Composition and Structure of Copper Clad Laminate
Copper Foil Layer
The copper foil layer in CCL is a thin, conductive material that ranges in thickness from 9 to 180 microns (µm). The most common thicknesses used in PCB Manufacturing are:
Copper Thickness (µm) | Copper Weight (oz/ft²) |
---|---|
18 | 0.5 |
35 | 1.0 |
70 | 2.0 |
105 | 3.0 |
The copper foil is treated with a surface finish to enhance adhesion to the substrate and protect it from oxidation. Some common surface finishes include:
- Electrodeposited (ED) copper
- Rolled annealed (RA) copper
- Reverse treated foil (RTF)
- Double-treated copper (DTC)
Dielectric Substrate
The dielectric substrate in CCL provides electrical insulation and mechanical support for the copper foil. The most widely used substrate materials are:
- FR-4: A glass-reinforced epoxy laminate with good mechanical and electrical properties, suitable for most PCB applications.
- CEM-3: A composite epoxy material with a non-woven glass reinforcement, offering lower cost and performance compared to FR-4.
- Polyimide: A high-performance substrate with excellent thermal stability and chemical resistance, used in advanced applications such as aerospace and Military Electronics.
- PTFE (Teflon): A low-dielectric-constant substrate with superior high-frequency performance, used in RF and microwave applications.
The choice of substrate material depends on the specific requirements of the PCB, such as thermal stability, dielectric constant, and cost.
Bonding Process
The copper foil is bonded to the dielectric substrate using a lamination process. The most common methods are:
- Prepreg lamination: The copper foil is laminated to a partially cured (B-stage) epoxy resin-impregnated glass fabric (prepreg) under heat and pressure.
- Pressure lamination: The copper foil is directly laminated to a fully cured (C-stage) substrate using a high-pressure press and an adhesive layer.
The lamination process ensures a strong and reliable bond between the copper foil and the substrate, minimizing the risk of delamination during PCB manufacturing and operation.
Properties and Characteristics of Copper Clad Laminate
Electrical Properties
The electrical properties of CCL are crucial for the performance of PCBs. Some key properties include:
- Dielectric constant (Dk): The ratio of the permittivity of the substrate material to that of vacuum. A lower Dk value indicates better high-frequency performance.
- Dissipation factor (Df): A measure of the energy loss in the substrate material. A lower Df value indicates lower signal attenuation and better high-frequency performance.
- Surface resistance: The resistance of the copper foil surface to the flow of electrical current. A lower surface resistance ensures better signal integrity and lower power losses.
- Insulation resistance: The resistance of the substrate material to electrical leakage between conductors. A higher insulation resistance prevents short circuits and signal crosstalk.
Mechanical Properties
The mechanical properties of CCL determine its durability and reliability during PCB manufacturing and operation. Some important mechanical properties include:
- Peel strength: The force required to peel the copper foil from the substrate. A higher peel strength indicates better adhesion and resistance to delamination.
- Flexural strength: The ability of the CCL to withstand bending forces without cracking or breaking. A higher flexural strength ensures better handling and durability during PCB Assembly.
- Dimensional stability: The ability of the CCL to maintain its dimensions under varying environmental conditions, such as temperature and humidity changes. Better dimensional stability ensures accurate alignment of layers and components during PCB manufacturing.
Thermal Properties
The thermal properties of CCL are essential for the reliable operation of PCBs in various environmental conditions. Some key thermal properties include:
- Glass transition temperature (Tg): The temperature at which the substrate material transitions from a glassy to a rubbery state. A higher Tg value indicates better thermal stability and resistance to deformation at elevated temperatures.
- Coefficient of thermal expansion (CTE): The rate at which the CCL expands or contracts with temperature changes. A lower CTE value ensures better dimensional stability and reduces stress on components and interconnections.
- Thermal conductivity: The ability of the CCL to conduct heat away from components and distribute it evenly across the PCB. A higher thermal conductivity helps in efficient heat dissipation and prevents localized hot spots.
Manufacturing Process of Copper Clad Laminate
The manufacturing process of CCL involves several steps to ensure consistent quality and performance. The main stages are:
- Substrate preparation: The dielectric substrate is cut to the required size and shape, and its surface is cleaned and treated to enhance adhesion to the copper foil.
- Copper foil preparation: The copper foil is cleaned, surface-treated, and cut to the desired size.
