What is PCB Prototyping?
PCB prototyping is the process of creating a small number of printed circuit boards for testing and validation purposes. These prototypes are used to verify the functionality, reliability, and manufacturability of the design before committing to large-scale production. PCB prototyping enables engineers to identify and resolve any issues early in the development cycle, saving time and resources in the long run.
Benefits of PCB Prototyping
- Design validation
- Cost-effective testing
- Faster time-to-market
- Improved reliability
- Opportunities for optimization
PCB Prototype Manufacturing Steps
The PCB prototype manufacturing process consists of several key steps, each of which plays a critical role in ensuring the quality and functionality of the final product.
Step 1: Design and Layout
The first step in PCB prototyping is creating the design and layout of the circuit board. This involves using specialized software, such as Altium Designer, Eagle, or KiCad, to create a schematic diagram and a physical layout of the components and traces.
Design Considerations
- Component selection
- Schematic capture
- Layout and routing
- Design rule checks (DRC)
Step 2: Material Selection
Once the design is finalized, the next step is to select the appropriate materials for the PCB. This includes choosing the substrate (e.g., FR-4, Rogers, polyimide), copper weight, and any additional layers or features required.
Common PCB Materials
Material | Description | Applications |
---|---|---|
FR-4 | Glass-reinforced epoxy laminate | General-purpose, high-volume |
Rogers | High-frequency, low-loss materials | RF and microwave applications |
Polyimide | Flexible, high-temperature resistant material | Flexible and high-density PCBs |
Aluminum | Metal-core PCBs for heat dissipation | High-power LED and automotive |
Step 3: PCB Fabrication
With the design and materials selected, the PCB fabrication process can begin. This involves several sub-steps, including:
-
Copper Clad Laminate Preparation: The chosen substrate material is cut to size and cleaned to remove any contaminants.
-
Dry Film Application: A light-sensitive dry film is applied to the Copper-Clad Laminate, which will serve as a resist during the etching process.
-
Exposure and Development: The PCB artwork is transferred onto the dry film using UV light exposure. The exposed areas are then developed, revealing the copper traces.
-
Etching: The unexposed copper is removed using a chemical etching process, leaving only the desired copper traces on the substrate.
-
Resist Stripping: The remaining dry film resist is removed, exposing the copper traces.
-
Inspection: The fabricated PCB is inspected for any defects or irregularities.
Step 4: PCB Assembly
After the bare PCB is fabricated, the components need to be assembled onto the board. This can be done through various methods, depending on the components and the desired level of automation.
PCB Assembly Techniques
-
Through-Hole Assembly (THA): Components with long leads are inserted through holes drilled in the PCB and soldered on the opposite side.
-
Surface Mount Technology (SMT): Components are placed directly onto pads on the PCB surface and soldered using reflow or wave soldering processes.
-
Mixed Assembly: A combination of through-hole and surface mount components are used on the same PCB.
Step 5: Soldering
Once the components are placed on the PCB, they need to be soldered to establish electrical connections. There are two primary Soldering Methods used in PCB assembly:
-
Reflow Soldering: SMT Components are placed on the PCB with solder paste applied to the pads. The board is then heated in a reflow oven, melting the solder and forming connections between the components and pads.
-
Wave Soldering: Through-hole components are inserted into the PCB, and the board is passed over a molten solder wave. The solder adheres to the component leads and PCB pads, creating electrical connections.
Step 6: Testing and Inspection
After the PCB is assembled, it undergoes rigorous testing and inspection to ensure its functionality and quality. This may include:
-
Visual Inspection: The assembled PCB is visually inspected for any obvious defects, such as missing components, solder bridges, or damaged traces.
-
Automated Optical Inspection (AOI): An automated system uses cameras and image processing algorithms to detect assembly defects and component placement issues.
-
In-Circuit Testing (ICT): The PCB is placed in a bed-of-nails fixture, which makes contact with specific test points on the board. Electrical tests are performed to verify the functionality of individual components and circuits.
-
Functional Testing: The PCB is powered up and tested under real-world operating conditions to ensure it performs as intended.
Step 7: Rework and Repair
If any issues are identified during the testing and inspection phase, the PCB may need to undergo rework or repair. This may involve:
-
Desoldering: Removing faulty components or correcting soldering defects.
-
Component Replacement: Replacing damaged or incorrect components with the correct ones.
-
Trace Repair: Fixing damaged or broken traces using conductive epoxy or wire jumpers.
Step 8: Finishing and Protection
To enhance the durability and longevity of the PCB, various finishing and protection methods can be applied, such as:
-
Conformal Coating: A thin, protective layer is applied to the PCB surface to protect against moisture, dust, and other environmental factors.
-
Potting: The PCB is encapsulated in a resin or epoxy compound to provide mechanical support and protection against vibration and shock.
-
Silk Screening: Text, logos, and other markings are printed on the PCB surface for identification and assembly guidance.
PCB Prototyping Techniques
There are several techniques used in PCB prototyping, each with its own advantages and limitations.
Traditional PCB Prototyping
Traditional PCB prototyping involves using the standard PCB fabrication and assembly processes, as described in the previous sections. This method is suitable for most prototyping needs and offers a balance between cost, time, and quality.
Rapid PCB Prototyping
Rapid PCB prototyping techniques aim to reduce the time and cost associated with creating prototypes. Some common rapid prototyping methods include:
-
PCB Milling: A computer-controlled milling machine is used to remove copper from a blank PCB, creating the desired traces and pads.
-
Laser PCB Prototyping: A laser is used to etch away the unwanted copper, leaving the desired circuit pattern on the substrate.
-
3D Printing: Conductive and non-conductive materials are used to 3D print the PCB structure and traces.
