What is a PCB?
A PCB, or printed circuit board, is the foundation of nearly all modern electronic devices. It is a flat board made of insulating materials like fiberglass, with conductive copper traces printed on the surface to connect electronic components. Components like resistors, capacitors, and integrated circuits are soldered onto the PCB to create a functional electronic circuit.
PCBs provide a compact, reliable way to assemble complex electronics. They eliminate the need for point-to-point wiring, allow for automated assembly, and provide mechanical support for components. PCBs can be single-sided (with traces on one side), double-sided, or multi-layer with traces sandwiched between insulating layers.
Common PCB Applications
PCBs are used in virtually all electronic products today, from simple toys to advanced aerospace systems. Some common applications include:
- Consumer electronics (smartphones, computers, TVs, etc.)
- Industrial control systems
- Medical devices
- Automotive electronics
- Telecommunications equipment
- Military and aerospace systems
PCB Manufacturing Process Overview
The PCB manufacturing process turns a circuit design into a physical board ready for assembly. While the exact process can vary depending on the PCB type and manufacturer, it generally follows these key steps:
- Design: Creating the schematic and PCB layout files
- Fabrication: Manufacturing the bare circuit board
- Assembly: Soldering components onto the fabricated PCB
- Testing and Inspection: Verifying functionality and quality
Let’s explore each of these steps in more detail.
PCB Design
Schematic Capture
The first step in creating a PCB is designing the schematic – a symbolic representation of the circuit. Engineers use electronic design automation (EDA) software to draw the schematic, specifying components and their connections.
The schematic defines the circuit functionality without regard for the physical layout. It’s important to choose the right components, verify the design through simulation, and check for errors before proceeding.
PCB Layout
With the schematic complete, the next step is to create the PCB layout. This involves arranging components on the board and routing the copper traces to connect them according to the schematic.
PCB layout is a complex process that requires balancing many factors:
- Component placement for optimal signal integrity and manufacturability
- Trace routing to minimize cross-talk and electromagnetic interference (EMI)
- Power and ground plane design for reliable power distribution
- Design rule adherence for successful fabrication (trace width/spacing, hole sizes, etc.)
Designers use EDA tools with rule-checking features to verify the layout meets manufacturing constraints. The output is a set of Gerber files that define the copper patterns, drill holes, and other features needed for fabrication.
PCB Stackup
For multi-layer PCBs, the stackup defines the arrangement of copper and insulating layers. A typical 4-layer stackup might include:
Layer | Description |
---|---|
Top | Components and signals |
Ground | Dedicated ground plane |
Power | Dedicated power plane |
Bottom | Components and signals |
The stackup is a key factor in signal integrity. Designers must carefully choose the layer arrangement, materials, and thicknesses to control impedance and cross-talk.
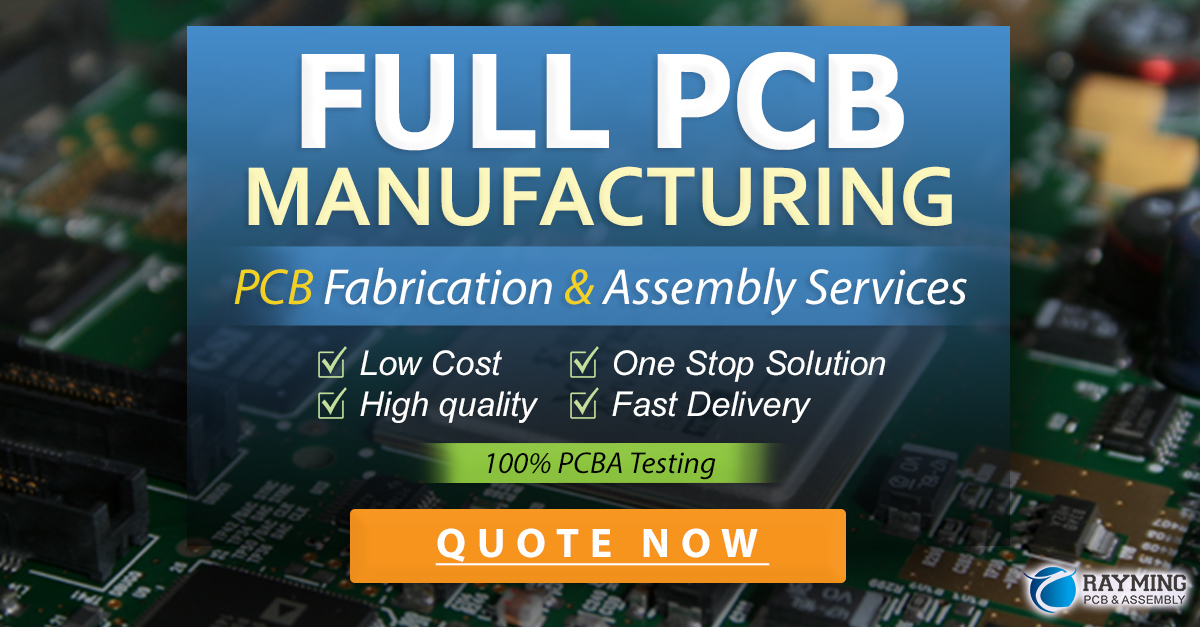
PCB Fabrication
With the design complete, the PCB is ready for fabrication. The fabrication process creates the bare board according to the Gerber files.
