Understanding Thermal Aging in PCBAs
Thermal aging refers to the degradation of materials over time when exposed to elevated temperatures. In the context of printed circuit board assemblies (PCBAs), thermal aging can lead to a variety of issues, such as component failures, solder joint deterioration, and delamination of the PCB Substrate.
PCBAs are subjected to various environmental stresses throughout their lifecycle, including temperature fluctuations and humidity exposure. These factors can accelerate the thermal aging process, compromising the reliability and performance of the assembly. Therefore, it is crucial to test PCBAs against heat and humidity to ensure their long-term durability and functionality.
Factors Contributing to Thermal Aging
Several factors contribute to the thermal aging of PCBAs:
- Temperature: Higher temperatures accelerate chemical reactions and material degradation, leading to faster aging.
- Humidity: Moisture can penetrate the PCBA, causing corrosion, delamination, and other moisture-related failures.
- Material properties: The inherent properties of the materials used in the PCBA, such as the glass transition temperature (Tg) of the PCB substrate and the melting point of the solder alloy, affect their susceptibility to thermal aging.
- Design factors: PCBA design aspects, such as component placement, thermal management, and coating selection, can influence the assembly’s ability to withstand thermal stress.
Effects of Thermal Aging on PCBAs
Thermal aging can have various detrimental effects on PCBAs:
- Component degradation: Prolonged exposure to high temperatures can cause components to degrade, leading to reduced performance or complete failure.
- Solder joint deterioration: Thermal stress can cause solder joints to crack, leading to intermittent connections or open circuits.
- Delamination: High temperatures and humidity can weaken the adhesion between the PCB Layers, resulting in delamination and loss of structural integrity.
- Insulation breakdown: Thermal aging can degrade the insulation properties of the PCB substrate and coatings, increasing the risk of electrical shorts and leakage currents.
Testing PCBAs Against Thermal Aging
To ensure the reliability and longevity of PCBAs, it is essential to perform thorough testing against thermal aging. This section will discuss various testing methods and standards commonly used in the industry.
Accelerated Thermal Aging Tests
Accelerated thermal aging tests expose PCBAs to elevated temperatures for a specified duration to simulate the effects of long-term exposure in a shorter timeframe. These tests help identify potential weaknesses and failure modes in the assembly.
Arrhenius Equation and Acceleration Factor
The Arrhenius equation is used to calculate the acceleration factor (AF) for thermal aging tests:
AF = exp[Ea/k * (1/T1 – 1/T2)]
Where:
– Ea = Activation energy (eV)
– k = Boltzmann’s constant (8.617 × 10^-5 eV/K)
– T1 = Reference temperature (K)
– T2 = Accelerated test temperature (K)
The acceleration factor determines how much faster the aging process occurs at the elevated test temperature compared to the reference temperature.
Parameter | Value |
---|---|
Ea | 0.7 eV (typical for PCBAs) |
k | 8.617 × 10^-5 eV/K |
T1 | 298 K (25°C) |
T2 | 398 K (125°C) |
Using these values, the acceleration factor for a test temperature of 125°C compared to a reference temperature of 25°C is approximately 190. This means that exposing the PCBA to 125°C for 100 hours is equivalent to 19,000 hours (2.17 years) at 25°C.
Test Conditions and Durations
The test conditions and durations for accelerated thermal aging tests depend on the specific application and reliability requirements of the PCBA. Some common test conditions include:
Test Condition | Temperature | Duration |
---|---|---|
High Temperature Operating Life (HTOL) | 125°C | 1000 hours |
Temperature Cycling | -40°C to 125°C | 1000 cycles |
Thermal Shock | -55°C to 125°C | 500 cycles |
These tests expose the PCBA to extreme temperature conditions to accelerate the aging process and identify potential failures.
Combined Temperature and Humidity Tests
In addition to thermal aging, PCBAs may also be subjected to humidity exposure during their lifecycle. Combined temperature and humidity tests evaluate the PCBA’s ability to withstand both thermal and moisture-related stresses.
Temperature-Humidity-Bias (THB) Test
The Temperature-Humidity-Bias (THB) test exposes the PCBA to elevated temperature and humidity conditions while applying a specified electrical bias. This test is designed to accelerate the effects of moisture-related failures, such as corrosion and delamination.