- Lamination: The prepared copper foil and substrate are laminated together using either the prepreg or pressure lamination method, as described earlier.
- Curing: The laminated CCL is cured under controlled temperature and pressure conditions to ensure a strong and stable bond between the copper foil and the substrate.
- Quality control: The finished CCL undergoes various quality control tests, such as peel strength, dimensional stability, and electrical properties, to ensure compliance with industry standards and customer specifications.
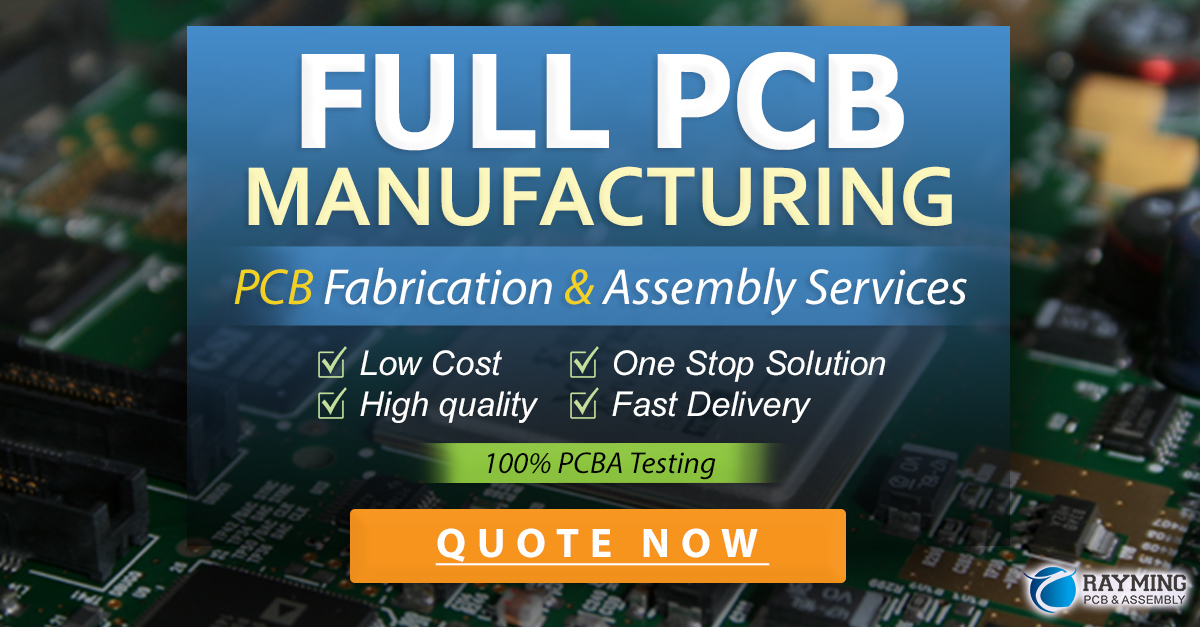
Applications of Copper Clad Laminate in PCB Manufacturing
CCL is the primary material used in the production of PCBs for various applications, including:
- Consumer electronics: Smartphones, tablets, laptops, and home appliances
- Automotive electronics: Engine control units, infotainment systems, and advanced driver assistance systems (ADAS)
- Industrial automation: Programmable logic controllers (PLCs), sensors, and control panels
- Medical devices: Diagnostic equipment, monitoring systems, and implantable devices
- Aerospace and defense: Avionics, radar systems, and satellite communication equipment
- Telecommunications: Routers, switches, and 5G infrastructure
The specific type of CCL used in each application depends on the required electrical, mechanical, and thermal properties, as well as the cost and manufacturing constraints.
Advancements and Future Trends in Copper Clad Laminate Technology
As the demand for high-performance and miniaturized electronic devices continues to grow, CCL technology is evolving to meet new challenges and requirements. Some notable advancements and future trends include:
- High-frequency materials: The development of low-loss, low-Dk substrates, such as modified polyimides and ceramic-filled PTFE, to support the growing demand for 5G and millimeter-wave applications.
- Embedded components: The integration of passive components, such as resistors and capacitors, into the CCL substrate to reduce PCB Size, improve signal integrity, and simplify assembly.
- Flexible and stretchable substrates: The development of flexible and stretchable CCL materials, such as polyimide and thermoplastic polyurethane (TPU), to enable the production of flexible and wearable electronics.
