Introduction to ENEPIG
ENEPIG (Electroless Nickel, Electroless Palladium, Immersion Gold) is a surface finish that has gained significant popularity in the electronics industry due to its excellent properties and performance. This advanced plating finish is applied to printed circuit boards (PCBs) and other electronic components to provide protection, enhance solderability, and improve the overall reliability of the devices. In this article, we will delve into the details of ENEPIG, its advantages, applications, and the process involved in its application.
What is ENEPIG?
ENEPIG is a multi-layer plating finish that consists of three distinct layers: electroless nickel, electroless palladium, and immersion gold. Each layer serves a specific purpose and contributes to the overall performance of the finish.
-
Electroless Nickel (EN): The first layer of ENEPIG is electroless nickel, which is deposited directly onto the copper substrate of the PCB. This layer acts as a barrier, preventing the diffusion of copper into the subsequent layers and providing a uniform surface for the deposition of palladium and gold. Electroless nickel also enhances the durability and wear resistance of the finish.
-
Electroless Palladium (EP): The second layer is electroless palladium, which is deposited on top of the nickel layer. Palladium serves as a barrier between the nickel and gold layers, preventing the formation of intermetallic compounds that can lead to brittle solder joints. It also improves the wettability of the surface, ensuring good solderability.
-
Immersion Gold (IG): The final layer of ENEPIG is immersion gold, which is deposited on top of the palladium layer. Gold provides excellent oxidation resistance and maintains the solderability of the surface over an extended period. It also enhances the electrical conductivity and improves the overall appearance of the finish.
Advantages of ENEPIG
ENEPIG offers several advantages over other surface finishes, making it a preferred choice for high-performance electronic devices. Let’s explore some of the key benefits of ENEPIG:
1. Excellent Solderability
One of the primary advantages of ENEPIG is its exceptional solderability. The combination of electroless nickel, palladium, and gold layers creates a surface that is highly wettable and compatible with various soldering processes, including reflow soldering, wave soldering, and hand soldering. The gold layer prevents oxidation and ensures a clean, solderable surface, even after prolonged storage.
2. Enhanced Durability
ENEPIG provides excellent durability and wear resistance compared to other surface finishes. The electroless nickel layer acts as a hard, protective barrier, preventing the underlying copper from wearing away due to mechanical stresses or environmental factors. This durability makes ENEPIG suitable for applications that require high reliability and long-term performance.
3. Improved Corrosion Resistance
The multi-layer structure of ENEPIG offers superior corrosion resistance. The electroless nickel layer forms a dense, uniform barrier that prevents the penetration of corrosive agents, while the gold layer provides additional protection against oxidation and corrosion. This combination of layers ensures that the finish remains intact and functional, even in harsh environments.
4. Compatibility with Fine-Pitch Components
ENEPIG is well-suited for applications involving fine-pitch components and high-density interconnects. The thin layers of palladium and gold allow for precise control over the thickness of the finish, enabling the use of smaller pad sizes and tighter spacing between components. This compatibility with fine-pitch designs makes ENEPIG an ideal choice for advanced electronic devices.
5. Extended Shelf Life
Another significant advantage of ENEPIG is its extended shelf life. The immersion gold layer provides a stable, non-reactive surface that resists oxidation and contamination, even when exposed to air for prolonged periods. This extended shelf life is particularly beneficial for components that may be stored for an extended duration before assembly or for devices that require long-term reliability.
Applications of ENEPIG
ENEPIG finds applications in various industries and electronic devices where high performance, reliability, and durability are essential. Some of the common applications of ENEPIG include:
-
Automotive Electronics: ENEPIG is widely used in automotive electronics, such as engine control units (ECUs), sensors, and infotainment systems. The harsh operating conditions in automotive environments, including temperature extremes, vibrations, and exposure to chemicals, require a robust and reliable surface finish like ENEPIG.
-
Aerospace and Defense: In the aerospace and defense industries, electronic devices are subjected to stringent requirements for reliability and performance. ENEPIG’s excellent solderability, corrosion resistance, and durability make it suitable for applications such as avionics, communication systems, and military equipment.
-
Medical Devices: Medical electronic devices demand high reliability and long-term functionality. ENEPIG is used in various medical applications, including implantable devices, diagnostic equipment, and monitoring systems, where the integrity of solder joints and the durability of the finish are critical.
