Introduction to PCB Impedance Control
In the world of high-speed electronic circuits, controlling the impedance of printed circuit boards (PCBs) is crucial for ensuring signal integrity and optimizing system performance. Impedance control is the process of designing PCBs to maintain a consistent characteristic impedance throughout the signal paths. This is particularly important for high-frequency signals, where mismatches in impedance can lead to signal reflections, crosstalk, and other issues that can degrade signal quality and reliability.
What is Characteristic Impedance?
Characteristic impedance is the resistance to the propagation of an electrical signal through a transmission line, such as a PCB trace. It is determined by the physical properties of the transmission line, including its width, thickness, dielectric constant of the substrate material, and the distance to the reference plane (usually ground or power). The characteristic impedance is typically expressed in ohms (Ω) and is often denoted as Z0.
Why is Impedance Control Important?
Impedance control is essential for several reasons:
-
Signal Integrity: Matching the impedance of the signal paths to the characteristic impedance of the transmission line minimizes signal reflections and ensures clean, undistorted signals.
-
Crosstalk Reduction: Proper impedance control helps reduce crosstalk between adjacent signal traces, preventing interference and maintaining signal quality.
-
EMI/EMC Compliance: Controlling impedance can help minimize electromagnetic interference (EMI) and improve electromagnetic compatibility (EMC), which is crucial for meeting regulatory requirements.
-
High-Speed Performance: As signal frequencies increase, the effects of impedance mismatches become more pronounced. Impedance control is critical for maintaining signal integrity in high-speed applications.
PCB Impedance Control Techniques
There are several techniques used to control impedance in PCB design and fabrication. Some of the most common methods include:
Trace Width and Spacing
One of the primary ways to control impedance is by adjusting the width and spacing of the PCB traces. The characteristic impedance of a trace is inversely proportional to its width, meaning that wider traces have lower impedance, while narrower traces have higher impedance. By carefully selecting trace widths and spacings, designers can achieve the desired characteristic impedance.
Dielectric Material Selection
The choice of dielectric material (substrate) also plays a significant role in impedance control. The dielectric constant (Dk) of the material determines how much the electric field is concentrated between the trace and the reference plane. Materials with higher Dk values, such as FR-4, result in lower characteristic impedance, while materials with lower Dk, such as Rogers laminates, lead to higher impedance.
Stackup Design
The PCB Stackup, which refers to the arrangement of copper layers and dielectric materials, is another important factor in impedance control. By strategically placing signal layers, ground planes, and power planes, designers can create a stackup that provides consistent reference planes for the signal traces. This helps maintain a uniform characteristic impedance throughout the board.
Differential Pairs
Differential signaling, which uses two complementary signals to transmit data, is commonly used in high-speed applications. To maintain signal integrity, it is crucial to route differential pairs with tightly controlled impedance. This is achieved by carefully managing the trace width, spacing, and length of the differential pair, as well as ensuring symmetry between the two traces.
PCB Impedance Calculation and Simulation
To design PCBs with controlled impedance, engineers rely on impedance calculation and simulation tools. These tools help determine the optimal trace geometries and stackup configurations to achieve the desired characteristic impedance.
Impedance Calculation Formulas
There are several formulas used to calculate the characteristic impedance of PCB traces, depending on the trace geometry and dielectric properties. Some of the most common formulas include:
- Microstrip: For traces on the outer layers of a PCB, with a single reference plane:
Z0 = 87 / √(εr + 1.41) * ln(5.98 * h / (0.8 * w + t))
Where:
– Z0 is the characteristic impedance (Ω)
– εr is the dielectric constant of the substrate material
– h is the dielectric thickness (mm)
– w is the trace width (mm)
– t is the trace thickness (mm)
- Stripline: For traces embedded within the PCB, with reference planes above and below:
Z0 = 60 / √εr * ln(4 * h / (0.67 * (0.8 * w + t)))
Where:
– Z0 is the characteristic impedance (Ω)
– εr is the dielectric constant of the substrate material
– h is the dielectric thickness between the trace and the reference plane (mm)
– w is the trace width (mm)
– t is the trace thickness (mm)
Impedance Simulation Tools
While impedance calculation formulas provide a good starting point, they have limitations and may not account for all the complex factors affecting impedance in a real-world PCB. This is where impedance simulation tools come into play. These software tools use advanced electromagnetic modeling techniques to accurately simulate the behavior of PCB traces and predict their characteristic impedance.
