Introduction to Robotic Arms
A robotic arm, also known as a mechanical arm or a manipulator, is a programmable mechanical device designed to mimic the functions and movements of a human arm. Robotic arms are widely used in various industries, including manufacturing, assembly lines, welding, and space exploration. They offer precision, speed, and the ability to perform repetitive tasks tirelessly, making them invaluable in many applications.
In this article, we will guide you through the process of building your own robotic arm project, covering the fundamental concepts, necessary components, and step-by-step instructions.
Table of Contents
- Understanding the Basics of Robotic Arms
- Essential Components for Building a Robotic Arm
- Designing Your Robotic Arm
- Assembling the Mechanical Structure
- Wiring and Electronics
- Programming the Robotic Arm
- Testing and Calibrating the Robotic Arm
- Advanced Features and Enhancements
- Troubleshooting Common Issues
- Applications and Future of Robotic Arms
- Frequently Asked Questions (FAQ)
Understanding the Basics of Robotic Arms
Before diving into the project, it’s essential to understand the basic concepts and terminology related to robotic arms.
Degrees of Freedom (DOF)
Degrees of Freedom (DOF) refers to the number of independent motions a robotic arm can perform. Each joint in the arm contributes to the overall DOF. A typical industrial robotic arm has six DOF, allowing it to move in three-dimensional space and orient its end effector (tool) in various positions.
Types of Robotic Arms
There are several types of robotic arms, each with its unique configuration and application:
Type | Description | Applications |
---|---|---|
Cartesian | Linear motion along X, Y, and Z axes | 3D printing, CNC machines |
Cylindrical | Combination of linear and rotary motion | Welding, assembly lines |
Spherical | Two rotary joints and one linear joint | Handling materials, painting |
Articulated | Multiple rotary joints, resembling a human arm | Versatile applications, industrial tasks |
SCARA | Selective Compliance Assembly Robot Arm | Pick and place, assembly |
Delta | Parallel linkage, high-speed operation | Packaging, food industry |
Kinematics
Kinematics is the study of motion without considering the forces that cause it. In the context of robotic arms, kinematics deals with the relationship between the joint angles and the position and orientation of the end effector. There are two main types of kinematics:
- Forward Kinematics: Calculating the position and orientation of the end effector based on the known joint angles.
- Inverse Kinematics: Determining the joint angles required to achieve a desired position and orientation of the end effector.
Essential Components for Building a Robotic Arm
To build a robotic arm, you’ll need the following components:
- Mechanical Structure
- Links: The rigid segments that make up the arm.
- Joints: The connections between the links, allowing for motion.
-
End Effector: The tool or device attached to the end of the arm, such as a gripper or a sensor.
-
Actuators
- Motors: Electric motors, such as DC motors or stepper motors, provide the necessary torque and speed to move the arm.
-
Servos: Specialized motors with built-in feedback control, commonly used in smaller robotic arms.
-
Control System
- Microcontroller: A programmable device, such as an Arduino or Raspberry Pi, that processes inputs and controls the actuators.
-
Motor Drivers: Electronic components that interface between the microcontroller and the motors, providing the necessary power and control signals.
-
Sensors
- Encoders: Sensors that measure the rotation or position of the joints, enabling precise control and feedback.
-
Limit Switches: Sensors that detect the end positions of the joints, preventing overextension or collisions.
-
Power Supply
-
Batteries or AC/DC power adapters to provide the necessary voltage and current for the motors and electronics.
-
Wiring and Connectors
- Breadboards, jumper wires, and connectors for prototyping and connecting the components.
