Introduction
Flexible printed circuit boards (flex PCBs) are a key technology enabling compact, lightweight and reliable electronics across industries. As products continue getting smaller and more complex, the demand for flex circuits is growing rapidly. This has led to the rise of many flex PCB manufacturers worldwide.
Selecting the right manufacturer is crucial to ensuring flex circuit quality, performance and on-time delivery for your products. This guide covers the key factors to consider when choosing a flex PCB production partner:
- Capabilities and expertise
- Quality and reliability
- Volume capacity and scalability
- Design support and DFM
- Assembly services
- Communication and customer service
- Location and logistics
- Competitive pricing
Weighing these criteria properly helps find the ideal flex circuit supplier for your needs.
Flex PCB Manufacturing Capabilities
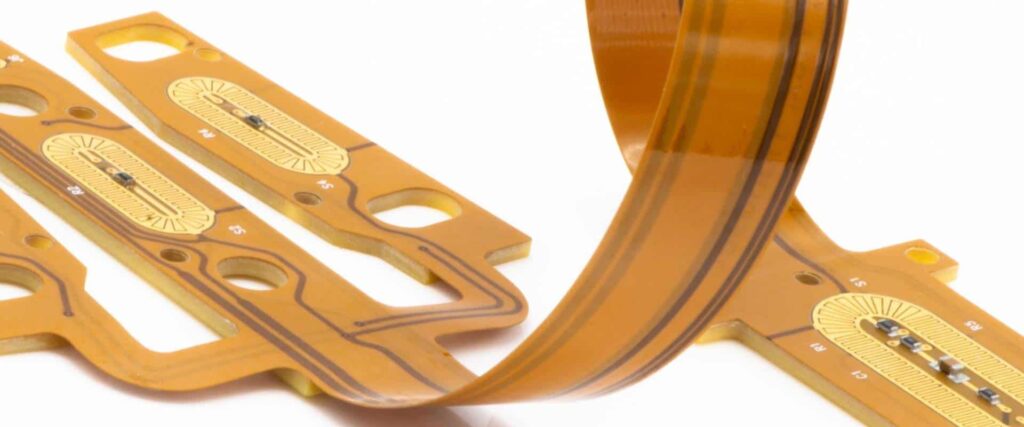
A flex manufacturer must have the full range of specialized equipment and processes to fabricate your boards correctly. Look for these essential capabilities:
Photolithography – The ability to image high-resolution copper traces and features onto both sides of flexible substrates. State-of-the-art equipment like laser direct imaging (LDI) offers finer lines and tolerances.
Etching – Wet etching to selectively remove unwanted copper, leaving only the desired conductor pattern.
Flexible Laminating – Bonding of thin flex materials together under high pressure and temperature.
Coverlay Application – Adhering protective overlay films over conductors and substrates.
Laser Drilling – Precise, high-density laser drilling to create via holes for connectivity between layers.
Plating – Electrolytic copper plating of drilled vias and conductor surfaces.
Testing and Inspection – Electrical testing and automated optical inspection to ensure quality boards.
Ideally, look for familiarity with the latest flex materials, fine line capabilities, and experience with high layer counts and densities.
Quality and Reliability Processes
Given the mission-critical nature of most flex PCB applications, quality and reliability are paramount. Look for robust quality assurance measures:
- IPC certification – Compliance with IPC flex circuit standards such as IPC-2223 and IPC-6013.
- Quality certifications – ISO-9001, ISO-13485, AS9100 or other quality management standards.
- Process controls – Use of statistical process control and defect monitoring.
- Traceability – Part numbering, version control and lot traceability.
- Testing – 100% electrical testing of boards and routine quality audits.
- Personnel – Strong training programs for employees.
Choose a manufacturer focused on quality, not just low cost. This helps avoid errors, inconsistencies, and potential field failures.
Volume Production Capacity
Evaluate production capacity in terms of:
- Monthly output – Can they meet your ongoing volume requirements reliably? Look at both quantity and mix fluctuations.
- Scalability – Do they have room to scale up as your needs grow? Or risk of being too big/small?
- Turn-around times – How long from order to delivery? Look for quick turns of prototypes and low-medium volume orders.
- Inventory – Some inventory of common substrates/materials helps reduce lead times.
- Staffing – Adequate staff across engineering, production and quality assurance. No bottlenecks.
Having a partner able to grow along with your expected product lifecycle needs avoids problems down the road.
Design Support and DFM
The manufacturer should have engineers to support design review and provide design for manufacturability (DFM) feedback on your boards. This helps avoid manufacturing issues and ensures performance.
Ask about capabilities like:
- Design rules/libraries – Do they provide proven flex board design rules?
- Stackup review – Can they evaluate layer stackup, materials, thickness, etc.?
- DFM checks – What DFM checks are done on customer designs? Such as trace widths, spacing, hole sizes, etc.
