What is Mixed Assembly?
Mixed assembly is a manufacturing process that combines both automated assembly lines and manual assembly stations. This approach offers several advantages over traditional assembly methods, allowing for greater flexibility, efficiency, and cost-effectiveness in the production process.
In a mixed assembly system, automated machines handle repetitive, high-volume tasks, while human workers focus on more complex, low-volume tasks that require dexterity, problem-solving skills, and adaptability. By leveraging the strengths of both machines and humans, mixed assembly can optimize production and improve overall product quality.
Key Components of Mixed Assembly
- Automated assembly lines
- Robotic Arms
- Conveyors
- Vision systems
-
Automated guided vehicles (AGVs)
-
Manual assembly stations
- Workbenches
- Hand tools
- Ergonomic equipment
-
Quality control instruments
-
Integration software
- Manufacturing execution systems (MES)
- Supervisory control and data acquisition (SCADA)
- Enterprise resource planning (ERP)
- Product lifecycle management (PLM)
Advantages of Mixed Assembly
1. Flexibility
One of the primary advantages of mixed assembly is its flexibility. By combining automated and manual processes, manufacturers can quickly adapt to changes in product design, production volume, and customer demands. This flexibility allows for:
- Faster product changeovers
- Easier customization and personalization
- Rapid prototyping and testing
- Efficient handling of high-mix, low-volume production
Case Study: Automotive Industry
In the automotive industry, mixed assembly has proven invaluable for managing the increasing complexity of modern vehicles. With the rise of electric and hybrid cars, manufacturers must be able to quickly adapt their production lines to accommodate new components and technologies.
For example, Tesla’s Fremont factory employs a mixed assembly approach, using automated robots for tasks like welding and painting, while human workers handle more complex tasks like final assembly and quality control. This allows Tesla to rapidly introduce new models and features, such as the Model Y and the Cybertruck, without requiring a complete overhaul of their production lines.
2. Efficiency
Mixed assembly can significantly improve production efficiency by optimizing the use of both automated and manual processes. Automated machines excel at handling repetitive, high-volume tasks with consistent quality and speed, while human workers can efficiently tackle more complex, low-volume tasks that require problem-solving and adaptability.
By assigning tasks to the most suitable resource, whether machine or human, mixed assembly can:
- Reduce cycle times
- Minimize downtime and bottlenecks
- Improve resource utilization
- Increase overall equipment effectiveness (OEE)
Case Study: Electronics Manufacturing
In the electronics industry, mixed assembly has become increasingly important for managing the high-mix, low-volume production of printed circuit boards (PCBs) and electronic components. Automated pick-and-place machines can quickly populate PCBs with standard components, while human workers handle the placement of odd-shaped or delicate components, as well as final inspection and testing.
Foxconn, a major contract manufacturer for companies like Apple and Dell, employs a mixed assembly approach in its factories. By combining automated SMT Lines with manual assembly stations, Foxconn can efficiently produce a wide range of electronic products, from smartphones to servers, while maintaining high quality standards and rapid time-to-market.
3. Cost-Effectiveness
Mixed assembly can help manufacturers reduce costs and improve profitability by optimizing labor and capital investments. By automating high-volume, repetitive tasks, companies can reduce labor costs and minimize the risk of human error. At the same time, by employing human workers for more complex, low-volume tasks, manufacturers can avoid the high capital costs associated with fully automated systems.
This balance of labor and capital allows for:
- Lower overall production costs
- Reduced inventory and work-in-progress (WIP)
- Improved return on investment (ROI)
- Greater scalability and adaptability
Case Study: Aerospace Industry
In the aerospace industry, mixed assembly has proven cost-effective for producing complex, high-value components and systems. Automated machines can handle tasks like drilling, riveting, and fastening, while human workers focus on more intricate tasks like wiring, plumbing, and final assembly.
Boeing, for example, uses a mixed assembly approach in its 777 and 787 Dreamliner production lines. Automated machines handle tasks like fuselage joining and wing assembly, while human workers install interiors, avionics, and other systems. This allows Boeing to efficiently produce high-quality aircraft while managing costs and adapting to customer requirements.
4. Quality Improvement
Mixed assembly can lead to significant improvements in product quality by leveraging the strengths of both automated and manual processes. Automated machines can consistently perform tasks with high precision and repeatability, reducing the risk of human error and ensuring uniform quality across large production runs. Human workers, on the other hand, can provide valuable quality control, identifying and correcting issues that machines may miss.
This combination of machine precision and human oversight can result in:
- Reduced defect rates
- Improved product reliability and durability
- Higher customer satisfaction
- Enhanced brand reputation
Case Study: Medical Device Manufacturing
In the medical device industry, product quality is of utmost importance, as defects can have serious consequences for patient safety and well-being. Mixed assembly has become a critical approach for ensuring the highest quality standards in medical device production.
Medtronic, a leading medical device manufacturer, employs a mixed assembly approach in its production facilities. Automated machines handle tasks like injection molding, laser welding, and packaging, while human workers focus on tasks like manual assembly, inspection, and testing. This allows Medtronic to produce high-quality, life-saving devices like pacemakers, insulin pumps, and surgical instruments, while meeting strict regulatory requirements and customer expectations.
