Introduction
Printed circuit boards (PCBs) are essential components in electronic devices that provide the necessary electrical connections between various components. Flex PCBs (also known as flex circuits) are a type of PCB that utilize flexible substrate materials that can bend and flex. This allows them to be used in applications where flexibility is required, like in wearable devices, medical equipment, consumer electronics and more.
Getting an accurate quote for your flex PCB order is crucial to ensure you get the best price and lead time. However, the flex PCB manufacturing process has some unique considerations that affect pricing. This guide will provide tips on how to get an accurate flex PCB quote by understanding flex PCB design, materials, tolerances and production methods.
Flex PCB Design Considerations

Your flex PCB design will have a significant impact on the quote. Here are some key design aspects manufacturers will evaluate:
Layer Count
The number of conductive copper layers in the flex PCB stackup affects material costs and production processes. More layers means higher costs.
Board Size
Larger boards use more materials and can require specialized manufacturing equipment, increasing costs. Maximum panel sizes vary amongst manufacturers.
Board Shape
Non-rectangular boards require additional processing like V-scoring or tab routing. Odd shapes can result in more material wastage too.
Bend Radii
Small bend radii increase risk of traces cracking. Larger bend radii are preferred and may have minimum requirements.
Stiffeners
Stiffeners made of FR4 or polyimide are sometimes added to prevent flexing in certain areas. This adds processing steps.
Adhesives
Adhesives are needed to bond layers. More adhesive types (eg. acrylic, epoxy) add costs.
Solder Mask
Solder mask application adds processing steps, especially for multilayer boards.
Finishes
Special finishes like ENIG or immersion silver add plating steps and material expenses.
Testing
Testing like ICT adds time and cost. Functional/environmental testing may also be required.
Tooling
New tooling charges may apply for custom board shapes or large panel sizes.
Documentation
Detailed documentation and tight tolerances require more manufacturing oversight.
Flex PCB Material Considerations
The materials used in the flex PCB laminate stackup impact the cost as well. Here are some common flex PCB materials and their pricing implications:
Substrates
The flexible substrate forms the base of the PCB. Polyimide is most common. Lower-cost PET/PEN films may also be used.
Adhesives
Acrylic or epoxy adhesives bond layers. Some are more expensive than others.
Copper Foil
Copper foils come in different thicknesses. Thicker copper is more expensive.
Coverlay/Coverfilm
Polyimide cover layers add processing steps and material costs.
Stiffeners
FR4 or polyimide stiffeners add material expenses. Their thickness impacts cost.
Solder Mask
Liquid Photo Imageable (LPI) solder mask is standard. Lower-cost ink-based masks are also used.
Finishes
Immersion silver, immersion tin, ENIG, HASL and more finishes have different material/processing costs.
So minimizing the types and quantities of special materials will help reduce your flex PCB costs.
Flex PCB Tolerance Considerations
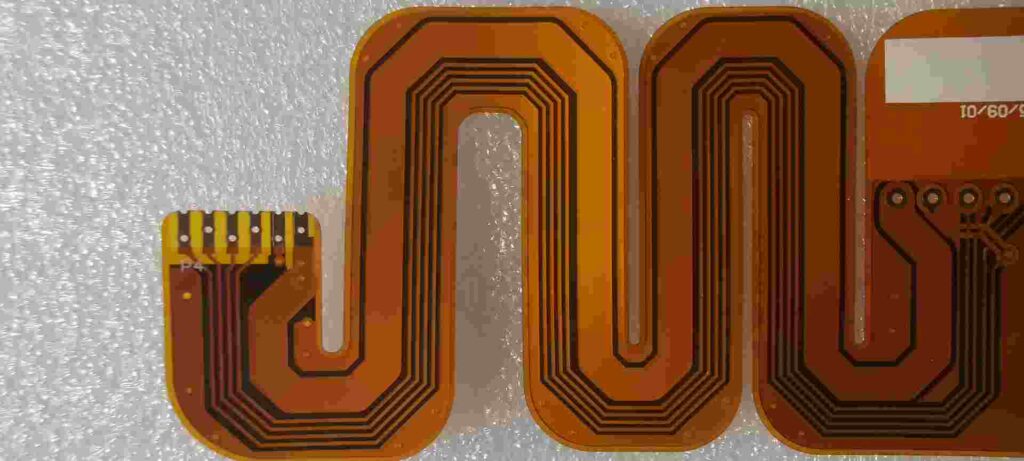
Manufacturing tolerances also affect flex PCB pricing. Tighter tolerances require more processing control and often have higher costs. Here are some common flex PCB tolerances:
Layers Alignment
Typical alignment is ~0.1mm. Tighter alignments add cost.
Line Width/Spacing
Standard is ~0.1mm width/spacing. Below 0.1mm adds cost.
Hole Size
~0.1mm is standard. Smaller holes are more challenging.
Hole to Hole Alignment
~0.2mm alignment is typical. Tighter adds alignment steps.