Some popular impedance simulation tools include:
-
Polar SI9000: A powerful impedance modeling and simulation tool that supports a wide range of PCB geometries and materials.
-
Altium Designer: A comprehensive PCB design software that includes built-in impedance calculation and simulation features.
-
Cadence Allegro PCB SI: A specialized tool for signal integrity analysis and impedance control in high-speed PCB designs.
By using these tools, engineers can optimize their PCB designs for controlled impedance and ensure robust signal integrity.
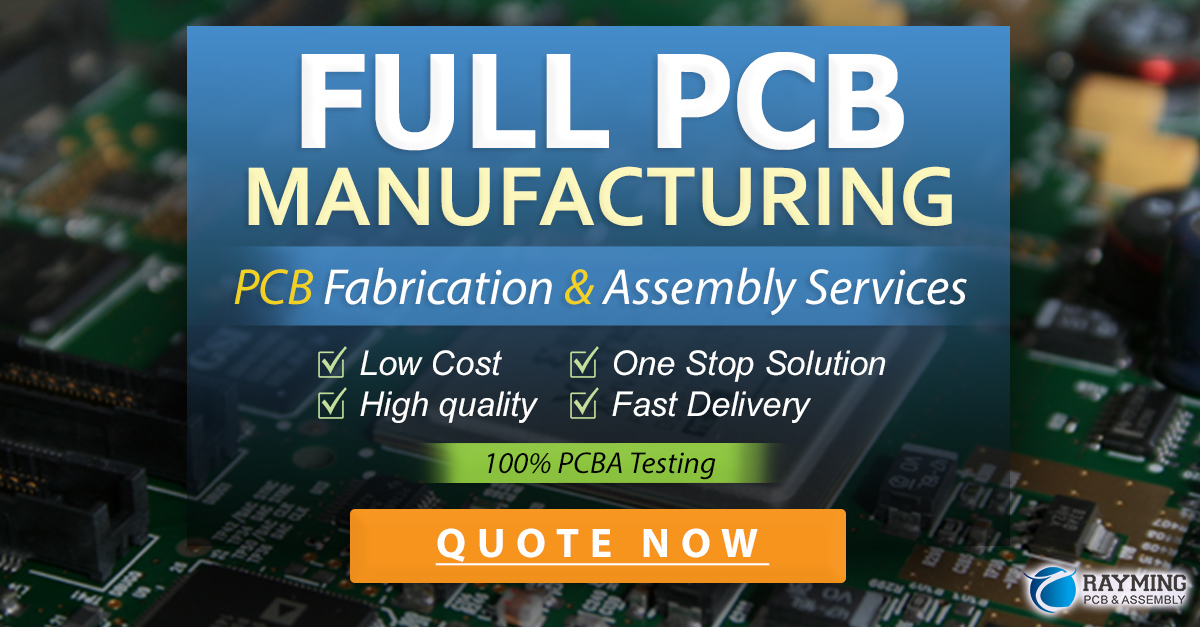
PCB Fabrication and Assembly for Impedance Control
Once the PCB design is finalized with controlled impedance, it is crucial to ensure that the fabrication and assembly processes maintain the desired impedance characteristics.
PCB Fabrication Considerations
During PCB fabrication, several factors can impact impedance control:
-
Material Selection: The dielectric materials used in the PCB stackup must match the specifications used in the impedance calculations and simulations.
-
Etching Process: The accuracy and consistency of the etching process directly affect the width and thickness of the PCB traces, which in turn impact the characteristic impedance.
-
Lamination: The lamination process, which bonds the layers of the PCB together, must be carefully controlled to maintain consistent dielectric thickness and prevent variations in impedance.
-
Plating: The plating process, used to add copper to the drilled holes (vias) and to protect the exposed copper traces, can also affect impedance if not properly controlled.
To ensure the fabricated PCBs meet the impedance requirements, manufacturers use specialized equipment and processes, such as impedance-controlled etching and laser direct imaging (LDI), to maintain tight tolerances and consistency.
PCB Assembly Considerations
During PCB assembly, the placement and soldering of components can also impact impedance control:
-
Component Placement: The positioning of components, particularly those with leads or pads connected to controlled impedance traces, must be accurate to maintain the desired impedance.
-
Soldering: The soldering process, whether through-hole or surface-mount, must be carefully controlled to prevent excessive solder buildup or bridging, which can alter the impedance of the traces.