Typical THB test conditions include:
Parameter | Value |
---|---|
Temperature | 85°C |
Relative Humidity | 85% RH |
Bias Voltage | Specified by the application |
Duration | 1000 hours |
During the THB test, the PCBA is monitored for any signs of degradation or failure, such as changes in electrical performance or visual defects.
Highly Accelerated Stress Test (HAST)
The Highly Accelerated Stress Test (HAST) is a more aggressive version of the THB test, using higher temperature and humidity conditions to further accelerate the aging process.
Typical HAST conditions include:
Parameter | Value |
---|---|
Temperature | 130°C |
Relative Humidity | 85% RH |
Pressure | 2 atm |
Duration | 96 hours |
HAST is often used to quickly screen for moisture-related failures and identify design weaknesses in the PCBA.
Evaluating Test Results
After conducting thermal aging and combined temperature and humidity tests, it is essential to evaluate the results and determine the PCBA’s reliability.
Visual Inspection
Visual inspection is the first step in evaluating the PCBA after testing. Look for any signs of physical damage, such as:
- Discoloration or charring of components or PCB substrate
- Cracks or delamination in the PCB
- Swelling or deformation of components
- Corrosion or dendrite growth on metal surfaces
Electrical Testing
Perform electrical tests to verify the functionality and performance of the PCBA after thermal aging. This may include:
- Continuity and isolation tests
- Functional tests
- Parametric tests (e.g., resistance, capacitance, and inductance measurements)
- Insulation resistance and dielectric withstanding voltage tests
Compare the post-test results with the initial measurements to identify any changes or degradation in electrical performance.
Failure Analysis
If failures are detected during visual inspection or electrical testing, conduct a thorough failure analysis to determine the root cause. This may involve:
- Cross-sectioning of the PCB and components
- Scanning Electron Microscopy (SEM) to examine solder joints and material interfaces
- Energy-Dispersive X-ray Spectroscopy (EDS) to analyze chemical composition
- Fourier-Transform Infrared Spectroscopy (FTIR) to identify organic contaminants or degradation products
Use the findings from the failure analysis to improve the PCBA design, material selection, or manufacturing processes to enhance reliability.
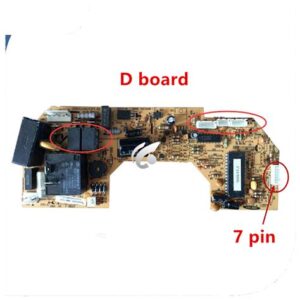
Designing PCBAs for Thermal Aging Resistance
To minimize the effects of thermal aging on PCBAs, consider the following design guidelines:
- Material Selection: Choose materials with high glass transition temperatures (Tg) and good thermal stability. Use high-temperature solder alloys and components rated for the expected operating conditions.
- Thermal Management: Implement effective thermal management techniques, such as using heatsinks, Thermal Vias, and proper airflow, to dissipate heat and reduce thermal stress on components.
- Conformal Coating: Apply conformal coating to the PCBA to protect against moisture ingress and corrosion. Select a coating material that is compatible with the expected environmental conditions.
- Design for Manufacturability (DFM): Follow DFM guidelines to ensure robust solder joints and minimize stress on components during assembly and operation. This includes proper component placement, pad sizing, and thermal expansion matching.
- Thermal Cycling Simulation: Use thermal cycling simulation tools to predict the PCBA’s response to temperature fluctuations and identify potential failure sites. Modify the design to improve thermal cycling performance.
By incorporating these design considerations, PCBAs can be made more resistant to thermal aging, improving their long-term reliability and performance.