-
Consumer Electronics: ENEPIG is also employed in consumer electronic devices, such as smartphones, tablets, and wearables. The compatibility with fine-pitch components and the ability to withstand multiple reflow cycles make ENEPIG suitable for the high-density designs and miniaturization trends in consumer electronics.
-
Industrial Electronics: Industrial electronic devices, such as control systems, automation equipment, and power electronics, benefit from the robustness and reliability provided by ENEPIG. The finish’s resistance to corrosion and wear ensures reliable performance in industrial environments.
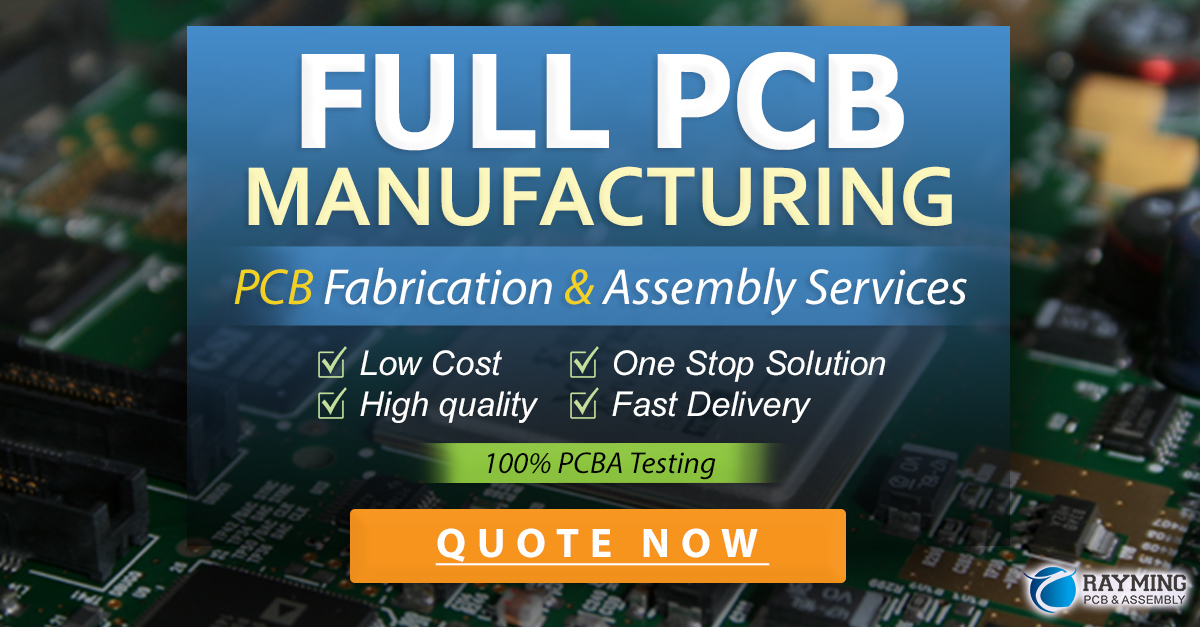
ENEPIG Application Process
The application of ENEPIG involves a series of steps to ensure a uniform and high-quality finish. The typical process flow for ENEPIG application is as follows:
-
Surface Preparation: The copper surface of the PCB is cleaned and prepared to remove any contaminants or oxides. This step may involve a combination of chemical cleaning, microetching, and water rinsing to achieve a clean and activated surface.
-
Electroless Nickel Plating: The cleaned copper surface is immersed in an electroless nickel plating solution. The nickel ions in the solution are reduced and deposited onto the copper surface through an autocatalytic reaction. The thickness of the nickel layer is typically in the range of 3-6 μm.
-
Electroless Palladium Plating: After the nickel plating, the surface is immersed in an electroless palladium plating solution. The palladium ions are reduced and deposited onto the nickel layer, forming a thin layer of palladium with a thickness of 0.05-0.2 μm.
-
Immersion Gold Plating: The final step involves immersing the surface in an immersion gold plating solution. The gold ions displace the palladium atoms on the surface, resulting in a thin layer of gold with a thickness of 0.05-0.2 μm. The immersion gold plating is a self-limiting process, ensuring a uniform and controlled gold thickness.
