What is a PCB Surface Finish?
A PCB surface finish is a coating applied to the exposed copper on a PCB to protect it from oxidation and enhance its solderability. The surface finish also provides a reliable contact surface for electronic components and ensures a strong mechanical and electrical connection.
Some common PCB Surface Finishes include:
- Hot Air Solder Leveling (HASL)
- Organic Solderability Preservatives (OSP)
- Electroless Nickel Immersion Gold (ENIG)
- Electroless Nickel Electroless Palladium Immersion Gold (ENEPIG)
- Immersion Silver
- Immersion Tin
Each surface finish has its own unique properties, advantages, and disadvantages. Let’s take a closer look at each one.
Hot Air Solder Leveling (HASL)
HASL is one of the most commonly used PCB surface finishes. In this process, the PCB is dipped into a molten solder bath, and then hot air is used to blow off the excess solder, leaving a thin, even layer on the copper surfaces.
Advantages of HASL:
- Cost-effective
- Excellent solderability
- Good shelf life (6-12 months)
- Suitable for both through-hole and surface mount components
Disadvantages of HASL:
- Uneven surface due to the nature of the process
- Not suitable for fine-pitch components
- Thermal shock during the process can cause board warpage
- Contains lead (Pb), which is subject to RoHS restrictions
Organic Solderability Preservatives (OSP)
OSP is a lead-free, organic compound that is applied to the copper surfaces of a PCB to protect against oxidation. The coating is transparent and very thin, typically less than 0.5 microns.
Advantages of OSP:
- Cost-effective
- Lead-free and RoHS compliant
- Flat surface, suitable for fine-pitch components
- Good solderability
Disadvantages of OSP:
- Limited shelf life (3-6 months)
- Can be difficult to inspect visually
- May require a nitrogen atmosphere during reflow soldering
- Not suitable for multiple reflow cycles
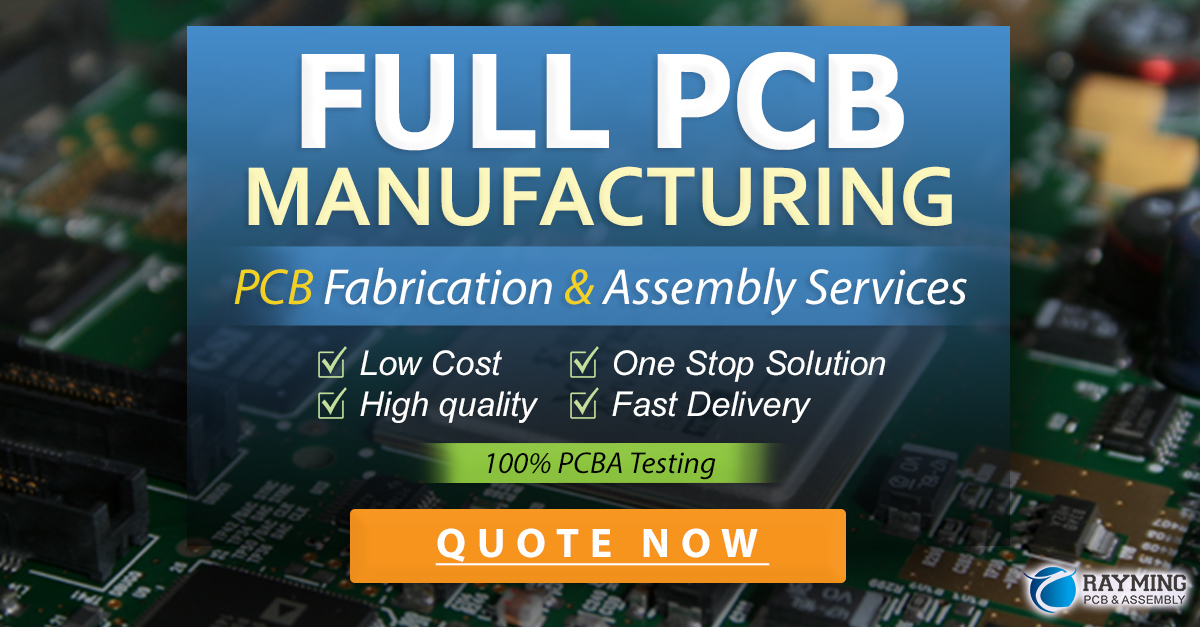
Electroless Nickel Immersion Gold (ENIG)
ENIG is a two-layer surface finish consisting of a nickel underlayer and a thin gold top layer. The nickel layer provides a barrier against copper diffusion, while the gold layer offers excellent solderability and protection against oxidation.
Advantages of ENIG:
- Excellent solderability
- Long shelf life (12+ months)
- Suitable for fine-pitch components
- Good thermal and mechanical stability
- RoHS compliant
Disadvantages of ENIG:
- Higher cost compared to HASL and OSP
- Nickel layer can be prone to “black pad” issues
- Gold layer may dissolve into solder during reflow, affecting joint strength
Electroless Nickel Electroless Palladium Immersion Gold (ENEPIG)
ENEPIG is an extension of the ENIG process, with an additional layer of palladium between the nickel and gold layers. This extra layer helps to prevent black pad issues and improves the Wire Bonding performance.
