What are PCB Copper Layers?
PCB copper layers are thin sheets of copper foil laminated onto the insulating substrate material of a printed circuit board. These layers act as conductive pathways for electrical signals and power distribution between various components on the board. The number of copper layers in a PCB can vary depending on the complexity and requirements of the circuit design.
Types of PCB Copper Layers
There are several types of PCB copper layers, each serving a specific purpose in the overall circuit design. Let’s explore some of the most common types:
1. Signal Layers
Signal layers are the most basic and essential copper layers in a PCB. They are responsible for carrying electrical signals between components on the board. These layers are usually located on the outer surfaces of the PCB and can be found in both single-sided and double-sided boards.
2. Power Planes
Power planes are copper layers that are dedicated to distributing power throughout the PCB. They provide a low-impedance path for the power supply to reach all the components on the board. Power planes are typically placed on the inner layers of a multi-layer PCB and are connected to the power supply through vias.
3. Ground Planes
Ground planes are copper layers that are connected to the ground potential of the circuit. They serve as a reference point for electrical signals and help to reduce electromagnetic interference (EMI) and crosstalk between signal traces. Ground planes are often placed adjacent to power planes to provide a return path for the current.
4. Mixed Signal Layers
Mixed signal layers are copper layers that contain both analog and digital signals. These layers require careful design considerations to minimize noise and interference between the different signal types. Techniques such as proper grounding, shielding, and signal isolation are employed to ensure the integrity of the mixed signals.
PCB Copper Layer Stackup
The arrangement of copper layers in a PCB is known as the layer stackup. The stackup determines the order and spacing of the layers, as well as the insulating materials used between them. A well-designed layer stackup is crucial for maintaining signal integrity, controlling impedance, and minimizing crosstalk and EMI.
Here’s an example of a typical 4-layer PCB Stackup:
Layer | Type | Material |
---|---|---|
Top | Signal | Copper |
Inner 1 | Ground | Copper |
Inner 2 | Power | Copper |
Bottom | Signal | Copper |
In this stackup, the top and bottom layers are used for signal routing, while the inner layers are dedicated to ground and power distribution. The insulating material, such as FR-4, is placed between the layers to provide electrical isolation.
PCB Copper Layer Manufacturing Process
The manufacturing process of PCB copper layers involves several steps to ensure the highest quality and reliability. Let’s walk through the key stages of the process:
1. PCB Design and Layout
The first step in the manufacturing process is to design the PCB using specialized software tools. The design includes the placement of components, routing of copper traces, and the creation of the layer stackup. The design files are then sent to the PCB manufacturer for fabrication.
2. Copper Foil Lamination
The insulating substrate material, such as FR-4, is cut to the desired size and thickness. Copper foil is then laminated onto the substrate using heat and pressure. The copper foil is typically available in various thicknesses, ranging from 0.5 oz to 2 oz per square foot.
3. Photoresist Application
A photosensitive resist material is applied to the copper surface of the laminated board. The resist is typically a thin, light-sensitive polymer that hardens when exposed to ultraviolet (UV) light.
4. Exposure and Development
The PCB design artwork is used to create a photomask, which is placed on top of the photoresist-coated copper layer. The board is then exposed to UV light, which hardens the resist in the areas not covered by the photomask. The unexposed resist is then removed using a chemical developer, leaving behind a pattern of hardened resist that matches the desired copper traces and pads.
5. Etching
The exposed copper areas not protected by the hardened resist are etched away using a chemical solution, typically an acidic copper etchant. This process removes the unwanted copper, leaving behind the desired copper traces and pads.
6. Resist Removal and Inspection
After etching, the remaining hardened resist is stripped away using a chemical solvent, revealing the final copper pattern. The PCB is then inspected for any defects or irregularities.
7. Multilayer Lamination and Drilling
For multi-layer PCBs, the individual layers are aligned and laminated together under heat and pressure. Holes are then drilled through the board to create vias that connect the different layers electrically.
8. Surface Finishing
The exposed copper surfaces are coated with a protective finish to prevent oxidation and improve solderability. Common surface finishes include HASL (Hot Air Solder Leveling), ENIG (Electroless Nickel Immersion Gold), and OSP (Organic Solderability Preservative).
Importance of PCB Copper Layers in Electronics Industry
PCB copper layers play a vital role in the electronics industry, enabling the creation of compact, reliable, and high-performance devices. Here are some of the key reasons why PCB copper layers are essential:
-
Miniaturization: PCB copper layers allow for the dense routing of electrical signals, enabling the design of smaller and more compact electronic devices. This is particularly important in the era of mobile and wearable electronics, where space is at a premium.
-
Signal Integrity: Properly designed PCB copper layers ensure the integrity of electrical signals by providing low-impedance paths and minimizing crosstalk and EMI. This is crucial for high-speed digital circuits and sensitive analog signals.
-
Power Distribution: Dedicated power planes in multi-layer PCBs provide efficient and stable power distribution to all components on the board. This helps to minimize voltage drops and ensures the reliable operation of the device.