- Simulation – Thermal/mechanical modeling to simulate bend radii, vibration, shock, etc.
- Prototype support – Building prototypes to test manufacturability before full production.
Strong design support eliminates problems upfront and ensures quality in volume production.
Assembly Services
Many flex PCB manufacturers offer in-house assembly of components onto the flex boards. Consider capabilities around:
- SMT assembly – High-precision surface mount assembly with advanced pick-place technologies.
- Through-hole assembly – Capable of press-fit pins, connectors and other through-hole components.
- Testing/inspection – Post-assembly testing like ICT/flying probe electrical test, X-ray, AOI.
- Inventory – Parts inventory to enable quick-turn assembled boards.
- Supply chain – Established supply channels for components and connectors.
Full assembly services provide added value and convenience of a turnkey solution from design through testing.
Communication and Customer Service
Your PCB partner should provide responsive, transparent communication and support at every step:
- Account management – Dedicated reps to understand needs and guide the relationship.
- Engineering contacts – Quick access to engineers for design reviews and technical queries.
- Manufacturing updates – Real-time production monitoring and notifications.
- Documentation – Detailed fabrication and assembly reports. Certificates of compliance.
- Language support – Fluency in languages needed by global customers.
- Problem resolution – Quick response to any issues, with thorough root cause analysis.
Good communication and service help uncover potential issues early and ensure smoother projects.
Location and Logistics
For optimized supply chain efficiency, evaluate:
- Proximity – How close is the flex manufacturer to your team and target market? Nearby suppliers allow better collaboration and rapid delivery.
- Shipping – What shipping options, times and costs? Flex boards require proper handling and packaging.
- Customs – Experience with customs clearance for international shipments? Localized support helps navigate cross-border complexities.
- Supply chain – Established channels for raw materials and component sourcing. Reduces lead times.
Choosing a strategically located supplier improves logistics speed, cost and reliability for your products.

Competitive Pricing
Of course, cost is a key criterion. Factors to consider:
- Economies of scale – Larger manufacturers enjoy cost savings from high volumes and purchasing power.
- Transparency – Upfront communication of all pricing factors – materials, layers, tolerances, testing requirements etc. No hidden charges.
- Flex expertise – Specialized flex focus lowers cost versus rigid PCB companies doing flex as a side business.
- NREs and setup – Carefully evaluate any non-recurring engineering fees. Should provide value.
- Prototypes – Affordable prototype pricing enables testing before committing to production.
- Assembly – Having PCB assembly in-house eliminates added cost/lead-time of separate assembly.
Seeking the best value requires balancing capabilities, quality, and cost across potential suppliers.
Key Flex PCB Manufacturer Selection Criteria
Criteria | Description |
---|---|
Capabilities | Photolithography, etching, lamination, plating, drilling/routing, testing |
Quality/Reliability | IPC certifications, process controls, traceability |
Volume Capacity | Output, scalability, turn-around times |
Design Support | DFM checks, simulations, prototypes |
Assembly Services | SMT, through-hole, testing capabilities |
Communication | Dedicated contacts, notifications, documentation |
Location/Logistics | Proximity, shipping options, customs expertise |
Pricing | Transparent pricing, cost competitiveness |
Conclusion
Choosing the right flex PCB manufacturing partner is crucial to realizing the benefits of flex circuits for your products. Evaluating expertise, quality, capacity, design/assembly services, communication, logistics and pricing ensures you select the best fit. Investing time upfront to properly qualify suppliers helps enable long-term electronics innovations.
Frequently Asked Questions
What are the most important factors when selecting a flex PCB manufacturer?
The key criteria are understanding their specific flex circuit manufacturing capabilities, expertise and experience with the technology; quality certifications and process controls; capacity to meet current and future volume needs; design support and review; communication and customer service; and competitive transparent pricing.
What quality certifications should I look for?
Key certifications validating quality processes include IPC class 2 and 3 standards like IPC-2223 (flex circuits), IPC-6013 (flex assembly) and IPC-A-600 (acceptability standard). Management standards like ISO 9001, ISO 13485 and AS9100 also demonstrate a commitment to consistency.
How can I evaluate technical capabilities for flex boards?
Look for specific flex focused capabilities like photolithography and etching optimized for thin flexible materials; precision laser drilling technology; high layer count lamination and plating; fine line/space patterning down to 25 microns or below; and the ability to work with latest substrates like LCP.
Why is location important for a flex PCB supplier?
Proximity to your team allows for better collaboration during design and engineering reviews and prototyping. It also reduces shipping time and costs for production boards. Local support helps navigate customs and cross-border logistics issues as well.
What design support should I expect from a flex manufacturer?
You should have access to flex PCB design rules, stackup recommendations, DFM checks on your designs to avoid manufacturability issues, thermal/mechanical simulations of flex circuits, and building prototypes to confirm performance before full production.
Leave a Reply