What are HDI PCBs?
HDI PCBs are a type of printed circuit board that features higher wiring density and smaller vias than conventional PCBs. These boards are designed to accommodate more components in a smaller space, enabling the creation of compact and highly functional electronic devices. HDI PCBs typically have a higher number of layers (8 or more) and use advanced materials and manufacturing techniques to achieve their superior performance.
Key features of HDI PCBs:
- High wiring density
- Smaller vias and microvias
- Increased number of layers
- Advanced materials and manufacturing techniques
- Improved signal integrity and reliability
Benefits of Using HDI PCBs
HDI PCBs offer numerous advantages over traditional PCBs, making them the preferred choice for many industries and applications. Some of the key benefits include:
1. Miniaturization
HDI PCBs allow for the creation of smaller, more compact electronic devices without sacrificing performance or functionality. This is particularly important for consumer electronics, wearables, and medical devices where size and weight are critical factors.
2. Enhanced Performance
With their higher wiring density and smaller vias, HDI PCBs offer improved signal integrity, reduced electromagnetic interference (EMI), and better power distribution. This leads to enhanced overall performance and reliability of the electronic devices.
3. Cost-Effectiveness
Although HDI PCBs may have a higher initial cost compared to traditional PCBs, they often prove to be more cost-effective in the long run. The increased functionality and miniaturization capabilities of HDI PCBs can lead to reduced overall system costs, as fewer components and less space are required.
4. Faster Time-to-Market
HDI PCBs enable faster design and manufacturing cycles, thanks to their advanced design tools and streamlined production processes. This allows companies to bring their products to market more quickly, gaining a competitive edge in their respective industries.
HDI PCB Manufacturing Process
The manufacturing process for HDI PCBs is more complex and precise than that of traditional PCBs. It involves several key stages, each requiring specialized equipment and expertise.
1. Design and Layout
The first step in HDI PCB manufacturing is the design and layout phase. This involves creating a detailed schematic of the circuit board, specifying the placement of components, and routing the connections between them. Advanced design software tools are used to ensure optimal layout and minimize signal interference.
2. Material Selection
Choosing the right materials is crucial for the performance and reliability of HDI PCBs. High-quality substrates, such as FR-4, Rogers, or Polyimide, are commonly used. The selection of materials depends on the specific requirements of the application, such as thermal stability, dielectric constant, and mechanical strength.
3. Lamination
Once the design is finalized and materials are selected, the PCB layers are laminated together under high pressure and temperature. This process ensures a strong bond between the layers and helps maintain the board’s structural integrity.
4. Drilling and Plating
After lamination, the PCB undergoes drilling and plating processes. Microvias are drilled using advanced laser or mechanical drilling techniques, allowing for the creation of small, precise holes. These holes are then plated with copper to establish electrical connections between layers.
5. Patterning and Etching
The next step involves patterning and etching the copper traces on the PCB. A photoresist layer is applied to the board, and the desired pattern is transferred using photolithography. The exposed copper is then etched away, leaving behind the desired circuit pattern.
6. Solder Mask and Silkscreen
A solder mask layer is applied to the PCB to protect the copper traces and prevent short circuits. This layer also provides insulation and improves the board’s aesthetic appearance. Silkscreen printing is then used to add labels, logos, and other markings to the board.
7. Surface Finish
The final step in HDI PCB manufacturing is applying a surface finish to the exposed copper pads. Common surface finishes include HASL (Hot Air Solder Leveling), ENIG (Electroless Nickel Immersion Gold), and OSP (Organic Solderability Preservative). The choice of surface finish depends on the specific requirements of the application, such as solderability, durability, and cost.
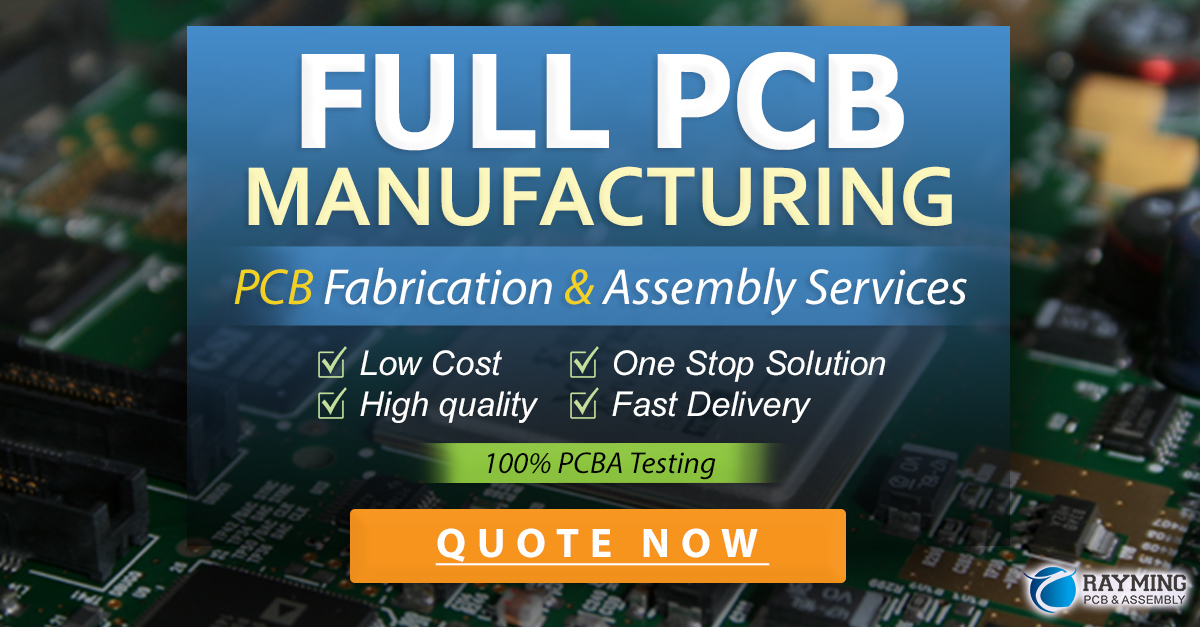
Choosing the Right HDI PCB Manufacturing Partner
Selecting the right HDI PCB manufacturing partner is essential for the success of your project. A reliable and experienced manufacturer can provide the expertise, quality, and support needed to bring your designs to life. When choosing an HDI PCB manufacturing partner, consider the following factors:
1. Experience and Expertise
Look for a manufacturer with a proven track record in HDI PCB fabrication. They should have experience working with a wide range of industries and applications, and be well-versed in the latest manufacturing technologies and processes.