-
Post-Treatment and Inspection: After the gold plating, the surface undergoes a post-treatment process, which may include rinsing, drying, and baking. The finished ENEPIG surface is then subjected to visual inspection and quality control tests to ensure the desired thickness, uniformity, and solderability of the finish.
The precise parameters and conditions for each step may vary depending on the specific requirements of the application and the guidelines provided by the plating solution manufacturers.
Quality Control and Testing
To ensure the reliability and performance of ENEPIG-plated surfaces, various quality control measures and testing methods are employed. Some of the common tests and inspections include:
-
Visual Inspection: Visual examination of the ENEPIG surface is performed to check for any defects, such as pinholes, blisters, or discoloration. Microscopic inspection may be used to assess the uniformity and coverage of the finish.
-
Thickness Measurement: The thickness of each layer (nickel, palladium, and gold) is measured using techniques such as X-ray fluorescence (XRF) or cross-sectional analysis. The measured thicknesses are compared against the specified requirements to ensure compliance.
-
Solderability Test: Solderability tests are conducted to evaluate the wetting and spreading characteristics of solder on the ENEPIG surface. Common test methods include the wetting balance test and the solder spread test. These tests assess the ability of the finish to form reliable solder joints.
-
Adhesion Test: Adhesion tests, such as the tape test or the cross-hatch test, are performed to evaluate the adhesion strength between the ENEPIG layers and the underlying copper substrate. Good adhesion is essential for the long-term reliability of the finish.
-
Porosity Test: Porosity tests are conducted to assess the presence of pores or defects in the ENEPIG layers. Techniques such as the electrochemical porosity test or the salt spray test can be used to detect any porosity that may compromise the corrosion resistance or solderability of the finish.
-
Environmental Testing: Environmental tests, such as thermal cycling, humidity exposure, or salt spray testing, are performed to evaluate the durability and stability of the ENEPIG finish under various environmental conditions. These tests help assess the long-term reliability of the finish in real-world applications.
Regular quality control and testing ensure that the ENEPIG-plated surfaces meet the specified requirements and deliver the desired performance and reliability in the end application.
Comparison with Other Surface Finishes
ENEPIG is one of several surface finishes used in the electronics industry. It is often compared with other common finishes such as ENIG (Electroless Nickel Immersion Gold), ImAg (Immersion Silver), and OSP (Organic Solderability Preservative). Let’s briefly compare ENEPIG with these finishes:
-
ENEPIG vs. ENIG: ENIG is a two-layer finish consisting of electroless nickel and immersion gold. While ENIG offers good solderability and durability, ENEPIG has the added advantage of the palladium layer, which provides better barrier properties and prevents the formation of brittle intermetallic compounds. ENEPIG also offers improved wire bonding performance compared to ENIG.
-
ENEPIG vs. ImAg: ImAg is a single-layer finish that involves the deposition of a thin layer of silver on the copper surface. ImAg provides good solderability but has limited shelf life and is prone to tarnishing over time. ENEPIG offers superior oxidation resistance and longer shelf life compared to ImAg.
-
ENEPIG vs. OSP: OSP is an organic coating that is applied to the copper surface to prevent oxidation and maintain solderability. OSP is a cost-effective option but has limitations in terms of durability and shelf life. ENEPIG provides better durability, corrosion resistance, and extended shelf life compared to OSP.
The choice of surface finish depends on various factors, including the specific application requirements, cost considerations, and the desired performance characteristics. ENEPIG’s combination of excellent solderability, durability, and compatibility with fine-pitch designs makes it a preferred choice for high-performance applications.
Future Trends and Developments
As the electronics industry continues to evolve, there is a constant drive for improved performance, reliability, and miniaturization. ENEPIG is expected to play a significant role in meeting these demands. Some of the future trends and developments related to ENEPIG include:
-
Thinner Layers: There is a trend towards reducing the thickness of the ENEPIG layers to accommodate the increasing miniaturization of electronic devices. Thinner layers allow for finer pitch sizes and improved signal integrity. Research is ongoing to optimize the plating processes to achieve thinner and more uniform layers without compromising the performance of the finish.
-
Alternative Metals: While gold is the most commonly used metal for the top layer of ENEPIG, there is interest in exploring alternative metals that can provide similar or enhanced properties. For example, ruthenium has been investigated as a potential replacement for gold due to its excellent wear resistance and stability. Further research is needed to assess the feasibility and performance of alternative metals in ENEPIG.
