What is FR4 PCB?
FR4 PCB, or Flame Retardant 4 Printed Circuit Board, is a type of printed circuit board (PCB) material that is widely used in the electronics industry. It is made from a composite material consisting of woven fiberglass cloth with an epoxy resin binder that is flame resistant. The “FR” in FR4 stands for “Flame Retardant,” and the “4” indicates the woven glass reinforcement used in the material.
FR4 PCB is known for its excellent mechanical, electrical, and thermal properties, making it an ideal choice for a wide range of electronic applications. It offers good insulation, high strength, and durability, as well as resistance to moisture and chemicals.
Composition of FR4 PCB
FR4 PCB is a composite material made up of two main components:
- Woven fiberglass cloth: This provides the mechanical strength and dimensional stability to the PCB.
- Epoxy resin: The fiberglass cloth is impregnated with epoxy resin, which acts as a binder and provides insulation properties.
The combination of these materials creates a strong, rigid, and flame-resistant PCB Substrate that can withstand high temperatures and maintain its structural integrity.
Properties of FR4 PCB
FR4 PCB exhibits several desirable properties that make it a popular choice for electronic applications:
- High mechanical strength and durability
- Excellent electrical insulation properties
- Good thermal stability and flame resistance
- Resistance to moisture and chemicals
- Dimensional stability over a wide temperature range
- Good dielectric properties
- Cost-effectiveness compared to other PCB materials
These properties enable FR4 PCB to be used in a variety of industries and applications, such as consumer electronics, telecommunications, automotive, aerospace, and medical devices.
Advantages of Using FR4 PCB
FR4 PCB offers several advantages over other PCB materials:
1. Mechanical Strength and Durability
FR4 PCB is known for its high mechanical strength and durability. The woven fiberglass reinforcement provides excellent tensile strength and resistance to bending and twisting. This makes FR4 PCB suitable for applications that require a robust and reliable PCB substrate that can withstand physical stress and vibrations.
2. Electrical Insulation
One of the key advantages of FR4 PCB is its excellent electrical insulation properties. The epoxy resin used in FR4 PCB provides a high dielectric constant and low dielectric loss, which helps to minimize signal loss and cross-talk between adjacent traces. This makes FR4 PCB suitable for high-speed and high-frequency applications.
3. Thermal Stability and Flame Resistance
FR4 PCB exhibits good thermal stability and flame resistance. It can withstand high temperatures without deforming or losing its mechanical and electrical properties. The flame-retardant properties of FR4 PCB also help to prevent the spread of fire in case of electrical faults or overheating, making it a safer choice for electronic applications.
4. Resistance to Moisture and Chemicals
FR4 PCB is resistant to moisture and chemicals, which makes it suitable for use in harsh environments. It can withstand exposure to humidity, solvents, and other chemicals without degrading or losing its properties. This makes FR4 PCB a reliable choice for industrial and outdoor applications.
5. Cost-Effectiveness
Compared to other PCB materials, such as polyimide or PTFE, FR4 PCB is relatively cost-effective. It offers a good balance of performance and affordability, making it a popular choice for a wide range of electronic applications.
Applications of FR4 PCB
FR4 PCB is used in a wide range of electronic applications across various industries:
- Consumer electronics: Smartphones, laptops, tablets, gaming consoles, and home appliances.
- Telecommunications: Routers, switches, modems, and other networking equipment.
- Automotive: Engine control units, infotainment systems, and sensors.
- Aerospace: Avionics, flight control systems, and satellite communication devices.
- Medical devices: Diagnostic equipment, patient monitoring systems, and implantable devices.
- Industrial automation: PLCs, motor drives, and control panels.
- Military and defense: Communication systems, radar, and surveillance equipment.
The versatility and reliability of FR4 PCB make it a suitable choice for a broad spectrum of electronic applications, from consumer gadgets to mission-critical systems.