Hole to Pad Alignment
~0.1mm alignment is standard. Tighter has cost impact.
Etch Factor
Standard is ~1.5x line width removed during etching. Tighter etch factors increase processing steps.
Impedance Control
Tighter impedance control requires more production oversight.
Flatness/Bow
Tolerances are typically ~3mm per 25mm panel size. Tighter requirements add cost.
So keeping your tolerances within standard manufacturing capabilities will help optimize costs. Discuss any tight tolerances with your PCB manufacturer.
Flex PCB Production Considerations
The production processes used by the manufacturer also influence the flex PCB quote. Here are some common production factors:
Volume
Higher order volumes achieve better economy of scale. Small orders are less cost efficient.
Lead Time
Standard lead times are cheaper. Rush orders add overtime and expedited processing fees.
Panel Utilization
Good panel utilization minimizes material waste. Low utilization increases cost per board.
Testing/Inspection
More rigorous testing (ICT, functional, environmental) adds time and cost.
Automation
Manual processes take longer. Automated operations are faster and cheaper.
Manufacturing Equipment
Up-to-date equipment improves capabilities and yields. Older equipment may have limitations.
Location
Labor rates, supply chain, and logistics vary by manufacturing location.
Certifications
Certifications like ISO demonstrate quality systems but add overhead.
Manufacturer Size/Experience
Large, experienced manufacturers benefit from economies of scale.
Understanding the manufacturer’s production processes helps determine what pricing to expect. Ask potential suppliers to explain their capabilities.
Getting Flex PCB Quotes
Now that you understand key pricing factors for flex PCBs, here are some tips for getting accurate quotes:
- Provide complete design files – This gives manufacturers all the details needed to quote accurately. Include layer stackup, board outline/dimensions, tolerances, testing requirements, and any other special instructions.
- Define order details upfront – Make qty, lead time, delivery terms clear. Smaller qtys and faster lead times increase costs.
- Get quotes from multiple manufacturers – Compare prices from several vendors. But make sure you give each the same information to get a fair comparison.
- Review line items closely – Look for tooling, NRE charges, rush fees. Ask about anything unclear.
- Clarify material/process alternatives – If a quote seems high, ask if lower-cost material substitutions or processes are possible.
- Leverage competition – Let vendors know you are shopping quotes. Some may reduce margins to win business. But don’t over leverage.
- Build long-term partnerships – Developing close supplier relationships leads to better pricing over time.
With these tips, you can get accurate flex PCB quotes to choose the best value manufacturer for your project needs. Proper upfront communication about designs, requirements and commercial expectations helps avoid surprises down the road.
Flex PCB Quote Factors Summary
Here is a summary of the key factors that affect flex PCB quoting:
Design Factors | Material Factors | Tolerance Factors | Production Factors |
---|---|---|---|
Layer count | Substrate type | Layer alignment | Volume |
Board size | Adhesive type | Line width/spacing | Lead time |
Board shape | Copper weight | Hole size/alignment | Testing needs |
Bend radii | Coverlay type | Etch factor | Automation level |
Stiffeners | Solder mask type | Impedance control | Equipment/capabilities |
Adhesives | Finish type | Flatness/bow | Location/logistics |
Solder mask | Certifications | ||
Finishes | Manufacturer size/experience | ||
Documentation |
Flex PCB Quote FAQ
Here are answers to some frequently asked questions about getting flex PCB quotes:
Q: How do minimum order quantities (MOQs) affect flex PCB pricing?
A: Most manufacturers have MOQ requirements that must be met to achieve standard pricing. Smaller orders often have higher cost per board. Typical MOQs are 100-500 boards.
Q: Does the number of pre-production samples impact the overall cost?
A: Initial sample builds required for prototyping and design validation incur NRE (non-recurring engineering) fees. This covers preliminary tooling, documentation, testing setups, etc. Budget for multiple spin samples.
Q: What are tooling and NRE fees?
A: Tooling fees cover production equipment like fabrication panels tailored for your board size/shape. NRE fees account for documentation, stencil generation, testing programming, and other one-time upfront engineering work required to prepare for manufacturing.
Q: How much does certifying a flex PCB supplier add to costs?
A: Certification audits like those required for ISO compliance add overhead for manufacturers. Much of this overhead may get passed onto customers. Uncertified suppliers often have lower pricing.
Q: Can I provide certain materials to reduce flex PCB costs?
A: Some manufacturers allow customer-supplied materials, though meeting their incoming inspection standards can be challenging. Ensure upfront that any cost-savings of supplied materials outweighs the logistics burden.
Conclusion
Getting an accurate quote is key to choosing the best flex PCB manufacturer for your project. By understanding the design, materials, tolerances, processes, and commercial expectations that drive cost, you can effectively compare vendor pricing. Leverage the knowledge from this guide during your quoting process to avoid surprises and get the ideal flex PCB solution for your requirements. With careful upfront planning, your flex PCB procurement can stay right on budget.
Leave a Reply