Introduction to Power Bank PCBs
A power bank PCB (printed circuit board) is the main component that enables portable Battery Chargers to store energy and charge various electronic devices on the go. Power banks have become an essential accessory for smartphone and tablet users who need extra battery life throughout the day.
Designing and assembling your own custom power bank PCB allows you to create a compact charger tailored to your specific device charging needs. In this guide, we’ll walk through the key components and steps required to make a DIY Power Bank circuit on a PCB.
Power Bank PCB Components
To build a functional power bank PCB, you’ll need the following main components:
Component | Description |
---|---|
Lithium-ion or LiPo battery | Rechargeable battery cell to store energy, typically 3.7V |
Boost Converter | DC-to-DC step-up converter to increase battery voltage to 5V USB output |
Battery protection IC | Protects battery from overcharge, over-discharge, and short circuit |
USB connector | Female USB-A port for connecting devices to charge |
Micro USB connector | Male micro USB port for charging the power bank battery |
Power switch | Slide or button switch to turn power bank on/off |
LED indicators | Show remaining battery capacity and charging status |
Resistors, capacitors | Supporting components for voltage regulation and filtering |
PCB | Printed circuit board to mount and connect components |
Choosing a Battery
The battery is the key component that determines your power bank’s capacity and size. Lithium-ion and lithium-polymer (LiPo) cells are most commonly used due to their high energy density and rechargeability.
Typical power bank battery capacities range from 2000mAh up to 20,000+mAh for high-capacity models. A rough estimate is that 2000-3000mAh is sufficient to fully charge most smartphones once.
Some popular battery sizes and configurations for PCB-mounted power banks include:
Config | Cell Type | Nominal Voltage | Typical Capacity | PCB layout |
---|---|---|---|---|
1S1P | 18650 Li-ion | 3.7V | 2600mAh | Single cell |
1S2P | 18650 Li-ion | 3.7V | 5200mAh | Side-by-side |
2S1P | 18650 Li-ion | 7.4V | 2600mAh | Stacked vertically |
1S | 103450 LiPo | 3.7V | 1800mAh | Flat pack |
The battery configuration you choose will influence your PCB layout and the required supporting circuitry. We’ll focus on a simple 1S 18650 cell power bank for this tutorial.
Designing the Power Bank Circuit
Battery Charging Circuit
The first stage is a battery charging circuit to recharge the Li-ion cell from a 5V USB power source. This requires a special Li-ion battery charger IC that safely controls the constant-current and constant-voltage (CC/CV) charging profile.
Some common battery charger ICs suitable for 1-cell Li-ion power banks:
- TP4056 – 1A linear charger
- TC4056A – 1A linear charger
- TP5000 – 2A switch-mode charger
- MCP73831 – 500mA linear charger
These ICs only require a few external resistors and capacitors to set the charge current and termination threshold.
Here’s a typical TP4056 charging circuit:
[TP4056 typical application circuit diagram]
The key components are:
- R1, R2: Charge current setting resistors. A lower value for R1 increases charge current.
- C1, C2: Input and output filtering capacitors to reduce noise.
- D1: Charge status LED. Lights up when charging, turns off when done.
- Vbat, GND: Positive and negative terminals of Li-ion battery.
5V Boost Converter
The single Li-ion battery only provides 3.7V nominally, but 5V is required to charge USB devices. Therefore, the second stage is a boost (step-up) DC-DC converter to regulate the battery voltage up to a constant 5V.
Many different boost converter ICs can be used, but some good options for power banks are:
- MT3608 – Up to 28V/4A output
- XL6009 – Adjustable up to 35V/4A
- SX1308 – Up to 28V/2A
These ICs require an inductor, diode, and capacitors for the boost conversion, plus feedback resistors to set the output voltage.
An example MT3608 boost converter circuit:
[MT3608 typical application circuit diagram]
The main components are:
- L1: Boost inductor. Higher inductance improves efficiency but increases size.
- D1: Schottky diode to prevent backflow from output to input.
- C1, C2: Input and output filtering capacitors. C2 should be low-ESR.
- R1, R2: Voltage feedback divider. Ratio of R1/R2 sets output voltage.
- EN: Enable pin, tie to Vbat to enable the converter.
Battery Protection
Lithium batteries can be dangerous if overcharged, over-discharged, or shorted out. Therefore, the power bank PCB needs a battery protection circuit to monitor the cell voltage and current.
Dedicated battery protection ICs like the DW01 and FS312 are commonly used. They sit between the battery and the boost converter, and will disconnect the load if an over-current or under/over-voltage condition is detected.
Here’s a typical DW01 protection circuit:
[DW01 battery protection circuit diagram]
The key parts are:
- U1: DW01 protection IC to monitor voltage and current
- U2: Dual MOSFET to disconnect battery when triggered
- R1, R2: Resistor divider to set overcharge detection voltage
- R3, C1: Over-current detection delay time constant
- T1, T2: Thermistor to monitor battery temperature
Final Power Bank PCB Assembly
To complete the power bank, the last step is to combine the charging, boost, and protection circuits on a single PCB along with the necessary connectors and switches.
Here’s a simplified diagram showing how the subsystems are connected:
[Block diagram of power bank PCB]
Some additional considerations:
- Input USB: Micro or Type-C USB port for charging the power bank. Should connect to Vbus and GND of charger IC.
- Output USB: One or more Type-A USB ports to plug in devices. Connect to 5V output and GND of boost converter.
