How Does a Boost Converter Work?
The basic principle of a Boost converter consists of 2 distinct states:
-
In the On-state, the switch S is closed, resulting in an increase in the inductor current.
-
In the Off-state, the switch is open and the only path offered to inductor current is through the diode D, the capacitor C and the load R. This results in transferring the energy accumulated during the On-state into the capacitor.
The input current is the same as the inductor current. So it is not discontinuous as in the buck converter and the requirements on the input filter are relaxed compared to a buck converter.
On State Operation
When the switch is closed, the inductor gets connected to the input voltage source. This voltage source starts to energize the inductor and the inductor current increases with a rate proportional to the input voltage divided by the inductance value L:
dI/dt = Vin/L
The current through the inductor IL increases linearly and the inductor stores the energy in the form of magnetic energy. During this state, the capacitor supplies energy to the load.
Off State Operation
When the switch is opened, the inductor gets connected to the output load and the capacitor, so energy stored in the inductor is transferred to the capacitor and the load. The voltage across the inductor is (Vout – Vin) and the current through the inductor falls linearly with a slope equal to (Vout – Vin)/L.
The diode D is forward biased and conducts the inductor current to charge the capacitor and provide current to the load.
The output voltage can be calculated as follows in the steady state condition. The change in current through the inductor during the On-state must be equal to the change in current during the Off-state:
ΔILon = ΔILoff
From this, the output voltage can be expressed as:
Vout = Vin / (1-D)
where D is the duty cycle and represents the fraction of the commutation period T during which the switch is On. Therefore, D ranges between 0 and 1.
So if we assume there is no power loss in the converter, by equating the input and output powers we can write:
Vin × Iin = Vout × Iout
And substituting for Vout from the previous equation we get:
Iout = Iin × (1-D)
From these equations it can be seen that the output voltage is always higher than the input voltage (as the duty cycle goes from 0 to 1), and that the output current is lower than the input current.
Boost Converter Design Considerations
There are several things to consider when designing a boost converter:
Inductor Selection
The inductor is one of the most important components in a boost converter. Its size and characteristics have a significant impact on the converter performance.
The inductor value is selected based on the desired ripple current through it. A larger inductor value reduces ripple current and results in less output voltage ripple, however it also increases the physical size of the inductor. A good rule of thumb is to choose an inductor value that results in a ripple current of about 20-40% of the average inductor current. The ripple current can be calculated as:
ΔIL = (Vin × D) / (fs × L)
Where fs is the switching frequency.
Output Capacitor Selection
The output capacitor is selected to handle the output voltage ripple requirements. The output voltage ripple is largely due to the charging and discharging of the output capacitor and is a function of the capacitor’s equivalent series resistance (ESR). A good starting point is to choose a minimum capacitance value that can handle the maximum output current while maintaining the desired output voltage ripple. The required minimum capacitance can be calculated as:
Cout(min) = (Iout × D) / (fs × ΔVout)
Where ΔVout is the desired peak-to-peak output voltage ripple.
MOSFET and Diode Selection
The main switch in a boost converter is typically a MOSFET, while the diode is typically a Schottky diode. The MOSFET is chosen based on its maximum drain-to-source voltage (it must be higher than the output voltage), current rating, and on-resistance (which impacts efficiency).
The diode must be selected with a peak inverse voltage (PIV) rating higher than the output voltage. The diode’s current rating must be higher than the peak inductor current. Schottky diodes are commonly used due to their low forward voltage drop and fast recovery times.
Boost Converter Applications
Boost converters are used in a variety of applications:
- Where a higher output voltage than input is required
- Battery powered systems where the battery voltage drops over time
- Regenerative braking of DC motors
- Solar cell and fuel cell applications where voltage needs to be increased
Some specific applications include:
White LED Drivers
White LEDs require a constant current to operate optimally and have a forward voltage higher than typical battery voltages. A boost converter provides both constant current and increased voltage.
5V to 12V Converters
Many electronic systems require 12V for peripheral devices but only have a 5V bus voltage available. A boost converter steps up the 5V to the required 12V.
Battery Chargers
Lithium-ion batteries typically require 4.2V to fully charge but the power source is often a lower voltage. A boost converter steps up the voltage to allow the battery to fully charge.