Material Preparation
PCBs start as a laminate material, typically FR-4, made of fiberglass cloth impregnated with epoxy resin. Copper foil is bonded to one or both sides of the core laminate. For multi-layer boards, additional prepreg layers (uncured epoxy and glass) and copper foil are stacked and bonded in a lamination press under high temperature and pressure.
Drilling
Holes are drilled through the PCB material to accommodate through-hole components and vias that connect traces on different layers. CNC machines drill the holes according to the drill file from the PCB design data. The holes are then cleaned and deburred.
Patterning
The copper traces are formed through a photolithography and etching process:
- The copper surface is cleaned and a photoresist layer is applied
- The photoresist is exposed through a phototool (mask) that defines the trace pattern
- The photoresist is developed, hardening the exposed areas
- The unhardened photoresist is stripped away, exposing the underlying copper
- The exposed copper is etched away in a chemical bath, leaving only the trace pattern
- The remaining photoresist is removed, revealing the final copper pattern
This process is repeated for each copper layer in the stackup. For double-sided and multi-layer boards, careful alignment is needed to ensure the layers match up.
Plating
The drilled holes are made conductive and traces are protected through electroplating:
- A thin layer of copper is electroless-plated onto the hole walls to make them conductive
- Additional copper is electroplated to the desired thickness to connect traces on different layers
- A thin layer of tin is plated to protect the exposed copper from oxidation
Soldermask Application
A soldermask layer is applied to protect the copper traces and prevent solder bridges during assembly. The soldermask is a polymer ink that is silkscreened onto the board and cured. Openings are left in the soldermask at component pads and vias where soldering will occur.
Silkscreen
A silkscreen legend is printed onto the soldermask to label components, E-Test-points-of-a-pcb/”>test points, and other features. This makes the PCB easier to assemble and debug. The silkscreen ink is usually white but other colors are available.
Surface Finish
A surface finish is applied to the exposed copper pads to protect them from oxidation and enhance solderability. Common finishes include:
- HASL (Hot Air Solder Leveling): A tin-lead alloy is applied and leveled with hot air
- ENIG (Electroless Nickel Immersion Gold): A layer of nickel is plated, followed by a thin layer of gold
- OSP (Organic Solderability Preservative): An organic compound is applied to protect the copper
The choice of surface finish depends on the components to be assembled, environmental requirements, and cost.
Profiling
The fabricated PCB panels are routed or scored to separate the individual boards. A CNC machine cuts the panel according to the board outline defined in the design files. V-score lines may be used to allow the boards to be snapped apart by hand.
Electrical Test
The bare boards undergo electrical testing to verify continuity and check for short circuits. Automated test equipment probes each net to ensure it matches the netlist from the design files. Boards that fail are diagnosed and reworked or scrapped.
With fabrication complete, the PCBs are packaged and shipped to the assembly house to have components soldered. The fabrication process is highly automated, allowing thousands of boards to be produced quickly and consistently.
PCB Assembly
PCB assembly involves soldering components onto the fabricated board. The main steps are:
- Solder Paste Application: Solder paste (a mixture of tiny solder balls and flux) is applied to the component pads through a stencil.
- Component Placement: SMT Components are placed onto the solder paste by robotic pick-and-place machines.
- Reflow Soldering: The board is passed through an oven that melts the solder paste, bonding the components to the pads.
- Through-Hole Assembly: Any through-hole components are inserted and soldered by hand or with wave soldering.
- Inspection and Test: The assembled boards are visually inspected and electrically tested to ensure proper function.
Automated optical inspection (AOI) systems check for missing components, incorrect polarity, and solder defects. Functional testing verifies that the board operates as intended in the final application.
PCB Testing and Inspection
Thorough testing and inspection are critical to delivering high-quality PCBs. Some key quality assurance steps include:
- Flying Probe Test: An in-circuit test that probes each net to verify continuity and isolation
- Boundary Scan Test: A functional test that uses built-in test circuitry (JTAG) to test component interconnects
- X-ray Inspection: Used to check solder joints and internal traces for defects
- Thermal Cycling: Exposes boards to alternating high and low temperatures to check for defects caused by thermal stress
- Burn-In Testing: Operates boards at elevated temperature and voltage to identify infant mortality failures
Boards that pass all inspections and tests are packaged and shipped to the customer. Traceability data is maintained throughout the manufacturing process to enable tracking and failure analysis.
