Introduction
Printed circuit boards (PCBs) are integral components of most modern electronic devices. Flexible PCBs provide many advantages over traditional rigid PCBs, including flexibility, durability, and the ability to fit into tight spaces. Although flexible PCBs are often more expensive than rigid ones, there are ways to obtain high-quality flexible PCBs at affordable prices. This article explores strategies for acquiring cheap flexible PCBs without sacrificing too much on quality or customizability.
What Are Flexible PCBs?
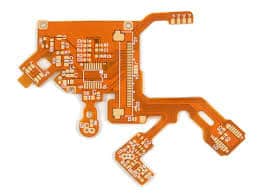
A flexible PCB is a printed circuit board made with a flexible and bendable material like polyimide or polyester rather than the standard rigid fiberglass used in traditional PCBs. The conductive traces are bonded to the flexible substrate and can bend and flex without breaking.
Flexible PCBs were initially designed for military and aerospace applications but are now commonly used in consumer electronics as well. Their flexible nature allows them to be folded, twisted, and bent to accommodate all manner of product designs. Common applications include:
- Wearable devices
- Medical equipment
- Curved displays
- Flexible smartphones/tablets
- Internet of Things (IoT) devices
Compared to rigid PCBs, flexible PCBs provide the following advantages:
- Can fit in tight, curved spaces
- Highly durable and crack-resistant
- Allow dynamic flexing and movement
- Good electromagnetic shielding
- Lightweight
On the downside, flexible PCBs tend to be more expensive than rigid PCBs. However, there are ways to obtain flexible PCBs at lower costs while still maintaining reasonable quality.
Cost Savings Tips for Flexible PCBs
Here are some tips for getting quality flexible PCBs at affordable prices:
1. Choose a Basic Substrate Material
The substrate is the flexible material that forms the base of the PCB onto which conductive traces are etched. Popular flexible substrate materials include:
- Polyimide (PI): High performance; expensive
- Polyester (PET): Affordable; lower temperature tolerance
- Polyethylene (PE): Cheapest option; less durable
Polyester (PET) substrates provide the best balance of cost and capabilities for many applications. Unless you specifically need the temperature resistance of polyimide, going with PET can save substantially on substrate costs.
2. Request 2 Layer or 4 Layer PCBs
Flexible PCBs can have from 1 to 12 or more conductive layers separated by dielectric material. The more layers, the higher the costs due to more complex fabrication.
2 layer and 4 layer flex PCBs meet the needs of many applications while keeping costs low. Unless you need 6+ layers for your design, stick to 2-4 layer PCBs.
3. Minimize Flex PCB Size
Flexible PCB manufacturers typically price boards based on the overall area. Smaller boards use less base material, require simpler fabrication, and allow more boards per panel.
Carefully analyze your design to see if the flex PCB size can be reduced. This will lower costs substantially. Just ensure heat dissipation and electrical clearances are still acceptable.
4. Choose a Flex PCB Assembly House Over Broker
Many companies broker flex PCB orders to actual flex PCB manufacturers. Using a flex PCB assembler directly reduces middleman markups resulting in lower prices.
Do some research to find reputable flexible PCB assembly houses. Getting assembly quotes from these companies directly can provide significant savings over brokers and resellers.
5. Optimize Shipping Costs
Flexible PCB production is centered in China and other parts of Asia. Shipping costs can become substantial for large or frequent orders.
You can optimize shipping costs by:
- Using sea freight instead of air for bulk orders
- Grouping multiple orders to share shipping expenses
- Ordering extra flex PCBs upfront to avoid frequent shipping
- Having PCBs shipped to a forwarder warehouse in Asia first to consolidate orders before final delivery
While the flex PCB production costs might be lower overseas, don’t neglect shipping expenses. Finding the optimal logistics flow for your orders can help minimize this.
6. Leverage Long-term Supplier Relationships
Developing an ongoing relationship with a flex PCB manufacturer over multiple orders can lead to greater cost savings. Suppliers will provide better pricing and services to valuable long-term customers.
