Definition and Purpose of Thermal Vias
A thermal via is a specialized type of via, which is a small hole drilled through a PCB to allow for the passage of heat from one layer to another. Unlike regular vias that are primarily used for electrical connectivity, thermal vias are designed to transfer heat away from heat-generating components, such as high-power processors, LEDs, or power transistors. By providing a low-resistance thermal path, thermal vias help to dissipate heat efficiently, preventing components from overheating and ensuring optimal performance.
How Thermal Vias Work
Thermal vias work by conducting heat from the heat-generating component through the PCB to a heat sink or other cooling solution. The process can be broken down into the following steps:
- Heat generation: The electronic component generates heat during operation.
- Heat transfer to PCB: The heat is conducted from the component to the PCB through the Thermal Pad or exposed copper area.
- Heat conduction through thermal vias: The heat is then transferred through the thermal vias, which act as a conduit for heat flow.
- Heat dissipation: The heat is finally dissipated through the heat sink or other cooling solution attached to the opposite side of the PCB.
By efficiently transferring heat away from the component, thermal vias help to maintain the device’s temperature within acceptable limits, ensuring optimal performance and reliability.
Design Considerations for Thermal Vias
When incorporating thermal vias into a PCB design, several key factors must be considered to ensure optimal heat transfer and overall performance. These factors include via size, via placement, via fill material, and via density.
Via Size
The size of a thermal via is a critical factor in determining its heat transfer capabilities. Larger vias offer lower thermal resistance, allowing for more efficient heat dissipation. However, larger vias also consume more board space and can impact signal integrity. Therefore, designers must strike a balance between thermal performance and other design constraints when selecting via sizes.
Typical thermal via sizes range from 0.2mm to 0.5mm in diameter, depending on the specific application and the amount of heat that needs to be dissipated.
Via Placement
The placement of thermal vias is another crucial design consideration. Thermal vias should be strategically located as close to the heat-generating component as possible to minimize the thermal path and ensure efficient heat transfer. Additionally, vias should be evenly distributed around the component to provide a uniform thermal path and avoid hot spots.
In some cases, thermal vias may be placed directly under the component, creating what is known as a “via-in-pad” design. This approach offers the shortest possible thermal path but requires careful consideration of solderability and manufacturing challenges.
Via Fill Material
Thermal vias can be filled with various materials to enhance their heat transfer capabilities and improve mechanical stability. The most common fill materials include:
- Copper: Copper-filled vias offer the highest thermal conductivity and are often used in high-power applications.
- Solder: Solder-filled vias provide good thermal conductivity and help to improve the mechanical strength of the via.
- Epoxy: Epoxy-filled vias offer a balance between thermal conductivity and cost, making them suitable for a wide range of applications.
The choice of fill material depends on the specific requirements of the application, including thermal performance, cost, and manufacturing constraints.
Via Density
Via density refers to the number of thermal vias per unit area. Higher via densities offer better heat dissipation but can also increase manufacturing complexity and cost. Designers must carefully consider the trade-offs between thermal performance and manufacturability when determining the appropriate via density for a given application.
Typical via densities range from 10 to 50 vias per square centimeter, depending on the heat dissipation requirements and the specific design constraints.
Manufacturing Processes for Thermal Vias
The manufacturing process for thermal vias involves several key steps, including drilling, plating, and filling. Each step must be carefully controlled to ensure the integrity and performance of the final product.
Drilling
Thermal vias are typically drilled using specialized equipment, such as laser drills or mechanical drills. The choice of drilling method depends on the required via size, aspect ratio, and the specific PCB material.
Laser drilling offers high precision and the ability to create small, high-aspect-ratio vias, making it suitable for advanced applications. Mechanical drilling, on the other hand, is a more cost-effective option for larger vias and lower-density designs.
Plating
After drilling, the thermal vias must be plated to create a conductive path for heat transfer. The most common plating materials include copper and copper alloys, such as copper-Nickel-Gold or copper-tin.
