Introduction
Flexible circuit boards, also known as flex circuits or flex PCBs, are printed circuit boards made of flexible materials like polyimide or polyester film. Compared to rigid PCBs, flex circuits can bend and flex to fit mechanically challenging spaces. They are often used in consumer electronics, medical devices, automotive applications, and aerospace products where reliability, space optimization, and dynamic flexing are critical considerations.
Choosing the right flexible PCB manufacturer is key to getting high-quality and reliable flex circuits for your application. This article provides an overview of flex PCBs, insights into the flex circuit manufacturing process, cost factors, top manufacturers, and frequently asked questions to help you find the best partner for your flexible PCB needs.
What are Flexible Circuit Boards?
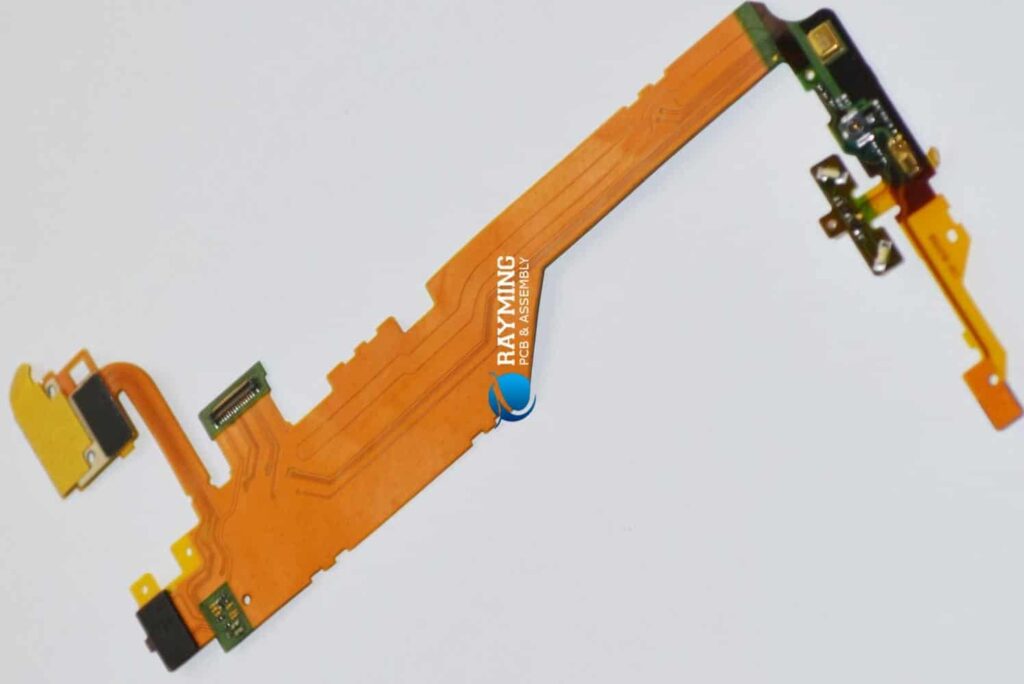
A flexible printed circuit board is made of a thin insulating flexible substrate such as polyimide or polyester film. Conductive pathways or traces are laminated onto this substrate to provide electrical connections between components. The traces are usually made of rolled annealed copper which allows for dynamic flexing. Components are soldered directly onto the flex PCB.
Unlike rigid boards which are flat, inflexible squares and rectangles, flex circuits can take any shape – circular, curved, folded, rolled, cylindrical etc. They are extremely lightweight and can bend repeatedly without damage.
Key Benefits of Flexible Circuit Boards
- Flexibility – Can be bent, folded, twisted to fit challenging spaces
- Lightweight – Up to 75% lighter than rigid PCBs
- Reliability – Withstands millions of flex cycles without failure
- Space saving – Fits in tight spaces where rigid boards cannot
- Reduced assembly costs – Allows higher component density
Flex PCBs are ideal for applications like:
- Wearable devices
- Medical equipment
- Consumer electronics
- Vehicles and aerospace systems
- Industrial equipment
- Robotics and mechatronics
Flexible PCB Manufacturing Process Overview
The specialized construction of flex circuits requires sophisticated manufacturing processes. Here is a brief overview:
1. Design and Prototyping
The first step is to design the flex circuit based on the application requirements and circuit complexity. PCB designers use CAD software to layout the flexible board. Rigorous simulation, analysis and prototyping are done to validate the design.
