Introduction to Carbon Nanotube PCBs
Carbon nanotubes (CNTs) are an advanced material that is finding increasing use in the manufacture of printed circuit boards (PCBs). CNTs consist of sheets of graphene rolled into nanoscale tubes. They possess a number of remarkable properties, including:
- Extremely high tensile strength (up to 100 times greater than steel)
- Excellent electrical conductivity
- High Thermal Conductivity
- Large current carrying capacity
- Low coefficient of thermal expansion
These properties make CNTs an attractive material for use in PCBs, offering the potential for boards with improved electrical performance, higher power handling, and greater reliability compared to conventional PCB materials. In this article, we’ll take an in-depth look at carbon nanotube PCB technology, including how CNTs are used in PCB Manufacturing, the benefits they provide, and some of the challenges that still need to be overcome.
How Carbon Nanotubes are Used in PCB Manufacturing
There are several ways that carbon nanotubes can be incorporated into the PCB manufacturing process:
CNT-Based Conductive Inks
One approach is to use CNT-based conductive inks for printing circuits onto the PCB Substrate. The CNTs are dispersed in a carrier fluid to create an ink that can be applied using inkjet printing or screen printing methods. After printing, the ink is cured to remove the solvent, leaving behind a conductive CNT trace.
CNT inks offer some advantages over conventional conductive inks based on metal particles:
- Higher conductivity for a given trace thickness
- Ability to print finer pitch traces
- Lower curing temperatures
- Potentially lower cost
CNT-Doped Laminates
Another way to use CNTs in PCBs is by doping the laminate material used for the board substrate with a small percentage of CNTs. The CNTs can be mixed into the resin used to impregnate the reinforcement fibers.
Adding CNTs to the laminate provides several benefits:
- Increased thermal conductivity for better heat dissipation
- Reduced coefficient of thermal expansion for improved reliability
- Enhanced mechanical strength
- Improved electrical conductivity
Challenges with CNT-Doped Laminates
While CNT-doped laminates offer intriguing possibilities, there are some challenges that need to be addressed:
- Achieving uniform dispersion of CNTs throughout the resin
- Preventing agglomeration of CNTs which reduces their effectiveness
- High cost of CNT materials
- Unknown long-term reliability
More research is needed to fully optimize the use of CNTs in laminate materials for PCBs.
Benefits of Carbon Nanotube PCBs
Using carbon nanotubes in PCBs offers a range of potential benefits compared to boards made with conventional materials:
Improved Electrical Performance
The high electrical conductivity of CNTs enables the printing of finer pitch traces while maintaining low resistance. This is advantageous for high-speed digital applications where signal integrity is critical. The high current carrying capacity of CNTs is also beneficial for power electronics.
Some specific improvements that have been demonstrated with CNT-based PCBs include:
Property | Improvement |
---|---|
Trace resistance | Up to 50% reduction |
Current carrying capacity | 2-3 times increase |
High-frequency loss | 20-30% reduction |
Crosstalk | 10 dB reduction |
Better Thermal Management
CNTs have a very high thermal conductivity, enabling more efficient heat spreading and removal from the PCB. This is especially important for high-power applications where a large amount of waste heat is generated.
Studies have shown that adding just 1% CNTs to the laminate material can increase thermal conductivity by 50-200% compared to standard FR-4 material. This can allow for a reduction in the size and number of thermal vias needed, increasing board design flexibility.
Enhanced Mechanical Properties
The extremely high tensile strength of CNTs can improve the mechanical robustness of PCBs. This is beneficial for applications where the board may be subjected to vibration, impact, or flexing.
CNT-doped laminates have been shown to provide:
- 30-50% increase in flexural strength
- 20-30% increase in impact strength
- 10-20% improvement in delamination resistance
These enhancements can lead to more reliable PCB assemblies with fewer failures due to mechanical stresses.
Reduced Thermal Expansion
The coefficient of thermal expansion (CTE) of PCB materials is an important consideration for reliability, as mismatches in CTE between the PCB and components can cause failures due to thermal stress.
CNTs have a very low CTE, and adding them to laminate materials can help reduce the overall CTE of the PCB. Reductions in CTE of 10-30% have been reported with CNT doping.
This reduction in CTE can improve reliability by minimizing thermal stresses and reducing the risk of solder joint failures or component cracking.
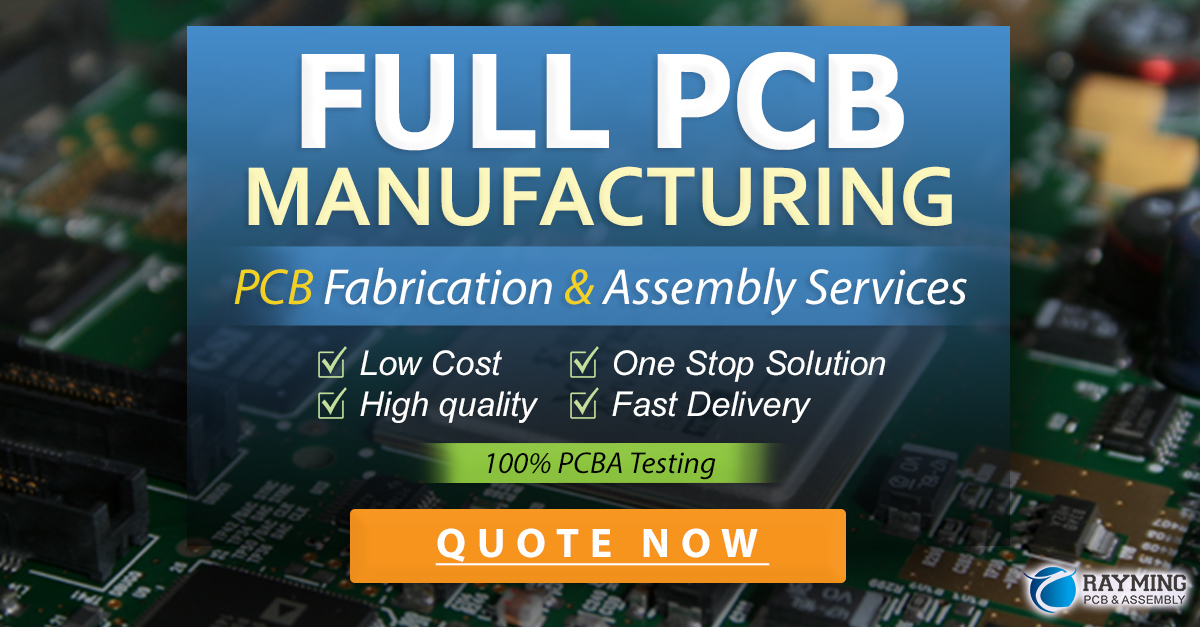
Challenges and Future Development
While carbon nanotube PCB technology offers many potential benefits, there are still some challenges that need to be overcome for widespread adoption:
High Material Costs
CNTs are currently much more expensive than conventional PCB materials like copper and FR-4 laminate. Prices have been declining as production volumes increase, but further cost reduction is needed to make CNT PCBs economically viable for most applications.