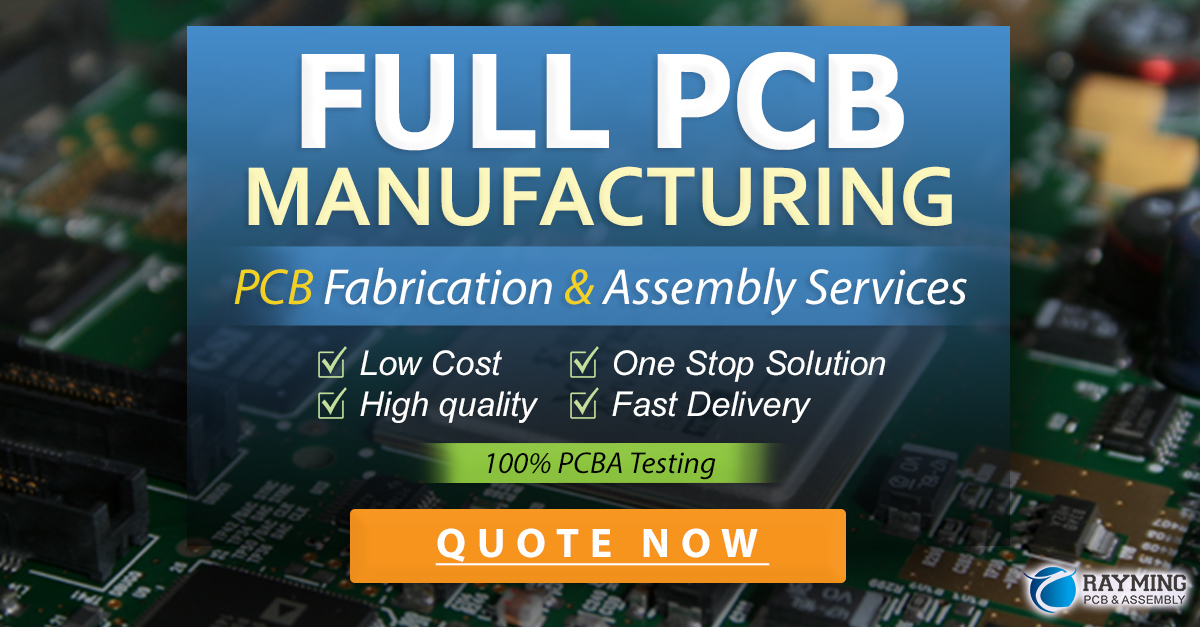
Manufacturing Process of FR4 PCB
The manufacturing process of FR4 PCB involves several steps:
- Raw material preparation: The woven fiberglass cloth is impregnated with epoxy resin and partially cured to form a prepreg material.
- Lamination: Multiple layers of prepreg and copper foil are stacked and laminated together under high temperature and pressure to form a solid FR4 PCB substrate.
- Drilling: Holes are drilled through the PCB substrate to accommodate through-hole components and vias.
- Copper plating: The drilled holes are plated with copper to create electrical connections between layers.
- Patterning: The desired circuit pattern is transferred onto the copper layers using photolithography and etching processes.
- Solder mask application: A protective solder mask layer is applied to the PCB surface, leaving only the exposed pads for component soldering.
- Surface finishing: The exposed pads are coated with a surface finish, such as HASL, ENIG, or OSP, to prevent oxidation and improve solderability.
- Silk screen printing: The component labels, logos, and other markings are printed onto the PCB surface using silk screen printing.
- Electrical testing: The manufactured PCB undergoes electrical testing to ensure proper functionality and compliance with design specifications.
- Singulation: The panel containing multiple PCBs is cut into individual boards using a routing or punching process.
The manufacturing process of FR4 PCB is well-established and can be automated for high-volume production, ensuring consistent quality and reliability.
FR4 PCB Grades and Specifications
FR4 PCB is available in different grades and specifications to cater to various application requirements. The most common grades are:
- FR4 Standard: This is the most widely used grade of FR4 PCB, suitable for general-purpose applications.
