What is PCB Design Software?
PCB design software is a specialized computer-aided design (CAD) tool used to create printed circuit boards (PCBs). It allows engineers and designers to lay out the electronic components and copper traces that make up a PCB. The software typically includes features for schematic capture, component placement, routing, design rule checking (DRC), and generating manufacturing files.
Using PCB design software is the first and most critical step in creating a new printed circuit board. It enables the PCB designer to efficiently design the board, validate that it meets specifications, and generate the files needed for manufacturing. High-quality PCB design is essential for ensuring the functionality, reliability, and manufacturability of the final board.
Types of PCB Design Software
There are several different types of PCB design software available on the market, each with its own strengths and target users:
Desktop PCB Design Software
Desktop PCB design tools like Altium Designer, OrCAD, and EAGLE run on Windows or Mac computers. They provide a full range of features for designing complex, multi-layer PCBs. These tools are used by professional engineers designing boards for commercial products.
Software | Operating System | Key Features |
---|---|---|
Altium Designer | Windows | Advanced routing, MCAD integration, simulation |
OrCAD | Windows | Constraint-driven flow, SPICE simulation, FPGA integration |
EAGLE | Windows, Mac, Linux | Extensive part libraries, scripting, affordable |
Web-Based PCB Design Software
A newer category of PCB design tools runs entirely in a web browser. Examples include EasyEDA, Upverter, and CircuitMaker. These tools offer rapid design entry, real-time collaboration, and easy access from any computer. However, they may have limited layer counts or manufacturing options compared to desktop software.
Software | Supported Browsers | Collaboration Features |
---|---|---|
EasyEDA | Chrome, Firefox, Safari, Edge | Real-time team collaboration, comments, version control |
Upverter | Chrome, Firefox | Live collaboration, version control, inline comments |
CircuitMaker | Chrome, Firefox | Real-time collaboration, version control, forums |
Free/Open Source PCB Design Software
For hobbyists, students, and small businesses, there are free and open source PCB Tools with reduced feature sets. The most popular is KiCad, a cross-platform tool with schematic capture and PCB Layout. Other free/low-cost tools include FreePCB, DesignSpark PCB, and ExpressPCB.
Software | Platforms | License |
---|---|---|
KiCad | Windows, Mac, Linux | Open source (GPLv3) |
FreePCB | Windows | Freeware |
DesignSpark PCB | Windows | Freeware |
ExpressPCB | Windows | Free version + low-cost upgrade |
Key Features of PCB Design Software
When evaluating PCB design software, there are several key features and capabilities to consider:
Schematic Capture
Schematic capture is the ability to create an electronic schematic diagram showing the components and connectivity. It is the first step in the PCB design process. The software should have an easy-to-use schematic editor with built-in symbols and the ability to create custom symbols.
Component Libraries
An extensive library of component footprints and 3D models can save significant time when designing a PCB. The software should include a large selection of common parts as well as the ability to create custom footprints. Many vendors provide CAD models of their components that can be imported.
PCB Layout & Routing
The PCB layout tools allow the designer to place components on the board and route the copper traces to make connections. The software should support advanced routing features like differential pairs, length matching, and automatic routing. It should allow setting design rules to ensure manufacturability.
Design Rule Checking (DRC)
DRC allows automatically checking the PCB layout against a set of design rules to verify it is error-free and manufacturable. Examples of design rules include minimum trace width, minimum clearance between traces, and hole size tolerances. DRC can catch errors before the board is manufactured.
MCAD Integration
Mechanical CAD (MCAD) integration allows linking the PCB design with the mechanical enclosure or other product assemblies. This capability is important for designing boards that must fit in tight spaces or have specific mounting requirements. The PCB software should allow importing STEP files and other 3D formats.
Manufacturing File Export
Once the PCB design is complete, the software must be able to export the files needed for manufacturing. These include Gerber files, drill files, pick and place files, and 3D files. The software should have built-in tools for panelizing boards and generating detailed drawings and assembly diagrams.