- Eco-friendly materials: The use of halogen-free, recyclable, and bio-based substrates to reduce the environmental impact of PCB manufacturing and comply with evolving regulations.
- Additive manufacturing: The application of 3D printing technologies, such as inkjet printing and aerosol jet printing, to directly deposit conductive traces on CCL substrates, enabling rapid prototyping and customization of PCBs.
Frequently Asked Questions (FAQ)
1. What is the difference between FR-4 and CEM-3 substrates in CCL?
FR-4 is a high-performance substrate made from glass-reinforced epoxy resin, offering excellent mechanical and electrical properties. CEM-3, on the other hand, is a lower-cost composite epoxy material with a non-woven glass reinforcement, providing reduced performance compared to FR-4. FR-4 is suitable for most PCB applications, while CEM-3 is often used in cost-sensitive consumer electronics.
2. How does the thickness of the copper foil affect the performance of CCL?
The thickness of the copper foil in CCL determines its current-carrying capacity and signal integrity. Thicker copper foils, such as 2 oz/ft² (70 µm) or 3 oz/ft² (105 µm), are used in power electronics and high-current applications to minimize resistive losses and improve thermal management. Thinner copper foils, such as 0.5 oz/ft² (18 µm) or 1 oz/ft² (35 µm), are preferred in high-density interconnect (HDI) PCBs to enable finer trace widths and spacing, reducing signal attenuation and crosstalk.
3. What are the advantages of using halogen-free CCL in PCB manufacturing?
Halogen-free CCL materials, such as those based on polyphenylene oxide (PPO) or polyethylene naphthalate (PEN), offer several advantages over traditional halogenated substrates:
- Reduced environmental impact: Halogen-free materials do not release toxic fumes during PCB manufacturing or disposal, making them more eco-friendly.
- Improved safety: Halogen-free CCL has better flame retardancy and generates less smoke in case of a fire, enhancing the safety of electronic devices.
- Compliance with regulations: Many countries have introduced restrictions on the use of halogenated substances in electronic products, making halogen-free CCL a preferred choice for compliance with evolving regulations.
4. How can embedded components in CCL benefit PCB Design and manufacturing?
Embedding passive components, such as resistors and capacitors, directly into the CCL substrate offers several benefits for PCB design and manufacturing:
- Miniaturization: Embedded components reduce the surface area required on the PCB, enabling smaller and more compact designs.
- Improved signal integrity: Embedding components close to the active devices reduces the length of interconnections, minimizing signal attenuation, distortion, and crosstalk.
- Simplified assembly: With fewer surface-mounted components, the PCB assembly process becomes simpler and more reliable, reducing the risk of defects and improving yield.
- Enhanced thermal management: Embedded components can be placed closer to heat sinks or thermal vias, improving heat dissipation and preventing localized hot spots.
5. What are the challenges in adopting additive manufacturing technologies for CCL processing?
While additive manufacturing technologies, such as inkjet printing and aerosol jet printing, offer promising opportunities for rapid prototyping and customization of PCBs, there are several challenges in their adoption for CCL processing:
- Material compatibility: Additive manufacturing processes require specialized conductive inks and substrates that are compatible with the printing technology. Developing and optimizing these materials for reliable and high-performance PCBs is an ongoing challenge.
- Resolution and accuracy: Achieving high resolution and accurate positioning of conductive traces on CCL substrates is crucial for the performance and reliability of PCBs. Additive manufacturing technologies are continually improving to meet these requirements, but there is still room for further advancements.
- Process control and repeatability: Ensuring consistent and repeatable results in additive manufacturing processes is essential for large-scale production of PCBs. Developing robust process control and monitoring systems is necessary to maintain the quality and reliability of additively manufactured CCL.
- Integration with conventional PCB manufacturing: Integrating additive manufacturing technologies into existing PCB manufacturing workflows requires significant investments in equipment, training, and process optimization. Overcoming these barriers is crucial for the widespread adoption of additive manufacturing in the PCB industry.
In conclusion, Copper Clad Laminate (CCL) is a vital material in the production of printed circuit boards, serving as the foundation for creating conductive paths and interconnections in various electronic devices. The composition, structure, and properties of CCL, along with advancements in materials and manufacturing technologies, play a crucial role in enabling the development of high-performance, miniaturized, and reliable electronic products. As the demand for advanced electronic devices continues to grow, innovations in CCL technology will be essential to meet the evolving requirements of the PCB industry and support the future of electronics.
Leave a Reply