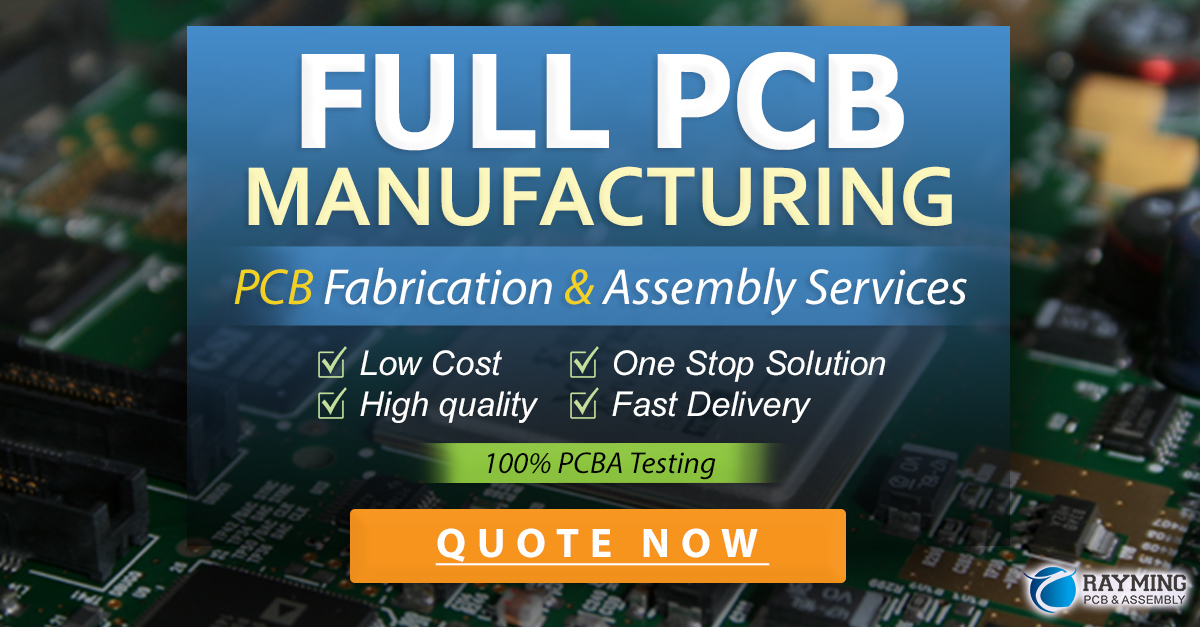
Designing Your Robotic Arm
Before building your robotic arm, it’s crucial to design and plan the mechanical structure, considering factors such as the desired DOF, load capacity, and workspace.
Mechanical Design
- Determine the number of joints and links required for your specific application.
- Consider the length and material of each link, ensuring sufficient strength and rigidity.
- Design the joints, choosing appropriate types (e.g., revolute, prismatic) and their range of motion.
- Select suitable actuators (motors or servos) based on the required torque and speed.
- Incorporate mounting points for the actuators, sensors, and end effector.
CAD Modeling
Using computer-aided design (CAD) software, create a 3D model of your robotic arm. This allows you to visualize the design, check for interferences, and make necessary adjustments before physically building the arm. Popular CAD software options include:
- SolidWorks
- Autodesk Fusion 360
- FreeCAD
- OpenSCAD
3D Printing or Machining
Once you have finalized the design, you can fabricate the mechanical components using 3D printing or traditional machining methods. 3D printing offers rapid prototyping and customization, while machining provides higher strength and precision for more demanding applications.
Assembling the Mechanical Structure
With the designed components ready, it’s time to assemble the mechanical structure of your robotic arm.
- Start by assembling the base, ensuring it is sturdy and level.
- Attach the first link to the base, using appropriate bearings or bushings to allow smooth rotation.
- Continue assembling the subsequent links and joints, following your design.
- Mount the actuators (motors or servos) at the designated locations, using brackets or mounts.
- Install any additional components, such as the end effector or sensors.
- Secure all the fasteners and check for proper alignment and smooth motion of the joints.
Wiring and Electronics
Once the mechanical structure is assembled, it’s time to focus on the wiring and electronics.
- Connect the motor drivers to the microcontroller, following the manufacturer’s guidelines.
- Wire the motors or servos to the motor drivers, ensuring correct polarity and connection.
- Connect any sensors, such as encoders or limit switches, to the microcontroller’s input pins.
