Introduction to M4 Mounting Holes
M4 mounting holes are commonly used in various industries for securing components, assemblies, and structures. These holes are designed to accommodate M4 screws, which have a nominal diameter of 4 mm. Understanding the dimensions and specifications of M4 mounting holes is crucial for engineers, designers, and technicians working on projects that require precise and secure fastening.
In this comprehensive article, we will explore the various aspects of M4 mounting hole dimensions, including their size, tolerances, thread specifications, and best practices for designing and implementing them in different applications.
M4 Screw Specifications
Before diving into the dimensions of M4 mounting holes, it is essential to understand the specifications of M4 screws. M4 screws are part of the metric screw thread system, which is widely used in Europe and many other parts of the world. The “M” in M4 stands for “metric,” while the number “4” represents the nominal diameter of the screw in millimeters.
M4 screws have the following specifications:
- Nominal diameter: 4 mm
- Pitch: 0.7 mm (standard)
- Thread angle: 60°
- Minor diameter: 3.242 mm
- Major diameter: 4.000 mm
- Tensile stress area: 8.78 mm²
These specifications are important to consider when designing M4 mounting holes, as they directly influence the hole dimensions and tolerances required for a proper fit.
M4 Mounting Hole Dimensions
Clearance Holes
Clearance holes are used when the screw is not required to engage with the threads of the hole. These holes allow the screw to pass through freely, and the screw is typically secured using a nut on the opposite side. The dimensions of M4 clearance holes are as follows:
Dimension | Value |
---|---|
Nominal diameter | 4.5 mm |
Tolerance | +0.2 mm / -0 mm |
Recommended drill size | 4.5 mm |
To create an M4 clearance hole, a 4.5 mm drill bit is commonly used. The slightly larger diameter allows for easy insertion of the M4 screw while still providing a snug fit.
Tapped Holes
Tapped holes, also known as threaded holes, are used when the screw is required to engage with the threads of the hole directly. In this case, the hole is pre-threaded to match the pitch and thread profile of the M4 screw. The dimensions of M4 tapped holes are as follows:
Dimension | Value |
---|---|
Nominal diameter | 4.0 mm |
Pitch | 0.7 mm |
Minor diameter | 3.3 mm |
Drill size for tapping | 3.3 mm |
Tapping size | M4 x 0.7 |
To create an M4 tapped hole, a 3.3 mm drill bit is used to create the initial hole, followed by an M4 x 0.7 tap to cut the threads into the hole. It is essential to use the correct tapping drill size and tap to ensure a proper fit and engagement of the M4 screw.
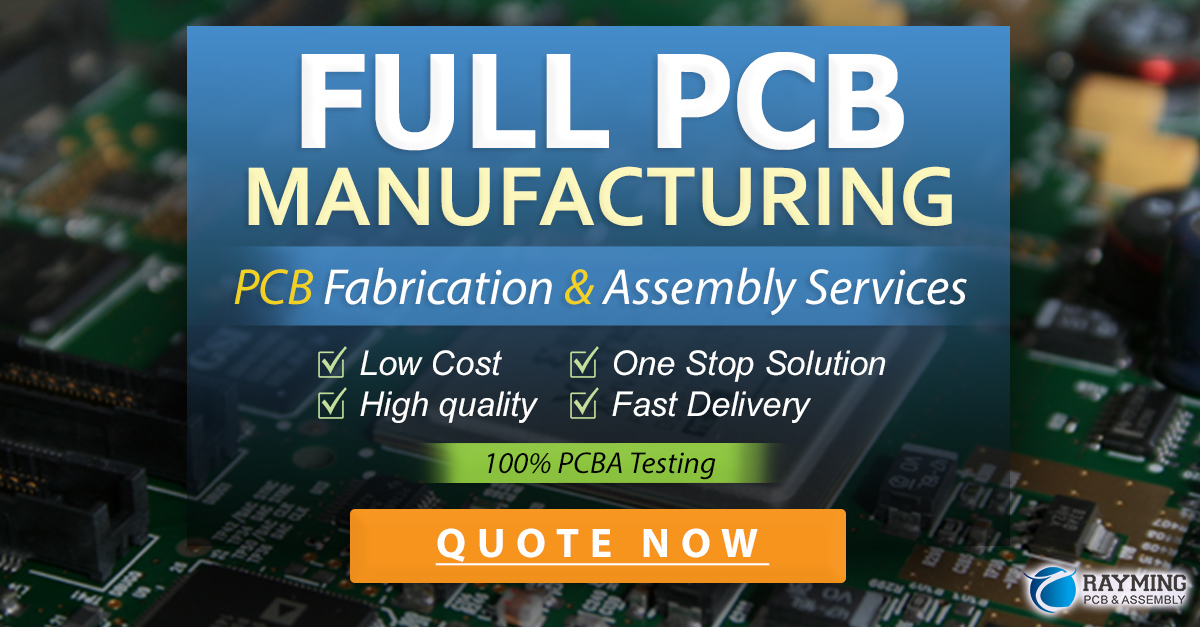
Tolerances and Fit
When designing M4 mounting holes, it is crucial to consider the tolerances and fit required for the specific application. Tolerances refer to the acceptable variation in the hole dimensions, while fit describes how closely the screw and hole mate together.