- Power switch: SPST slide or push-button switch in series with positive battery terminal to turn the bank on or off and prevent unwanted discharge.
- LED indicators: Connect LEDs (often in a 3 or 4-bar arrangement) via a resistor divider to the battery voltage to show remaining charge level.
After designing the schematic and PCB layout in EDA software, you can order the board for fabrication. Finally, solder on all the components, plug in a battery, and test it out!
Power Bank PCB Assembly Tips
- Use a good soldering iron, solder, and flux. Lead-free solder requires higher temps.
- Double-check polarities before soldering, especially for the battery connector.
- Include test points for easy debugging and take measurements while powering up the board for the first time.
- Ensure the switches and USB ports are solidly mounted and have strain relief.
- Consider adding battery pack mounting holes or brackets to the PCB.
- Program custom charge parameters and safety limits if your ICs allow it.
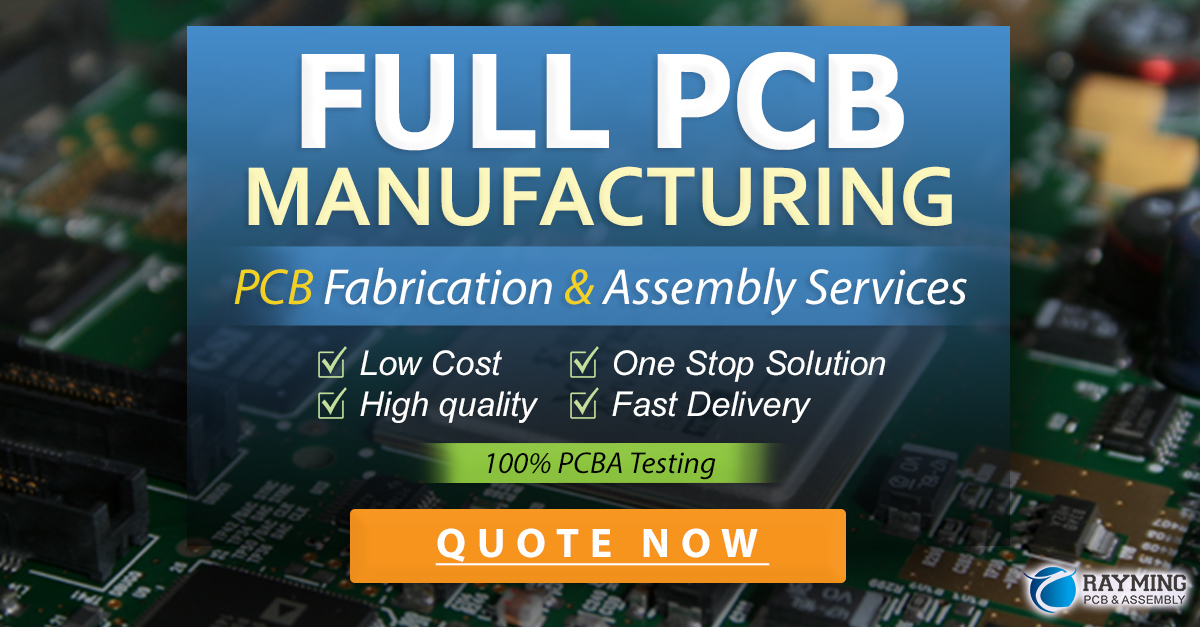
FAQ
What is the typical efficiency of a DIY power bank?
Most DIY power banks achieve around 65-85% efficiency end-to-end, meaning 65-85% of the energy from the wall charger makes it into the device you’re charging. The losses come from the boost converter, protection circuit, and cable resistance. Using quality components and keeping PCB traces short and wide helps maximize efficiency.
How long does it take to charge a power bank?
Charge time depends on the battery capacity and the charge current supported by the charger IC. For example, a 2000mAh battery would take about 2 hours to charge at 1A, or 4 hours at 500mA. Some fast-charge ICs can charge even quicker. Check the IC datasheet for info on setting the charge current.
Can I use salvaged batteries from old devices?
It’s generally not recommended, as you don’t know the history or health of salvaged Li-ion cells. For safety and reliability, it’s best to buy new cells from a reputable vendor. Mismatched or degraded cells can be a fire hazard in a power bank.
What is the typical lifespan of a DIY power bank?
The lifespan mainly depends on the battery, which is typically rated for 300-1000 charge/discharge cycles before capacity drops to 70-80% of original. With moderate use, a well-made DIY bank can last 3-5 years. The electronics themselves can last much longer if not physically damaged.
What are some advanced features to consider adding?
- USB-C PD fast charging with a compatible boost IC and USB-C port
- Qi wireless charging by integrating a wireless power transmitter coil and module
- Digital battery level display instead of just LEDs
- Solar charging with a small solar panel and compatible charge IC
- Multi-cell balancing for larger battery packs
- Adjustable output voltage for various devices
Conclusion
Building your own power bank PCB can be a fun and educational electronics project. With some basic soldering skills, you can create a custom USB charger for everyday use.
By understanding the key components like the battery, protection IC, charger, and boost converter, you can design a circuit optimized for your desired size and charging specs. Following best practices for battery safety and PCB layout will result in a reliable DIY power bank.
While DIY power banks aren’t necessarily cheaper than commercial ones, the ability to pick quality parts and customize the features makes it a worthwhile endeavor for electronics enthusiasts. So grab some cells and a PCB, and start powering your projects!
Leave a Reply