Choosing a PCB Manufacturer
Selecting the right PCB manufacturer is key to ensuring a successful project. Some important factors to consider:
- Technical Capabilities: Can they handle your PCB complexity, layer count, materials, and surface finishes?
- Quality Systems: Do they have certified quality management systems (ISO 9001, AS9100, etc.)?
- Experience: Do they have experience with your industry and application type?
- Capacity and Lead Time: Can they meet your volume and delivery requirements?
- Communication: Do they respond quickly and clearly to inquiries and provide regular project updates?
- Cost: Are their prices competitive for the quality and service level provided?
It’s also wise to consider the location of the manufacturer. Offshore factories may offer lower costs but can introduce risks around communication, intellectual property, and logistics. Domestic manufacturers provide easier collaboration and faster turnaround times.
Get quotes and capabilities from multiple manufacturers to find the best fit for your needs. Building a strong relationship with your PCB supplier can streamline future projects.
PCB Design Best Practices
Designing a manufacturable, reliable PCB requires following industry best practices:
- Adhere to the manufacturer’s design rules for minimum trace width/spacing, hole sizes, annular rings, etc.
- Use a consistent grid size and place components orthogonally to simplify placement and routing
- Minimize the number of layer transitions and use vias strategically to simplify routing
- Provide adequate clearance between components and traces to avoid short circuits
- Use copper pours for power and ground to improve current carrying capacity and reduce EMI
- Minimize trace lengths and loops to reduce EMI and cross-talk
- Terminate high-speed traces properly to ensure signal integrity
- Place decoupling capacitors close to ICs to suppress power supply noise
- Use thermal reliefs and large pads on high-current traces to improve soldering and heat dissipation
- Panelize boards efficiently to maximize material usage and minimize tooling costs
Following these guidelines and collaborating closely with your manufacturer will help you create PCBs that are easier to fabricate, assemble, and test, reducing costs and time to market.
FAQ
What is the typical turnaround time for PCB manufacturing?
Turnaround times vary depending on the complexity of the board and the manufacturer’s workload. Simple 2-layer boards can often be fabricated in 1-2 days, while complex multi-layer boards may take a week or more. Assembly typically adds another 1-2 weeks. Rush services are available at additional cost.
What file formats are needed for PCB fabrication and assembly?
The most common file format for PCB fabrication is RS-274X Gerber, which defines the copper patterns, drill holes, and other features. Assembly requires a pick-and-place file (usually CSV or ASCII format) that specifies the component locations and rotations, and a bill of materials (BOM) that lists the part numbers and quantities.
What are the most common PCB Surface Finishes?
The most common surface finishes are HASL (hot air solder leveling), ENIG (electroless nickel immersion gold), and OSP (organic solderability preservative). HASL is the most economical but can result in uneven surfaces. ENIG provides excellent solderability and flatness but is more expensive. OSP is a good compromise for low-cost, lead-free assemblies.
How much do PCBs cost?
PCB costs depend on many factors, including the number of layers, size, quantity, materials, and surface finish. Simple 2-layer boards in small quantities may cost $10-20 each, while large, complex boards can cost hundreds of dollars each. Higher volumes provide significant cost savings due to economies of scale. Get quotes from multiple manufacturers to compare pricing.
What are the most common reasons for PCB failure?
PCBs can fail for many reasons, including design errors, manufacturing defects, assembly issues, and environmental stresses. Some common failure modes include:
- Short circuits caused by insufficient clearance or solder bridging
- Open circuits caused by broken traces or cold solder joints
- Component failures caused by overstress, overheating, or electrostatic discharge
- Delamination or cracking caused by thermal cycling or physical stress
Careful design, thorough testing, and robust manufacturing processes can minimize the risk of PCB failures in the field.
Conclusion
PCBs are essential to modern electronics, providing a reliable and efficient means of interconnecting components. The PCB manufacturing process involves many steps, from design through fabrication, assembly, and testing. By understanding the process and collaborating closely with experienced manufacturers, you can create high-quality PCBs that meet your performance, reliability, and cost targets.
To recap, the key steps in PCB manufacturing are:
- Design: Creating the schematic and layout files that define the circuit
- Fabrication: Manufacturing the bare board according to the design files
- Assembly: Soldering components onto the fabricated board
- Testing and Inspection: Verifying the assembled board meets functional and quality requirements
By following best practices in PCB design and partnering with a reputable manufacturer, you can streamline the manufacturing process and bring your electronic products to market quickly and successfully. As PCB technology continues to evolve, staying up-to-date on the latest manufacturing capabilities and design techniques will be key to staying competitive in the fast-paced world of electronics.
Leave a Reply