Clearance Hole Tolerances
For M4 clearance holes, a positive tolerance of +0.2 mm is typically used. This means that the hole diameter can be up to 0.2 mm larger than the nominal 4.5 mm diameter, but not smaller. The positive tolerance allows for easier insertion of the screw and accommodates any minor variations in screw dimensions.
Tapped Hole Tolerances
Tapped holes require tighter tolerances to ensure proper engagement of the screw threads. The tolerance for M4 tapped holes depends on the class of fit required. The most common classes of fit for metric threads are:
- 6H: Standard fit for general applications
- 6G: Close fit for more precise applications
The 6H class of fit allows for a slightly looser thread engagement, while the 6G class of fit provides a tighter engagement. The choice of fit class depends on the specific requirements of the application, such as the need for high strength, frequent disassembly, or resistance to vibration.
Design Considerations
When incorporating M4 mounting holes into a design, there are several key factors to consider to ensure optimal performance and reliability.
Material Selection
The material of the component or structure containing the M4 mounting hole plays a significant role in determining the hole dimensions and tolerances. Different materials have varying strengths, hardness, and machinability, which can affect the ability to create precise and stable holes.
For example, softer materials like plastics may require larger hole diameters to accommodate potential deformation during screw insertion. On the other hand, harder materials like metals can maintain tighter tolerances and provide a more secure fit.
Thread Engagement Length
The thread engagement length refers to the depth of the threaded portion of the hole that engages with the screw threads. Adequate thread engagement is necessary to ensure a strong and secure connection.
For M4 screws, a minimum thread engagement length of 4.5 mm (1.5 times the screw diameter) is recommended for most applications. However, in cases where higher loads or vibrations are expected, a longer thread engagement may be necessary.
Counterbores and Countersinks
In some applications, it may be desirable to use counterbores or countersinks in conjunction with M4 mounting holes. Counterbores are used to create a flat surface for the screw head to sit flush with the surface of the component, while countersinks create a angled surface for flush fitting of countersunk screw heads.
When using counterbores or countersinks, it is important to consider the dimensions of the screw head and ensure that the counterbore or countersink diameter and depth are appropriate for the specific screw being used.
Hole Spacing and Edge Distance
When designing multiple M4 mounting holes in a component or assembly, it is important to consider the spacing between the holes and the distance from the holes to the edges of the component.
Adequate hole spacing is necessary to ensure that the material between the holes has sufficient strength to withstand the loads and stresses imposed by the screws. The minimum recommended spacing between M4 mounting holes is 2 times the screw diameter (8 mm).
Similarly, sufficient edge distance is required to prevent the material from cracking or failing due to the stress concentrations around the holes. The minimum recommended edge distance for M4 mounting holes is 1.5 times the screw diameter (6 mm) from the edge of the component.
Best Practices for M4 Mounting Holes
To ensure the best performance and reliability of M4 mounting holes, consider the following best practices:
- Use the appropriate drill sizes and taps for creating clearance and tapped holes.
- Ensure that the holes are perpendicular to the surface to prevent misalignment and stress concentrations.
- Deburr the holes after drilling and tapping to remove any sharp edges that could cause stress concentrations or damage to the screw threads.
- Use appropriate lubrication when tapping holes to reduce friction and improve thread quality.
- Consider using thread-locking compounds or mechanical locking methods to prevent loosening of the screws under vibration or dynamic loads.
- Follow the recommended hole spacing and edge distance guidelines to ensure the structural integrity of the component.
- Use appropriate torque values when tightening M4 screws to prevent over-tightening and damaging the threads or components.
Frequently Asked Questions (FAQ)
-
Q: What is the difference between a clearance hole and a tapped hole for M4 screws?
A: A clearance hole is a plain hole that allows the M4 screw to pass through freely, while a tapped hole has pre-cut threads that engage with the threads of the M4 screw. -
Q: What is the recommended drill size for creating an M4 clearance hole?
A: The recommended drill size for creating an M4 clearance hole is 4.5 mm. -
Q: What is the minimum recommended thread engagement length for M4 screws?
A: The minimum recommended thread engagement length for M4 screws is 4.5 mm, which is equal to 1.5 times the screw diameter. -
Q: How far apart should M4 mounting holes be spaced?
A: The minimum recommended spacing between M4 mounting holes is 2 times the screw diameter, which equals 8 mm. -
Q: What is the purpose of using a counterbore or countersink with M4 mounting holes?
A: Counterbores and countersinks are used to create a flush surface for the screw head to sit in, providing a more aesthetically pleasing and streamlined appearance.
Conclusion
M4 mounting holes are a crucial aspect of many engineering and manufacturing applications. By understanding the dimensions, tolerances, and best practices associated with these holes, designers and engineers can ensure that their components and assemblies are securely fastened and able to withstand the required loads and stresses.
When designing M4 mounting holes, it is important to consider factors such as material selection, thread engagement length, hole spacing, and edge distance. By following the recommended guidelines and best practices outlined in this article, designers can create robust and reliable fastening solutions using M4 screws.
As with any engineering design, it is always important to consider the specific requirements and constraints of the application and to consult with experienced professionals when necessary. By taking a thoughtful and informed approach to M4 mounting hole design, engineers and manufacturers can create high-quality products that meet the needs of their customers and end-users.
Leave a Reply