-
Inspection: Post-assembly inspection, using automated optical inspection (AOI) or X-ray inspection, is crucial for detecting any soldering defects or component misalignments that could affect impedance.
By paying close attention to these factors during PCB fabrication and assembly, manufacturers can ensure that the final product meets the specified impedance requirements and performs as intended.
Testing and Verification of Impedance Control
After PCB fabrication and assembly, it is essential to test and verify the impedance control to ensure that the board meets the design specifications. There are several methods used for impedance testing, including:
-
Time Domain Reflectometry (TDR): TDR is a technique that sends a fast-rising electrical pulse through the PCB trace and measures the reflections caused by impedance mismatches. By analyzing the reflected waveforms, engineers can determine the characteristic impedance along the trace and identify any discontinuities.
-
Frequency Domain Reflectometry (FDR): FDR is similar to TDR but uses a swept frequency signal instead of a pulse. It measures the reflected energy at different frequencies to characterize the impedance of the PCB traces.
-
Vector Network Analyzer (VNA): A VNA is a sophisticated instrument that measures the scattering parameters (S-parameters) of a PCB trace over a range of frequencies. By analyzing the S-parameters, engineers can determine the characteristic impedance, insertion loss, and return loss of the trace.
-
Impedance Test Coupons: Many PCB designs include impedance test coupons, which are small sections of the board that replicate the controlled impedance traces. These coupons are used for destructive testing, where a precise cross-section of the trace is measured to verify its dimensions and calculate the characteristic impedance.
By employing these testing methods, manufacturers can validate the impedance control of the fabricated PCBs and ensure that they meet the required specifications. This helps guarantee the performance and reliability of the final product.
FAQ
-
What is the difference between single-ended and differential impedance?
Single-ended impedance refers to the characteristic impedance of a single trace with respect to a reference plane, such as ground. Differential impedance, on the other hand, is the impedance between two traces in a differential pair, which carry complementary signals. Differential impedance is important for maintaining signal integrity in high-speed differential signaling applications. -
How does the dielectric constant affect impedance control?
The dielectric constant (Dk) of the substrate material plays a significant role in determining the characteristic impedance of PCB traces. A higher Dk value results in lower impedance, while a lower Dk leads to higher impedance. When selecting a dielectric material for impedance control, it is important to consider its Dk value and how it affects the trace geometries required to achieve the desired impedance. -
What is the impact of via stubs on impedance control?
Via stubs, which are the unused portions of a via below the signal layer, can create impedance discontinuities and lead to signal reflections. In high-speed designs, via stubs can significantly degrade signal integrity. To minimize their impact, designers can use techniques such as back-drilling, which removes the unwanted portion of the via, or blind and buried vias, which do not extend through the entire board stackup. -
How do you control impedance in high-density interconnect (HDI) PCBs?
Controlling impedance in HDI PCBs, which feature fine-pitch traces and microvias, can be challenging due to the smaller geometries involved. To maintain impedance control in HDI designs, engineers must carefully select dielectric materials, optimize trace widths and spacings, and use advanced simulation tools to model the complex interactions between traces and reference planes. Additionally, the use of advanced manufacturing techniques, such as modified semi-additive process (mSAP), can help achieve the required precision and consistency in trace geometries. -
What are the benefits of using a PCB stackup with dedicated reference planes for impedance control?
Using a PCB stackup with dedicated reference planes, such as ground and power planes, can significantly improve impedance control. By providing a continuous and uninterrupted reference for the signal traces, these planes help maintain a consistent characteristic impedance throughout the board. They also help reduce crosstalk and EMI by providing a low-impedance return path for the signals. When designing a stackup for impedance control, it is important to carefully consider the placement and spacing of the reference planes to optimize signal integrity.
Conclusion
PCB impedance control is a critical aspect of designing and manufacturing high-speed electronic systems. By carefully managing the characteristic impedance of PCB traces, engineers can ensure signal integrity, reduce crosstalk and EMI, and optimize system performance. This article has covered the fundamentals of PCB impedance control, including the importance of characteristic impedance, common impedance control techniques, calculation and simulation methods, fabrication and assembly considerations, and testing and verification procedures.
As the demand for faster and more complex electronic systems continues to grow, the importance of effective impedance control in PCB design and manufacturing will only increase. By staying up-to-date with the latest techniques, tools, and best practices, engineers and manufacturers can meet the challenges of designing and producing high-performance PCBs with reliable and consistent impedance characteristics.
Leave a Reply