You benefit from:
- Improved response and support
- Volume discounts
- Prioritized production
- Lower NRE charges
- Better contractual terms
Keep quality and performance as top priorities in choosing suppliers. But maintaining strong long-term supply partnerships improves leverage and stability in pricing negotiations.
7. Take Advantage of Design and Assembly Package Deals
Many flex PCB manufacturers provide discounts when ordering design services, PCB production, and assembly as a package deal. This simplifies logistics with a single supplier.
Evaluate the total costs when requesting package quotes from assemblers. There are often savings versus handling design, fabrication, and assembly separately. Package deals also ensure components, design, and production are optimized together.
Just be careful about vendor lock-in. Make sure package deals are still price competitive overall.
Quality Considerations
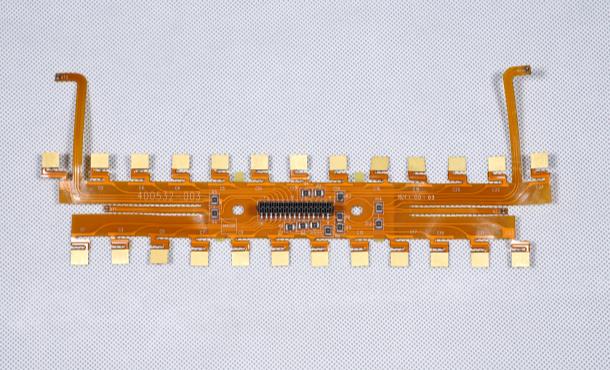
When implementing the above cost reduction tips, keep in mind that flex PCB quality should still meet your requirements. Here are some key considerations:
- Reliability – Avoid overly cheap boards that risk defects and reliability issues. Rigorously vet suppliers on their quality processes and use known reliable materials.
- Capabilities – Ensure the flex PCB can still support necessary features like layer counts, densities, and high-frequency operation. Don’t sacrifice capabilities just for lower price.
- Testing – Require suppliers to conduct testing like AOI inspection, netlist testing, etc. to ensure quality. Perform in-house testing on received boards as well.
- Qualifications – Require certifications (e.g. ISO), qualifications, and approvals appropriate for your industry and application.
- Traceability – Confirm suppliers provide lot traceability, reliable chain of custody, and counterfeit avoidance procedures.
Insist on regular quality reporting, change notification, and failure analysis when issues occur. The goal is achieving affordable pricing without severely degrading quality or reliability.
Conclusion
Flexible PCBs enable innovative designs but can become quite expensive. With careful considerations like minimizing size, choosing economical substrates, shipping optimization, and supplier negotiations, quality flexible PCBs can be obtained at very reasonable costs. Just ensure proper quality precautions are still maintained. Leveraging strategies like this allows incorporating flexible PCB technology into designs cost-effectively.
Frequently Asked Questions
What are some key differences when designing a flex PCB versus a rigid PCB?
Some key flex PCB design differences include:
- Accounting for flexibility and dynamics in trace routing
- Minimizing rigid sections and allowing generous bend radii
- Using teardrop pads and other stress relief techniques
- Allowing for stretch and contraction of traces
- Avoiding 90-degree angles
Can flex PCBs be assembled with standard SMT assembly processes?
Yes, the same SMT assembly equipment and processes used for rigid boards can be utilized for flex PCBs. Additional care may need to be taken during some handling steps due to the flexible nature.
Are there limitations on the number of board layers with flex PCBs?
Flexible PCBs are commonly available from 1 to 12 layers or more. The flex PCB thickness increases with more layers, which reduces bendability. Very high layer counts above 12 layers can become difficult to fabricate for flex boards.
How durable are most flexible PCBs?
Flex PCB durability depends on the substrate material. Polyimide boards are extremely durable with bend cycles often rated over 1 million. Lower-cost Polyester PCBs are still robust but have lower bend cycle ratings around 50,000 cycles.
Are there any environmental concerns with flexible PCBs?
Flex PCBs use the same base materials like FR-4 rigid boards. Lead-free assembly processes are also the same. Flex PCB disposal and recycling follows similar guidelines and regulations as other e-waste containing PCBs.
Leave a Reply