Process Integration Difficulties
Incorporating CNTs into existing PCB manufacturing lines can be challenging. New equipment and processes may be needed to handle CNT-based materials, and existing processes may need to be adapted. This can require significant upfront investment.
Supply Chain Concerns
The supply chain for CNT materials is not as well-established as for conventional PCB materials. There are a limited number of suppliers, and availability can be constrained. This raises concerns about the ability to scale up production and maintain consistent quality.
Unknown Long-Term Reliability
While initial studies have shown good reliability for CNT-based PCBs, there is still limited data on long-term performance in real-world conditions. More testing and field experience is needed to fully validate the reliability of this new technology.
Despite these challenges, research and development of CNT PCB technology is continuing at a rapid pace. As material costs come down and manufacturing processes are optimized, it is expected that CNT PCBs will start to see adoption in high-performance applications where their benefits can justify the added cost.
Some of the key areas of ongoing development include:
- Optimizing CNT dispersion and alignment in inks and laminates
- Developing lower-cost CNT materials and production methods
- Improving the interfacial bonding between CNTs and polymer matrices
- Investigating hybrid approaches that combine CNTs with other materials
- Modeling and simulation tools to help design CNT-based PCBs
As these developments progress, it is likely that CNT PCBs will become an increasingly important part of the electronics manufacturing landscape.
Frequently Asked Questions
What are carbon nanotubes?
Carbon nanotubes (CNTs) are cylindrical molecules consisting of rolled-up sheets of single-layer carbon atoms (graphene). They typically have diameters in the nanometer range and lengths that can be many times greater. CNTs can be single-walled (SWCNT) with a single graphene sheet, or multi-walled (MWCNT) with multiple concentric graphene sheets.
How are carbon nanotubes produced?
There are several methods for producing carbon nanotubes, including arc discharge, laser ablation, and chemical vapor deposition (CVD). Arc discharge and laser ablation involve vaporizing a graphite target in the presence of a metal catalyst, while CVD grows CNTs on a substrate from gaseous carbon-containing precursors. CVD is the most widely used method for large-scale production of CNTs.
What are the properties of carbon nanotubes?
Carbon nanotubes have a unique combination of properties, including:
- Exceptionally high tensile strength, up to 100 times greater than steel
- Excellent electrical conductivity, similar to copper or silver
- High thermal conductivity, comparable to diamond
- Large current carrying capacity, up to 1000 times that of copper wire
- Low coefficient of thermal expansion
- Good chemical and environmental stability
These properties arise from the strong carbon-carbon bonds and the unique structure of CNTs.
How do carbon nanotubes improve PCB performance?
Using CNTs in PCBs can improve performance in several ways:
- CNT-based conductive inks enable printing of finer pitch traces with lower resistance, which improves signal integrity and power handling.
- CNT-doped laminates have higher thermal conductivity, which enhances heat dissipation and allows for more compact designs.
- CNTs increase the mechanical strength and reduce the CTE of PCB materials, improving reliability.
- The high current carrying capacity of CNTs is beneficial for power electronics applications.
What challenges remain for widespread adoption of CNT PCBs?
Some of the key challenges that need to be addressed for widespread adoption of CNT PCBs include:
- Reducing the cost of CNT materials to be competitive with conventional PCB materials
- Developing scalable and reliable manufacturing processes that can be integrated into existing production lines
- Establishing a robust supply chain for CNT materials with consistent quality and availability
- Generating more data on the long-term reliability of CNT-based PCBs in real-world conditions
As research and development efforts continue, it is expected that these challenges will be gradually overcome, enabling broader use of CNT PCBs in the electronics industry.
Conclusion
Carbon nanotube technology is a promising development for the PCB industry, offering the potential for significant improvements in electrical performance, thermal management, and mechanical robustness. While there are still challenges to be overcome in terms of cost, manufacturability, and long-term reliability, ongoing research and development efforts are making steady progress.
As CNT materials and manufacturing processes continue to mature, it is likely that CNT PCBs will see increasing adoption in high-performance applications where their benefits can justify the additional cost. In the longer term, CNT PCBs may become a mainstream technology that enables a new generation of electronic devices with enhanced capabilities.
PCB designers and manufacturers should keep a close eye on developments in CNT technology and consider how it could be applied to their products and processes. By staying at the forefront of this emerging field, companies can position themselves to take advantage of the benefits of CNT PCBs and stay competitive in the rapidly evolving electronics industry.
Leave a Reply