-
Advanced Plating Techniques: Efforts are being made to develop advanced plating techniques that can improve the efficiency, uniformity, and control of the ENEPIG process. For example, the use of pulse plating or the incorporation of additives in the plating solutions can help achieve better thickness distribution and surface morphology. These advancements aim to enhance the overall quality and reliability of the ENEPIG finish.
-
Environmental Considerations: There is a growing emphasis on developing environmentally friendly and sustainable plating processes. Researchers are exploring ways to reduce the use of hazardous chemicals and minimize the environmental impact of ENEPIG plating. This includes the development of green plating solutions and the implementation of waste reduction and recycling strategies.
-
Hybrid Surface Finishes: Hybrid surface finishes that combine the advantages of ENEPIG with other finishes are being explored. For example, a combination of ENEPIG and OSP (known as ENEPIG-OSP) has been developed to provide the benefits of both finishes, such as improved solderability, corrosion resistance, and cost-effectiveness. Further research is needed to evaluate the performance and reliability of hybrid surface finishes.
As the electronics industry evolves, ENEPIG is expected to adapt and improve to meet the changing requirements. Ongoing research and development efforts will focus on enhancing the performance, reliability, and environmental sustainability of ENEPIG, ensuring its continued relevance in the ever-advancing world of electronic devices.
FAQs
- Q: What is the typical thickness of each layer in ENEPIG?
A: The typical thickness of each layer in ENEPIG is as follows: - Electroless Nickel (EN): 3-6 μm
- Electroless Palladium (EP): 0.05-0.2 μm
-
Immersion Gold (IG): 0.05-0.2 μm
-
Q: Can ENEPIG be used for wire bonding applications?
A: Yes, ENEPIG is suitable for wire bonding applications. The gold layer provides a clean and stable surface for wire bonding, and the palladium layer acts as a barrier to prevent the formation of intermetallic compounds that can weaken the bond strength. -
Q: How does ENEPIG compare to ENIG in terms of cost?
A: ENEPIG is generally more expensive than ENIG due to the additional palladium layer and the more complex plating process. However, the enhanced performance and reliability provided by ENEPIG often justify the higher cost, especially in high-end applications where long-term reliability is crucial. -
Q: Is ENEPIG compatible with lead-free soldering processes?
A: Yes, ENEPIG is fully compatible with lead-free soldering processes. The finish provides excellent solderability and wetting characteristics, ensuring reliable solder joints even with lead-free solder alloys. -
Q: What is the shelf life of ENEPIG-plated surfaces?
A: ENEPIG-plated surfaces have an extended shelf life compared to other finishes. The immersion gold layer provides a stable and non-reactive surface that resists oxidation and contamination. Typically, ENEPIG-plated surfaces can maintain their solderability and performance for 12 months or more under proper storage conditions.
Conclusion
ENEPIG has emerged as a superior surface finish for high-performance electronic devices, offering a combination of excellent solderability, durability, corrosion resistance, and compatibility with fine-pitch designs. Its multi-layer structure, consisting of electroless nickel, electroless palladium, and immersion gold, provides a robust and reliable solution for a wide range of applications, including automotive electronics, aerospace and defense, medical devices, consumer electronics, and industrial electronics.
The ENEPIG application process involves careful surface preparation, followed by sequential plating of the nickel, palladium, and gold layers. Strict quality control measures and testing methods ensure the consistency and reliability of the finish. The comparison of ENEPIG with other surface finishes highlights its advantages, particularly in terms of solderability, durability, and shelf life.
As the electronics industry continues to advance, ENEPIG is expected to evolve and adapt to meet the ever-increasing demands for performance and reliability. Ongoing research and development efforts focus on optimizing the plating processes, exploring alternative metals, and developing environmentally friendly solutions. The future of ENEPIG looks promising, with potential advancements in thinner layers, advanced plating techniques, and hybrid surface finishes.
In conclusion, ENEPIG is a superior surface finish that offers numerous benefits for high-performance electronic devices. Its excellent properties, reliability, and compatibility with advanced manufacturing processes make it a preferred choice for a wide range of industries and applications. As the electronics landscape continues to evolve, ENEPIG is well-positioned to meet the challenges and demands of the future, ensuring the reliability and performance of electronic devices in an increasingly interconnected world.
Leave a Reply