- FR4 High Tg: This grade offers a higher glass transition temperature (Tg) than the standard grade, making it suitable for high-temperature applications.
- FR4 Halogen-Free: This grade is made without the use of halogenated flame retardants, making it more environmentally friendly and compliant with RoHS regulations.
- FR4 Controlled Impedance: This grade is designed to maintain a specific characteristic impedance for high-speed signal transmission.
- FR4 High-Density Interconnect (HDI): This grade is designed for high-density PCB Layouts with fine pitch components and micro vias.
The choice of FR4 PCB grade depends on the specific requirements of the application, such as operating temperature, signal integrity, and environmental compliance.
Design Considerations for FR4 PCB
When designing an FR4 PCB, several factors need to be considered to ensure optimal performance and reliability:
- Layer stackup: The number and arrangement of copper layers and prepreg layers in the PCB stackup affect the signal integrity, power distribution, and mechanical strength of the board.
- Trace width and spacing: The width and spacing of the copper traces should be designed to maintain the desired characteristic impedance and minimize signal reflections and crosstalk.
- Via design: The size, location, and type of vias (through-hole, blind, or buried) should be designed to minimize signal integrity issues and improve manufacturability.
- Thermal management: Proper thermal management techniques, such as the use of thermal vias and copper pours, should be employed to dissipate heat from power-hungry components.
- EMI/EMC: Appropriate design techniques, such as proper grounding, shielding, and filtering, should be used to minimize electromagnetic interference (EMI) and ensure electromagnetic compatibility (EMC).
- DFM: The design should adhere to design for manufacturability (DFM) guidelines to ensure that the PCB can be manufactured reliably and cost-effectively.
By considering these design factors, engineers can create robust and reliable FR4 PCB designs that meet the specific requirements of their applications.
FAQ
1. What is the difference between FR4 and other PCB materials?
FR4 is a composite material made of woven fiberglass and epoxy resin, offering a good balance of mechanical, electrical, and thermal properties. Other PCB materials, such as polyimide and PTFE, offer higher performance in specific areas, such as high-temperature resistance or low dielectric loss, but at a higher cost.
2. Can FR4 PCB be used for high-frequency applications?
Yes, FR4 PCB can be used for high-frequency applications up to a few gigahertz. However, for very high-frequency applications, such as microwave or millimeter-wave frequencies, other PCB materials with lower dielectric loss, such as Rogers or Teflon, may be more suitable.
3. Is FR4 PCB environmentally friendly?
Standard FR4 PCB contains halogenated flame retardants, which can be harmful to the environment if not properly disposed of. However, halogen-free grades of FR4 PCB are available, which are more environmentally friendly and comply with RoHS regulations.
4. What is the maximum operating temperature of FR4 PCB?
The maximum operating temperature of FR4 PCB depends on the specific grade and glass transition temperature (Tg). Standard FR4 PCB has a Tg of around 130°C, while high Tg grades can have a Tg of up to 170°C or higher. The maximum operating temperature is typically around 20-30°C below the Tg.
5. How can I ensure the reliability of my FR4 PCB design?
To ensure the reliability of your FR4 PCB design, consider factors such as layer stackup, trace width and spacing, via design, thermal management, EMI/EMC, and DFM guidelines. Additionally, use reputable PCB Manufacturers and perform thorough testing and inspection of the manufactured boards to identify any potential issues.
Conclusion
FR4 PCB is a versatile and widely used PCB material that offers a good balance of mechanical, electrical, and thermal properties. Its high strength, excellent insulation, and flame resistance make it suitable for a wide range of electronic applications across various industries.
When designing with FR4 PCB, it is important to consider factors such as layer stackup, trace design, via design, thermal management, EMI/EMC, and DFM guidelines to ensure optimal performance and reliability.
By understanding the properties, advantages, and design considerations of FR4 PCB, engineers can create robust and reliable electronic products that meet the specific requirements of their applications.
Leave a Reply