2. Materials Selection
The flexible substrate material (polyimide, polyester etc) and adhesive layers are selected based on flex and bend radius requirements. The thickness of traces is also determined based on current loads.
3. Imaging and Etching
Photolithographic processes are used to image and etch the traces pattern onto the flexible copper clad substrate. This is similar to rigid PCB fabrication.
4. Die Cutting and Component Assembly
Once the core flexible circuit is ready, the required shapes are die cut using laser or mechanical tools. Components are then precisely assembled onto the board.
5. Functional Testing
Each completed flex PCB goes through comprehensive functional testing to ensure reliability and performance.
6. Final Finishing
Additional finishing steps like legends, protective coatings, contours etc. are applied as needed to complete the flex circuit boards.
Key Factors that Determine Flexible PCB Costs
As complex electro-mechanical assemblies, flex circuits incur higher costs compared to rigid boards. Here are some key considerations:
- Board complexity – Number of layers, high-density traces, blind/buried vias all increase fabrication costs.
- Flexible substrate material – Price increases for high-temperature/specialty flex materials.
- Flexibility requirements – Tight bend radii demand extra thin flexible substrates.
- Component density – Dense component assembly requires more precision.
- Quantity – Smaller production volumes have higher per-unit costs.
- Testing requirements – Extensive functional/environmental testing adds cost.
- Certifications – Medical or military-spec compliance certification adds overhead.
- Special finishes – Metal backed boards, special coatings etc. increase price.
However, the benefits of reliability, space optimization, and design flexibility offset the higher cost of quality flex circuits in many applications.
Top Flexible PCB Manufacturers
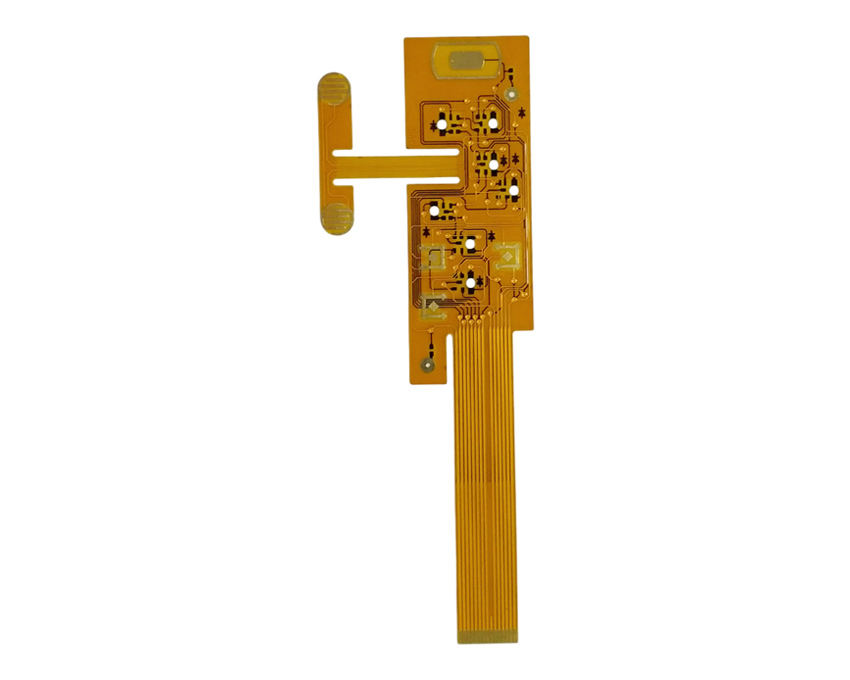
With the growth in flex PCB demand from various industries, many manufacturers now offer specialized flex circuit fabrication and assembly services. Here are some of the top global flexible circuit board manufacturers:
1. Flexible Circuit Technologies (FCT)
FCT is a leading flex PCB producer focused exclusively on flexible printed circuits. They offer a range of base materials, thin flexible substrates, and can fabricate complex multilayer flex boards. FCT has over 48 years of experience in flex PCB manufacturing and has worked with major aerospace, defense, and medical companies.