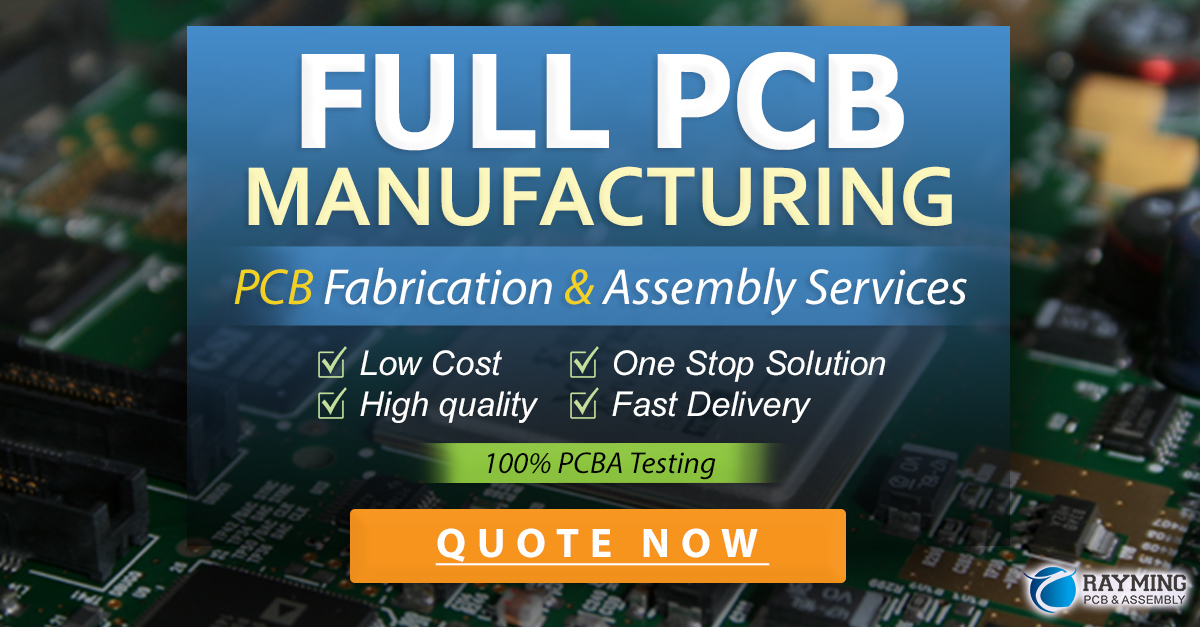
Frequently Asked Questions (FAQ)
- Q: What is thermal aging, and why is it important to test PCBAs against it?
A: Thermal aging refers to the degradation of materials over time when exposed to elevated temperatures. In PCBAs, thermal aging can lead to component failures, solder joint deterioration, and delamination of the PCB substrate. Testing PCBAs against thermal aging helps ensure their long-term durability and functionality in the intended operating environment. - Q: What factors contribute to the thermal aging of PCBAs?
A: Several factors contribute to the thermal aging of PCBAs, including temperature, humidity, material properties, and design factors. Higher temperatures and moisture exposure accelerate chemical reactions and material degradation, while the inherent properties of the materials used and the PCBA design aspects influence the assembly’s ability to withstand thermal stress. - Q: What are some common thermal aging tests for PCBAs?
A: Common thermal aging tests for PCBAs include accelerated thermal aging tests, such as High Temperature Operating Life (HTOL), Temperature Cycling, and Thermal Shock, as well as combined temperature and humidity tests, like Temperature-Humidity-Bias (THB) and Highly Accelerated Stress Test (HAST). These tests expose the PCBA to elevated temperature and humidity conditions to simulate long-term exposure and identify potential failures. - Q: How can I design PCBAs to be more resistant to thermal aging?
A: To design PCBAs for thermal aging resistance, consider the following guidelines: - Choose materials with high glass transition temperatures and good thermal stability
- Implement effective thermal management techniques
- Apply conformal coating to protect against moisture ingress and corrosion
- Follow Design for Manufacturability (DFM) guidelines for robust solder joints and minimized component stress
- Use thermal cycling simulation tools to predict PCBA response to temperature fluctuations and identify potential failure sites
- Q: What should I do if failures are detected during thermal aging tests?
A: If failures are detected during thermal aging tests, conduct a thorough failure analysis to determine the root cause. This may involve visual inspection, cross-sectioning, and advanced analytical techniques like Scanning Electron Microscopy (SEM) and Energy-Dispersive X-ray Spectroscopy (EDS). Use the findings from the failure analysis to improve the PCBA design, material selection, or manufacturing processes to enhance reliability.
Leave a Reply