy of EMI at specific frequencies.
-
Compliance with EMC Standards:
- Ensure that the LED driver circuit complies with relevant electromagnetic compatibility (EMC) standards, such as FCC Part 15, EN 55015, or CISPR 15, depending on the target market and application.
Proper EMI mitigation helps to ensure the compatibility and reliability of LED lighting systems in various environments.
Frequently Asked Questions (FAQ)
- What is the purpose of an LED driver circuit?
-
An LED driver circuit is designed to regulate the power supplied to an LED or an array of LEDs. It provides a constant current or voltage to ensure stable and consistent illumination while protecting the LEDs from voltage fluctuations and overdriving.
-
Why is constant current important for LED lighting?
-
LEDs are current-driven devices, and their brightness is directly proportional to the current flowing through them. Maintaining a constant current ensures optimal performance, longevity, and prevents overdriving, which can lead to reduced lifespan or permanent damage to the LEDs.
-
What are the advantages of
Leave a Reply