Introduction to Nickel-Gold Plating
Nickel-gold (Ni-Au) plating is a popular surface finish used in the electronics industry for printed circuit boards (PCBs) and other components. This combination of metals provides excellent solderability, electrical conductivity, and corrosion resistance. The nickel layer acts as a barrier to prevent the diffusion of copper from the substrate into the gold layer, while the gold layer provides a solderable and oxidation-resistant surface.
Advantages of Nickel-Gold Plating
Nickel-gold plating offers several advantages over other surface finishes:
- Excellent solderability
- High electrical conductivity
- Good corrosion resistance
- Compatibility with a wide range of soldering processes
- Durability and wear resistance
Applications of Nickel-Gold Plating
Nickel-gold plating is widely used in various industries, including:
- Electronics: PCBs, connectors, and components
- Aerospace: Connectors, switches, and sensors
- Automotive: Electrical connectors and sensors
- Medical: Implantable devices and surgical instruments
- Telecommunications: Connectors and switches
Traditional Nickel-Gold Plating Process
The traditional nickel-gold plating process involves several steps:
- Surface preparation: Cleaning and activation of the substrate surface
- Nickel plating: Electroless or electrolytic deposition of a nickel layer
- Gold plating: Electroless or electrolytic deposition of a gold layer
- Post-treatment: Rinsing and drying
Electroless Nickel Plating
Electroless nickel plating is a chemical process that deposits a nickel-phosphorus alloy on the substrate without the use of an external electrical current. The process involves the following steps:
- Cleaning: Removal of surface contaminants and oxides
- Activation: Creation of catalytic sites on the substrate surface
- Deposition: Immersion of the substrate in an electroless nickel plating solution containing nickel ions, reducing agents, and stabilizers
- Rinsing: Removal of excess plating solution and byproducts
Electroless nickel plating offers several advantages, such as uniform coating thickness, ability to plate complex shapes, and good corrosion resistance. However, it has limitations, such as slower deposition rates and higher material costs compared to electrolytic processes.
Electrolytic Nickel Plating
Electrolytic nickel plating involves the use of an external electrical current to deposit a nickel layer on the substrate. The process consists of the following steps:
- Cleaning: Removal of surface contaminants and oxides
- Activation: Creation of a conductive surface for electroplating
- Deposition: Immersion of the substrate in an electrolytic nickel plating solution containing nickel ions and application of an electrical current
- Rinsing: Removal of excess plating solution and byproducts
Electrolytic nickel plating offers faster deposition rates and lower material costs compared to electroless processes. However, it may result in non-uniform coating thickness on complex shapes and requires a conductive substrate.
Gold Plating
After the nickel layer is deposited, a thin layer of gold is plated onto the surface. Gold plating can be performed using either electroless or electrolytic processes, similar to nickel plating. The gold layer thickness typically ranges from 0.05 to 0.2 µm, depending on the application requirements.
Electroless gold plating is often preferred for its ability to produce uniform coatings on complex shapes and its compatibility with non-conductive substrates. Electrolytic gold plating, on the other hand, offers faster deposition rates and better control over the coating thickness.
Challenges with Traditional Nickel-Gold Plating
While traditional nickel-gold plating has been widely used in the electronics industry, it faces several challenges:
-
Porosity: The nickel layer may contain pores that allow the diffusion of copper from the substrate into the gold layer, leading to reduced solderability and corrosion resistance.
-
Black pad: The formation of a brittle nickel-phosphorus layer between the nickel and gold layers can cause solderjoint fractures, known as “black pad.”
-
Whisker growth: The growth of small, filamentary whiskers from the nickel layer can cause short circuits and reliability issues.
-
Environmental concerns: Traditional nickel-gold plating processes often use hazardous chemicals, such as cyanide-based gold plating solutions, which pose environmental and health risks.
-
Cost: The use of precious metals, such as gold, and the multi-step plating process contribute to the high cost of nickel-gold plating.