The plating process typically involves several steps, including:
- Cleaning: The drilled vias are cleaned to remove any debris or contaminants.
- Activation: The via surfaces are activated to promote adhesion of the plating material.
- Electroless plating: A thin layer of copper is deposited onto the via surfaces using an electroless plating process.
- Electrolytic plating: Additional copper is deposited using an electrolytic plating process to achieve the desired thickness and conductivity.
The plating thickness and quality are critical factors in determining the thermal performance of the via. Thicker plating offers lower thermal resistance but can also increase manufacturing costs and impact signal integrity.
Filling
After plating, the thermal vias can be filled with a conductive material to further enhance their heat transfer capabilities and improve mechanical stability. The filling process typically involves the following steps:
- Applying fill material: The fill material, such as copper paste or solder, is applied to the vias using a screen printing or dispensing process.
- Curing or reflow: The fill material is then cured or reflowed to create a solid, conductive plug within the via.
- Planarization: The filled vias are planarized using a grinding or polishing process to create a smooth, level surface for subsequent processing steps.
The choice of fill material and the specific filling process depends on the requirements of the application, including thermal performance, cost, and compatibility with other manufacturing processes.
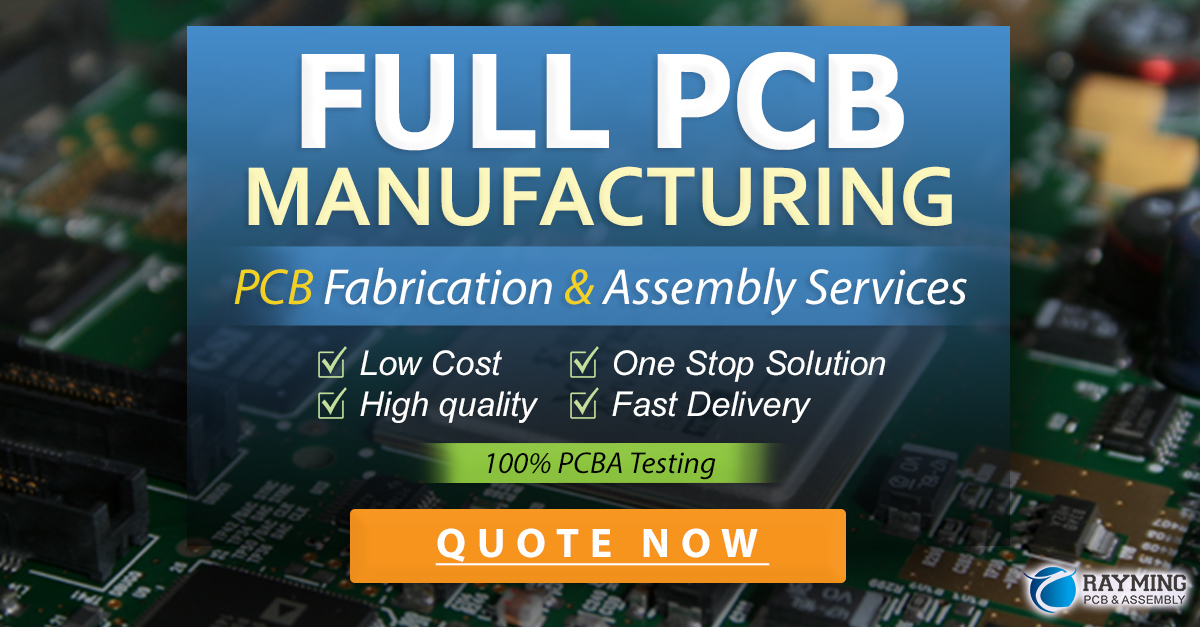
Applications of Thermal Vias
Thermal vias find application in a wide range of electronic devices, from consumer electronics to industrial and automotive systems. Some of the most common applications include:
Power Electronics
In power electronic applications, such as switched-mode power supplies, motor drives, and inverters, thermal vias are used to dissipate heat from high-power components, such as MOSFETs, IGBTs, and diodes. By effectively managing heat dissipation, thermal vias help to ensure the reliability and longevity of these critical components.