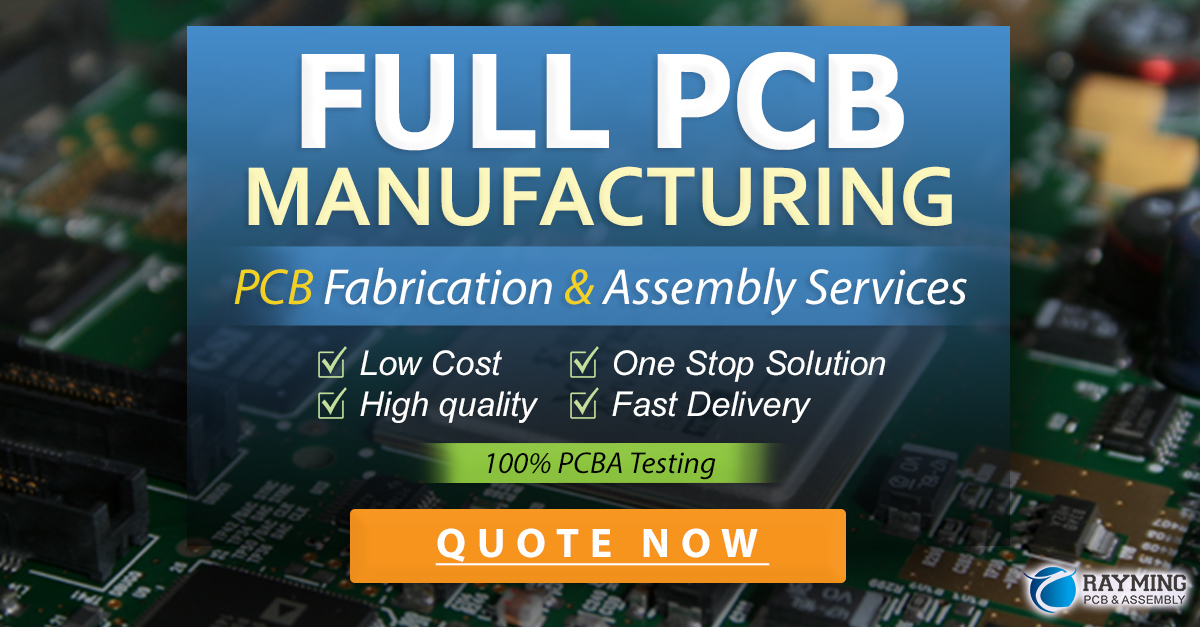
The PCB Design Process
Using PCB design software involves several steps to go from concept to a completed board:
-
Schematic Capture – Create the schematic diagram showing the components and connections. Assign component values and verify against the datasheet.
-
Component Placement – Place the component footprints on the board outline. Arrange them to minimize crossing traces and allow room for mounting holes and keep-out areas.
-
Routing – Route the copper traces on the various signal layers to make the connections between components. The router must avoid obstacles and follow the design rules.
-
Design Rule Check – Run DRC to verify the board is error-free. Inspect any violations and make corrections to the layout as needed.
-
Manufacturing Prep – Once the design is finalized, export the Gerber files and drill files for manufacturing. Generate the assembly drawings, BOM, and centroid file for the pick and place machine.
-
Post-Processing – Perform any final post-processing steps like panelizing the board for production. Some PCB tools have features for arranging multiple copies of a board in an array to maximize usage of the material.
By following this process using PCB design software, engineers can efficiently design complex, multi-layer PCBs that are ready for manufacturing. The software automates many tedious and error-prone steps to streamline the design process.
Challenges of PCB Design
Despite the power of modern PCB design software, designing a complex PCB still involves challenges the tools cannot fully automate. Some of the top challenges include:
High-Speed Design
Designing boards to carry high-speed digital or RF signals requires specialized knowledge and tools. The PCB layout must control impedances, avoid crosstalk, and match trace lengths to ensure signal integrity. Many PCB tools include features for high-speed design like controlled impedance routing and scheduled routing.
Dense Layouts
Fitting all the required components and traces onto a small PCB can be very challenging. Designers must carefully plan the placement and minimize wasted space. Using smaller components, blind/buried vias, and high density interconnect (HDI) techniques can make routing easier.