Advantages of ENEPIG:
- Excellent solderability
- Long shelf life (12+ months)
- Suitable for fine-pitch components
- Good thermal and mechanical stability
- Suitable for wire bonding
- RoHS compliant
Disadvantages of ENEPIG:
- Higher cost compared to ENIG
- More complex process with tight control requirements
Immersion Silver
Immersion silver is a simple, single-layer surface finish that deposits a thin layer of silver onto the copper surfaces of the PCB. Silver provides good solderability and is a cost-effective alternative to ENIG.
Advantages of Immersion Silver:
- Cost-effective compared to ENIG and ENEPIG
- Good solderability
- Flat surface, suitable for fine-pitch components
- RoHS compliant
Disadvantages of Immersion Silver:
- Limited shelf life (6-12 months)
- Silver can tarnish over time, affecting solderability
- Not suitable for multiple reflow cycles
- May require a nitrogen atmosphere during reflow soldering
Immersion Tin
Immersion tin is another single-layer surface finish that deposits a thin layer of tin onto the copper surfaces of the PCB. Tin offers good solderability and provides a lead-free alternative to HASL.
Advantages of Immersion Tin:
- Cost-effective
- Lead-free and RoHS compliant
- Good solderability
- Suitable for fine-pitch components
Disadvantages of Immersion Tin:
- Limited shelf life (3-6 months)
- Tin whiskers can form, causing short circuits
- Not suitable for multiple reflow cycles
Factors to consider when choosing a PCB surface finish
When selecting a surface finish for your PCB project, there are several key factors to consider:
-
Application requirements: Consider the specific needs of your application, such as the operating environment, expected lifespan, and performance requirements.
-
Component types: Different surface finishes may be more suitable for certain component types, such as fine-pitch or BGA Packages.
-
Solderability: Evaluate the solderability of each surface finish and its compatibility with your soldering process.
-
Shelf life: Consider the expected shelf life of your PCB and choose a surface finish that offers adequate protection against oxidation.
-
Cost: Compare the costs of different surface finishes and balance them against your project’s budget and performance requirements.
-
Environmental regulations: Ensure that the chosen surface finish complies with relevant environmental regulations, such as RoHS.
-
Manufacturing capabilities: Verify that your PCB manufacturer has the capability and expertise to apply the desired surface finish consistently.
Comparison table of PCB surface finishes
Surface Finish | Solderability | Shelf Life | Fine-Pitch Suitability | Cost | RoHS Compliance |
---|---|---|---|---|---|
HASL | Excellent | 6-12 months | Limited | Low | No (contains Pb) |
OSP | Good | 3-6 months | Yes | Low | Yes |
ENIG | Excellent | 12+ months | Yes | High | Yes |
ENEPIG | Excellent | 12+ months | Yes | High | Yes |
Immersion Silver | Good | 6-12 months | Yes | Medium | Yes |
Immersion Tin | Good | 3-6 months | Yes | Low | Yes |
FAQ
1. What is the most cost-effective PCB surface finish?
HASL and OSP are generally the most cost-effective PCB surface finishes. However, HASL contains lead (Pb) and may not be suitable for RoHS-compliant applications.
2. Which surface finish offers the longest shelf life?
ENIG and ENEPIG offer the longest shelf life, typically 12 months or more, due to the protective properties of the nickel and gold layers.
3. Are all surface finishes suitable for fine-pitch components?
No, not all surface finishes are suitable for fine-pitch components. HASL, for example, can result in an uneven surface that may not be compatible with fine-pitch components. OSP, ENIG, ENEPIG, Immersion Silver, and Immersion Tin are better choices for fine-pitch applications.
4. Which surface finishes are RoHS compliant?
OSP, ENIG, ENEPIG, Immersion Silver, and Immersion Tin are all RoHS compliant surface finishes. HASL, which contains lead (Pb), is not RoHS compliant.
5. Can the choice of surface finish affect the reliability of my PCB?
Yes, the choice of surface finish can impact the reliability of your PCB. Factors such as solderability, shelf life, and compatibility with your manufacturing processes can all affect the overall reliability of the final product. It’s essential to carefully consider your application requirements and consult with your PCB manufacturer when selecting a surface finish.
Conclusion
Choosing the right surface finish for your PCB project is a critical decision that can impact the performance, reliability, and cost of your final product. By understanding the various surface finish options available and their unique properties, you can make an informed choice that best suits your application requirements.
Consider factors such as solderability, shelf life, fine-pitch suitability, cost, and environmental compliance when evaluating surface finishes. Consult with your PCB manufacturer to ensure that they have the capabilities and expertise to apply the desired surface finish consistently.
By selecting the appropriate PCB surface finish, you can ensure that your PCB project meets its performance goals and provides a reliable foundation for your electronic device.
Leave a Reply