LED Lighting
LED lighting applications, particularly high-power LED arrays, generate significant amounts of heat that must be effectively dissipated to ensure optimal performance and longevity. Thermal vias are used to transfer heat from the LED package to the heat sink, maintaining the LED junction temperature within acceptable limits.
High-Performance Computing
In high-performance computing applications, such as servers, workstations, and gaming systems, thermal vias are used to dissipate heat from high-power processors, GPUs, and other components. By effectively managing heat dissipation, thermal vias help to ensure optimal performance and prevent thermal throttling or shutdown.
Automotive Electronics
Automotive electronics, such as engine control units, infotainment systems, and advanced driver assistance systems, are subject to harsh environmental conditions, including high temperatures and vibration. Thermal vias are used to dissipate heat from critical components, ensuring reliable operation in these demanding conditions.
Internet of Things (IoT) Devices
IoT devices, such as smart sensors, wearables, and connected appliances, often require compact, low-power designs. Thermal vias are used to effectively dissipate heat from power-dense components, such as processors and wireless modules, while maintaining a small form factor and low power consumption.
Frequently Asked Questions (FAQ)
1. What is the difference between a thermal via and a regular via?
A thermal via is specifically designed to transfer heat from one layer of a PCB to another, while a regular via is primarily used for electrical connectivity. Thermal vias are typically larger in diameter and may be filled with a conductive material to enhance heat transfer, while regular vias are smaller and may not be filled.
2. How do I determine the appropriate size and number of thermal vias for my application?
The appropriate size and number of thermal vias depends on several factors, including the amount of heat that needs to be dissipated, the thermal conductivity of the PCB material, and the specific design constraints of the application. Thermal simulation and modeling tools can be used to optimize the via design for a given application.
3. Can thermal vias be used in high-frequency applications?
Yes, thermal vias can be used in high-frequency applications, but careful design considerations must be made to minimize their impact on signal integrity. Strategies such as via shielding, ground plane stitching, and careful placement of thermal vias can help to mitigate the effects of thermal vias on high-frequency signals.
4. What are the most common fill materials for thermal vias?
The most common fill materials for thermal vias include copper, solder, and epoxy. Copper offers the highest thermal conductivity but can be more expensive and difficult to process. Solder provides a good balance of thermal conductivity and manufacturability, while epoxy offers a lower-cost option with moderate thermal performance.
5. How do I ensure the reliability of thermal vias in harsh environmental conditions?
To ensure the reliability of thermal vias in harsh environmental conditions, several strategies can be employed, including:
- Selecting PCB materials with high glass transition temperatures and low thermal expansion coefficients
- Using filled vias to improve mechanical stability and prevent via cracking or delamination
- Employing conformal coating or underfill materials to protect the vias from moisture and contaminants
- Conducting thorough testing and qualification to validate the performance and reliability of the thermal via design in the intended operating environment
Conclusion
Thermal vias are a critical component in the design and manufacture of PCBs for a wide range of electronic applications. By providing a low-resistance thermal path for heat dissipation, thermal vias help to ensure the performance, reliability, and longevity of electronic devices.
Effective thermal via design requires careful consideration of factors such as via size, placement, fill material, and density, as well as a thorough understanding of the specific requirements and constraints of the intended application. Through the use of advanced manufacturing processes, such as laser drilling, electroplating, and Via Filling, thermal vias can be fabricated to meet the demanding requirements of today’s electronic devices.
As electronic systems continue to push the boundaries of performance and power density, the importance of effective thermal management, and the role of thermal vias, will only continue to grow. By staying at the forefront of thermal via design and manufacturing technologies, engineers and manufacturers can ensure that the electronic devices of tomorrow are able to meet the ever-increasing demands of the market.
Leave a Reply