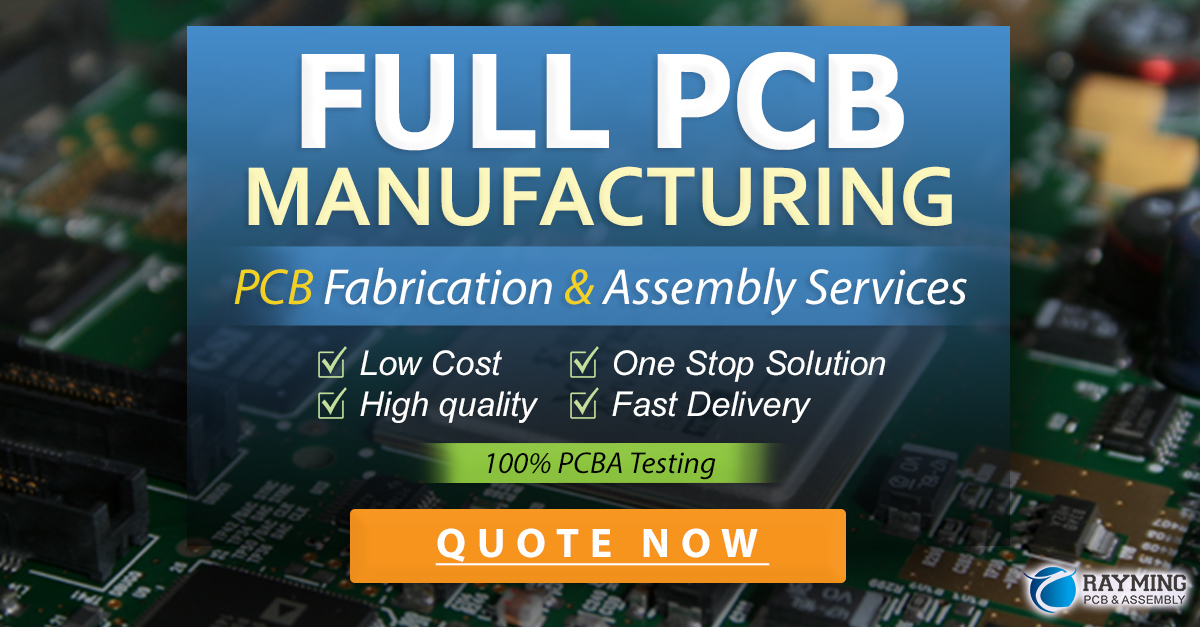
New Options for Chemical Nickel-Gold Surface Finish
To address the challenges associated with traditional nickel-gold plating, researchers and industry experts have developed new options for chemical nickel-gold surface finishes. These innovative approaches aim to improve the performance, reliability, and environmental sustainability of nickel-gold plating.
Electroless Nickel/Electroless Palladium/Immersion Gold (ENEPIG)
ENEPIG is a multi-layer surface finish that consists of an electroless nickel layer, followed by an electroless palladium layer, and finally an immersion gold layer. This combination offers several advantages over traditional nickel-gold plating:
-
Improved solderability: The palladium layer acts as a barrier to prevent the diffusion of nickel into the gold layer, maintaining excellent solderability.
-
Reduced risk of black pad: The palladium layer prevents the formation of a brittle nickel-phosphorus layer, minimizing the risk of black pad.
-
Better wire bonding performance: The palladium layer provides a suitable surface for wire bonding, improving the reliability of wire-bonded connections.
-
Compatibility with lead-free soldering: ENEPIG is compatible with lead-free soldering processes, meeting the requirements of RoHS regulations.
Layer | Thickness (µm) | Function |
---|---|---|
Immersion Gold | 0.05-0.2 | Provides solderability and oxidation resistance |
Electroless Palladium | 0.05-0.3 | Acts as a barrier layer and improves wire bonding |
Electroless Nickel | 3-6 | Provides a diffusion barrier and improves corrosion resistance |
Electroless Nickel/Immersion Silver/Immersion Gold (ENISIG)
ENISIG is another multi-layer surface finish that replaces the palladium layer in ENEPIG with an immersion silver layer. This combination offers some unique advantages:
-
Cost-effectiveness: Silver is less expensive than palladium, making ENISIG a more cost-effective option compared to ENEPIG.
-
Good solderability: The immersion silver layer provides excellent solderability and is compatible with both lead-free and tin-lead soldering processes.
-
Improved adhesion: The immersion silver layer enhances the adhesion between the nickel and gold layers, reducing the risk of delamination.
-
Anti-tarnish properties: The immersion silver layer helps prevent the tarnishing of the surface finish, maintaining its appearance and solderability over time.
Layer | Thickness (µm) | Function |
---|---|---|
Immersion Gold | 0.05-0.2 | Provides solderability and oxidation resistance |
Immersion Silver | 0.05-0.3 | Enhances adhesion and provides anti-tarnish properties |
Electroless Nickel | 3-6 | Provides a diffusion barrier and improves corrosion resistance |
Electroless Nickel/Electroless Palladium/Autocatalytic Gold (ENPAG)
ENPAG is a variation of ENEPIG that replaces the immersion gold layer with an autocatalytic gold layer. Autocatalytic gold plating is a self-catalyzing process that allows for the deposition of thicker gold layers without the need for an external reducing agent. This process offers several benefits:
-
Improved wire bonding: The thicker autocatalytic gold layer provides a better surface for wire bonding, ensuring reliable connections.
