What is FR4 PCB Material?
FR4 (Flame Retardant 4) is a composite material made from woven fiberglass cloth with an epoxy resin binder. It is the most common base material used for the production of printed circuit boards (PCBs). FR4 PCBs are known for their excellent mechanical, thermal, and electrical properties, making them suitable for a wide range of applications in the electronics industry.
Composition of FR4
FR4 is composed of two main components:
- Fiberglass cloth: This provides the structural strength and dimensional stability to the PCB.
- Epoxy resin: The resin binds the fiberglass layers together and provides insulation between the conductive copper layers.
The combination of these materials results in a strong, rigid, and flame-retardant substrate for PCBs.
Properties of FR4 PCBs
FR4 PCBs exhibit several desirable properties that make them the preferred choice for most electronic applications:
Mechanical Properties
- High tensile strength
- Good flexural strength
- Excellent dimensional stability
- Resistance to cracking and breaking
Thermal Properties
- Glass transition temperature (Tg) around 135°C
- Suitable for lead-free soldering processes
- Low thermal expansion coefficient
Electrical Properties
- Good dielectric constant (4.5 at 1 MHz)
- Low dissipation factor (0.02 at 1 MHz)
- High insulation resistance
- Suitable for high-frequency applications
Advantages of Using FR4 PCBs
1. Cost-effectiveness
FR4 is widely available and relatively inexpensive compared to other PCB materials. The raw materials used in FR4 production are readily accessible, and the manufacturing process is well-established, contributing to its cost-effectiveness.
2. Versatility
FR4 PCBs can be used in a wide range of applications, from consumer electronics to industrial equipment and aerospace systems. They can be manufactured in various thicknesses, copper weights, and layer counts to meet specific design requirements.
3. Reliability
The combination of fiberglass and epoxy resin provides excellent mechanical strength and durability to FR4 PCBs. They can withstand shock, vibration, and thermal stress, ensuring reliable performance in harsh environments.
4. Flame Retardancy
As the name suggests, FR4 is flame-retardant. This property is essential for ensuring the safety of electronic devices and compliance with industry standards and regulations.
5. Ease of Fabrication
FR4 PCBs are compatible with standard PCB manufacturing processes, including drilling, routing, and plating. The material is easy to work with and allows for the creation of complex PCB designs with fine features and high-density interconnects.
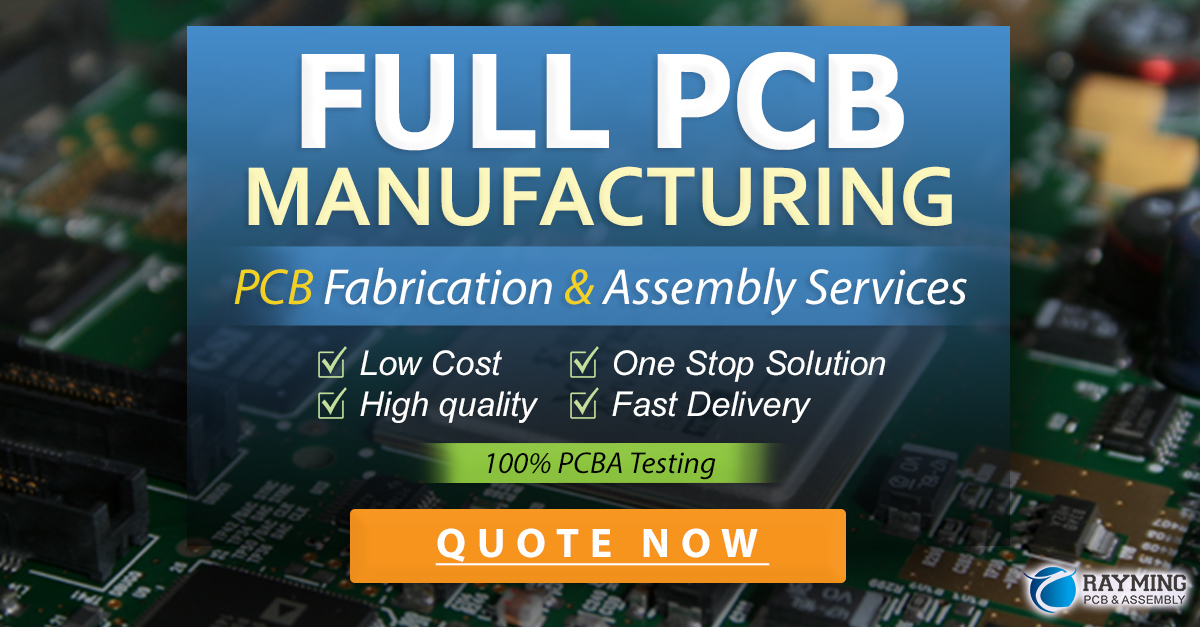
Applications of FR4 PCBs
FR4 PCBs find applications in various industries and products, such as:
- Consumer electronics (smartphones, laptops, gaming consoles)
- Telecommunications equipment (routers, switches, modems)
- Automotive electronics (engine control units, infotainment systems)
- Medical devices (patient monitors, diagnostic equipment)
- Industrial control systems (PLCs, HMIs, sensors)
- Aerospace and defense systems (avionics, radar, communication devices)
FR4 PCB Grades and Variants
FR4 PCBs come in different grades and variants to cater to specific application requirements:
Standard FR4
This is the most common type of FR4 PCB, suitable for general-purpose applications. It has a Tg of 135°C and can withstand lead-free Soldering Temperatures.