- Set up the power supply, providing the necessary voltage and current for the motors and electronics.
- Use breadboards and jumper wires for prototyping and testing the connections.
- Double-check all the wiring and connections to ensure they are secure and correctly connected.
Programming the Robotic Arm
With the hardware setup complete, it’s time to program your robotic arm to perform the desired movements and tasks.
Inverse Kinematics
Implement inverse kinematics algorithms to calculate the necessary joint angles for reaching a specific position and orientation of the end effector. There are several approaches to solving inverse kinematics, such as:
- Analytical Methods: Using geometric and trigonometric equations to calculate joint angles.
- Numerical Methods: Iterative techniques, such as the Jacobian inverse method or the cyclic coordinate descent (CCD) algorithm.
- Machine Learning: Training neural networks to learn the inverse kinematics mapping.
Motion Planning
Develop motion planning algorithms to generate smooth and efficient trajectories for the robotic arm. Consider factors such as obstacle avoidance, joint limits, and singularities. Some common motion planning techniques include:
- Point-to-Point Motion: Moving the end effector from one position to another in a straight line.
- Interpolation: Generating intermediate points between the start and end positions to create a smooth trajectory.
- Path Planning: Finding an optimal path from the start to the end position while avoiding obstacles.
Control Algorithms
Implement control algorithms to ensure accurate and stable motion of the robotic arm. Some popular control techniques include:
- PID Control: Proportional-Integral-Derivative control, which adjusts the motor outputs based on the error between the desired and actual positions.
- Feedforward Control: Calculating the required motor outputs based on the desired trajectory and the system’s dynamics.
- Adaptive Control: Adjusting the control parameters in real-time to compensate for changes in the system or environment.
Programming Languages and Libraries
Choose a suitable programming language and libraries for your robotic arm project. Some popular options include:
- Arduino: Using the Arduino IDE and libraries for microcontroller programming.
- Python: Utilizing libraries such as ROS (Robot Operating System) or PySerial for high-level control and communication.
- C/C++: For low-level programming and optimization.
- MATLAB/Simulink: For simulation, modeling, and control design.
Testing and Calibrating the Robotic Arm
After programming your robotic arm, it’s essential to thoroughly test and calibrate it to ensure accurate and reliable performance.
- Start with basic movements, such as moving individual joints and verifying their range of motion.
- Test the inverse kinematics by specifying desired end effector positions and orientations and observing the resulting joint angles.
- Validate the motion planning algorithms by generating smooth trajectories and checking for any collisions or violations of joint limits.
- Calibrate the sensors, such as encoders or limit switches, to ensure accurate feedback and positioning.
- Fine-tune the control parameters, such as PID gains, to achieve stable and responsive motion.
- Perform extensive testing under various conditions and loads to identify and address any issues or limitations.
Advanced Features and Enhancements
Once you have a functional robotic arm, you can explore advanced features and enhancements to expand its capabilities and performance.
-
Gripper or End Effector Design: Customize the end effector based on your specific application, such as a gripper for grasping objects or a tool for performing specific tasks.
-
Force Sensing and Control: Incorporate force sensors or load cells to enable force feedback and control, allowing the arm to interact with the environment more intelligently.
-
Vision Integration: Add cameras or depth sensors to enable visual perception and object recognition, enhancing the arm’s ability to locate and manipulate objects.
-
Machine Learning and AI: Implement machine learning algorithms, such as reinforcement learning or imitation learning, to enable the arm to learn and adapt to new tasks and environments.
-
Collaborative Robotics: Design safety features and implement collaborative control strategies to enable safe human-robot interaction in shared workspaces.
Troubleshooting Common Issues
During the development and operation of your robotic arm, you may encounter various issues. Here are some common problems and their potential solutions:
- Mechanical Issues
- Loose or misaligned joints: Check and tighten all the fasteners, and ensure proper alignment of the joints.
- Excessive friction or binding: Lubricate the joints and check for any obstructions or debris.
-
Broken or deformed components: Replace any damaged parts and reinforce weak points in the design.
