Introduction to Selective Soldering
Selective soldering is a process used in printed circuit board (PCB) assembly where specific components are soldered onto the board without affecting nearby components. This technique allows for precise soldering of selected components while leaving heat-sensitive or pre-assembled components intact. Selective soldering offers several advantages over traditional wave soldering and reflow soldering methods, making it an increasingly popular choice for PCB manufacturing.
Key Benefits of Selective Soldering
- Targeted soldering of specific components
- Avoids damage to heat-sensitive components
- Allows for soldering of pre-assembled components
- Reduces thermal stress on PCB
- Enables soldering of complex board designs
- Improves solder joint quality and reliability
Selective Soldering Process Overview
The selective soldering process involves several key steps to ensure accurate and reliable soldering of selected components onto the PCB. Here’s an overview of the typical selective soldering process:
Step 1: PCB Preparation
- The PCB is designed with designated areas for selective soldering
- Solder mask is applied to protect areas not to be soldered
- Solder paste is applied to the selected component pads
Step 2: Component Placement
- Selected components are placed onto the PCB using pick-and-place machines or manually
- Components are held in place by the solder paste
Step 3: Flux Application
- Liquid flux is applied to the component leads and pads to improve solder wetting and prevent oxidation
Step 4: Preheating
- The PCB is preheated to activate the flux and prepare the board for soldering
- Preheating helps prevent thermal shock and improves solder joint quality
Step 5: Selective Soldering
- A precisely controlled solder nozzle applies molten solder to the selected component leads and pads
- The solder nozzle is guided by a programmed path to ensure accurate soldering
- Nitrogen gas is often used to create an inert atmosphere and prevent oxidation
Step 6: Cooling and Cleaning
- The PCB is cooled to allow the solder joints to solidify
- Any excess flux residue is cleaned from the board using appropriate cleaning agents
Selective Soldering Equipment and Technologies
Various types of selective soldering equipment and technologies are available to suit different PCB Assembly requirements. Some common selective soldering systems include:
Laser Selective Soldering
- Uses a focused laser beam to heat and solder specific components
- Offers high precision and speed
- Suitable for soldering small, delicate components
Mini-Wave Selective Soldering
- Employs a miniature wave solder nozzle to apply solder to selected areas
- Provides good solder joint quality and throughput
- Ideal for soldering through-hole components and connectors
Robotic Selective Soldering
- Utilizes a Robotic Arm equipped with a solder nozzle
- Offers flexibility and programmability for complex soldering paths
- Suitable for high-mix, low-volume production
Selective Soldering System | Key Features | Typical Applications |
---|---|---|
Laser Selective Soldering | High precision, fast speed | Small, delicate components |
Mini-Wave Selective Soldering | Good solder joint quality, high throughput | Through-hole components, connectors |
Robotic Selective Soldering | Flexible, programmable | High-mix, low-volume production |
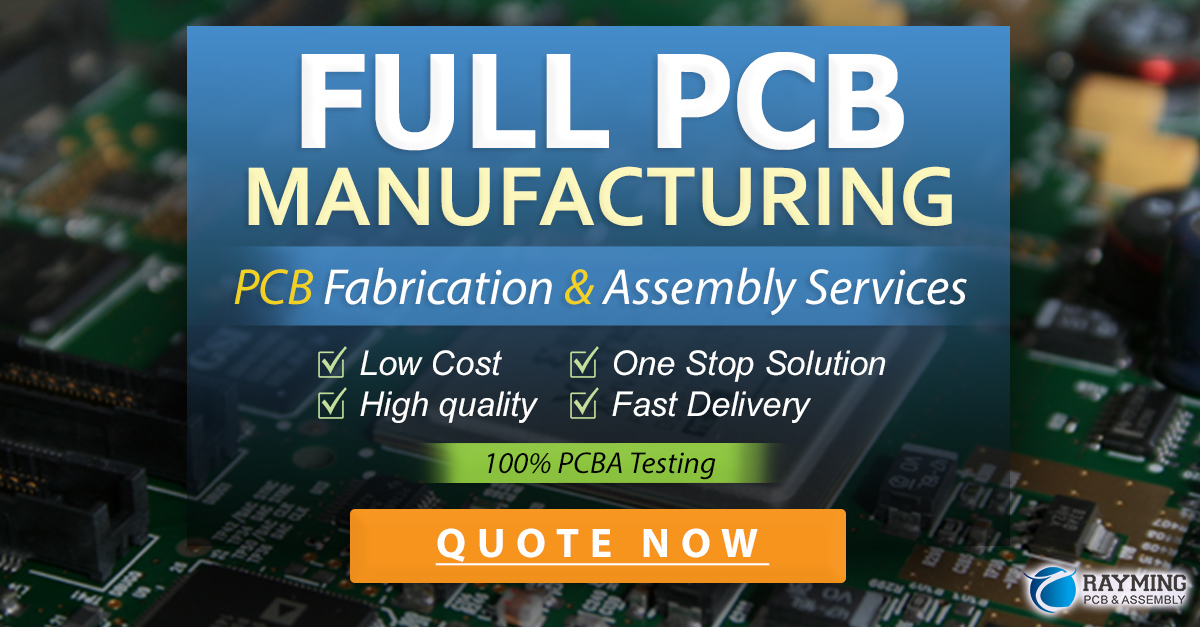
Process Control and Optimization
To ensure consistent and reliable selective soldering results, several process control and optimization techniques are employed:
Temperature Control
- Precise control of solder nozzle temperature is crucial for achieving optimal solder joint quality
- Temperature profiling and monitoring systems are used to maintain the desired temperature range
Flux Management
- Proper application and control of flux are essential for good solder wetting and preventing defects
- Automated flux dispensing systems ensure consistent flux application
- Regular maintenance and cleaning of flux dispensers are necessary
Nozzle Selection and Maintenance
- Selecting the appropriate solder nozzle size and shape is important for accurate soldering
- Regular cleaning and maintenance of solder nozzles prevent clogging and ensure consistent solder flow
Nitrogen Inerting
- Using nitrogen gas to create an inert atmosphere during soldering helps prevent oxidation and improve solder joint quality
- Nitrogen flow rate and purity should be controlled and monitored
Process Monitoring and Inspection
- In-line process monitoring systems, such as cameras and sensors, are used to detect any soldering defects or anomalies in real-time
- Post-soldering visual inspection and electrical testing ensure the quality and functionality of the soldered components
Selective Soldering Defects and Troubleshooting
Despite the advantages of selective soldering, various defects can occur during the process. Some common selective soldering defects include:
Bridging
- Solder bridges form between adjacent component leads or pads
- Causes: Excessive solder, incorrect nozzle size, poor nozzle alignment
Insufficient Solder Joint
- Solder joints are incomplete or have inadequate solder volume