Thermal Management
High-power components like FPGAs and power supplies generate significant heat that must be dissipated to avoid damage. The PCB layout must provide sufficient copper pour for heatsinking and allow airflow for cooling. Thermal simulation tools can predict hot spots and validate the thermal design.
EMI/EMC Compliance
Many electronic products must meet strict limits on electromagnetic emissions to avoid interfering with other devices. PCB design plays a key role in ensuring EMC by proper grounding, shielding, and filtering. The layout may need to be simulated or tested in an EMC lab to verify compliance.
Future of PCB Design Software
PCB design software continues to evolve to keep pace with advances in electronics technology. Some of the key trends shaping the future of PCB tools include:
AI-Driven Design
Artificial intelligence and machine learning techniques are being applied to PCB design to automate complex tasks. Examples include AI-assisted component placement, constraint-driven routing, and design rule optimization. AI can learn from past designs to make intelligent suggestions.
Cloud Collaboration
The rise of web-based PCB tools is enabling new forms of cloud collaboration. Designers can work on the same PCB layout simultaneously from different locations, with changes synced in real-time. Cloud platforms also make it easy to share designs with manufacturers and access from any device.
Virtual Prototyping
Advanced PCB design tools are adding features for virtual prototyping, allowing designers to simulate and test their boards in software before committing to a physical prototype. This includes thermal simulation, signal integrity analysis, and 3D visualization. Virtual prototyping can reduce design iterations and speed time-to-market.
Additive Manufacturing
3D printing technologies are being applied to PCB fabrication, enabling new possibilities for embedding components and creating non-planar circuit boards. Some PCB design tools are adding support for 3D-printed electronics, allowing designers to create freeform shapes and experiment with novel packaging concepts.
PCB Design Software FAQ
What is the best PCB design software?
There is no single “best” PCB design software since the right tool depends on the specific needs of the user. For professional engineers designing complex boards, Altium Designer and OrCAD are popular choices. For hobbyists and educators, KiCad and EasyEDA are good free/low-cost options.
How much does PCB design software cost?
The cost of PCB design software varies widely, from free to tens of thousands of dollars. Free tools like KiCad have reduced feature sets but are suitable for simple designs. Professional tools like Altium Designer and OrCAD have a high upfront cost but offer advanced capabilities for complex boards. Many vendors offer monthly subscriptions for a lower entry price.
What skills are needed to use PCB design software?
Using PCB design software requires a combination of technical skills and creative problem-solving. A background in electrical engineering is helpful for understanding circuit theory and component selection. Familiarity with CAD tools is useful for efficient schematic capture and layout. Attention to detail is critical for ensuring the design is error-free and manufacturable.
How long does it take to learn PCB design software?
The time required to learn PCB design software depends on the complexity of the tool and the user’s prior experience. Simple tools like KiCad and EasyEDA can be picked up in a few days of intense use. More complex tools like Altium Designer may take several weeks to become proficient. Having an experienced mentor and working on real projects can accelerate the learning curve.
What are the system requirements for PCB design software?
The system requirements vary by specific software, but most PCB design tools require a modern computer with a fast CPU, ample RAM, and a dedicated graphics card. For complex designs with large component libraries, 16GB or more of RAM is recommended. A large, high-resolution display is helpful for visualizing the layout. Some tools only run on Windows, while others support Mac and Linux.
Conclusion
PCB design software is an essential tool for anyone involved in designing and manufacturing printed circuit boards. It allows quickly capturing schematics, laying out the board, and generating manufacturing files. A wide range of PCB tools are available, from simple hobbyist software to advanced professional suites.
When selecting PCB design software, consider the types of boards being designed, the required features, and the budget and expertise of the user. The right tool can streamline the design process, reduce errors, and accelerate time to market.
As PCB technology continues to advance, the capabilities of design software are also evolving. Trends like AI-assisted design, cloud collaboration, and virtual prototyping are shaping the future of PCB tools. Staying current with these developments can give designers and engineers a competitive edge.
Leave a Reply