2. Quality Control and Certifications
Ensure that your chosen manufacturer has strict quality control measures in place and holds relevant industry certifications, such as ISO 9001, UL, and RoHS. These certifications demonstrate their commitment to quality and compliance with international standards.
3. Advanced Equipment and Facilities
HDI PCB manufacturing requires state-of-the-art equipment and facilities. Choose a manufacturer that invests in the latest technology and maintains a clean, well-organized production environment. This ensures consistent quality and reliability of your PCBs.
4. Customer Support and Communication
Clear communication and responsive customer support are essential for a successful partnership. Look for a manufacturer that prioritizes customer satisfaction, offers personalized support, and maintains open lines of communication throughout the project.
5. Prototyping and Testing Services
A good HDI PCB manufacturing partner should offer prototyping and testing services to help you validate your designs before moving to full-scale production. This can save time and costs by identifying and addressing any issues early in the development process.
FAQ
1. What is the difference between HDI PCBs and traditional PCBs?
HDI PCBs have higher wiring density, smaller vias, and more layers compared to traditional PCBs. This allows for the creation of more compact and high-performance electronic devices.
2. What industries commonly use HDI PCBs?
HDI PCBs are widely used in industries such as consumer electronics, aerospace, medical devices, automotive, and telecommunications, where miniaturization, high performance, and reliability are crucial.
3. How do I choose the right materials for my HDI PCB?
The choice of materials depends on the specific requirements of your application, such as thermal stability, dielectric constant, and mechanical strength. Consult with your HDI PCB manufacturing partner to select the most suitable materials for your project.
4. What surface finishes are available for HDI PCBs?
Common surface finishes for HDI PCBs include HASL (Hot Air Solder Leveling), ENIG (Electroless Nickel Immersion Gold), and OSP (Organic Solderability Preservative). The choice of surface finish depends on factors such as solderability, durability, and cost.
5. How can I ensure the quality and reliability of my HDI PCBs?
To ensure the quality and reliability of your HDI PCBs, choose a reputable and experienced manufacturing partner with strict quality control measures and relevant industry certifications. Additionally, invest in thorough prototyping and testing to validate your designs before moving to full-scale production.
Conclusion
HDI PCBs have revolutionized the electronics industry, enabling the creation of smaller, more powerful, and more reliable devices. As the demand for advanced electronic products continues to grow, the importance of HDI PCBs will only increase. By understanding the intricacies of HDI PCB manufacturing and partnering with a trusted and experienced manufacturer, you can ensure the success of your projects and stay ahead of the competition in your industry.
HDI PCB Manufacturing Process | Key Steps |
---|---|
Design and Layout | – Create a detailed schematic – Specify component placement – Route connections between components |
Material Selection | – Choose high-quality substrates (e.g., FR-4, Rogers, Polyimide) – Select materials based on application requirements |
Lamination | – Laminate PCB layers together under high pressure and temperature – Ensure strong bond between layers |
Drilling and Plating | – Drill microvias using laser or mechanical techniques – Plate holes with copper for electrical connections |
Patterning and Etching | – Apply photoresist layer – Transfer desired pattern using photolithography – Etch away exposed copper |
Solder Mask and Silkscreen | – Apply solder mask to protect copper traces – Add labels, logos, and markings using silkscreen printing |
Surface Finish | – Apply surface finish to exposed copper pads (e.g., HASL, ENIG, OSP) – Choose finish based on solderability, durability, and cost |
When selecting an HDI PCB manufacturing partner, remember to consider their experience, expertise, quality control measures, advanced equipment, customer support, and prototyping and testing services. By making an informed decision and collaborating closely with your chosen manufacturer, you can bring your innovative electronic products to life and succeed in today’s competitive market.
Leave a Reply