High Tg FR4
High Tg FR4 has a glass transition temperature of 170°C or higher. It is used in applications that require better thermal stability and resistance to higher temperatures.
Halogen-free FR4
Halogen-free FR4 is made without the use of brominated flame retardants. It is more environmentally friendly and complies with stringent green initiatives and regulations.
FR4 with High-Performance Materials
Some FR4 variants incorporate high-performance materials, such as:
- High-speed/low-loss materials for improved signal integrity
- Thermally conductive materials for better heat dissipation
- Controlled impedance materials for precise impedance control
These specialized FR4 PCBs cater to specific application requirements and enhance the overall performance of the end product.
FR4 PCB Manufacturing Process
The manufacturing process for FR4 PCBs involves several key steps:
-
Material preparation: The FR4 laminate is cut to the required size, and the copper foil is cleaned and treated for better adhesion.
-
Layup and lamination: The FR4 layers are stacked with the copper foil and other materials (prepreg, solder mask, etc.) and laminated under high pressure and temperature.
-
Drilling: Holes are drilled through the laminated board for component mounting and interconnections.
-
Plating: The drilled holes are plated with copper to create electrical connections between layers.
-
Patterning: The desired circuit pattern is transferred onto the copper layers using photolithography and etching processes.
-
Solder mask and silkscreen: A solder mask is applied to protect the copper traces, and a silkscreen layer is added for component labeling and identification.
-
Surface finish: A surface finish (HASL, ENIG, OSP, etc.) is applied to the exposed copper areas to prevent oxidation and improve solderability.
-
Cutting and routing: The manufactured panel is cut and routed into individual PCBs.
-
Quality control and testing: The PCBs undergo various quality control checks and electrical tests to ensure functionality and reliability.
Comparison of FR4 with Other PCB Materials
While FR4 is the most widely used PCB material, there are other substrates available for specific applications:
Material | Advantages | Disadvantages |
---|---|---|
Polyimide | – High temperature resistance – Flexible – Lightweight |
– Expensive – Limited availability – Difficult to process |
PTFE (Teflon) | – Low dielectric constant – Low dissipation factor – Excellent high-frequency performance |
– Expensive – Difficult to process – Poor mechanical strength |
Ceramic | – High thermal conductivity – Low CTE – Excellent high-frequency performance |
– Brittle – Expensive – Limited design flexibility |
Despite the availability of these alternative materials, FR4 remains the most popular choice for the majority of PCB Applications due to its balanced properties, cost-effectiveness, and versatility.
Future Trends in FR4 PCB Technology
As the electronics industry continues to evolve, FR4 PCB technology is adapting to meet new challenges and requirements:
-
High-speed materials: The demand for faster data transmission and higher signal integrity is driving the development of high-speed FR4 variants with improved dielectric properties.
-
Miniaturization: Advances in FR4 processing technologies enable the fabrication of smaller and denser PCBs, supporting the trend towards miniaturization in electronic devices.
-
Environmental sustainability: There is a growing emphasis on environmentally friendly FR4 materials, such as halogen-free and lead-free variants, to comply with green initiatives and regulations.
-
Integration with advanced packaging: FR4 PCBs are being integrated with advanced packaging technologies, such as embedded components and 3D packaging, to create more compact and functional electronic modules.
Frequently Asked Questions (FAQ)
1. What does FR4 stand for?
FR4 stands for “Flame Retardant 4,” indicating that the material is designed to be flame-resistant and self-extinguishing.
2. Is FR4 suitable for high-frequency applications?
Yes, FR4 can be used for high-frequency applications up to a few gigahertz. However, for very high-frequency applications (e.g., millimeter-wave), other materials like PTFE or ceramic may be more suitable due to their lower dielectric constant and dissipation factor.
3. Can FR4 PCBs be used in flexible applications?
Standard FR4 PCBs are rigid and not suitable for flexible applications. For Flexible PCBs, materials like polyimide or flexible FR4 variants (e.g., FR4-Flex) can be used.
4. How does the thickness of FR4 PCBs affect their performance?
Thicker FR4 PCBs offer better mechanical strength and thermal stability but may have higher dielectric losses and reduced high-frequency performance. Thinner FR4 PCBs, on the other hand, are more suitable for high-density designs and have better high-frequency characteristics but may be more fragile.
5. What is the typical lead time for FR4 PCB manufacturing?
The lead time for FR4 PCB manufacturing depends on various factors, such as the complexity of the design, the number of layers, and the manufacturing volume. Typical lead times can range from a few days for simple, quick-turn prototypes to several weeks for large-volume production orders.
Conclusion
FR4 PCBs have become the backbone of the electronics industry due to their excellent mechanical, thermal, and electrical properties, as well as their cost-effectiveness and versatility. The combination of fiberglass and epoxy resin provides a strong, reliable, and flame-retardant substrate that can be used in a wide range of applications, from consumer electronics to industrial and aerospace systems.
As the electronics industry continues to evolve, FR4 PCB technology is adapting to meet new challenges and requirements, with ongoing developments in high-speed materials, miniaturization, environmental sustainability, and integration with advanced packaging technologies.
By understanding the properties, advantages, and applications of FR4 PCBs, electronics designers and manufacturers can make informed decisions when selecting the most suitable material for their projects, ensuring optimal performance, reliability, and cost-effectiveness.
Leave a Reply