- Causes: Insufficient solder, low solder temperature, poor flux activation
Cold Solder Joint
- Solder joints appear dull, rough, or cracked due to improper solder wetting
- Causes: Low solder temperature, contaminated surfaces, inadequate flux
Flux Residue
- Excess flux remains on the PCB after soldering, potentially causing corrosion or contamination
- Causes: Excessive flux application, inadequate cleaning process
To troubleshoot and prevent selective soldering defects:
– Optimize process parameters (temperature, nozzle size, flux amount)
– Ensure proper nozzle alignment and programming
– Maintain clean and contamination-free surfaces
– Implement effective cleaning processes
– Conduct regular equipment maintenance and calibration
Selective Soldering Standards and Quality Control
Selective soldering processes are guided by various industry standards and quality control measures to ensure consistent and reliable results:
IPC Standards
- IPC-A-610: Acceptability of Electronic Assemblies
- IPC-J-STD-001: Requirements for Soldered Electrical and Electronic Assemblies
- IPC-7711/7721: Rework, Modification, and Repair of Electronic Assemblies
Quality Control Measures
- Visual inspection: Microscopic examination of solder joints for defects
- X-ray inspection: Non-destructive analysis of solder joint quality and voids
- Electrical testing: Continuity and functionality testing of soldered components
- Thermal cycling: Assessing solder joint reliability under temperature stress
- Cross-sectioning: Destructive analysis of solder joint microstructure and intermetallic formation
Implementing and adhering to these standards and quality control measures help ensure the production of high-quality, reliable PCB assemblies using selective soldering processes.
Future Trends in Selective Soldering
As PCB designs continue to evolve and become more complex, selective soldering technologies are advancing to meet new challenges:
Miniaturization
- Increasing demand for smaller, more compact electronic devices drives the need for precise selective soldering of miniaturized components
Automation and Robotics
- Continued development of automated and robotic selective soldering systems for improved efficiency, flexibility, and consistency
Inline Process Control
- Integration of real-time process monitoring, data analytics, and machine learning for enhanced process control and optimization
Sustainable Soldering
- Adoption of lead-free solders and environmentally friendly flux formulations to comply with RoHS and REACH regulations
By embracing these emerging trends, the selective soldering industry can stay at the forefront of PCB assembly technology and meet the ever-changing demands of the electronics manufacturing sector.
Frequently Asked Questions (FAQ)
- What are the advantages of selective soldering over traditional soldering methods?
-
Selective soldering allows for targeted soldering of specific components without affecting nearby components. It reduces thermal stress on the PCB, enables soldering of pre-assembled components, and improves solder joint quality and reliability.
-
How does selective soldering differ from wave soldering?
-
Wave soldering involves passing the entire PCB over a wave of molten solder, soldering all components simultaneously. Selective soldering, on the other hand, applies solder only to selected components using a precisely controlled solder nozzle, leaving other components unaffected.
-
What types of components are typically soldered using selective soldering?
-
Selective soldering is commonly used for through-hole components, connectors, and other components that cannot withstand the high temperatures of reflow soldering. It is also suitable for soldering components onto boards with heat-sensitive or pre-assembled components.
-
How does flux application work in the selective soldering process?
-
Liquid flux is applied to the component leads and pads prior to soldering. The flux helps remove oxides, improves solder wetting, and prevents oxidation during the soldering process. Automated flux dispensing systems ensure consistent and precise flux application.
-
What are some common defects that can occur in selective soldering, and how can they be prevented?
- Common selective soldering defects include bridging, insufficient solder joints, cold solder joints, and flux residue. These defects can be prevented by optimizing process parameters, ensuring proper nozzle alignment and programming, maintaining clean surfaces, implementing effective cleaning processes, and conducting regular equipment maintenance and calibration.
Conclusion
Selective soldering has revolutionized the PCB assembly process, offering a precise and efficient method for soldering specific components without compromising the integrity of nearby components. By understanding the technical details, process control measures, and quality standards involved in selective soldering, manufacturers can produce high-quality, reliable PCB assemblies that meet the demanding requirements of modern electronics. As the industry continues to evolve, staying informed about the latest selective soldering technologies and trends is essential for staying competitive in the ever-changing landscape of PCB manufacturing.
Leave a Reply