Key capabilities:
- Rigid-flex PCBs, metal-backed flex circuits
- Flex and rigid-flex assemblies
- Quick turn prototype circuits
- Design support and DFM analysis
2. Compass Circuits
Compass Circuits provides full turnkey flex PCB services from rapid prototyping to volume production of complex boards. They specialize in manufacturing ultra-thin flex circuits down to 25 microns. Compass Circuits supports various industries including medical, automotive, and industrial applications.
Key capabilities:
- Ultra-thin flex circuits down to 25 microns
- Multilayer rigid-flex PCBs
- Flex and rigid-flex assemblies
- ISO 13485 and AS 9100 certified
3. Mina Circuits Limited
Mina is a fast-growing flex PCB company with manufacturing operations in the US and China. They offer advanced flex board fabrication capabilities covering single, double, and multilayer flex along with rigid-flex boards. Mina also provides flex PCB assembly and rapid prototyping services.
Key capabilities:
- Flex and rigid-flex PCB manufacturing
- Multilayer flex circuits
- Quick turn prototype circuits
- Design and fabrication support
- Flexible PCB assemblies
4. Flexible Interconnect Technologies
As a specialist manufacturer, Flexible Interconnect Technologies produces a wide array of flex circuits for the defense, aerospace, telecom, and medical sectors. Their flex PCBs meet stringent quality standards for advanced applications.
Key capabilities:
- Defense/aerospace grade flex PCBs
- Multilayer rigid-flex
- Flex assemblies and cabling
- Prototype to medium-volume production
- ITAR registered and AS 9100 certified
5. Lenthor Engineering
Lenthor offers end-to-end flex PCB design, fabrication and assembly services. They have worked on a diverse range of flex circuit projects – from simple consumer devices to complex aerospace systems. Lenthor provides dedicated support throughout the manufacturing process.
Key capabilities:
- Quick-turn prototype circuits
- Multilayer rigid-flex PCBs
- Flex circuit assemblies
- Flex circuit product design
- IPC 6013 qualification
Flexible PCB Manufacturer Selection Criteria
Choosing the right flexible circuit board manufacturer for your specific product needs can be challenging. Here are key criteria to consider during selection:
- Technical expertise in fabricating complex flex board designs
- Manufacturing capabilities that match your requirements
- Quality certifications like ISO, IPC, ITAR etc.
- Past experience in your industry and application segments
- Reliability and consistency
- Production capacity for your projected volume
- Pricing that provides value for money
- Customer service and design support
- Proactive communication and transparency
- Proximity to your location
- Prototyping abilities for validating designs
- EPC and DFM analysis during design stage
Carefully evaluating manufacturers against these parameters helps identify the right flexible circuit board partner for your project.
Frequently Asked Questions
Here are some common questions about flexible PCB manufacturing:
Q: Can flex circuit boards be double sided?
Yes, double-sided flex PCB fabrication with traces on both sides of the substrate is commonly done. Multilayer boards with 2 or more conductive layers separated by insulating adhesive are also manufactured.
Q: What are some common flexible PCB materials?
Polyimide films like Kapton from DuPont are most commonly used. Other options include Polyester (PET), PEEK, Polyurethane etc. depending on flexibility, temperature resistance and cost considerations.
Q: Can components be assembled directly on the flex boards?
SMT components are typically directly assembled by soldering onto the flex PCBs. Through-hole parts can also be hand assembled for lower volume production.
Q: What are typical flex circuit thickness and trace sizes?
Flex board thickness ranges from 25 microns to around 150 microns. Copper traces are generally 12 microns to 35 microns in thickness. Thicker traces handle higher amperage.
Q: How much do prototype flex circuits cost?
simple 2 layer prototype with minimum tooling can cost $1000 to $1500 and take about 2 weeks. Complex boards can cost $3000 upwards and have longer lead times.
Conclusion
Flexible PCBs enable innovative and reliable product designs in a variety of industries where space constraints, dynamic bending, lightweight, and ruggedness are important considerations. Partnering with the right manufacturer is crucial to harness the benefits of flex circuits. Carefully evaluating technical capabilities, experience, certifications, customer support and costs helps identify the best supplier for your specific project needs.
Leave a Reply