Implementing Mixed Assembly
To successfully implement a mixed assembly system, manufacturers must carefully consider several key factors:
- Task allocation
- Identify which tasks are best suited for automation and which require human intervention
- Analyze task complexity, volume, and variability
-
Consider ergonomics and worker safety
-
Equipment selection
- Choose automated machines that can handle the required tasks with precision and reliability
- Ensure compatibility between automated and manual processes
-
Invest in ergonomic tools and workstations for human workers
-
Process design
- Optimize the layout and flow of the assembly line
- Minimize material handling and transportation
-
Incorporate lean manufacturing principles, such as just-in-time (JIT) and continuous improvement
-
Workforce training
- Provide comprehensive training for both machine operators and manual assembly workers
- Foster a culture of teamwork and communication between automated and manual processes
- Encourage continuous learning and skill development
Best Practices for Mixed Assembly
- Regularly assess and adjust the balance between automated and manual processes
- Implement robust quality control measures, including machine vision systems and human inspection
- Utilize data analytics and machine learning to optimize production and identify improvement opportunities
- Foster a culture of innovation and continuous improvement, encouraging workers to suggest process enhancements
- Prioritize worker safety and ergonomics, providing appropriate training and equipment
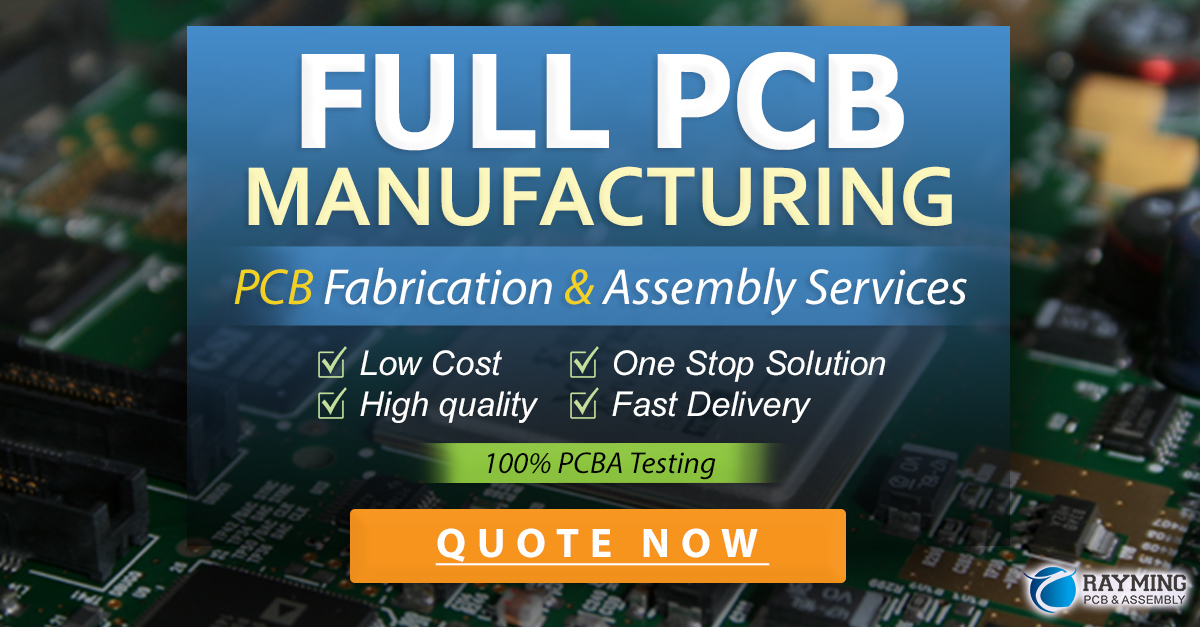
Frequently Asked Questions (FAQ)
1. How does mixed assembly differ from fully automated assembly?
Mixed assembly combines both automated and manual processes, while fully automated assembly relies entirely on machines and robots. Mixed assembly offers greater flexibility and adaptability, allowing for easier handling of high-mix, low-volume production and complex tasks that require human intervention.
2. What types of industries can benefit from mixed assembly?
Mixed assembly can be applied in a wide range of industries, including:
- Automotive
- Electronics
- Aerospace
- Medical devices
- Consumer goods
- Industrial equipment
Any industry that requires a balance of high-volume, repetitive tasks and low-volume, complex tasks can benefit from a mixed assembly approach.
3. How can mixed assembly improve product quality?
Mixed assembly leverages the strengths of both automated machines and human workers to improve product quality. Automated machines ensure consistent precision and repeatability, while human workers provide valuable quality control, identifying and correcting issues that machines may miss. This combination of machine precision and human oversight can lead to reduced defect rates, improved product reliability, and higher customer satisfaction.
4. What are the key considerations when implementing a mixed assembly system?
When implementing a mixed assembly system, manufacturers must carefully consider task allocation, equipment selection, process design, and workforce training. It is essential to identify which tasks are best suited for automation and which require human intervention, choose compatible equipment, optimize the assembly line layout, and provide comprehensive training for both machine operators and manual assembly workers.
5. How can manufacturers ensure the success of a mixed assembly implementation?
To ensure the success of a mixed assembly implementation, manufacturers should follow best practices such as regularly assessing and adjusting the balance between automated and manual processes, implementing robust quality control measures, utilizing data analytics and machine learning, fostering a culture of innovation and continuous improvement, and prioritizing worker safety and ergonomics.
Conclusion
Mixed assembly offers a powerful approach for manufacturers seeking to optimize production, improve quality, and reduce costs. By combining the strengths of both automated machines and human workers, mixed assembly provides the flexibility, efficiency, and adaptability needed to succeed in today’s fast-paced, highly competitive manufacturing landscape.
As technology continues to advance and customer demands evolve, the adoption of mixed assembly is likely to grow across a wide range of industries. By carefully considering the key factors and best practices outlined in this article, manufacturers can successfully implement mixed assembly systems and reap the numerous benefits they offer.
Ultimately, the success of mixed assembly lies in finding the right balance between automation and human intervention, leveraging the unique capabilities of each to create a more efficient, flexible, and cost-effective production process. As manufacturers continue to explore and refine this approach, mixed assembly will undoubtedly play an increasingly vital role in shaping the future of manufacturing.
Leave a Reply