While rapid prototyping techniques offer faster turnaround times and lower costs, they may have limitations in terms of design complexity, material options, and performance compared to traditional methods.
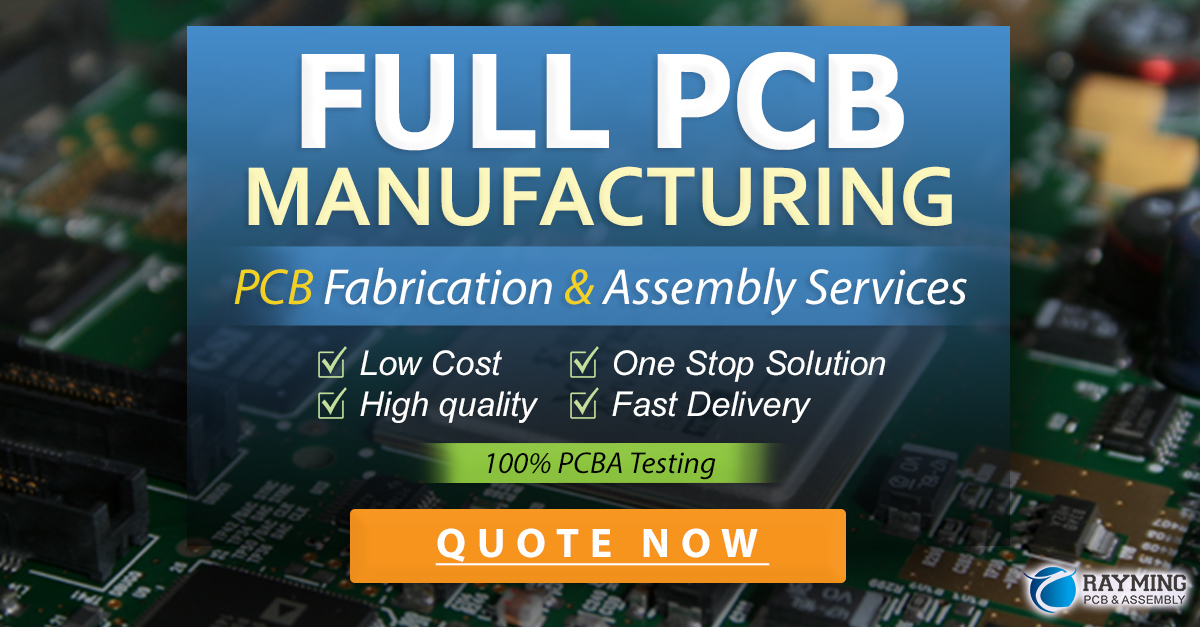
PCB Prototyping Considerations
When embarking on a PCB prototyping project, there are several key considerations to keep in mind:
Design for Manufacturability (DFM)
Designing a PCB with manufacturability in mind is crucial for a successful prototyping process. This involves adhering to design rules, such as minimum trace widths, clearances, and hole sizes, to ensure the PCB can be fabricated and assembled without issues.
Component Selection
Choosing the right components for your PCB prototype is essential for both functionality and manufacturability. Consider factors such as package size, availability, and compatibility with the chosen assembly methods.
Prototype Quantity
Determine the appropriate number of prototypes needed for testing and validation. While a small number of prototypes may be sufficient for basic functional testing, more comprehensive testing may require a larger quantity to account for process variations and statistical significance.
Time and Cost
PCB prototyping can be a time-consuming and costly process, especially when multiple iterations are required. Plan your project timeline and budget accordingly, and consider ways to optimize the process, such as using rapid prototyping techniques or outsourcing certain steps to specialized providers.
Frequently Asked Questions (FAQ)
-
Q: How long does PCB prototyping typically take?
A: The time required for PCB prototyping can vary depending on the complexity of the design, the chosen fabrication and assembly methods, and the workload of the prototyping service provider. Generally, traditional PCB prototyping can take anywhere from a few days to several weeks, while rapid prototyping methods may offer shorter lead times. -
Q: What is the cost of PCB prototyping?
A: The cost of PCB prototyping depends on factors such as the PCB size, layer count, material selection, component types, and the number of prototypes required. Rapid prototyping methods may offer lower costs for small quantities, while traditional methods may be more cost-effective for larger prototype runs. It’s essential to obtain quotes from multiple prototyping service providers to compare costs and find the best option for your project. -
Q: Can I prototype a PCB at home?
A: Yes, it is possible to prototype PCBs at home using various methods, such as PCB milling, laser etching, or even hand-etching using ferric chloride. However, these methods may have limitations in terms of design complexity, precision, and repeatability compared to professional prototyping services. -
Q: What are the advantages of outsourcing PCB prototyping?
A: Outsourcing PCB prototyping to a professional service provider offers several advantages, including access to specialized equipment and expertise, faster turnaround times, and higher quality results. Prototyping service providers can also offer guidance on design optimization, component selection, and manufacturability, helping to streamline the development process. -
Q: How do I choose the right PCB prototyping service provider?
A: When selecting a PCB prototyping service provider, consider factors such as their experience, capabilities, turnaround times, and customer support. Look for providers that offer a range of prototyping options to suit your specific needs and budget. Reading customer reviews and requesting sample projects can also help you gauge the quality and reliability of a prototyping service provider.
Conclusion
PCB prototyping is an essential step in the development of electronic devices, allowing engineers and designers to test and validate their designs before committing to mass production. By understanding the various steps involved in the PCB prototype manufacturing process, as well as the different techniques and considerations, you can effectively plan and execute your prototyping projects, ensuring a smooth transition from concept to reality.
Leave a Reply