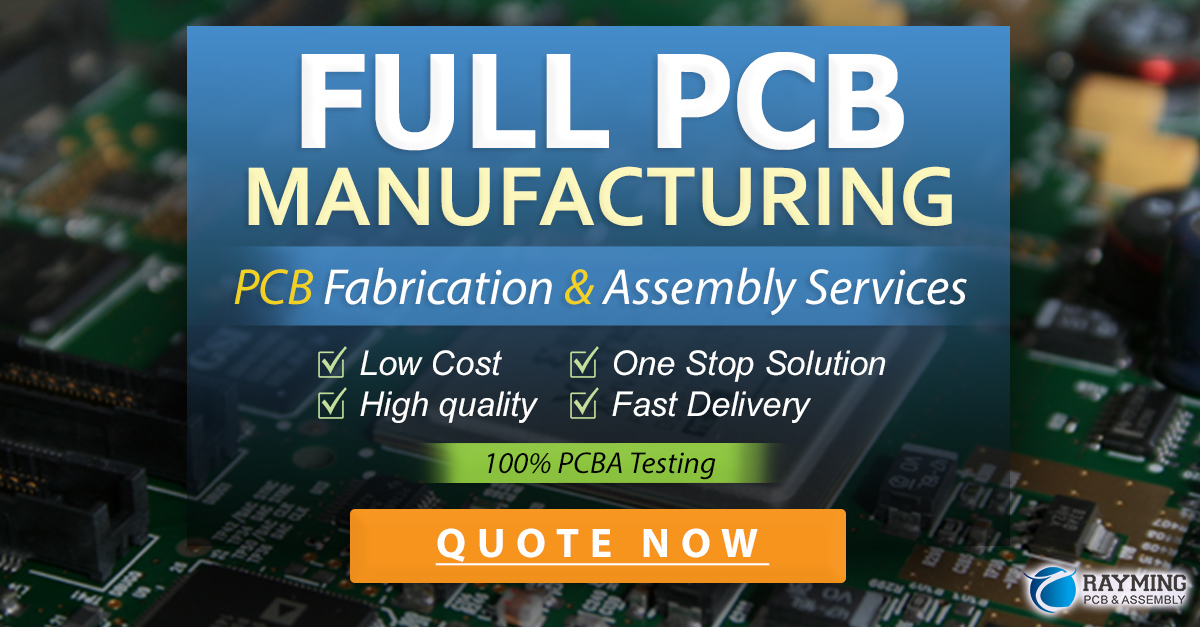
Boost Converter Efficiency
The efficiency of a boost converter is defined as the output power divided by the input power:
η = Pout / Pin = (Vout × Iout) / (Vin × Iin)
Where η is the efficiency, typically represented as a percentage.
The efficiency of a real boost converter is reduced by the losses in the circuit elements, including:
- Inductor losses (copper loss and core loss)
- Capacitor losses (ESR)
- Switching losses in the MOSFET and diode
- Conduction losses in the MOSFET, inductor, and diode
- Controller IC power consumption
Typically, boost converters operate at 85% to 95% efficiency, although they can be over 95% efficient with careful design.
Boost Converter Frequently Asked Questions (FAQ)
1. What is the difference between a boost converter and a buck converter?
A boost converter steps up the input voltage to a higher output voltage, while a buck converter steps down the input voltage to a lower output voltage.
2. Can a boost converter be used for voltage regulation?
Yes, a boost converter can be used for voltage regulation. The output voltage is regulated by varying the duty cycle of the switch.
3. How do I select the inductor for a boost converter?
The inductor is selected based on the desired ripple current, which is usually chosen to be between 20% and 40% of the average inductor current. The exact inductor value can then be calculated based on the input voltage, output voltage, and switching frequency.
4. What is the efficiency of a typical boost converter?
The efficiency of a well-designed boost converter is typically between 85% and 95%, although it can exceed 95% with careful design and component selection.
5. What are some common applications for boost converters?
Common applications for boost converters include LED drivers, battery chargers, and power supplies where the output voltage needs to be higher than the input voltage. They are also used in regenerative braking systems and in solar power systems.
Here is a summary table of the key characteristics of boost converters:
Parameter | Description |
---|---|
Input Voltage | Lower than output voltage |
Output Voltage | Higher than input voltage |
Efficiency | 85% to 95% typical |
Key Components | Inductor, MOSFET switch, diode, capacitor |
Typical Applications | LED drivers, battery chargers, 5V to 12V converters |
In conclusion, boost converters are a type of switched-mode power supply that steps up the input voltage to produce a higher output voltage. They operate by storing energy in an inductor when the switch is closed and transferring that energy to the output when the switch is opened. Careful selection of the inductor, capacitor, MOSFET switch, and diode is necessary to ensure efficient and reliable operation. Boost converters are widely used in battery-powered devices, LED drivers, and other applications where a higher voltage is needed than is available from the input source.
Leave a Reply