-
Heat Dissipation: Copper layers also serve as heat spreaders, helping to dissipate heat generated by components on the board. This is particularly important for high-power devices and those operating in harsh environments.
-
Cost-effective Manufacturing: PCB copper layers enable the mass production of electronic devices using automated manufacturing processes. This reduces the cost per unit and makes electronics more affordable and accessible to consumers.
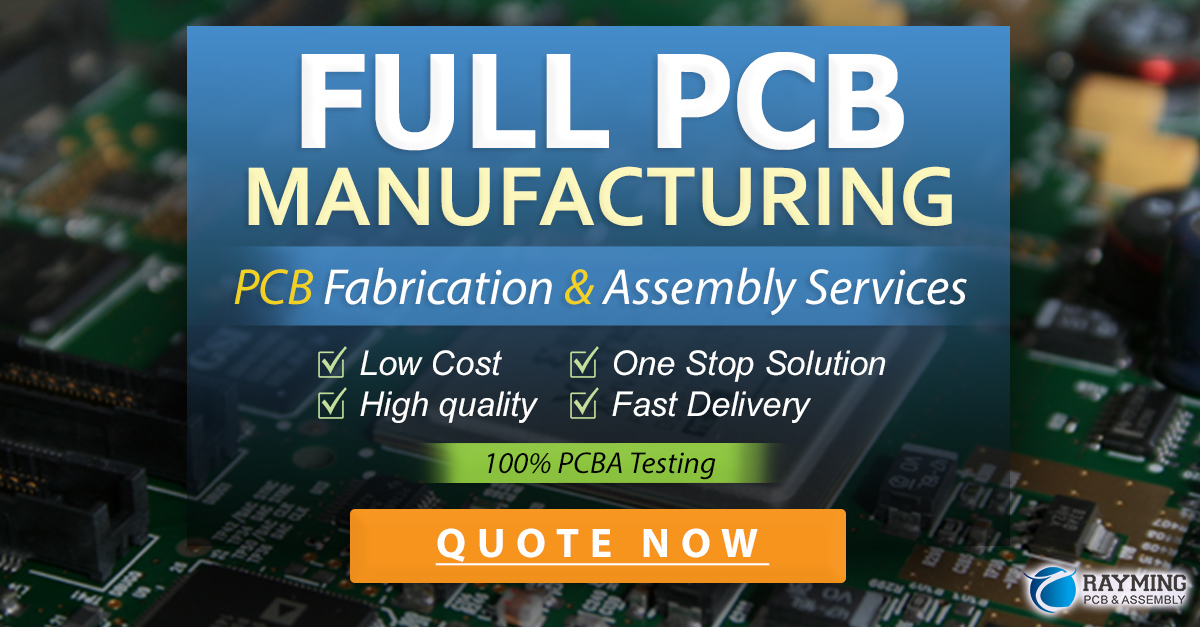
Frequently Asked Questions (FAQ)
-
What is the difference between a single-sided and double-sided PCB?
A single-sided PCB has copper traces and components on only one side of the board, while a double-sided PCB has copper layers and components on both sides. Double-sided PCBs offer more design flexibility and higher component density compared to single-sided boards. -
What is the purpose of vias in a multi-layer PCB?
Vias are conductive holes drilled through the PCB that connect different copper layers electrically. They allow signals and power to be routed between layers, enabling more complex circuit designs and efficient use of board space. -
What factors determine the number of copper layers needed in a PCB?
The number of copper layers required in a PCB depends on several factors, including the complexity of the circuit design, the number of components, signal integrity requirements, power distribution needs, and the available board space. More complex designs with a higher component count and stricter performance requirements typically require more layers. -
What is the significance of copper thickness in PCB manufacturing?
The thickness of the copper foil used in PCB manufacturing, typically measured in ounces per square foot, determines the current-carrying capacity and the resistance of the traces. Thicker copper layers can handle higher currents and provide lower resistance, which is important for power distribution and high-current applications. -
How does the choice of surface finish affect the performance of PCB copper layers?
The surface finish applied to the exposed copper layers affects the solderability, durability, and shelf life of the PCB. Different surface finishes, such as HASL, ENIG, and OSP, offer varying levels of protection against oxidation, ease of soldering, and compatibility with different assembly processes. The choice of surface finish depends on the specific requirements of the application and the manufacturing process.
Conclusion
PCB copper layers are the unsung heroes of the electronics industry, providing the essential connectivity and functionality that enables the creation of sophisticated devices. From signal routing and power distribution to heat dissipation and miniaturization, copper layers play a critical role in the performance and reliability of modern electronics.
As the demand for more advanced and compact electronic devices continues to grow, the importance of PCB copper layers will only increase. Innovations in materials, manufacturing processes, and design tools will drive the development of ever-more complex and capable PCBs, pushing the boundaries of what is possible in the world of electronics.
By understanding the types, manufacturing process, and significance of PCB copper layers, engineers, designers, and manufacturers can collaborate to create the next generation of electronic devices that will shape our future.
Leave a Reply