-
Enhanced durability: The thicker gold layer offers better wear resistance and durability, making it suitable for applications that require frequent mating and unmating of connectors.
-
Compatibility with high-frequency applications: The autocatalytic gold layer provides a smooth, low-porosity surface that is ideal for high-frequency applications.
-
Reduced process complexity: The autocatalytic gold plating process eliminates the need for a separate reducing agent, simplifying the plating process and reducing costs.
Layer | Thickness (µm) | Function |
---|---|---|
Autocatalytic Gold | 0.5-2.0 | Provides a thicker gold layer for improved wire bonding and durability |
Electroless Palladium | 0.05-0.3 | Acts as a barrier layer and improves wire bonding |
Electroless Nickel | 3-6 | Provides a diffusion barrier and improves corrosion resistance |
Electroless Nickel/Immersion Silver/Electroless Gold (ENISEG)
ENISEG is a hybrid surface finish that combines the advantages of ENISIG and electroless gold plating. This combination offers the following benefits:
-
Excellent solderability: The immersion silver layer provides excellent solderability, while the electroless gold layer protects the silver from oxidation and tarnishing.
-
Improved wire bonding: The electroless gold layer offers a suitable surface for wire bonding, ensuring reliable connections.
-
Cost-effectiveness: The use of an immersion silver layer instead of palladium reduces the overall cost of the surface finish.
-
Compatibility with high-frequency applications: The electroless gold layer provides a smooth, low-porosity surface that is ideal for high-frequency applications.
Layer | Thickness (µm) | Function |
---|---|---|
Electroless Gold | 0.05-0.2 | Protects the silver layer from oxidation and provides a surface for wire bonding |
Immersion Silver | 0.05-0.3 | Enhances adhesion and provides anti-tarnish properties |
Electroless Nickel | 3-6 | Provides a diffusion barrier and improves corrosion resistance |
Environmental Considerations
As the electronics industry becomes increasingly focused on environmental sustainability, new options for chemical nickel-gold surface finishes must also address environmental concerns. Some of the key environmental considerations include:
-
Reduction of hazardous substances: New surface finishes should minimize the use of hazardous chemicals, such as cyanide-based gold plating solutions, and replace them with more environmentally friendly alternatives.
-
Waste management: Plating processes generate waste streams that must be properly treated and disposed of to prevent environmental contamination. New surface finishes should aim to reduce waste generation and facilitate easier waste management.
-
Energy efficiency: Plating processes consume significant amounts of energy. New surface finishes should strive to improve energy efficiency by optimizing process parameters and using energy-efficient equipment.
-
Recyclability: The use of precious metals, such as gold, in surface finishes makes recycling an important consideration. New surface finishes should be designed to facilitate the recovery and recycling of precious metals from end-of-life products.
Conclusion
New options for chemical nickel-gold surface finishes offer significant advantages over traditional nickel-gold plating, addressing challenges such as porosity, black pad, whisker growth, and environmental concerns. ENEPIG, ENISIG, ENPAG, and ENISEG are promising alternatives that provide improved solderability, wire bonding performance, and durability while reducing costs and environmental impact.
As the electronics industry continues to evolve, the development and adoption of new surface finish technologies will be critical to meeting the ever-increasing demands for performance, reliability, and sustainability. By embracing innovative approaches to chemical nickel-gold plating, manufacturers can stay ahead of the curve and deliver products that meet the highest standards of quality and environmental responsibility.
Frequently Asked Questions (FAQ)
- What is the main advantage of ENEPIG over traditional nickel-gold plating?
-
ENEPIG offers improved solderability and reduced risk of black pad formation due to the presence of the palladium layer, which acts as a barrier between the nickel and gold layers.
-
How does ENISIG differ from ENEPIG?
-
ENISIG replaces the palladium layer in ENEPIG with an immersion silver layer, making it a more cost-effective option while providing good solderability and improved adhesion between the nickel and gold layers.
-
What are the benefits of using an autocatalytic gold layer in ENPAG?
-
The autocatalytic gold layer in ENPAG allows for the deposition of thicker gold layers, improving wire bonding performance and durability. It also simplifies the plating process by eliminating the need for a separate reducing agent.
-
Why is environmental sustainability an important consideration for new nickel-gold surface finishes?
-
As the electronics industry becomes more focused on environmental responsibility, new surface finishes must address concerns such as the reduction of hazardous substances, waste management, energy efficiency, and recyclability to minimize their environmental impact.
-
How can manufacturers stay ahead of the curve in adopting new nickel-gold surface finish technologies?
- Manufacturers can stay ahead of the curve by actively researching and evaluating new surface finish options, collaborating with suppliers and industry experts, and investing in the development and implementation of innovative plating processes that meet the evolving needs of the electronics industry.
Leave a Reply