-
Electrical Issues
- Motor not responding: Check the wiring connections, power supply, and motor driver configuration.
- Sensor readings incorrect: Verify the wiring and calibration of the sensors, and ensure they are correctly connected to the microcontroller.
-
Overheating or burning smell: Immediately disconnect the power supply and check for any short circuits or overloaded components.
-
Software Issues
- Incorrect inverse kinematics calculations: Double-check the equations and algorithms, and verify the input and output units.
- Motion planning errors: Debug the motion planning code and ensure it accounts for joint limits, singularities, and obstacles.
- Control instability: Tune the control parameters, such as PID gains, and consider implementing additional filtering or compensation techniques.
Applications and Future of Robotic Arms
Robotic arms have a wide range of applications across various industries and domains. Some notable examples include:
- Industrial Automation: Assembly lines, material handling, welding, painting, and quality inspection.
- Healthcare and Medical: Surgical assistance, rehabilitation, and prosthetics.
- Agriculture and Food Processing: Harvesting, sorting, and packaging of agricultural products.
- Space Exploration: Robotic arms for spacecraft and planetary rovers, enabling remote manipulation and sample collection.
- Education and Research: Teaching robotics concepts, conducting experiments, and exploring new control strategies and algorithms.
As technology advances, the future of robotic arms looks promising, with potential developments in areas such as:
- Soft Robotics: Flexible and compliant arms that can adapt to unstructured environments and delicate objects.
- Swarm Robotics: Coordination and collaboration among multiple robotic arms for complex tasks and increased efficiency.
- Neuromorphic Computing: Biologically-inspired computing paradigms that can enable more efficient and adaptive control of robotic arms.
- Human-Robot Collaboration: Seamless integration of robotic arms in human workspaces, enabling safe and intuitive interaction.
Frequently Asked Questions (FAQ)
- What is the difference between a robotic arm and a robotic manipulator?
-
A robotic arm and a robotic manipulator are often used interchangeably. However, a robotic arm specifically refers to a programmable mechanical arm that mimics the functions and movements of a human arm, while a robotic manipulator is a more general term that encompasses various types of robotic devices used for manipulation tasks.
-
How do I choose the right motors for my robotic arm?
-
When selecting motors for your robotic arm, consider factors such as the required torque, speed, and power consumption. Determine the maximum load your arm needs to handle and the desired speed of motion. Stepper motors offer precise positioning, while DC motors provide higher speed and torque. Servos are commonly used for smaller robotic arms due to their built-in feedback control.
-
Can I use 3D printed parts for my robotic arm?
-
Yes, 3D printing is a popular choice for fabricating custom parts for robotic arms. It allows for rapid prototyping and customization. However, keep in mind that 3D printed parts may have limitations in terms of strength and durability compared to machined or molded parts. Consider the loads and forces your arm will experience and choose appropriate materials and printing techniques.
-
What programming language should I use for my robotic arm project?
-
The choice of programming language depends on your preferences and the microcontroller or computer you are using. Arduino programming language (based on C/C++) is commonly used with Arduino boards. Python is a popular choice for high-level control and communication, especially when using libraries like ROS (Robot Operating System). Other options include C/C++, MATLAB/Simulink, and Java.
-
How can I ensure the safety of my robotic arm?
- Safety is crucial when working with robotic arms. Implement emergency stop buttons or switches that can quickly halt the arm’s motion in case of any issues. Use limit switches to prevent the arm from exceeding its joint limits and causing damage. Incorporate collision detection and avoidance algorithms in your motion planning. Follow proper wiring and electrical safety practices, and always wear protective gear when working with the arm.
Building a robotic arm project is an exciting and rewarding experience that combines mechanical, electrical, and software skills. By following this step-by-step guide, you can design, assemble, and program your own robotic arm, exploring the fascinating world of robotics and automation. Remember to start with a solid understanding of the fundamentals, plan your design carefully, and iterate and improve upon your project as you learn and gain experience. Happy building!
Leave a Reply